治具とは?種類や特徴についてわかりやすく解説
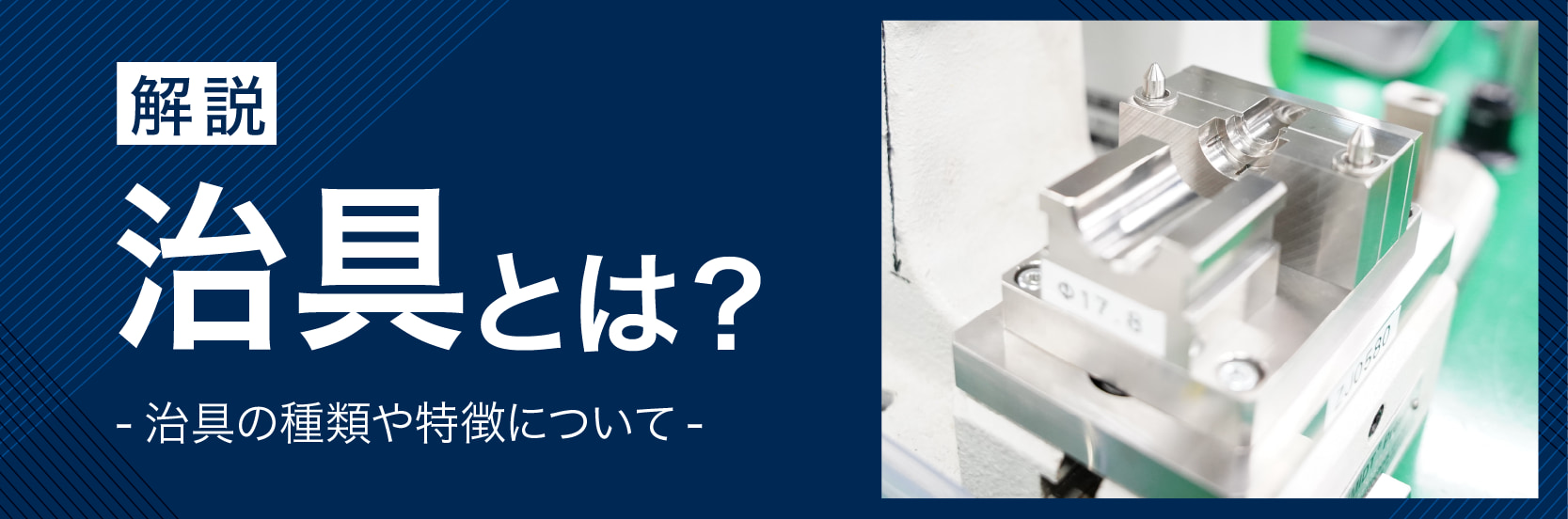
目次
治具とは?
治具(じぐ)とは、製造や加工の現場で部品を固定したり位置決めを行ったりする専用の器具や装置です。
特に精密な加工が要求される場合や、大量生産を行う際に不可欠な存在であり、その役割は非常に重要です。
治具を使うことで部品を手で保持しなくても機械や作業者が安定して作業できるようになるため、精度や作業効率が向上し、加工時の誤差を最小限に抑えることができます。
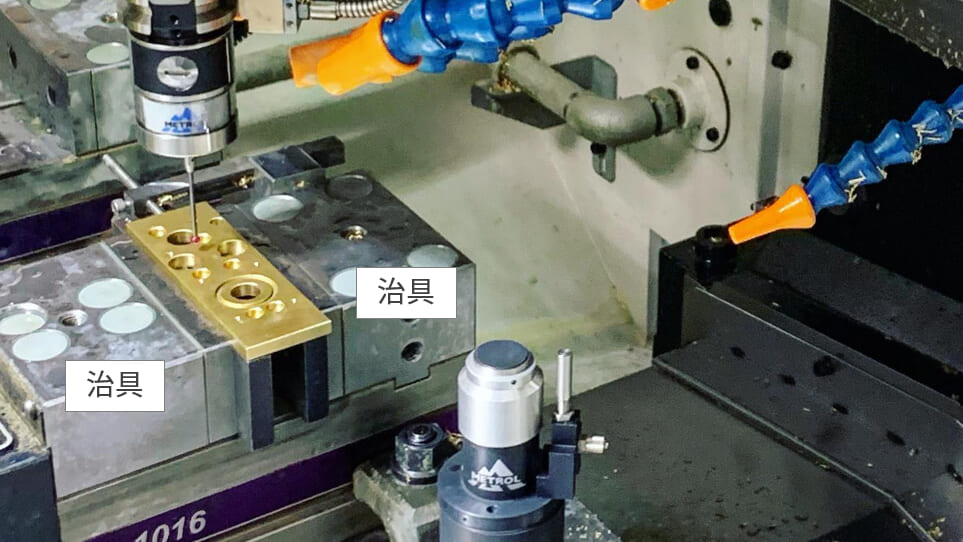
治具は、穴あけ、溶接、切削、組立など、さまざまな製造プロセスで使用され、製造業に欠かせない要素です。その設計は製品の仕様や要求される精度によって異なり、特定の部品に特化したものから汎用的に使えるものまで様々な種類があります。また、治具は特定の機械に合わせて設計されることが多く、各製造現場のニーズに応じてカスタマイズされます。
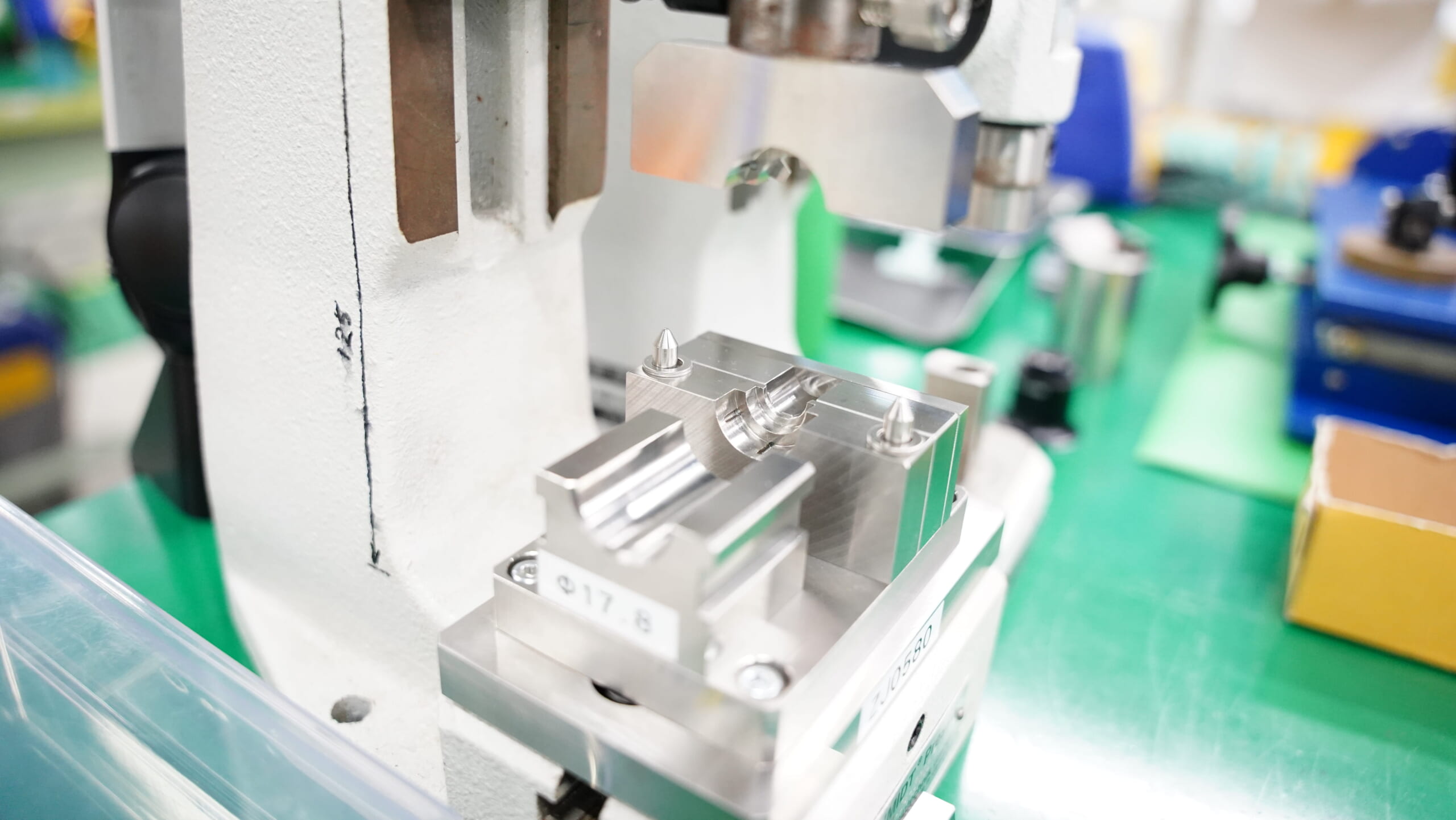
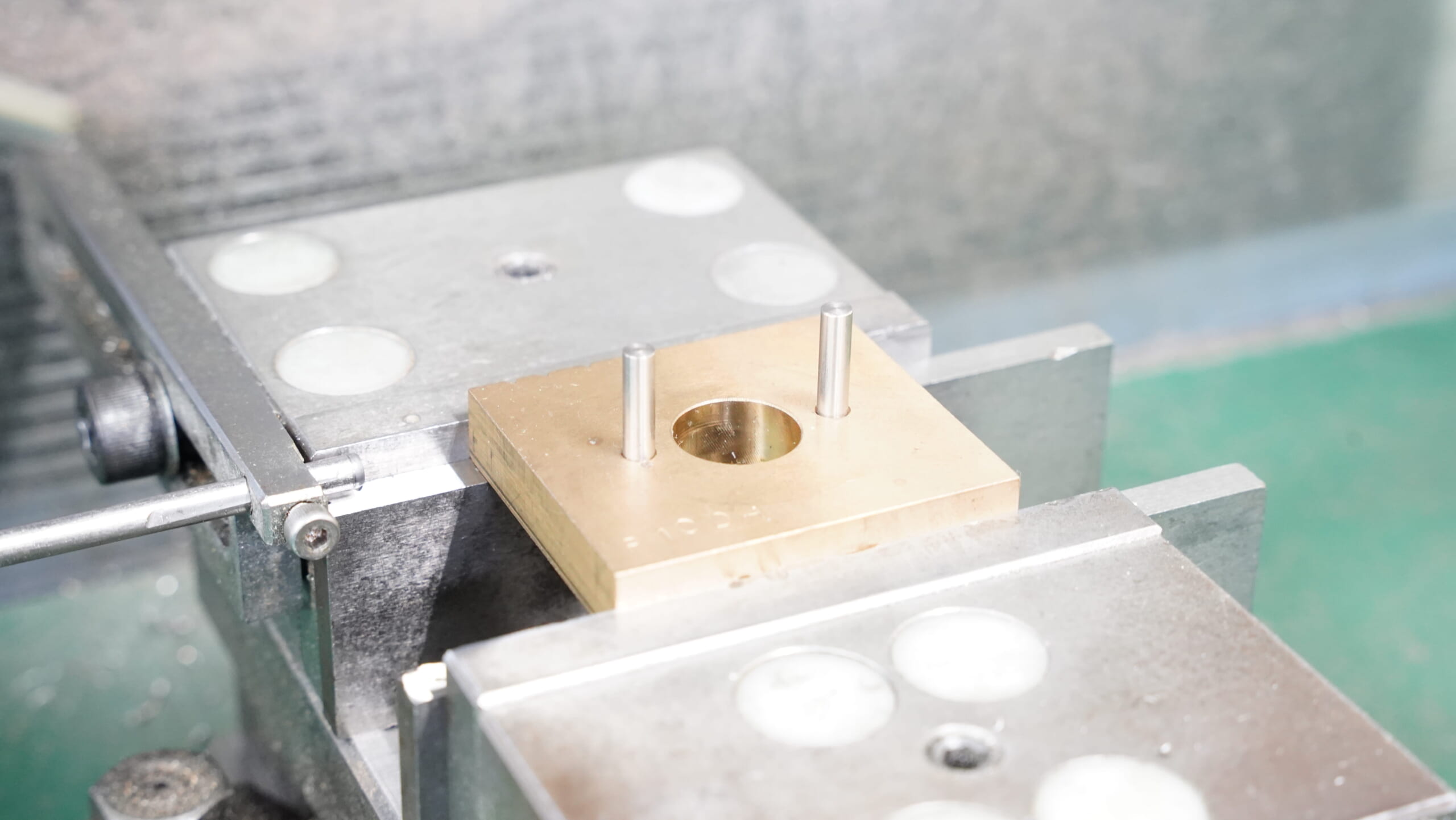
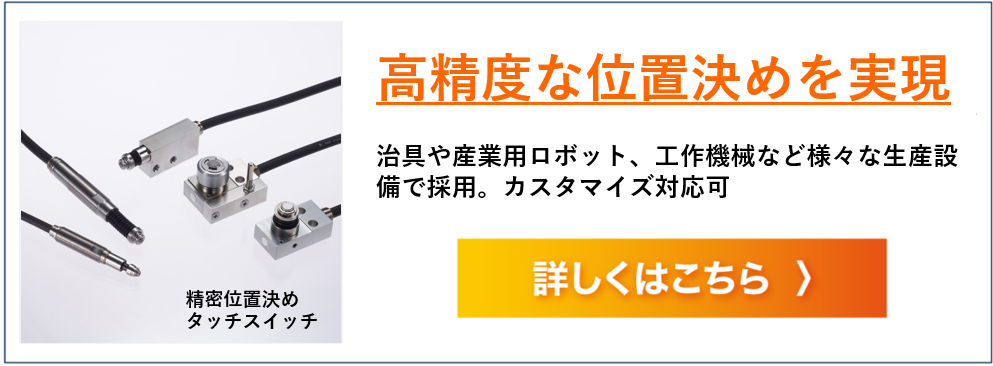

