ワーク搬送でなぜ高精度な着座確認が必要なのか?
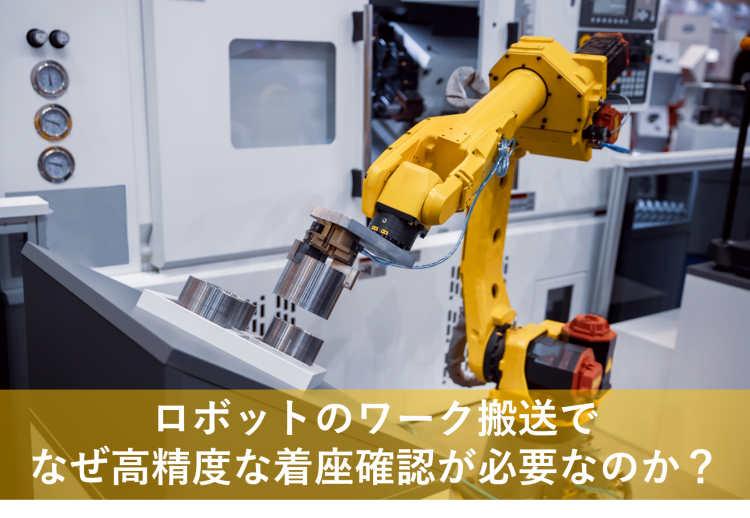
製造業の生産工程の省人化・自動化において産業ロボットは必要不可欠な存在となっています。
そんな産業ロボットの主な用途の1つに「ワーク搬送・着脱作業」があります。
本記事では「ロボットによるワーク搬送・着脱作業」にフォーカスし、その課題と改善策をご紹介します。
以下の方に参考となる記事になります。
- これから協働ロボットの導入を検討されている方
- 産業、協働ロボット×センサのアプリケーションでお悩みの方
- 着座確認用のセンサの選定でお悩みの設計者の方
目次
ロボットによる「ワーク搬送」とは?
人手による「ワークの段取り替え」は負担が大きく事故にも繋がるため、ロボットやローダーによる「ワーク搬送・脱着」が生産現場で急激に広がっています。
同時にロボットがワークを
- 「つかむ」
- 「治具に取り付ける」
- 「治具から外す」
- 「次工程に搬送する」
などの作業が増えています。
かつての、重量物を所定の場所に「置く、運ぶ」といった単純作業から、「精密動作が求められる加工現場」での導入ケースがますます増えてきています。
しかし精密加工では「ワークの精密な位置決め」が求められるため、
- 微小なワークのズレ
- 切粉による加工不良
などの問題が起きており、今までとは異なるニーズがロボット導入には求められています。
ロボットによる「ワーク搬送」の課題
ワークの正確な位置決めは、精密加工では大前提です。
ワークの着座時に起きる、位置ズレや傾きは加工不良の原因となります。
「ワークの段取り替え」において、こんな課題を抱いたことはないでしょうか?
- ワーク着座時の切粉の噛み込みによって加工不良が発生する
- ワークの有無確認はできるが、治具とワークのシビアな密着確認ができない
- センサ誤検知による機械のダウンタイムが発生している
作業者が毎回「着座確認」を行えば、着座時の微妙なズレ・浮き上がりを感覚や目視で判別できるかもしれません。
しかしロボットが脱着を行う場合、明確なしきい値をもって高精度に着座確認をしないと大量に加工不良がでるのではないか?という不安を抱える方も多いではないでしょうか
高精度な着座を安定検出する方法に、「エアマイクロセンサ」を使用した方法があります。
エアセンサを搭載することで、ワークの着座成功・失敗を容易に判定可能になります。
※本記事では高精度な着座確認を『隙間20μm以下の密着度』とします。
ワーク搬送・着座確認の検出方法
エアセンサとは?
エアセンサには「エアギャップセンサ」と「エアマイクロセンサ」の2種類があります。
共通点は、どちらもエアの流量から、『ワークの着座』を検出することができるセンサです。
「エアマイクロセンサ」と「エアギャップセンサ」は違いとは?
