フライス加工の基本。材料特性や工具、依頼する際のポイントなど
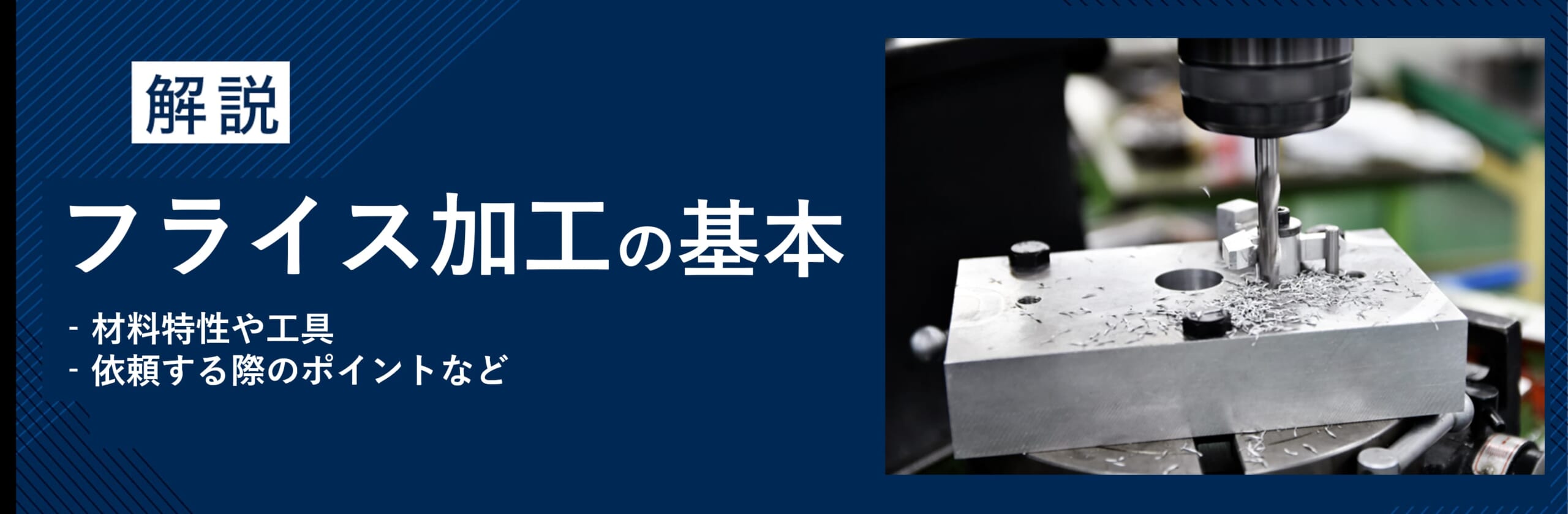
現在、製造現場では「マシニングセンター」を使用した加工が主流なので、経験の浅い作業者でも短期間で高精度な製品の加工が可能です。その結果「フライス加工の基本」を知らない方が多く、加工中のトラブルに対応できないという状況が少なくありません。
この記事では、フライス加工の基礎や工具・被削材、トラブルへの対処法などをわかりやすく解説していきます。
目次
フライス加工の基本知識
フライス加工は「高速で回転する工具を被削材に押し当てて加工する」方法で、正面フライス(フェイスミル)やエンドミルなどの工具を使用し、任意の形状にする「除去加工」(不要な部分を切削により除去する方法)に該当します。
フライス加工では「6面体などの角物の加工」がメインですが、ドリルやサイドカッターなどのさまざまな工具を使い分けることで、平面・曲面・溝・穴明けなどの複雑な形状の加工が可能です。
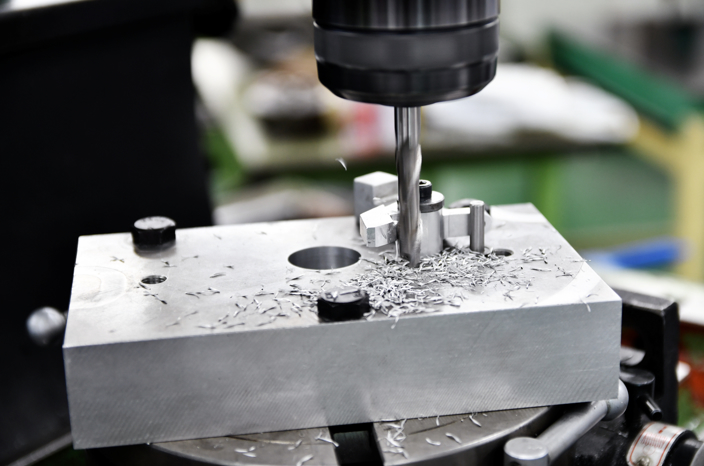
他加工方法(旋盤加工)との違い
切削加工には、大きく分けて「転削加工」と「旋削加工」の2種類の方式があります。転削加工では「フライス盤」を使用し、旋削加工では「旋盤」を使用します。
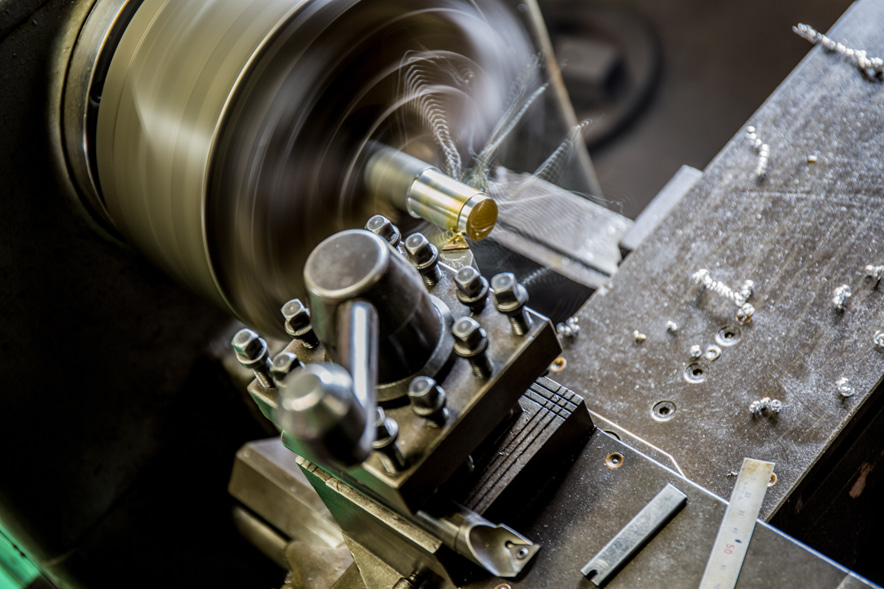
旋削加工は、旋盤という機械を使用し「被削材(ワーク)を高速回転させ、刃物台に固定した工具を押し当てる」加工方法です。加工可能な軸方向は「径方向(X軸)」「長手方向(Z軸)」の2軸です。そのため、従来の旋盤で加工できる基本形状は、円柱、円筒、円錐、ねじ切りなどの回転対称形状が中心となります。
それに対し、転削加工(フライス加工)は、加工軸がX(左右)、Y(前後)、Z(上下)の3軸を持つため、平面加工、溝加工、ポケット加工、3次元曲面など、旋盤よりも複雑な形状の加工が可能です。
フライス加工で使用する工作機械と工具
製品の加工形状やサイズ、必要な加工精度によって、使用する工作機械と工具の適切な選択が必要になります。
