切削工具 折損の基本。加工条件設定とよくある課題
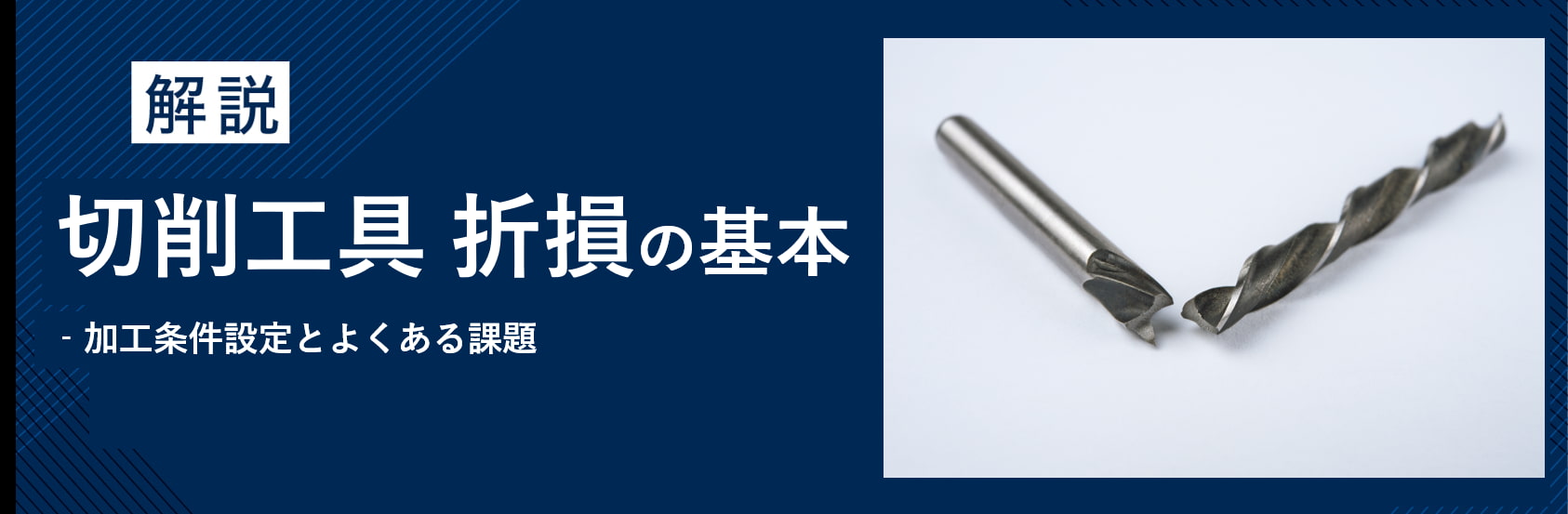
切削加工に携わる人なら、誰もが一度は経験している「工具の折損」。折損とは、切削工具が加工中に突然折れたり変形したりしてしまう現象のことを言います。
「消耗品だから折れるのは仕方ない」と考えている人は少なくありません。
しかし、なぜ折損するのかを理解することで、折損による製品の損失・工具の消耗を減らすことが可能です。
この記事では、工具折損の主な原因、その対策についてわかりやすく解説します。
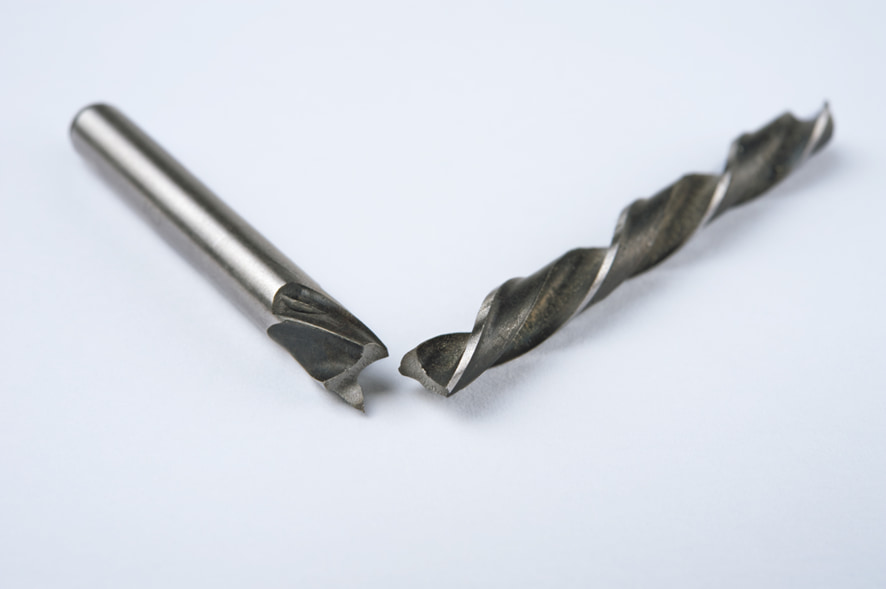
目次
切削工具の基本理解
切削工具には「その加工形状や必要とする精度」により使い分ける必要があるため、いろいろな種類・材質の工具があります。以下に示す工具は、切削加工に欠かせない代表的な工具です。
切削工具の種類と特徴
フライス
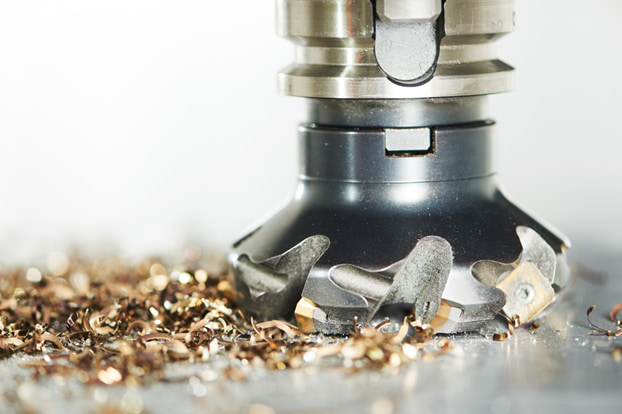
エンドミルやフェイスミルなど、主に「フライス盤」や「マシニングセンター」で使用する工具。
平面・側面などの加工が可能で、ハイスや超硬、チップを使用したスローアウェイタイプがある。
ドリル
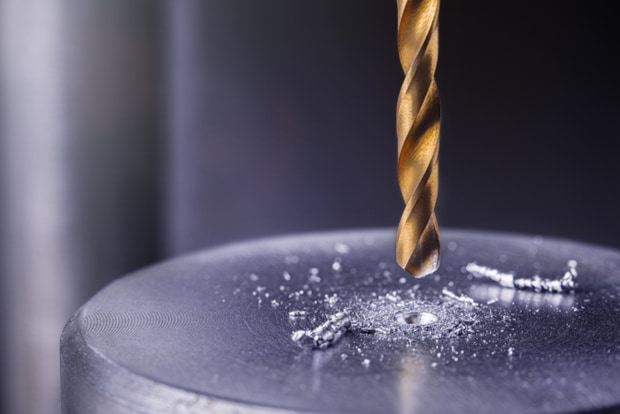
ボール盤や旋盤、マシニングセンターやCNC旋盤などで使用される「穴あけ」加工の工具。
主な工具材種はハイスや超硬で、スローアウェイタイプや先端交換式のほか、「ザグリドリル」や「段付きドリル」、深穴加工に特化した「ガンドリル」などもある。
タップ
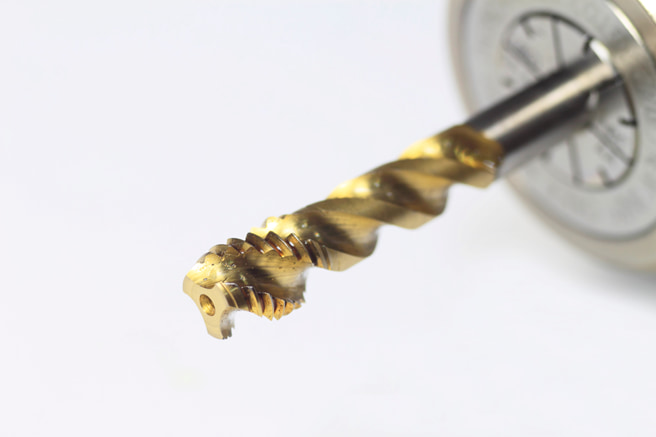
ネジ穴(めねじ)を加工するための工具で、通し穴用のポイントタップや止まり穴用のスパイラルタップなどがある。主にボール盤(タッピング加工装置付き)や旋盤などで使用。
材質もハイス・超硬があり、マシニングセンターのヘリカル補間を使用して加工する「スレッドミル」などもある。
リーマー
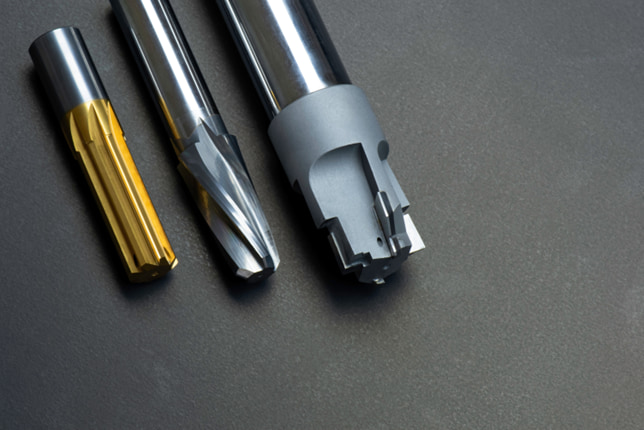