原理は似ていますが両センサは繰返し精度が大きく異なるため、使用用途が違います。
●エアギャップセンサ:ワークの有り無し検出が主な用途。(繰返し精度2~30µm。)
●エアマイクロセンサ:ワークと治具の密着確認が主な用途。(繰返し精度±0.5μm。)
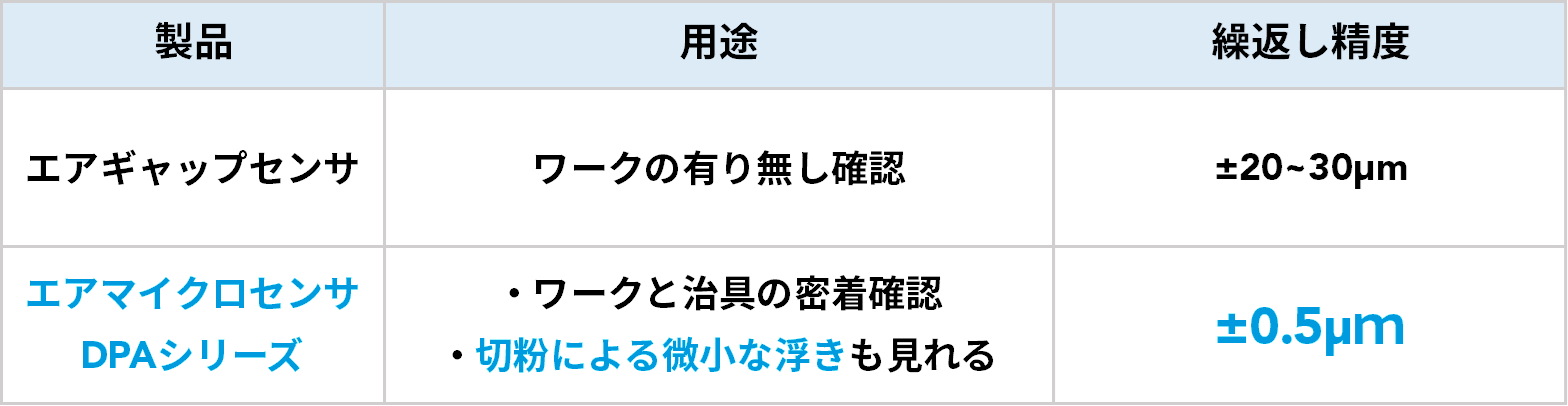
精度が違いによって起きる課題
「エアギャップセンサ」で精度の高い着座確認を行う場合、精度が安定せず、信号点がばらつきます。
そのため
- 微小な浮き上がりがあっても、着座成功の信号を出してしまい加工不良が起きる
- 着座成功しているにもかかわらず、着座失敗の信号でチョコ停が発生
などが発生します。
一方で、「エアマイクロセンサ」を使用すれば、これらの問題を未然に防ぐことが可能です。
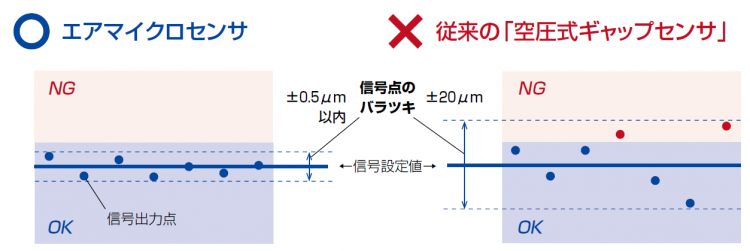
精度が異なるエアセンサの使用改善事例
エアギャップセンサとエアマイクロセンサを使用した事例をご紹介します。
※実際にセンサを採用されたお客様の改善を元にした事例になります。
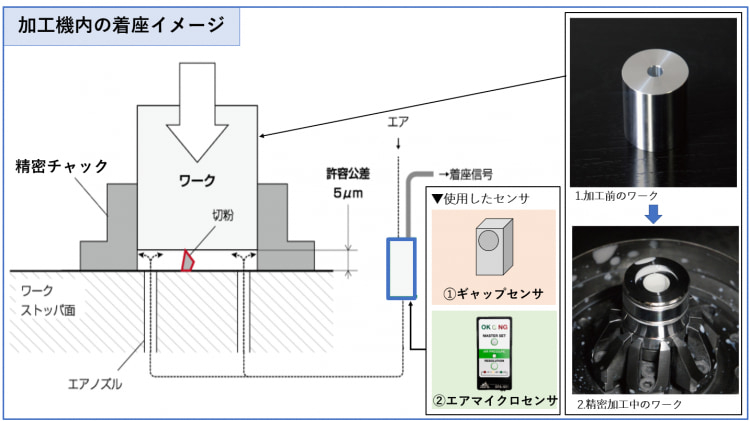

《解説する事例の設定》
ワーク | 画像1のような円筒形状のワーク(エンジン部品)を切削加工を行う | |
自動化ライン | 加工設備へロボットがワークを搬送し、加工が終わると後工程へさらに搬送する | |