以下に示す表を参考に、適切な機械・工具を選択するようにしましょう。
使用する工作機械
使用する機械 | メリット | デメリット |
---|---|---|
フライス盤![]() | ・段取りを簡素化できる。 ・工具破損などの突発的なアクシデントに対応しやすい。 ・数値制御装置よりもランニングコストが安い。 | ・ある程度の熟練が必要。 ・曲面などの複雑な形状は加工が困難。 ・加工精度は作業者の熟練度により差が出る。 |
NCフライス![]() | ・曲面などの複雑な形状が加工できる。 ・個人差や熟練度による加工精度のバラつきが少ない。 ・加工条件の保存が可能。 ・ある程度の省力無人化が可能。 | ・加工プログラムの習得が必要。 ・多種の工具を必要とするワークには向かない。 |
マシニングセンター ![]() | ・手作業では困難な曲面、角度の加工が可能で、寸法精度も高い。 ・一度に多種の工具を使用できる。 ・熟練者でなくても作業ができるので、人的コストを安くできる。 ・比較的安全に作業ができる。 ・ロボットやパレットチェンジャーを活用すれば、省力化・夜間の無人加工が可能。 | ・加工プログラムの習得が必要。 ・ 段取りが複雑になる。 ・潤滑油やクーラント、ツールホルダーなどランニングコストが高い。 ・設備本体および初期費用や維持費が高額。 |
NC歯車加工機![]() | ・専用の工具を使用するため、複雑な座標計算、プログラミング、段取りが不要。 | ・基本的に歯車加工しかできない。 ・専用工具の「ホブ」は、比較的高額である。 |
工具と加工の種類
角物を加工するときに使用する主な工具は、次のようなものがあります。
工具 | 主な用途 | 補足事項 |
---|---|---|
正面フライス![]() | ワークの正面切削に使用。 エンドミルよりも加工径が大きく、広い面を加工できる。 | 近年は、沈み加工(ヘリカル加工)に対応した製品も多く販売されている。 |
サイドカッター![]() | ワークの溝加工に使用。 側面の切れ刃が交互に付いた千鳥刃サイドカッターは、重切削が可能。 | メタルソーとの違いは、カッター側面の刃の有無。 |
