【現場改善事例 Vol.1】ワークの精密着座確認で、CNC工作機械の加工不良品の発生をストップ
目次
株式会社デンソー様の「エアマイクロセンサ」採用事例
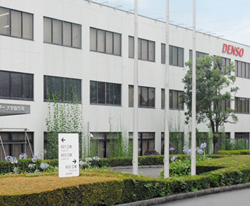
自動車の安全運転に欠かせない、ブレーキ部品やABS アクチュエータの製造を担う、株式会社デンソー 走行安全製造部。
そこでは、メトロールの「エアマイクロセンサ」が、ABS アクチュエータ部品の精密着座確認に、採用されています。
今回は、モノづくりの観点で、開発から量産・工程設計にまで携われている、生産技術室の村田様に、メトロールセンサ採用についてお話を伺いました。
ワークの着座不良に気づかず、加工不良品が発生
全数検査によるラインストップで、困っていた…
株式会社デンソー 走行安全製造部では、高い加工精度が要求される、ABS アクチュエータ部品を製造しています。
従来、CNCマシニングセンタで部品を切削加工をする際、空圧式の「ギャップセンサ」を使用し、
ワークとチャックの着座確認をされていました。
しかし、従来の空圧式「ギャップセンサ」の繰返し精度が、20 ~ 30μm と安定せず、切粉の挟み込みや、
ワークの浮き上がりが検知できず、着座不良による加工不良品の発生でお困りでした。
加工ワークはすべて全数検査するため、加工不良品を後工程に送ると、検査工程でラインがストップしてしまい、生産性が低下してしまいます。
村田様
従来の空圧式ギャップセンサでは、見れて20μm の着座が限界。
着座センサとは呼ばず、〔ワーク有り無しセンサ〕と呼んでいました。
後工程には良品しか流さない、削る前に不具合に気づく技術 を目指し、今までにない、ワークの着座不良の検出方法を模索していました。
その要求精度は、ナント5μm
「量産精度ではない…」と言われながらも、チャックメーカーと共同で、新たなワークの着座確認の開発に乗り出されていました。
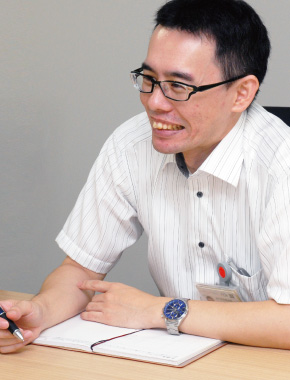
走行安全製造部 村田 祥一 様
課題
- 従来の空圧式「ギャップセンサ」は繰返し精度が20μm と低く、
ワークチャック時の精密着座が検出できない。 - 加工不良により全数検査でラインがストップし、生産性が低下。
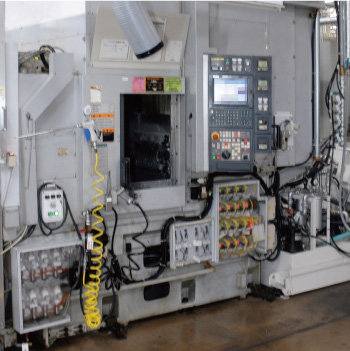