センサ | 着座確認を以下の2パターンで行う | |
➀エアギャップセンサで着座確認を行った場合 | ②エアマイクロセンサで着座確認を行った場合 | |
求着座の要精度 | ワークと治具の隙間が5µm以下の着座確認が必要 | |
センサしきい値の設定 | ①②どちらも、隙間距離のしきい値は5µⅿで設定する この場合、以下のように判定信号を出力する ・隙間5µⅿ以下を着座成功(OK)と判定 ・隙間5µⅿを超えた浮き上りは全て着座不良(NG) と判定 ⇒着座不良を検知した場合は、設備を異常停止させる |
エアギャップセンサを使用した『ワーク搬送』事例
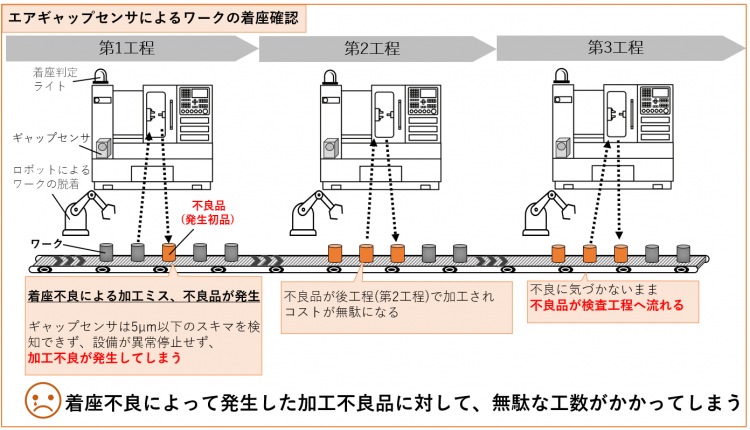
図1では前工程で着座不良による加工不良が発生、不良品を送り込まれた後工程は加工不良分のムダな作業を行っています。
また、検査工程で不良が発見されると、工程のラインストップにより歩留まりが低下、作業者の負荷も増えます。不良品がユーザへ流出する恐れもあります。
エアギャップセンサの場合は、切粉による5µⅿ以下のワークの浮き上りを安定して検知出来ません。
本来、着座不良があれば加工が始まる前に設備を停止させてワークをラインからはじく必要があります。
不良の発生は不良品の廃棄コスト、材料費、労務費などが損失しコスト問題の原因の1つです。
検査規格を変更せずに不良トラブルを改善するには、高精度な着座確認によって、不良を作らない仕組み作りが重要です