エンドミル![]() | ワークの側面・溝などの加工に使用。 沈み・ヘリカル加工に対応した製品も多い。 | 切粉詰まりしやすい深穴や溝加工のため、ホルダ内部からクーラントを供給できる(スルークーラント)タイプもある。 |
ソリッドエンドミル | 側面・溝・沈み・ヘリカル・ザグリ加工に使用。 ハイスや超硬のものがあり、側刃・底刃の再研磨も可能。 | コーティングされたものは高価だが、耐摩耗性が高く難削材での加工に適している。 |
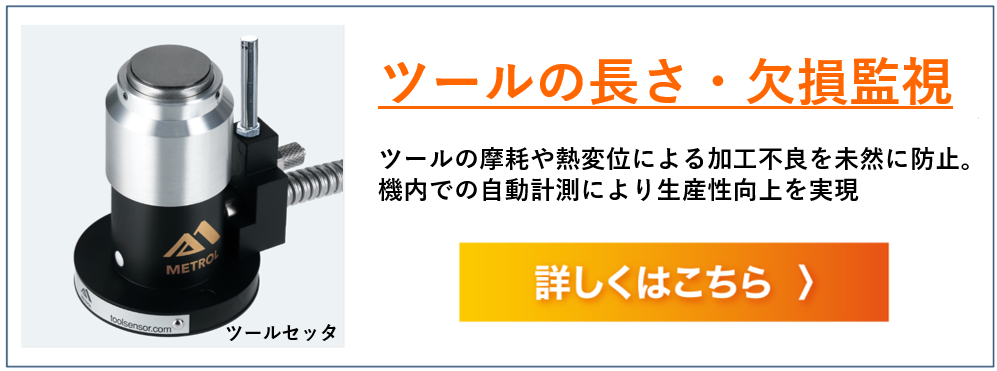

フライス加工に使用される材料
フライス加工でよく使用される被削材は、以下になります。
SS400やS45Cなどの鉄鋼材料
SS400やS45Cは機械加工の現場でよく利用されている材料で、入手がしやすく価格もそれほど高価ではありません。
特にS45Cは「機械構造用炭素鋼鋼材」に分類されており、熱処理を加えることで硬度が増したり機械的性質が向上します。
切削性がよく、非鉄用やダイヤモンド工具を除き、数多くの工具材種で加工が可能です。
アルミ合金
アルミ合金は切削性がよく鉄鋼材料よりも軽いため、航空機の部品で使用されています。鋳造や押し出し加工を利用した大量生産も可能です。
また、鉄鋼材料よりも耐腐食性が高く「非磁性」である特徴を活かし、磁気の影響を受けやすい場所や真水・海水にさらされる環境、低温環境などで利用されています。
融点が低く溶着しやすいため、加工は湿式加工がメインで、超硬工具を使用した高速切削加工が最適です。
銅・黄銅(真鍮)
銅は切削性がよい材料ですが、粘り気が強く融解温度が低いため構成刃先(刃先に材料が溶着)ができやすい材料です。
切削には油性のクーラントとすくい角の大きいシャープな工具を使用し、切削速度を上げた高速加工が適しています。
黄銅(真鍮)は切削性がよく、曲げ・溶接・研磨などの加工が容易な金属です。
主な用途は、機械部品や電子機器の端子・配線器具のほか、外観のよさを活かしたトランペットなどの金管楽器です。
展伸性が高いため、加工時のバリが出やすく工具の食い込みが大きいので、すくい角の小さい工具の使用をおすすめします。
樹脂