治具使用のメリット
治具を使用することには、様々なメリットがあります。以下にその主要なポイントを挙げてみます。
1. 精度の向上
治具を使用することで、部品の位置決めが正確に行えるため、加工精度が向上します。特に、微細な加工や複雑な形状の部品においては、治具の精度がそのまま製品の品質に直結します。
2. 生産性の向上
治具を使用することで、作業者が部品を手で保持する必要がなくなり、作業時間が短縮されます。また、治具は特定の工程に特化して設計されるため、作業の標準化が進むことから、より効率的な生産が可能になります。
3. 安全性の向上
治具を使用することで、作業者が危険な場所に手を近づける必要がなくなるため、作業環境の安全性が向上します。特に、重い部品や鋭利な部品を扱う場合、治具がそのリスクを軽減します。
4. 品質の安定
治具を使用することで、作業が標準化され、作業者によるばらつきが減少します。これにより、製品の品質が安定し、顧客満足度の向上につながります。
5. コスト削減
初期投資が必要ですが、治具を使用することで加工時間が短縮され、結果的にコストが削減されます。特に大量生産においては、治具の効果が顕著に現れます。
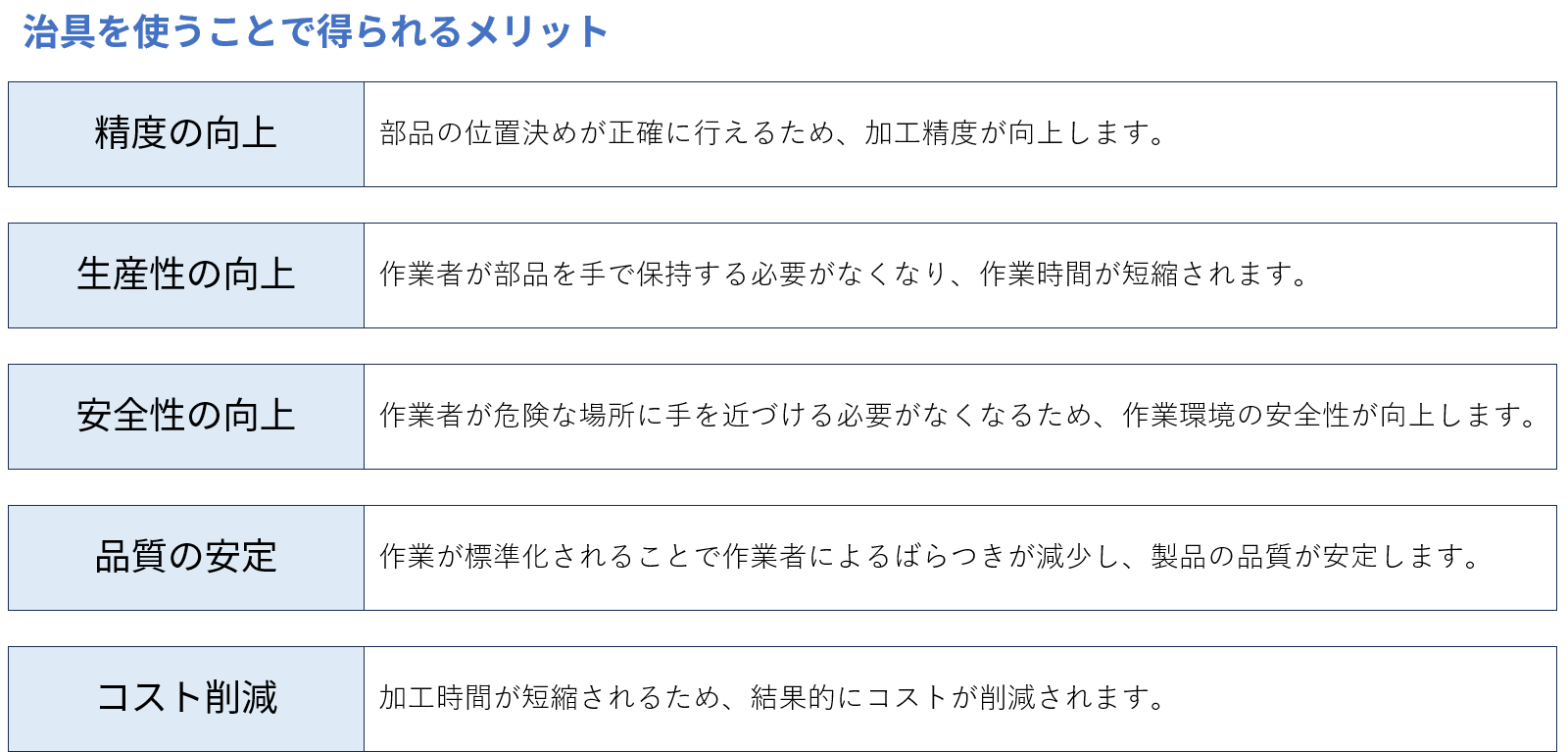
治具の種類
治具は、その目的や用途に応じて多くの種類があります。以下に代表的な治具の種類を紹介します。