エアマイクロセンサを使用した『ワーク搬送』事例
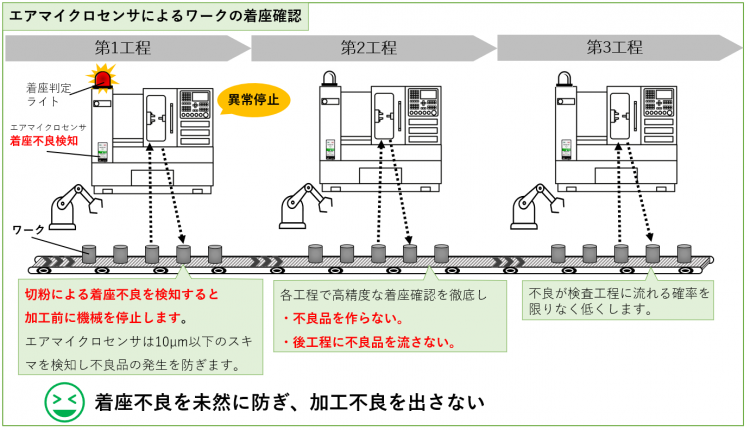
図2ではエアマイクロセンサを導入、着座不良による加工不良を未然に防止し自工程で不良を作らない、後工程に流さない仕組みが実現しています。
±0.5µmの繰り返し精度で、5µm以下のワークと治具のスキマを確実に検知出来ます。
着座不良(NG)の場合、設備がワークを削る前に停止するため、作業者は異常を確認する事が出来ます。
これにより検査工程の不良流出が減少し、歩留まりが大幅に向上しました。
検査工程の削減で自動化を実現
不良を出さない仕組みは検査工程においてもメリットがあります。
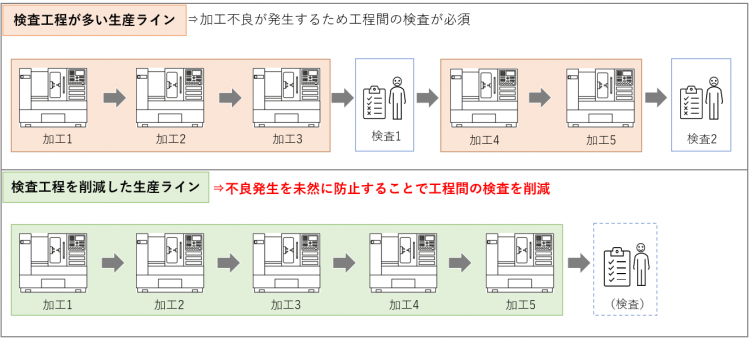
加工工程で不良が出なければ工程間の検査は不要であり、検査工数を減らすことができます。
加工工程間の検査は前後に仕掛品が滞留しやすく、自動化ラインにおいて極力削減すべきです。
工程間に検査が何度も入っては生産性も上がりません。
検査工程が少なく停滞のないストレートな生産ラインは、工場の自動化に貢献します。
【動画解説】協働ロボットによるワークの着座確認
協働ロボットとエアマイクロセンサを組み合わせた「ワーク搬送・脱着」をデモ動画でご紹介します。
先述した着座確認の事例を、「協働ロボット」を使用してを再現しています。
エアマイクロセンサによる着座確認の流れ、設定方法などご紹介します。