樹脂はその融点の違いにより、プラスチック、エンジニアリングプラスチック、スーパーエンジニアリングプラスチックに分類されます。そのほか、ABSやポリエチレン、PETやアクリル、ポリカーボネートなども切削加工に向いています。
樹脂は熱伝導性が低く、加工で生じる熱が製品の寸法精度に影響しやすい材料なので、すくい角が大きいシャープな工具の使用がおすすめです。
難削材の加工
難削材とは、一般的な金属材料と比べて加工が困難な材料の総称です。高い強度、耐熱性、耐食性などの優れた特性を持つ一方で、加工効率に課題もあります。
SUS303やSUS304などのステンレス材
SUS303やSUS304は耐熱性や耐腐食性が高いため、主に過酷な環境で使用される機械の部品や外装に使用されます。
強度や硬度が高く、切削加工では工具の寿命が短く加工に要する時間も長くなるため、ステンレス材の製品や部品は鉄鋼部品よりも割高です。 ステンレスは熱伝導性が低く、加工硬化しやすい性質もあるため、乾式での切削よりもクーラントを十分に使用した湿式加工が適しています。
チタン
チタンは鉄鋼材料よりも軽く、強度や耐熱性・耐腐食性にすぐれた金属ですが、切削加工は難しく材料単価も高いため、チタンの加工製品は鉄鋼よりも高額です。
チタン合金は引っ張り強度が鉄鋼の約2倍あり、熱伝導率が低いため工具が損傷しやすいという特徴があります。
また、びびりが発生しやすく切削時の切りくずは発火しやすいので、加工の際は超硬の工具を使用して切削速度を落とし、こまめに切りくずを処理してください。
インコネル
耐熱合金に分類されるインコネルは、高温・高圧な条件下で使用される機械の部品に使用され、航空機やロケットのエンジン、発電所の蒸気タービン、車やバイクのマフラーで使われています。
同じ難削材であるステンレスよりも刃先が摩耗しやすいので、耐摩耗性に優れたコーティングの超硬工具がおすすめです。
また、強ねじれ刃やポジティブすくい角、刃数の多いカッターを使用して刃先へのダメージを分散させるのも有効な方法です。
フライス加工のトラブルシューティング
フライス加工でよくあるトラブルについて、原因や対策方法をまとめてみました。
トラブル内容 | 主な原因 | 対策 |
---|---|---|