ドリルで加工した穴の内径寸法や、面相度を精密に仕上げるための工具。
材質もハイス・超硬があり、下穴の形状により通し穴・止まり穴用などがある。
工具の先端がエンド刃形状になっている「ミルリーマー」は、高精度の位置決めや工具数削減による加工時間短縮が可能。
バイト
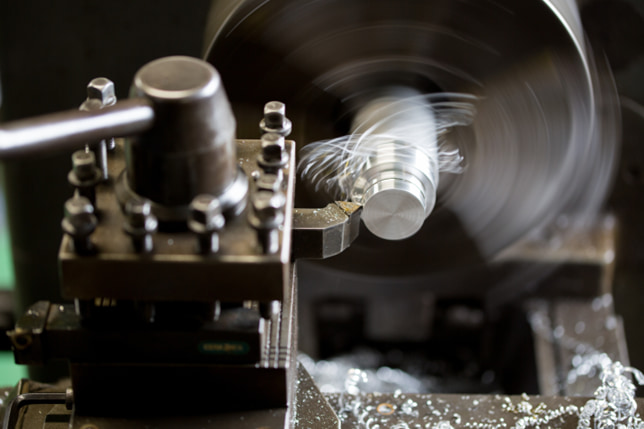
バイトは、旋削加工でよく使われる切削工具で、片刃バイトや剣バイト・突っ切り・中ぐり・ねじ切りなど、加工形状に適したものがある。
超硬やスローアウェイが一般的だが、低切削速度でのねじ切り加工に適したハイス製スローアウェイチップも販売されている。
工具材種について
ハイス
ハイスは一般的な工具材種で、安価で入手しやすい・刃が欠けにくい・切削時の切粉が飛散しにくいなどの利点がある。
超硬よりも靭性が高く安価だが、高温に弱く焼き入れ済みの高硬度被削材には適さない。
超硬
ハイスよりも高い硬度と耐熱性があるため、乾式での高速切削加工が可能だが、強い衝撃を加えると破損しやすい。
被削材の材質や硬度に合わせた超硬材種や加工条件を選択することで、長寿命で安定した加工ができる。
CBN
CBNは、立方晶窒化ホウ素(Cubic Boron Nitride)という人工鉱物でできた工具で、主に鉄系焼き入れ鋼の仕上げ加工に使われる。硬度は高いが「割れ」や「欠け」が出やすく、熱衝撃にも弱いので、乾式での低切り込み切削加工が基本である。
ダイヤモンド
ダイヤモンドは硬度が高く、超硬工具と比較して「構成刃先」が形成されにくいので、長寿命で安定した加工が可能。
アルミなどの非鉄金属の切削に適しているが、ダイヤモンドを構成する炭素と鉄の親和性が高いため、鉄系被削材の加工には不向きである。
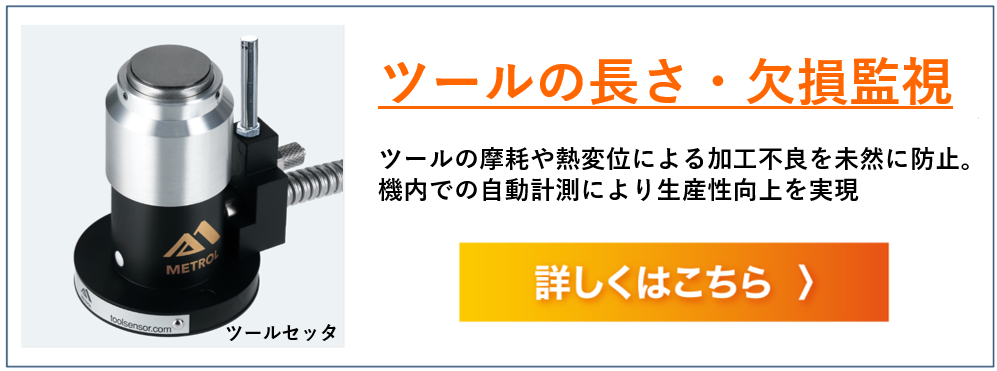

折損の基本要因
切削工具の折損には、3つの基本要因があります。
【機械的要因】
- 工具の強度を超える負荷
- 想定外の振動
- 工具の把握状況
機械的要因は、加工時の物理的な力や動きに関連する問題です。