1. 固定治具
部品を一定の位置に固定するための治具です。
最も一般的な治具であり、加工時に部品が動かないように保持します。
例えば、穴あけ治具や切削治具などがあります。
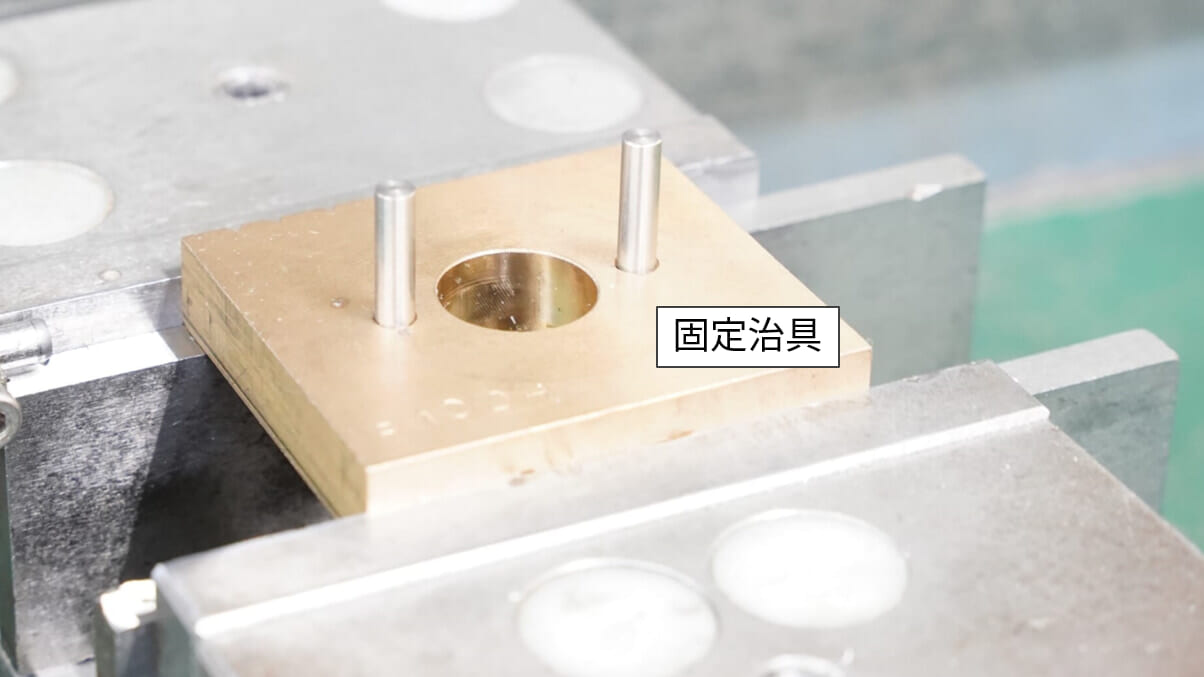
2. 組立治具
部品を組み立てる際に使用される治具です。
部品の位置決めを行い、正確に組み立てるためのサポートをします。特に自動車や電子機器の製造において重要な役割を果たします。
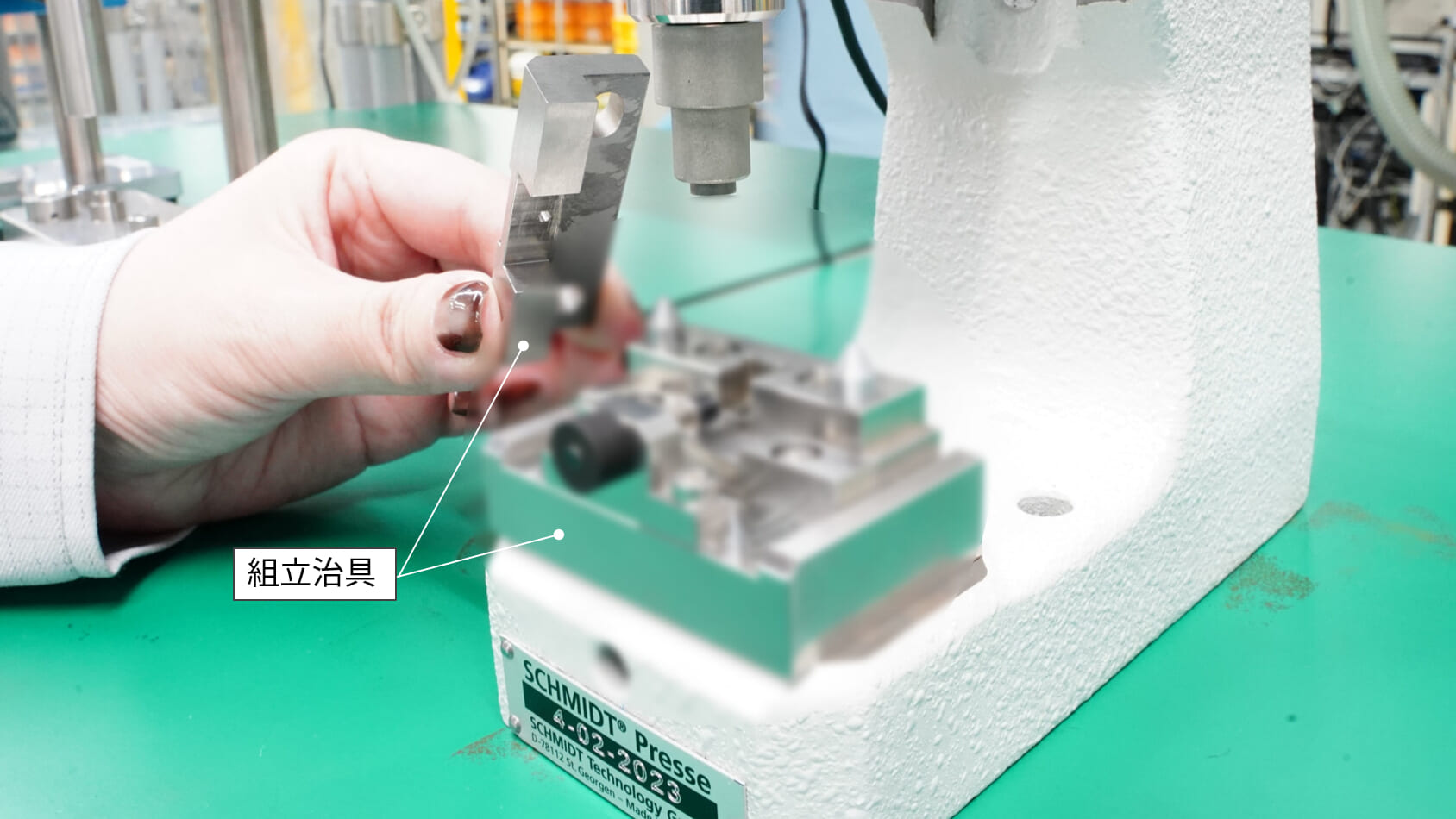
3. 溶接治具
溶接作業を行う際に、部品を正確に位置決めするための治具です。
溶接部分の精度を確保するために使用され、特に大型部品や複雑な形状の部品において重要です。
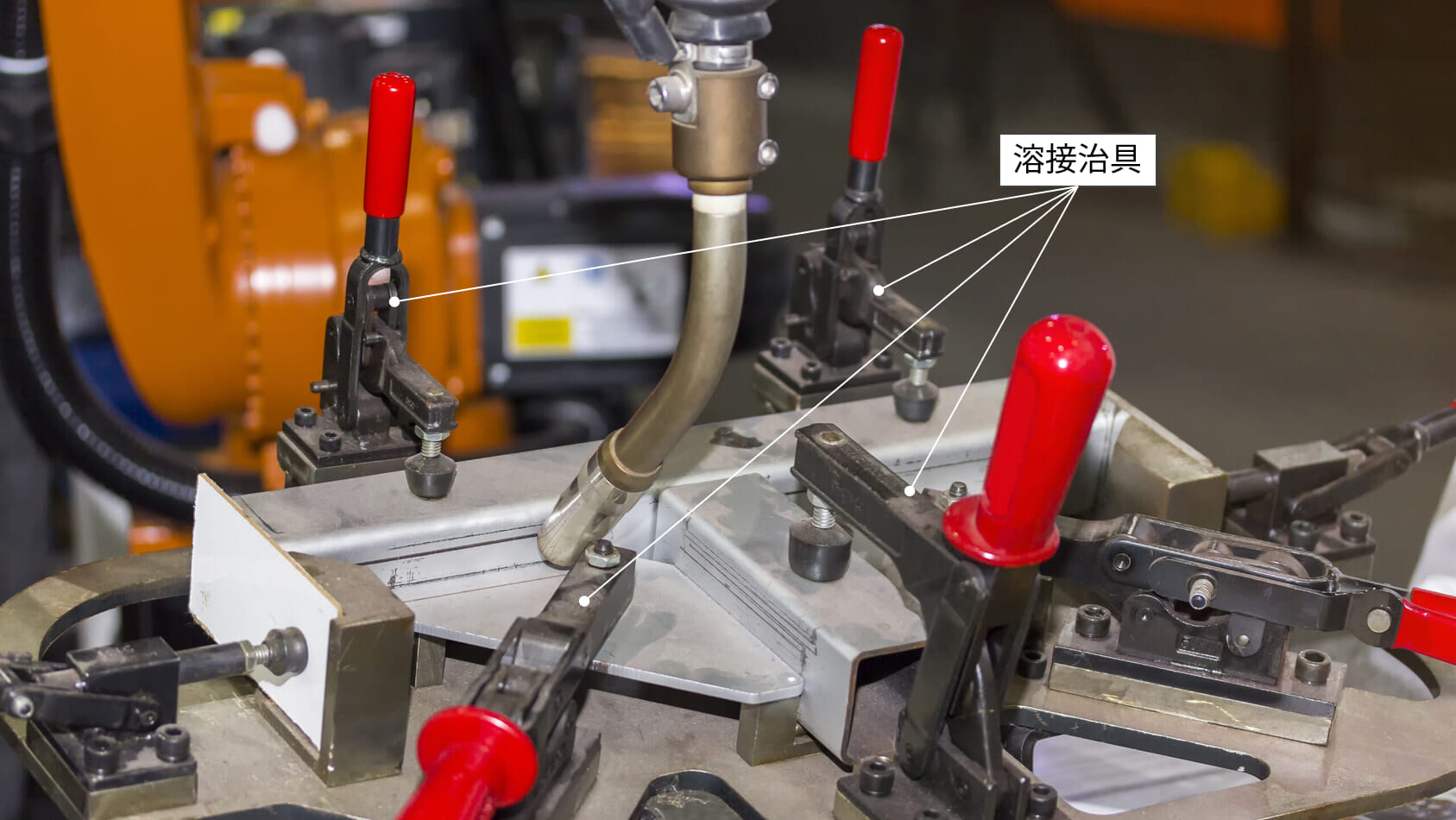
4. テスト治具
製品が仕様通りに機能するかどうかを確認するための治具です。
電気機器や機械部品の試験に使用され、性能評価を行う際に必要です。
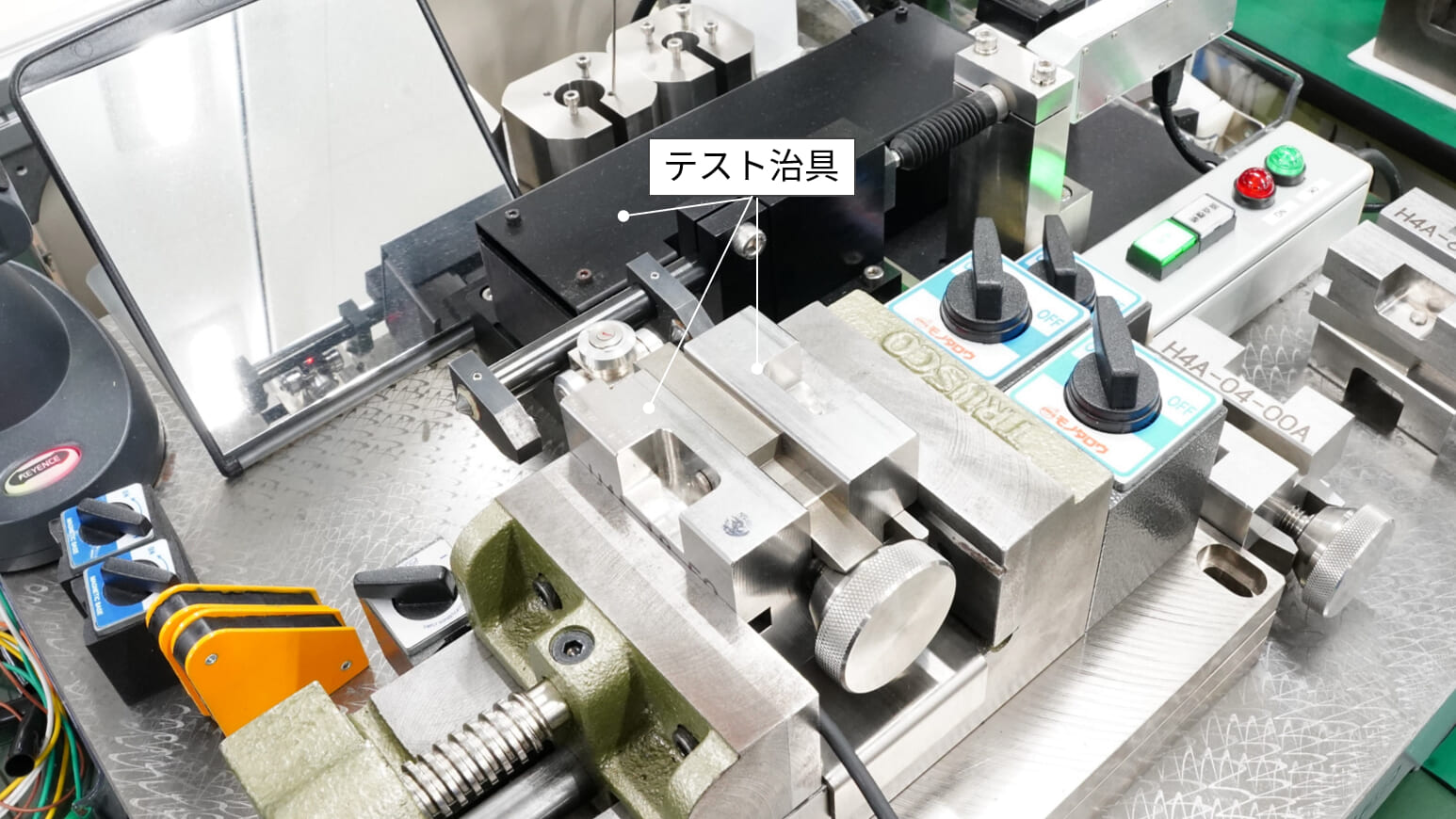
治具を使った加工例
治具を使用することで、さまざまな加工が効率的かつ高精度に行えます。以下に具体的な加工例を示します。
1. 穴あけ加工