びびり | ワーク保持の弱さ | ・ワークの保持方法の見直し。 ・切り込み量を減らし、切削抵抗を少なくする。 ・コーナーRや平行ランドの小さい工具の選択。 ノンコーティングの工具を使用する。 |
軸方向に弱いワーク | ・ポジブレーカー付きスクエアカッターを使用。 ・コーナーRの小さい工具を選択。 ・切り込みを小さくする。 ・こまめな工具摩耗のチェック。 ・ツールホルダーの振れや保持方法の改善。 | |
工具突き出しが長い | ・最低限の突き出しにする。 ・不等ピッチのカッターを使用。 ・刃当たりの送りを上げる。 ・仕上げ加工時はアップカットを使用。 ・超硬工具を使用する。 ・切り込み角45°、大きなコーナーRまたは丸チップの選択。 | |
低剛性のスピンドル テーブル送りが不安定 | ・工具径の小さいものを選択。 ・アップカットを試してみる。 ・ポジまたは軽切削のカッターを使用する。 ・スピンドルやテーブル送りのたわみをチェックする。 | |
切削条件 | ・切削速度を下げる ・送りを上げる ・適切な切り込み量の選択。 | |
切りくずの詰まり | チップのコーナー欠損 刃先のチッピングや欠損 切りくずの再切削(リカット) | ・十分な吐出圧・方向性のある切削油や圧縮エアーの供給。 ・切削加工のパス回数を増やす。 ・深溝ではアップカットを試す。 ・コースピッチカッターや超硬エンドミル、ねじれ角の大きなエンドミルを使用する。 |
切りくずのリカット | 切れ刃破損 工具寿命 切りくず詰まり | ・圧縮エアーや十分な吐出圧 ・方向性のある切削油の供給。 ・内部給油可能な工具・機械の選択。 ・送りを下げる。 ・カッター位置やツールパスの変更、およびパス回数を増やす。 |
面粗度 | 過度の回転当たり送り | ・スピンドルの振れとカッター取り付け面をチェック。 ・送りをチップの平行ランド幅の7割に下げる。 ・仕上げ加工時にワイパーチップを使用する。 |
構成刃先の発生 | ・切削速度を上げる。 ・ドライ加工を試す。 ・すくい角の大きい工具や、ポジチップブレーカーを選択。 ・サーメット材種を使用する。 | |
加工物のつぶれ | ・送りを下げる。 ・カッター位置を調整し、抜け際の切りくずを薄くする。 ・シャープなチップや軽切削のブレーカーを使用。 ・工具の逃げ面摩耗のチェック。 | |