切削速度や送り速度が高すぎると、工具が耐えられない大きな負荷がかかります。また、工作機械の振動や工具のたわみによって、予期せぬ振動が発生することがあります。工具の取り付けが不適切な場合も、通常の加工条件でも折損のリスクが高まります。
【材料的要因】
- 被削材に対する工具材種の選択ミス
- 被削材硬度や延性に対する工具材種の選択ミス
- 被削材形状による過負荷・振動の発生
材料的要因は、工具と被削材の相性に関する問題です。
例えば、高硬度の材料を切削する際に、それに適さない工具材種を選択すると、急激な摩耗や欠損が起こります。
被削材の延性が高い場合、切りくずの処理が難しくなり、工具への負荷が増大します。また、被削材の形状が複雑な場合、切削中に予期せぬ振動や衝撃が発生し、工具の寿命を縮める原因となります。
【使用環境要因】
- 冷却不足
- クーラントの選定ミス
- 切粉の詰まり
使用環境要因は、加工時の周辺条件に関する問題です。 切削点の温度が上昇しすぎると、工具の強度が低下し、摩耗が急激に進行します。不適切なクーラントの使用は、効果的な冷却や潤滑が得られず、工具の寿命を短くします。また、切粉が適切に排出されないと、切削部に堆積して異常な負荷を生じさせ、工具の折損を引き起こす可能性があります。
折損パターンの種類
折損パターンは複数あり、それぞれの発生メカニズムも解説します。
チッピング
チッピングは、超硬工具やCBN工具などの硬く脆い材種の工具が「びびり」や急激な熱変化などで「刃先が細かくノコギリ状」に欠損した状態です。
被削材に対して工具の硬度が高すぎたり、送り量が大きすぎたりする場合や、断続切削時に発生しやすくなります。
また、刃先に溶着した構成刃先の脱落もチッピングの原因のひとつです。
破断
破断は加工時に工具の内部で大きな応力が生じ、工具材種の引っ張り強度を超えた負荷の発生により起こる現象で、「重切削時の過負荷による折損」がこれに該当します。
引っ張り強度以下の負荷でも、繰り返される負荷で発生する「金属疲労」も破断の一種です。
塑性変形