治具を使用することで、部品を固定し、正確な位置に穴をあけることができます。
特に、高精度が求められる部品の場合、治具が不可欠です。例えば、航空機部品の製造においては、数ミリメートルの誤差が致命的な影響を及ぼすため、治具による精密な位置決めが重要です。
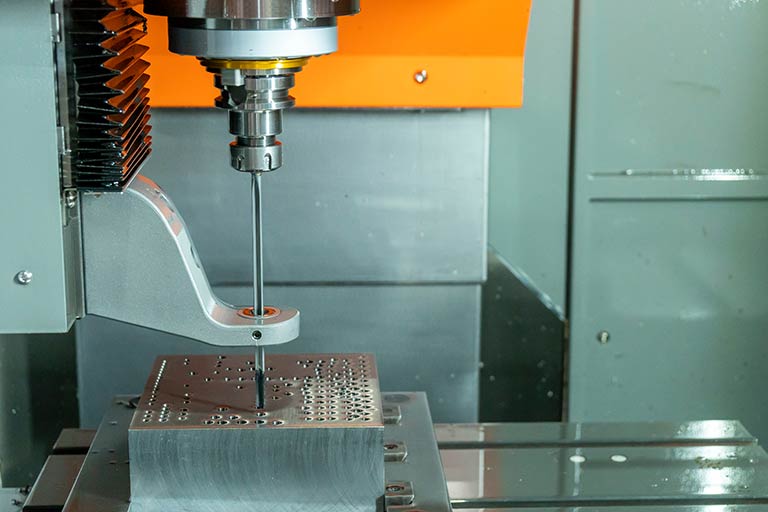
(画像出典:穴あけ加工とは?穴あけ加工と穴あけで使われるドリルを解説|『はじめの工作機械』)
2. 切削加工
切削加工においても、治具を使用することで安定した加工が可能になります。
例えば、金属の部品をフライス加工する際には、治具で部品をしっかりと固定することで、切削工具の動きがスムーズになり、精度が向上します。
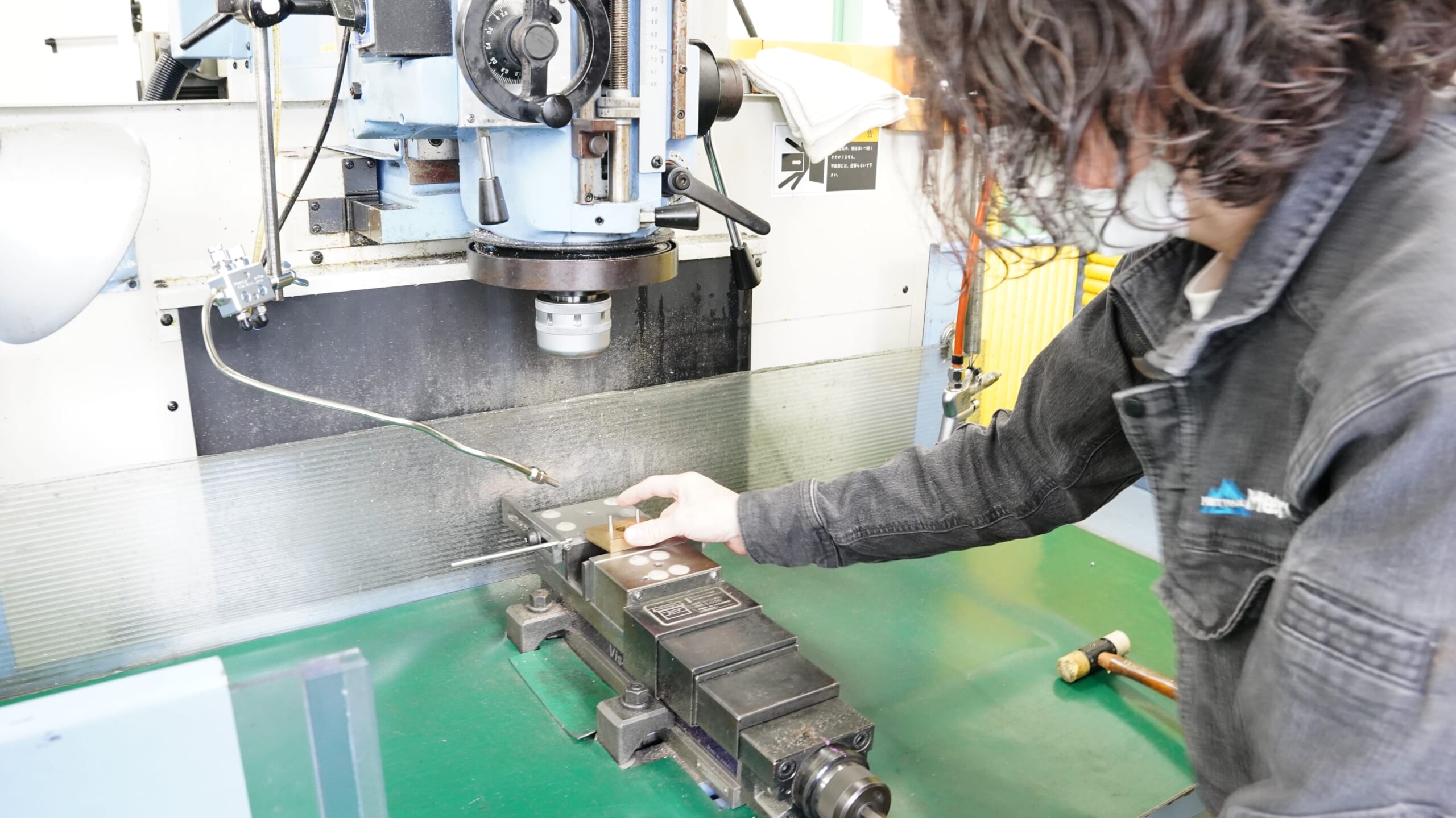
3. 溶接加工
溶接においては、治具を使用して部品の位置を固定することで、正確な溶接が可能になります。
特に、構造物やフレームの製造では、 治具が部品の位置を維持し、均一な溶接を実現します。
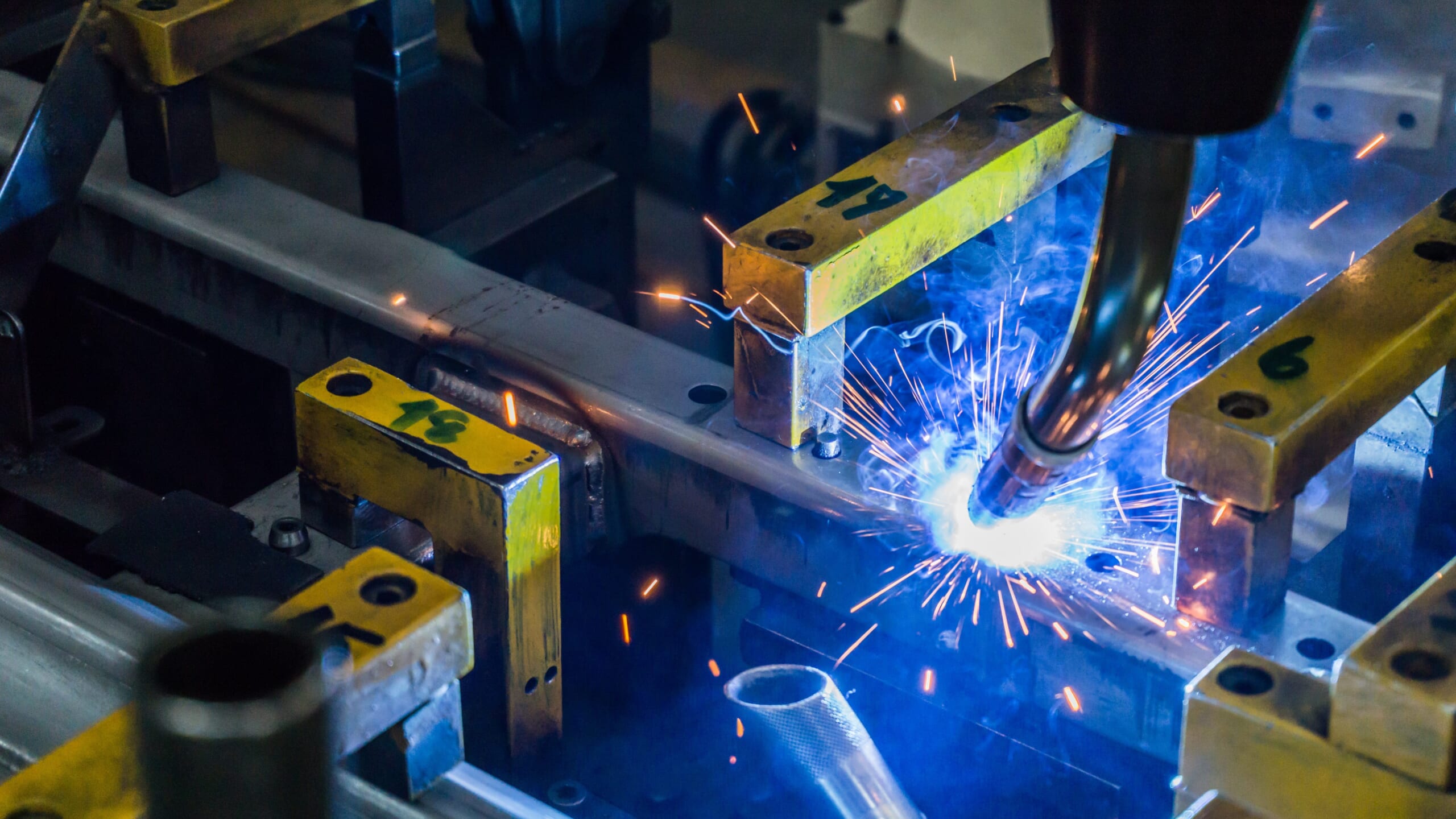
4. 組立加工
組立作業においても、治具を使うことで部品の位置決めが容易になり、効率的な組立が可能です。