バリの発生 | 被削材の性質 ノッチ摩耗 | ・大きなコーナーRのチップを使用して、切込み角を小さくする。 ・切り込み量をコーナーRよりも小さくする。 ・カッターパスを見直す。 |
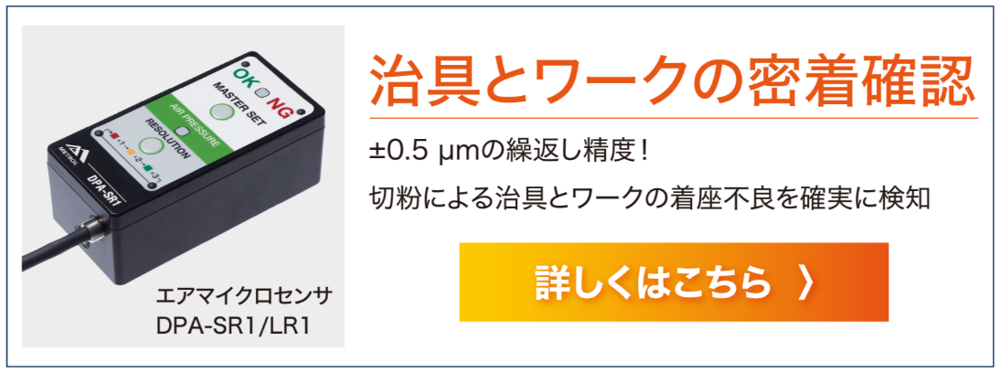

フライス加工を依頼する際のポイント
フライス加工を外注・依頼するときは、加工対象の形状や精度、使用材料、数量、納期など、重要なポイントを明確に伝えましょう。その中でも重要な点は以下です。
図面作成におけるポイント
まず基本となる各部の長さ、幅、高さなどの寸法数値、寸法公差や幾何公差、表面粗さの要件(Ra 値など)はしっかりと記入しましょう。
コスト削減の策としては、特に高精度が必要な加工面は図面上で示す一方で、製品性能に大きく影響しない加工面については、公差や表面粗さの要求を適度に緩和することも覚えておくとよいでしょう。
公差と仕上げ
フライス加工では一般的に中級程度の寸法公差が得られます。また、表面粗さはRa 1.6や Ra 3.2を目安に指定することが多いです。必要以上の公差や面粗度を指定すると、加工コストが跳ね上がる可能性がありますので、ご注意ください。
加工箇所・形状に関する注意点
小さなR指定エンドミルの干渉により加工ができない場合があります。実際に指定通りのR寸法が必要かどうかを事前に検討し、加工業者と共有することが重要です。
また、深穴加工やポケット形状といった加工を行う場合、工具のたわみや加工時の振動が大きくなりやすく、加工精度の低下やコスト増加の原因となる場合があります。このような場合は、可能な範囲で部品を分割構造にしたり、加工しやすい寸法に変更したりしましょう。
フライス加工自動化に貢献するメトロールのセンサ
位置決めタッチスイッチ
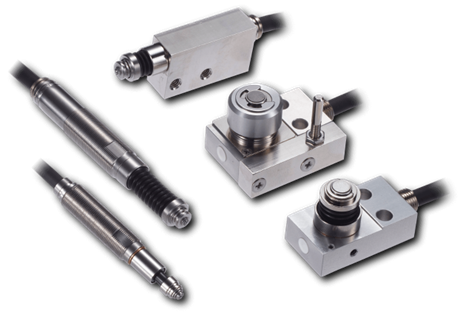
メトロールの位置決めタッチスイッチは、アンプを必要としない高精度タッチセンサです。
フライス加工で使用すれば「X軸やY軸の位置決め」「ワークの有無や着座・寸法確認」のほか、小径工具の工具長測定・折損のチェック、ロボットの位置決めなどに利用できます。