塑性変形は、材料内部の特定の結晶面(転位という線状の格子欠陥)を境にして原子がすべる(動く)ことによって起こります。弾性変形と違い、塑性変形したものは時間が経過しても元に戻りません。変形の限界・引っ張り強度の限界を超えた時に起こるのが破損(折損)です。
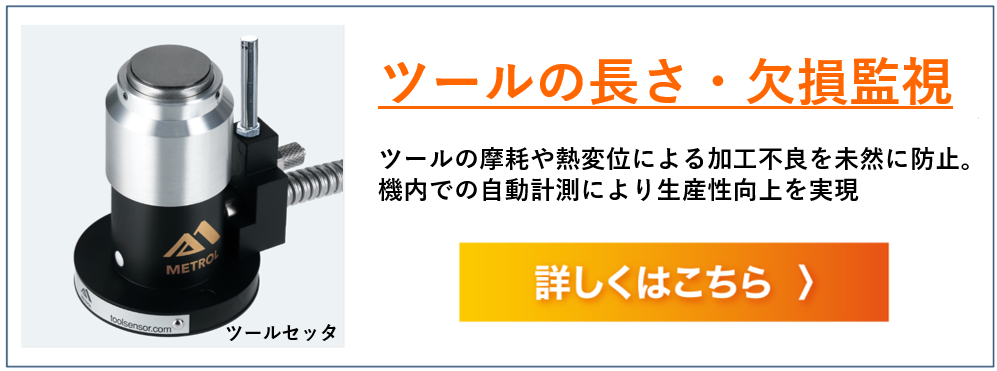

折損防止のための加工条件設定
加工中に工具が折損すると、機械や加工中の製品にさまざまな被害が発生します。
貴重な製品や工具、加工に要した時間を無駄にしないためにも、折損防止のための最適な加工条件を設定しましょう。
切削条件の設定
切削速度を上げるのは、折損防止に有効な方法です。
しかし、ドリルやエンドミル・ボールエンドミルなどの「工具の芯に近い部分」や、小径のエンドミルなどは切削速度が上がりにくいので、切削速度を意識した条件設定が必要になります。
また、加工パスや切り込み量の最適化、前工程追加による切削量の均一化・負荷軽減なども工具折損を防ぐ手段として有効ですが、加工時間増大による経済的コストを考慮した段取りが必要です。
機械要因の見直し
主軸や刃物台の精度・機械的剛性も、工具の折損防止のための要素となります。
加工プログラム変更や、前工程の調整・改善、ワークの保持方法の再検討なども有効な手段です。
また、近年の5軸同時制御加工機を使えば、ボールエンドミルの芯部を避けた仕上げ加工が可能なため、切削速度を落とさない加工ができます。
クーラントと潤滑剤の活用
適切なクーラントの選択も工具折損の防止に有効です。
被削材により油性・水溶性を使い分けることで、加工で生じる熱を逃がし、工具の摩耗や構成刃先の発生を防ぐことができます。クーラントが届きにくい箇所の加工や深部の加工では、内部給油が可能な機械や工具の選択も工具折損防止に有効です。
よくある問題と解決策
最後に、工具の折損について、よくある問題と解決策を見ていきましょう。
素材が硬すぎる
素材の硬度が高すぎる場合は、超硬工具やCBN工具・ダイヤモンド工具の使用を検討し、切り込み量を抑えた加工条件にしてください。また、焼き入れ鋼の切削では、切削油の使用により「工具の滑り」が起きやすいため、乾式での加工、または水溶性クーラントの使用がおすすめです。