まずはこちらの動画をご覧ください。
【静止画解説】協働ロボットの着座確認
本章では、動画内容を静止画で詳しく解説しています。
◆動画の内容
⑴デモ機の構成
⑵ロボットの着座動作・エアマイクロセンサの判定について
⑶エアマイクロセンサの設定方法
デモ機の説明
デモ機を構成する設備は以下のようになります。
・協働ロボット
・ワーク
・着座用治具
・エアマイクロセンサ+着座判定用LED
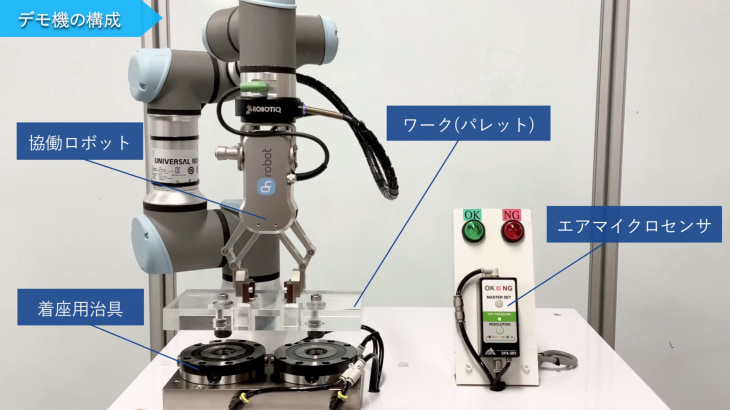
《デモ機の動作の説明》
協働ロボットがワークを搬送し、着座用治具にワークをクランプする工程を再現しています。
ロボットの先端についている「透明のブロック」が加工ワークやパレットを想定しています。
クランプの際に、エアマイクロセンサが着座の判定を行います。
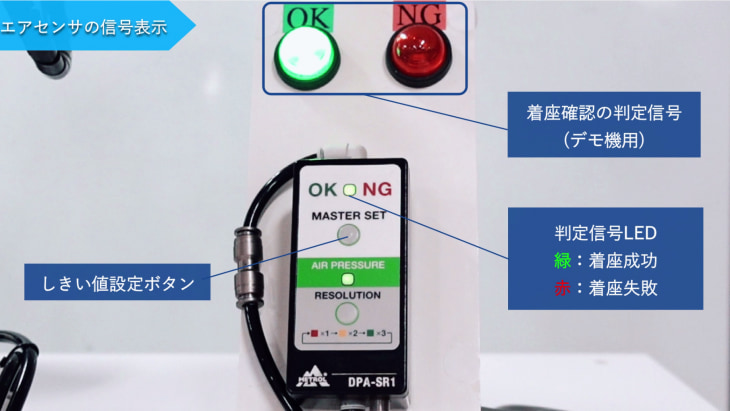
《エアマイクロセンサの説明》
①『着座確認の判定信号(デモ機用)』:センサの判定信号と連動し、OK/NGのLEDが点灯。
②『判定信号LED』 :判定結果を表示するLED 。 OK時は緑点灯、NG時は赤点灯。
③『しきい値設定ボタン』:着座時の隙間距離のしきい値を設定するボタン。
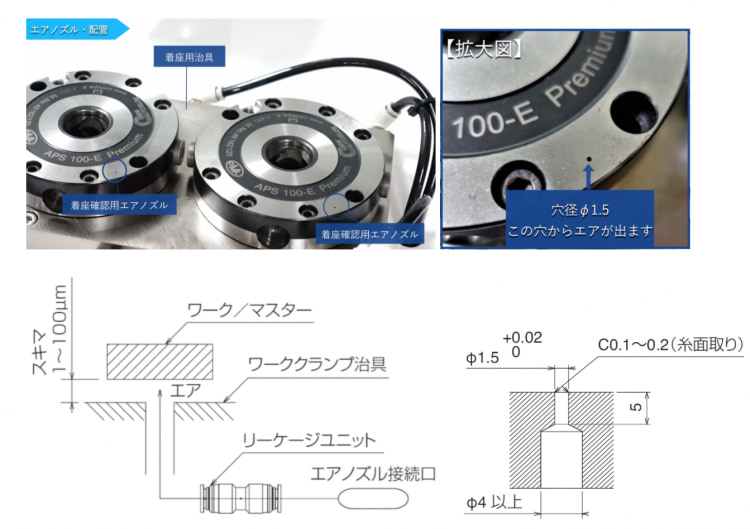
《着座用治具の説明》
ワークをクランプするための着座用治具です。