例えば下の画像では、装置に取り付けた治具で部品を固定することで、別の部品を正確な角度で圧入することができます。治具がガイドの役割を果たし、スピーディーな組立作業に貢献します。
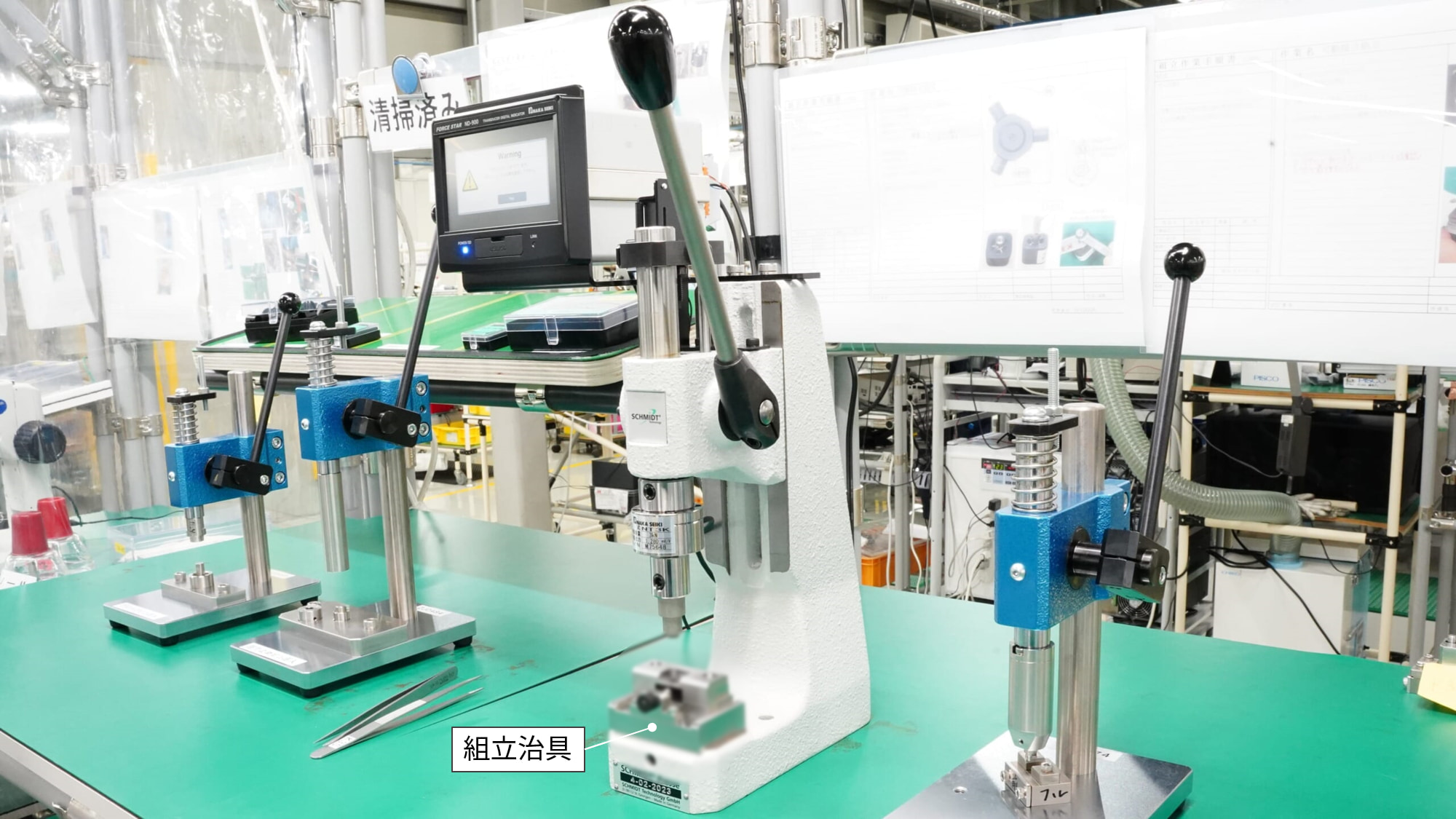

治具制作の流れ
治具の制作は、通常以下のような流れで行われます。
1. ニーズの確認
まず、どのような治具が必要かを明確にします。部品の仕様や加工精度、使用環境などの要件を確認します。
2. 設計
要件に基づいて治具の設計を行います。この段階では、CADソフトウェアを用いて治具の詳細な設計図を作成します。
3. 材料の選定
治具に使用する材料を選定します。耐久性や加工性、コストなどを考慮して最適な材料を決定します。
4. 加工
設計図に基づいて、材料を加工します。切削、溶接、組立などの工程が含まれます。
メトロールでは3Dプリンターを使って治具を製作することもあります。
5. 検査
完成した治具の検査を行い、設計通りに仕上がっているか確認します。必要に応じて修正を行います。
6. 納品と使用開始
検査が完了した治具を納品し、実際の製造現場で使用を開始します。治具の効果を確認し、必要に応じて改良を行うこともあります。
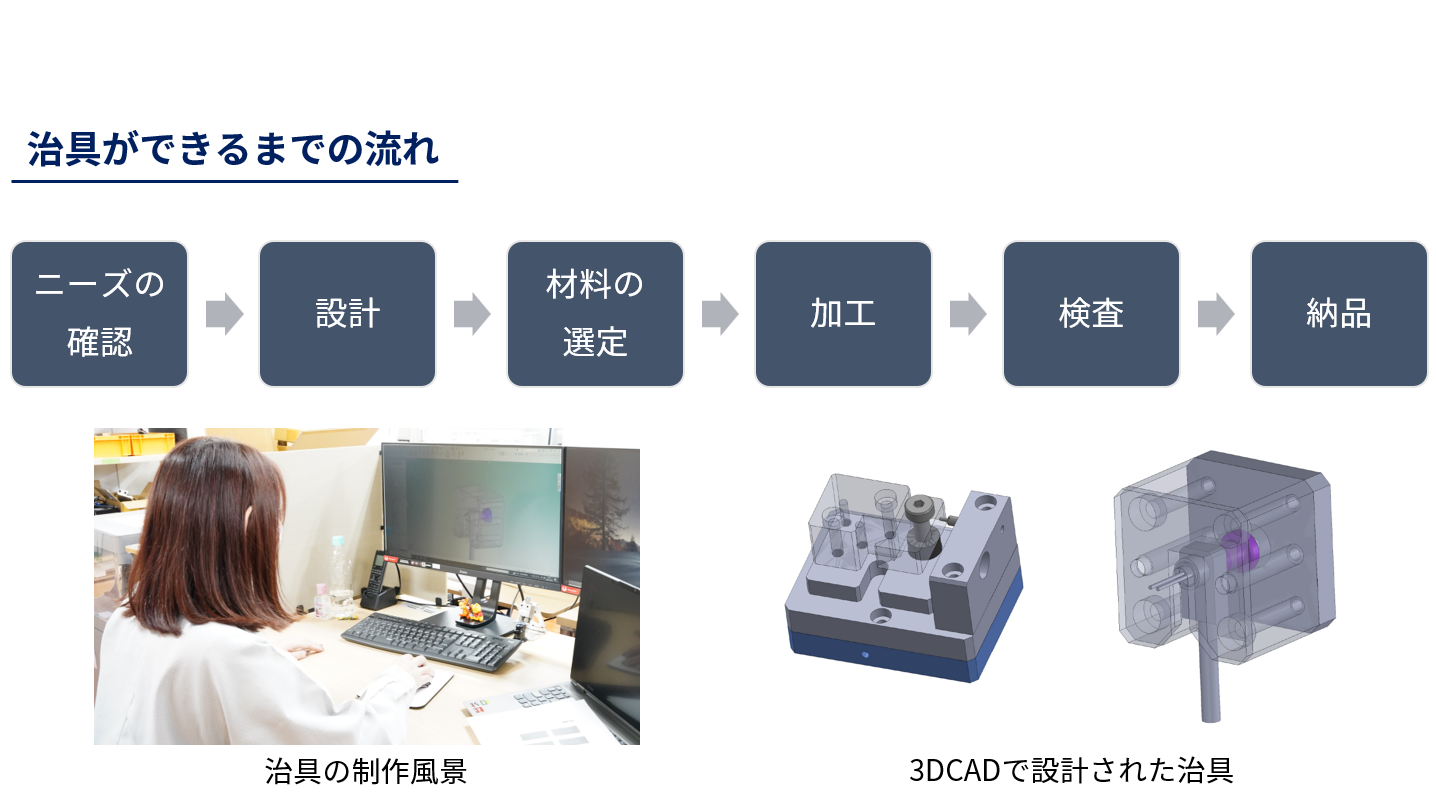
治具制作担当者の声: 治具制作のポイントは?