まずは、精密ダイアフラムチャックにより、精度の高いチャッキングを実現。残るZ 軸の着座精度が課題だった
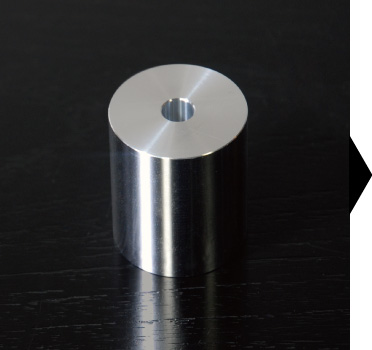
加工不良の発生を未然に防止する為、5μm の着座精度が要求されていた
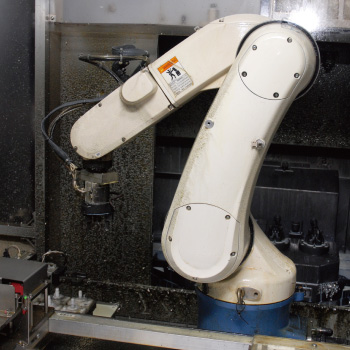
24 時間稼働のため、ワークの着座不良に気づかず加工を続けると、歩留まりが低くなり、生産性が低下
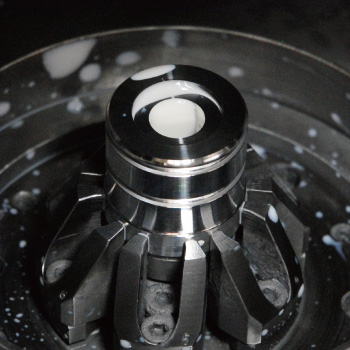
旋盤→穴あけ加工を経て、アクチュエータ部品へと加工されていく
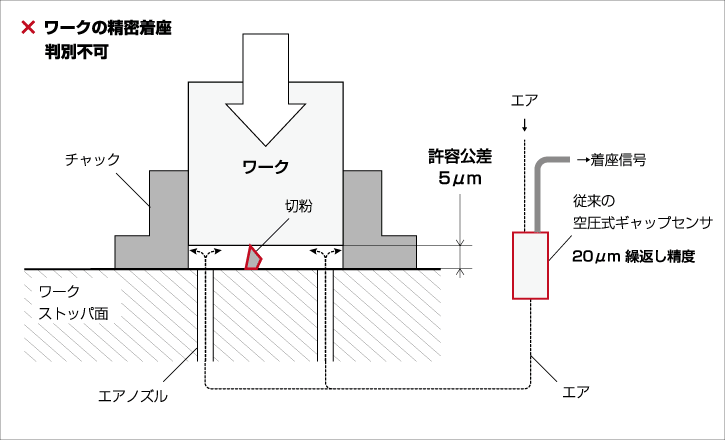
繰返し精度が20~30μm と低く、5μm の切粉によるワークの着座不良を検出できない
「まさに探していた精密着座センサ!?」展示会で発見!
チャックメーカーとともに、評価試験を開始
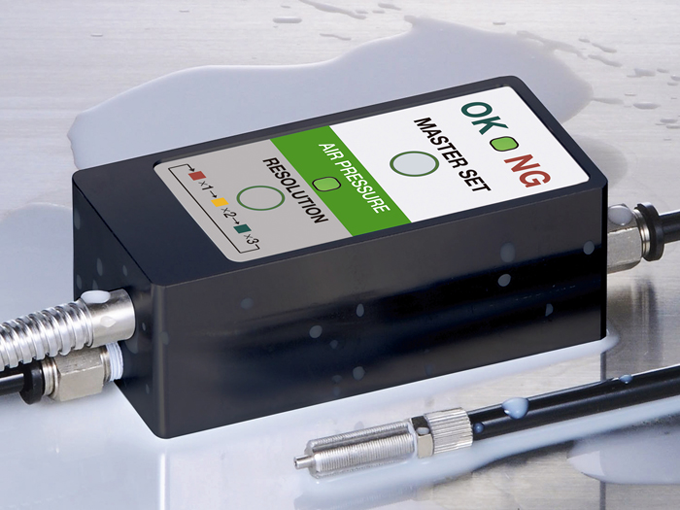
メトロール製センサ採用のキッカケは、2013 年 東京ビックサイトで開催された、〔 M-TECH 機械要素技術展 〕。
たまたま立ち寄られたメトロールのブースで、精密着座センサ「エアマイクロセンサ」のデモ実演をご覧になられ、その場でお問合せを頂きました。
村田様
展示会でエアマイクロセンサの着座デモを見て、
ピン!ときました。
まさに、探していた精密着座センサ。
すぐに試用サンプルをお願いし、チャックメーカーと一緒に評価試験を始めました。
従来、CNC 工作機械に採用されている、空圧式「ギャップセンサ」は、加工ワークの検出に使用されていますが、繰返し精度が20μm と低く、できてもせいぜいワークの有り無し確認が限界。
治具とワークの精密な着座確認はできませんでした。
デンソー社内の厳しい要求精度に、精密着座センサ「エアマイクロセンサ」が、見事にマッチしたのです。
切削加工をする前に、不具合に気づく技術!
生産工程の中に、加工不良品が発生しない仕組みを取り入れる
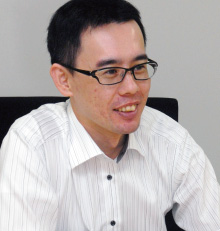
村田様
ホントに5μm の許容公差で、精密着座が見れるの!?
半信半疑でしたが、チャックメーカーでの評価結果は±1μm
聞いた瞬間、イケル!と思いました。
工作機械自体の精度も考慮しなければいけないので、
安定した精度を出すのは大変でしたが、加工ラインはこれで行く!