治具の着座面にはエアノズル用の穴が2ヵ所開いており、エアが吹き出ています。
ワークが治具に着座すると、ワークによってエア穴がふさがれます。このとき、エアの流量の変化をセンサが検知し着座を判定します。
ロボットの着座動作とエアマイクロセンサの表示
ロボットが治具へのワークを着座させてから、着座判定までの一連の動作を説明します。
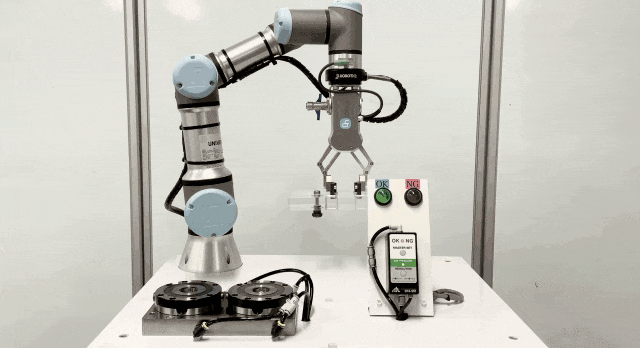
《一連の動作》
ロボットがワークを治具へ着座します。
着座時にワークと治具の隙間がしきい値を超えているかをエアマイクロセンサが検知しOK/NGの判定をします。
例えば、しきい値を10µmで設定した場合
隙間が10µm以下であれば着座OK、10µmを超える隙間が空いていれば、着座NGの判定をします。
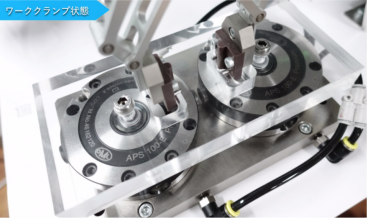
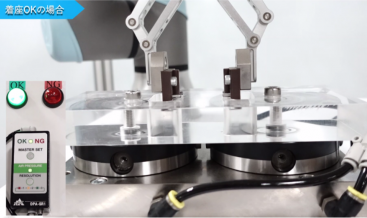
《着座OKの場合》
着座時にワークの浮き上りがなく、正常に着座されているためセンサは緑色のLEDのOK判定を表示。
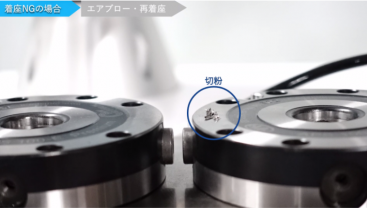
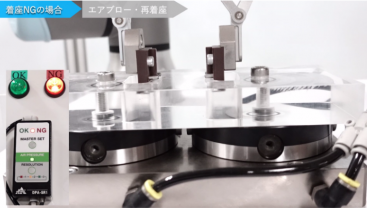
《着座NGの場合》
「切粉による浮き上がり」がしきい値を超える場合は、センサは赤色のLEDで着座NGを判定します。