「安全」で「誰でもムラなく作業できること」を大前提に治具を設計しています。
次に重要なのは「費用対効果」です。具体的には、
・どれくらいの発注がある製品なのか
・どの程度の精度が求められるのか
などを考慮して、治具の構成や予算を決定します。
また、これまで人が行っていた作業を治具化する際には、作業者からの丁寧なヒアリングが不可欠です。
慣れた作業性に沿った治具構成でないと、部品の入れ忘れや作業手順飛ばしが頻発したり、作業の難しさから不満の声があがったりする可能性があります。
実際に使用する人が違和感を感じない治具づくりを大切にしています。
治具と工具の違い
治具と工具は、製造工程において重要な役割を果たしますが、それぞれの役割には明確な違いがあります。
治具
主に部品を固定したり、位置決めを行ったりするための器具です。 加工や組立作業を支援するために使用され、特定の部品に特化したものが多いです。
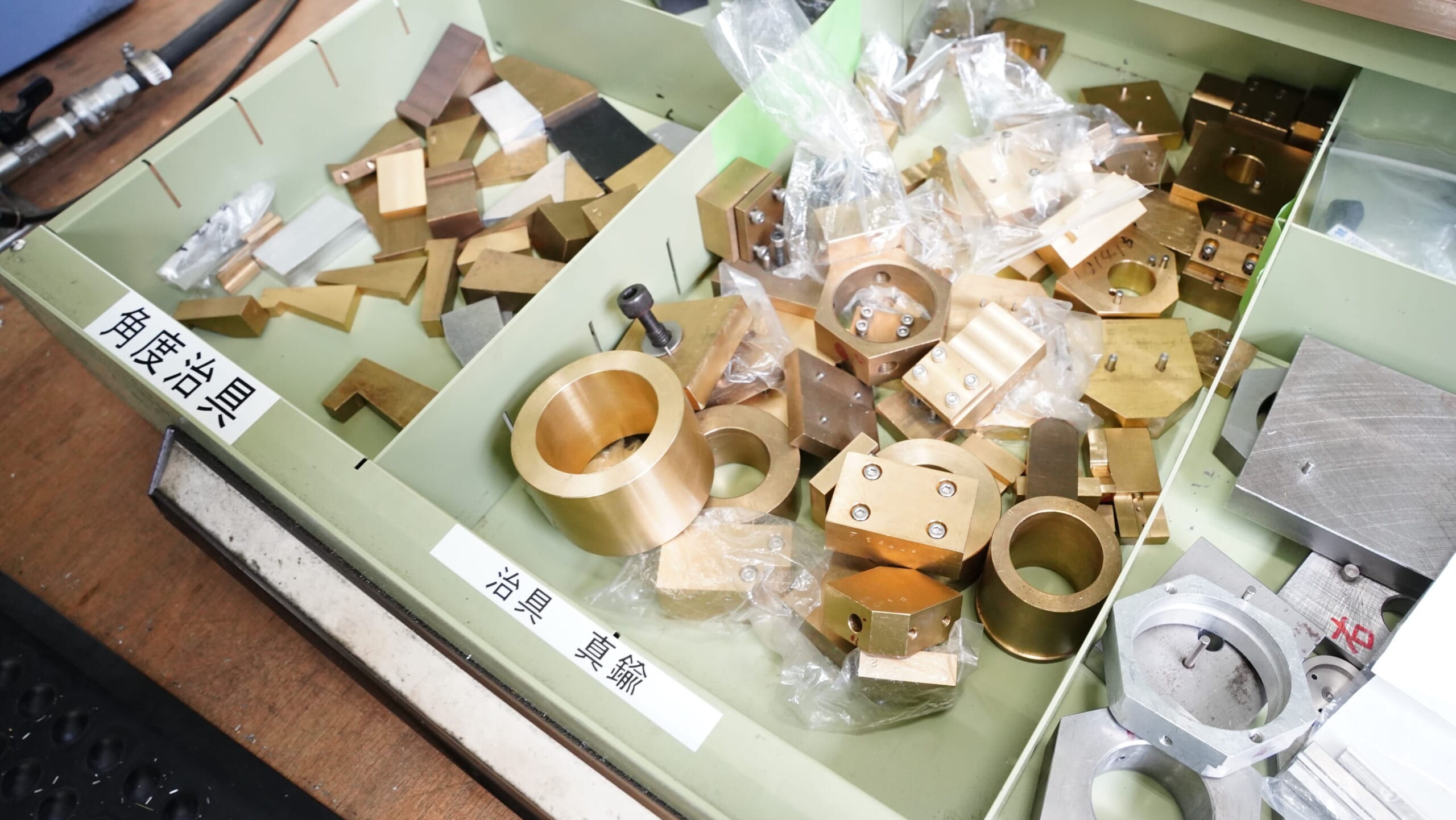
工具
一方、工具は主に加工を行うための器具です。ドリルやノコギリ、フライスなどが該当し、実際に材料を削ったり切断したりする役割を果たします。工具は、部品に直接作用します。
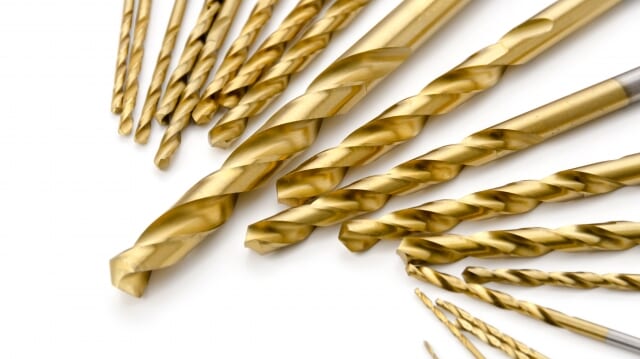