ツールセッタ
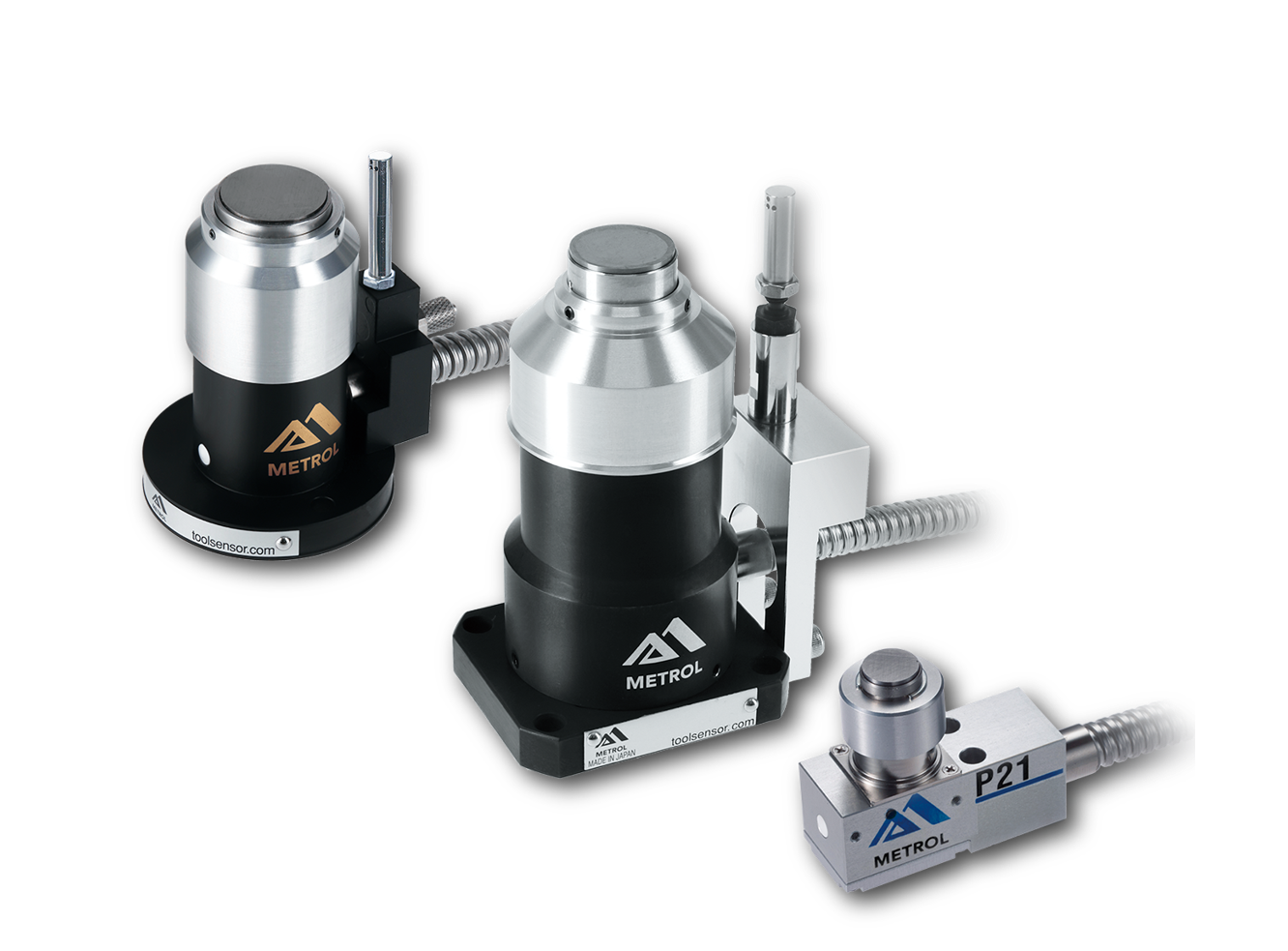
メトロールのツールセッターは、CNC工作機械・産業用ロボットのツールやノズルの位置決めに使用される高精度タッチセンサです。
工具長測定や摩耗・折損検出、熱変位検知などに使用可能で、工具の摩耗や折損による加工不良や衝突を防止できます。
タッチプローブ
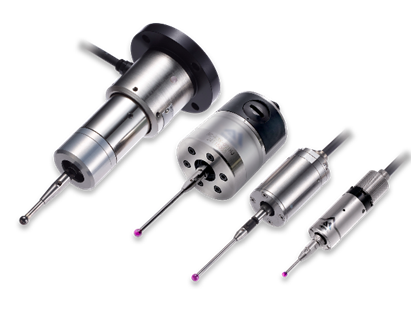
タッチプローブは、主にCNC工作機械や産業用ロボットで使用されるインライン計測用接触式センサです。
メトロールのタッチプローブは、加工前ワークの原点測定や加工後のワーク寸法測定などの自動化が可能で、属人化の解消や段取り時間の短縮・サイクルタイム向上、加工不良の防止を可能にします。
エアマイクロセンサ
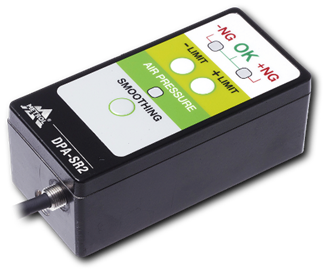
メトロールのエアマイクロセンサは、ワークの「密着確認」ができる高精度エアセンサです。
ワーククランプ時に起こりがちな「切粉の嚙み込み」で発生する数ミクロンの隙間の検出や、ワーク内径の検査、CNC研削盤の回転砥石の位置合わせなどで活用できます。 通信規格「IO-Link」にも対応しているため、省配線が可能です。
関連記事
【設備検討中の方必見】当社がCNC自動旋盤Cincomを導入した理由
メトロールでも導入しているシチズンマシナリーのCNC自動旋盤 Cincomシリーズについて解説しています。
・加工部門のNC化を進めたい
・機械トラブルやチョコ停を無くして稼働率を上げたい
・工程集約して、検査などの前後工程を効率化したい
とお考えの方におススメです。
エアマイクロセンサ ~自動化時代を支える「精密着座センサ」~
一般的な「空圧式ギャップセンサ」は信号点のバラツキが大きいため、ワークの「有り無し検知」にしか使えませんでした。「エアマイクロセンサ〔SR1〕」はその常識を根底から覆し、従来品の約60倍、±0.5µmの繰返し精度を達成しました。
切粉などによる「ワーク」の浮き上がりを検出して、「着座不良」による加工不良品の発生を生産工程で確実に防止します。