拡大図のように治具の着座面に切粉があるとします。
切粉を噛みこむように着座させた場合、ワークと治具の隙間に浮き上がり生じます。
以上が、ユニバーサルロボットとエアマイクロセンサを組み合わせたアプリケーションです。
着座OK、着座NGによって、その後の動作をどのようにプログラムするかで生産性は変わります。
エアマイクロセンサの使用方法
エアマイクロセンサの特長の1つに、「ワンタッチで簡単にしきい値設定ができる」機能があります。
誰でも簡単に設定ができるので、複雑なオペレーションや引継ぎはいりません。
では、以下のイラスト例のように
しきい値を20µmで設定して、スキマが30µmの時にセンサが着座NGと判定できる設定方法を解説します。
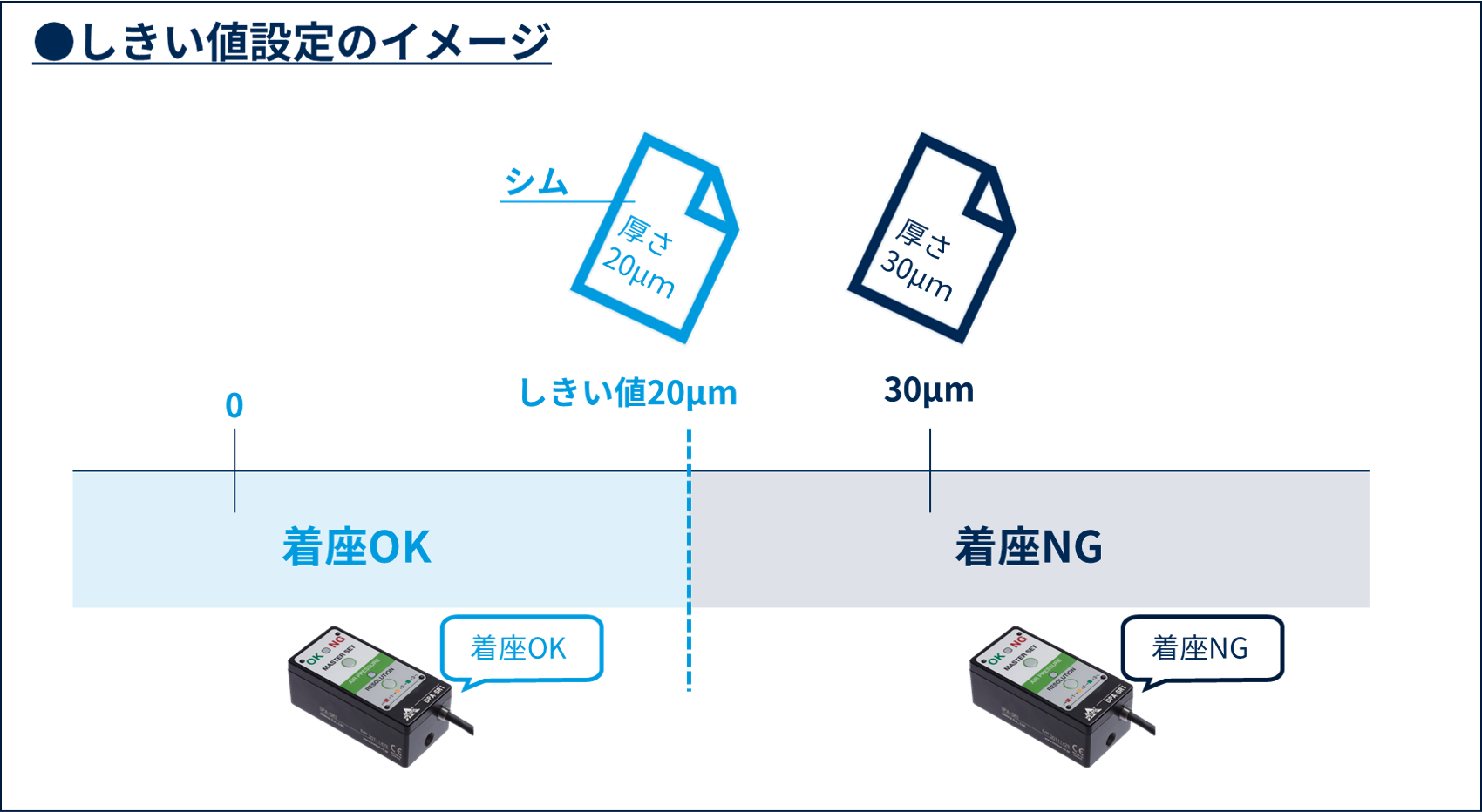
《用意するもの》
・しきい値設定用の20µmのマスターシム
・着座判定の確認用30µmのシム
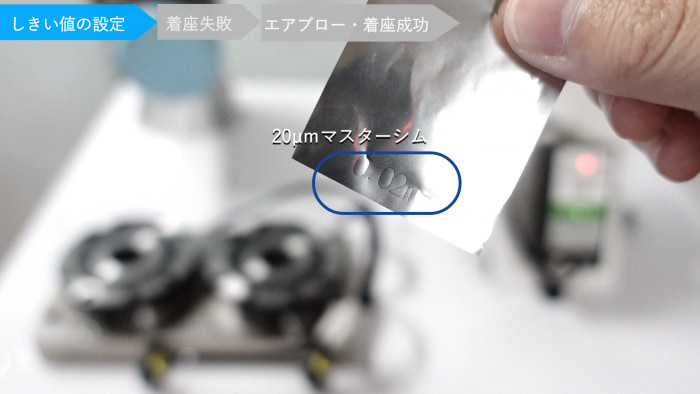
本事例では、20μmのシムを使用してしきい値を20µmで設定します。
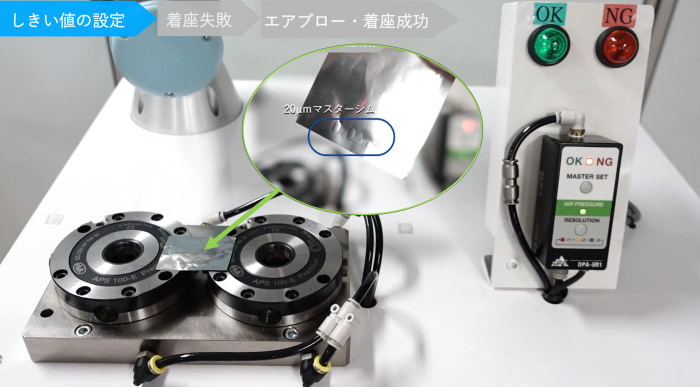
治具にシムを置きます。
このとき、着座時に治具とワークの間に20µmの隙間ができるようシムを挟みます。
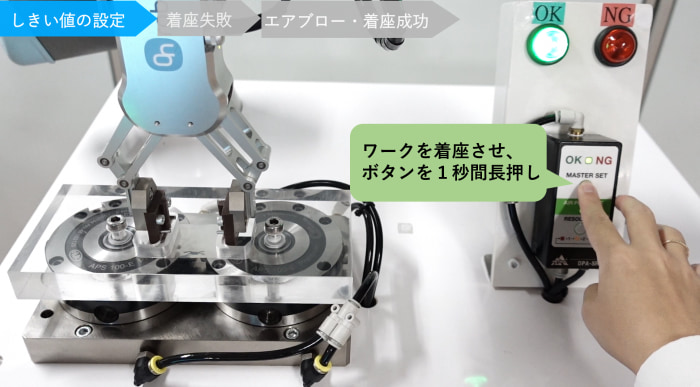