このように、治具と工具はそれぞれ異なる役割を持ち、製造現場において互いに補完し合う重要な要素です。治具を使用することで、工具の効果を最大限に引き出し、高品質な製品を効率的に生産することが可能になります。
治具へのセンサ活用事例
タッピングセンタでエンジン用ターボチャージャーを加工する際、加工テーブルの僅かなズレが、ターボチャージャーの品質に影響するため、悪環境下でも精度の高い位置決めができるセンサをお探しでした。
メトロールの「精密位置決めスイッチ」は、耐クーラント性の高いフッ素ゴムを採用した、密閉構造の接触式スイッチ。
切粉やクーラントが飛び散る工作機械の悪環境下でも、加工テーブルに直接接触し安定検知。0.5μmの繰返し精度で、ターボチャージャーの高精度加工が実現します。
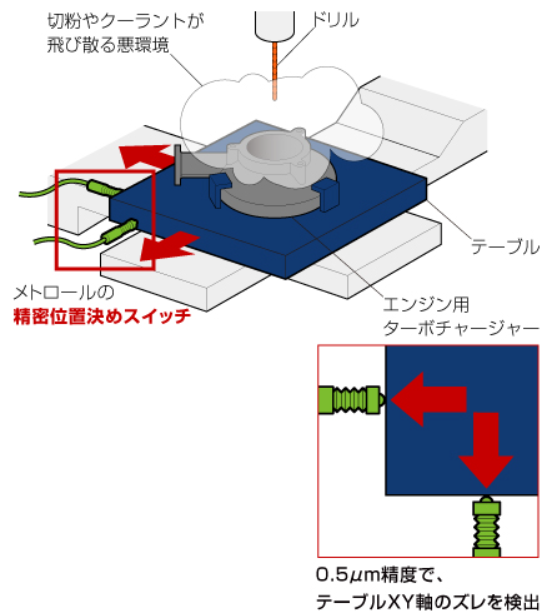
CNC工作機械の治具とワークの浮き上りを、非接触で安定検出
CNC工作機械の治具とワークの浮き上がりを非接触で安定検出する事例を紹介します。切削加工時に切粉が挟まることで浮き上がりが発生し、加工不良の原因となっていました。他社製のエアセンサは精度が低く、10μmの浮き上がりを安定して検出できませんでしたが、メトロールのエアマイクロセンサは±0.5μmの精度でこれを実現します。機内設置が可能でエア配管が短く、応答速度も0.8秒に向上し、生産性が大幅に改善されました。