とスグに決めました。
その後、4ヶ月に渡る厳しい評価試験を経て、正式に加工ラインへの採用が決定。
切粉によるワークの着座不良を加工前に検出することで、加工不良品の発生を未然に防止。
検査工程のラインストップがなくなり、歩留まりが大幅向上しました。
まさに、「削る前に気づく!」を実現したのです。
効果
- 「エアマイクロセンサ」で、ワークチャック時の精密着座確認が実現。
- 加工不良品の発生を、生産工程の中で防止。生産性が大幅に向上。
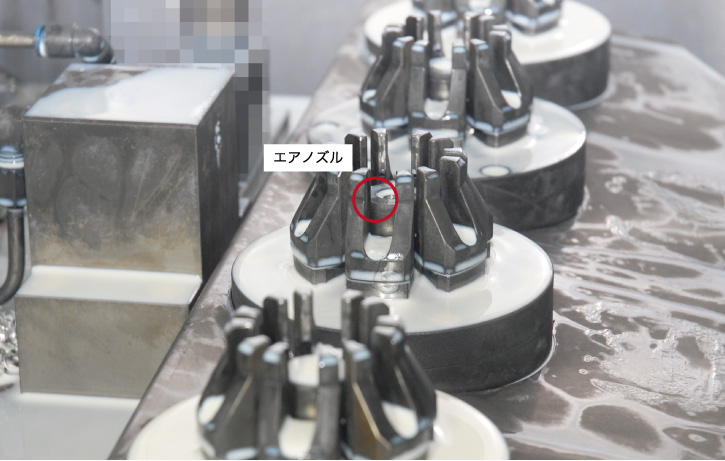
精密ダイアフラムチャック+精密着座センサ「エアマイクロセンサ」〈不良品撲滅の最強コンビ〉
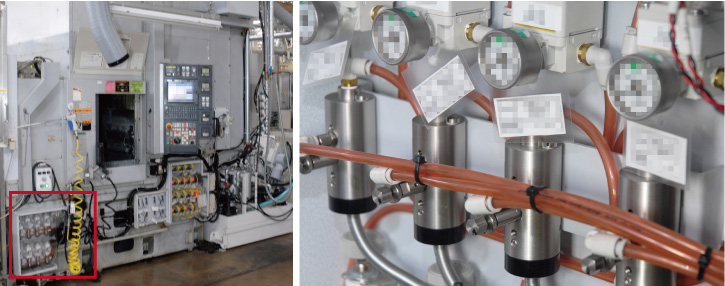
従来の空圧式「ギャップセンサ」のエア配管をそのまま流用、センサは後付けで入れ替えるだけ、工事は簡単。
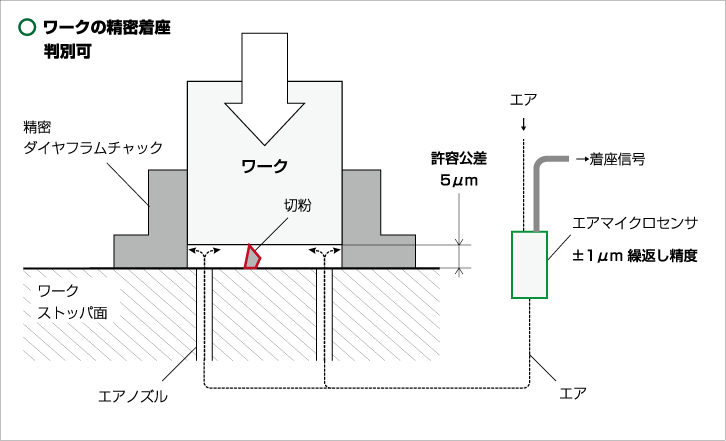
±1μm の繰返し精度で、5μm の切粉によるワークの着座不良を安定検出。
超精密加工と生産性向上へのチャレンジは続く
今回採用頂いた「エアマイクロセンサ」は、デンソー社内でも高い評価を頂き、現在では、他部署の加工ラインにもゾクゾクと採用、全社展開をして頂いています。

村田様
採用後は、トラブルなく稼働しています。
削る前の “着座不良” に確実に気づくことで、後工程へ不良品を流すことがなくなりました。
次の課題は、デジタル世代に合わせた新たな加工ラインづくり。
人と設備を融合させた、精度の高い部品加工を目指してチャレンジしています!
今後の村田様のご活躍に期待致します。
本日は、お話しありがとうございました。
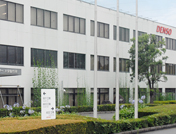
〔今回の取材ご協力先〕
株式会社デンソー 走行安全製造部
http://www.denso.co.jp