ワークを治具に着座させ、着座した状態でセンサのしきい値設定ボタンを1秒間長押しします。
20µmの隙間がある状態でボタンを押すと、隙間の距離20µmをセンサが記憶します。
エアセンサのLEDが点滅するとしきい値の設定が完了です。
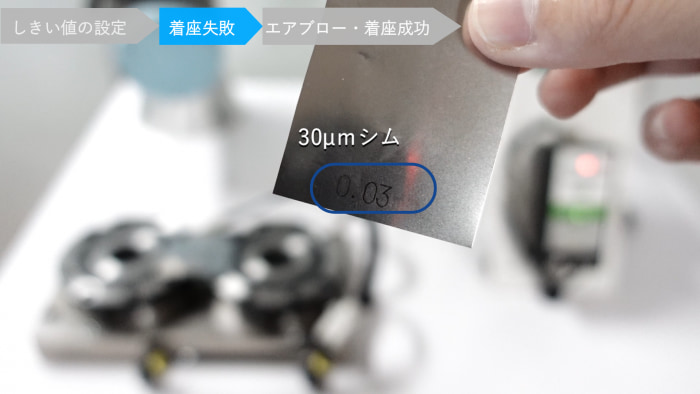
次に、しきい値の設定を確認するため、NG判定を再現します。
30µⅿのシムを使用し切粉による浮き上がり(着座不良)を再現します。
治具から20µⅿのシムを外し、30µⅿのシムと交換します。
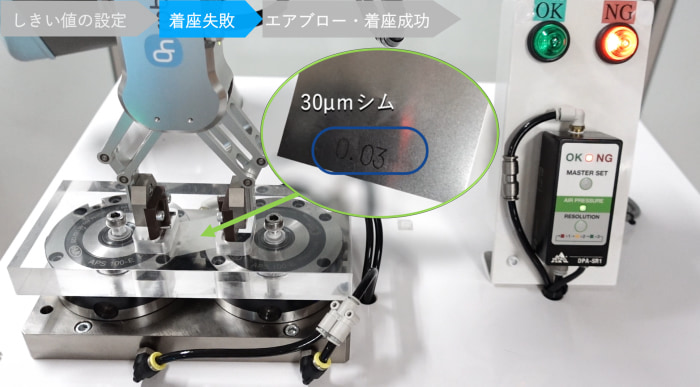
シムを置いた状態でワークを着座させます。
20µⅿのしきい値に対して、30µⅿの浮き上りがあるためNG判定を確認することができました。
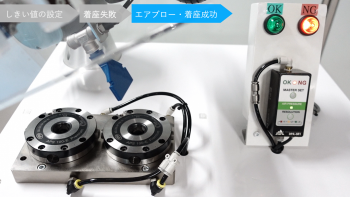
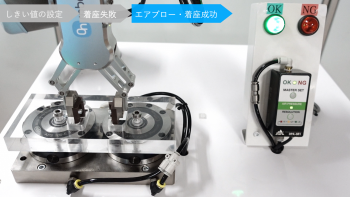
▲NG判定の場合、ロボットは治具をエアブローし、切粉を吹き飛ばします。
OK、NG判定後のロボットの動作はプログラム次第です。
本事例ではNG判定を検出すると、エアブローで治具表面を清掃し、再度ワークを着座させます。
切粉がなく正常な着座状態を確認できれば、センサはOK判定、加工をスタートします。
以上、産業・協働ロボットによるワーク搬送の着座確認でした。
ロボットによる生産ラインの自動化で、皆様のお役に立てますと幸いです。