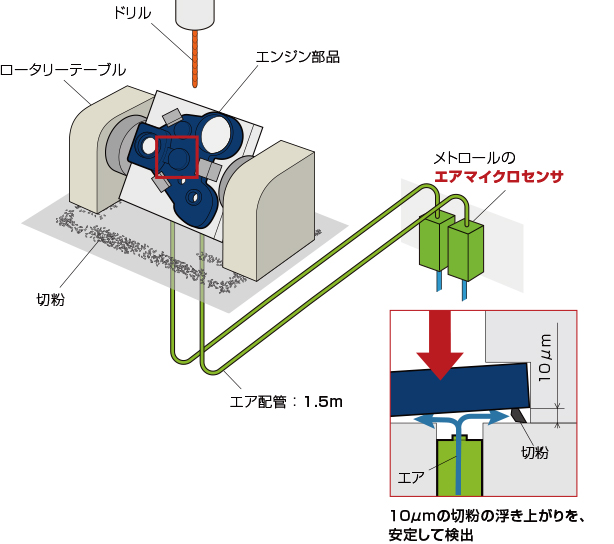
内面研削盤のワーク着座不良の検出で、 L寸不良の発生を未然に防止
バー材のL寸不良の問題と、メトロールのエアマイクロセンサがどのようにそれを防止できるかを説明しています。エアマイクロセンサは、工具とワークピースの間の10μm以下の隙間を検出できます。これにより、L寸不良の早期検出が可能になり、不良品の発生が防止されます。
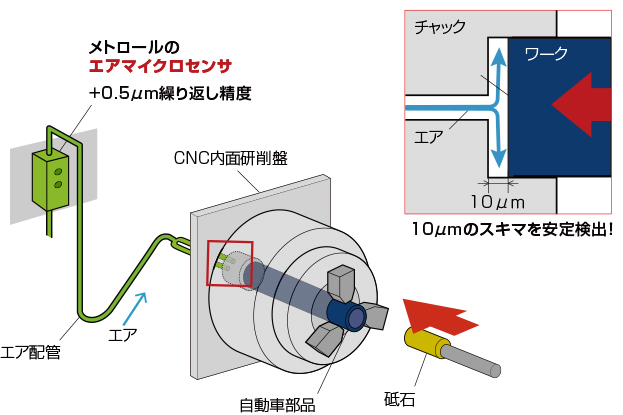

【動画】治具とワークのスキマを検知するセンサ
関連記事
【保存版】位置決め タッチスイッチの選び方と用語を徹底解説!
『位置決めタッチスイッチ』は、検出体に触れることでON/OFF信号を出力する接触式のセンサです。最も多く使われている用途は、検出体の着座確認や位置決めです。用途ではリミットスイッチやマイクロスイッチと似ていますが、精度・耐久性の面で大きく異なり悪環境下でも取り付けが可能です。
スイッチの種類によって動作方法、動作する位置、動作の動き、動作に必要な力が異なります。本記事では、タッチスイッチの選定に役立つ基本的な構造と用語について解説します。
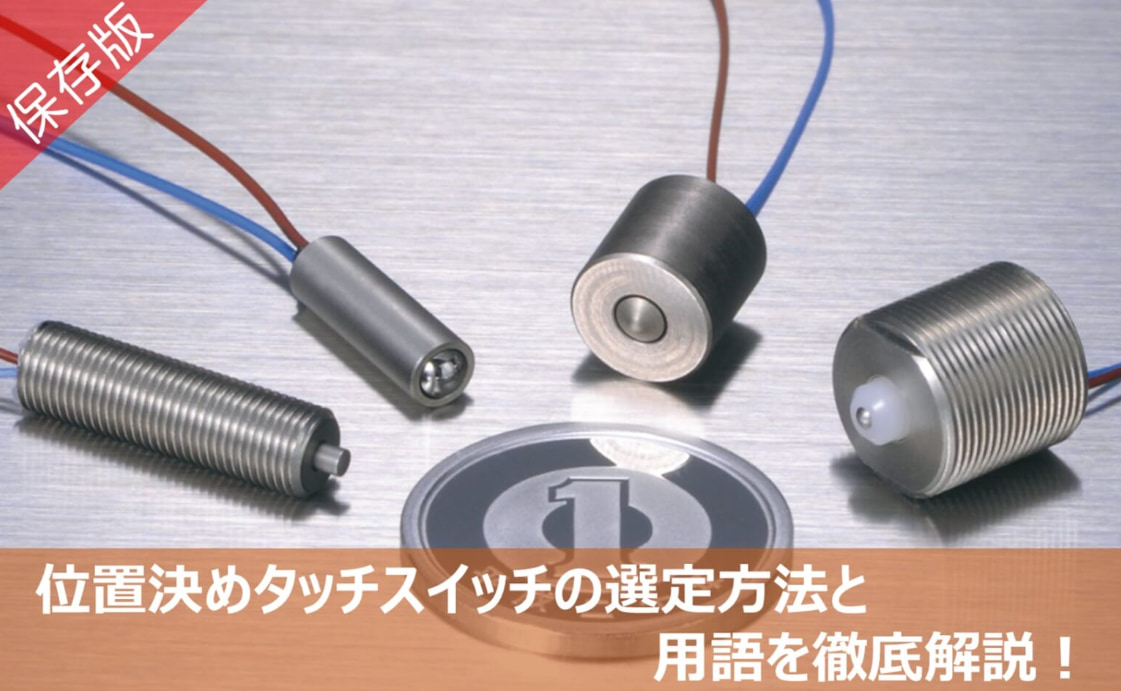