クーラントと潤滑剤の活用
適切なクーラントの選択も工具折損の防止に有効です。
被削材により油性・水溶性を使い分けることで、加工で生じる熱を逃がし、工具の摩耗や構成刃先の発生を防ぐことができます。クーラントが届きにくい箇所の加工や深部の加工では、内部給油が可能な機械や工具の選択も工具折損防止に有効です。
振動による折損
振動による折損を防止するには、工具の突き出し長さや工具のクランプ方法を見直します。
熱変化による収縮を利用した「シュリンクチャック」の使用も、振動による折損の防止に最適です。 また、ロングシャンクエンドミルなどをコレットチャックで使用する場合は、事前にシャンクの余分な長さをカットすることで、加工時の振動による「コレット内部での折損」を防止できます。
過熱による折損
過熱による折損を防止するには、方向性のある圧縮エアや十分なクーラントの供給が必要です。
深穴加工や、クーラント・エアが届きにくい部分の加工では、内部給油装置のある機械や工具を選択することで刃先を効率的に冷却できます。
メトロールの工具折損検出センサ
工具折損検出センサ DFMシリーズ
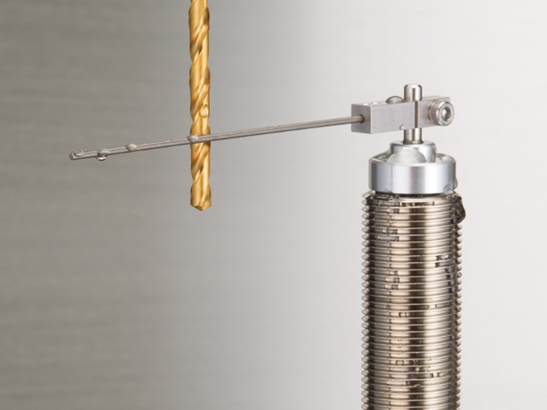
メトロールの工具折損検出センサ「DFMシリーズ」は、機械の加工範囲内に取り付け、エア駆動式のニードルで工具の折損を検出します。
ニードル状の接触子で工具に直接触れて検知するので、クーラントや切粉がかかる悪条件下でも、誤検知が少なく価格もリーズナブルです。
【動画】機内でツール折損を検出!
関連記事
切削による摩耗・昼と夜の温度差・機械の熱変位など、クーラントや切粉の飛び散るCNC工作機械の過酷な悪環境下で、ツールの長さは常に変動しています。
メトロールの「ツールセッタ」は、ツールの工具長の数値を、NCにフィードバックすることで、ツールの摩耗を1μm精度で検出し補正。
従来の試し削り・計測・NC入力などの熟練が不要になり、機械の稼働率が大幅に向上します。
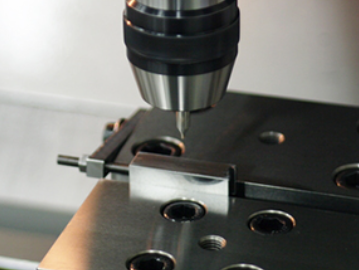