CNC自動旋盤、絶対に知っておきたい活用方法とは?
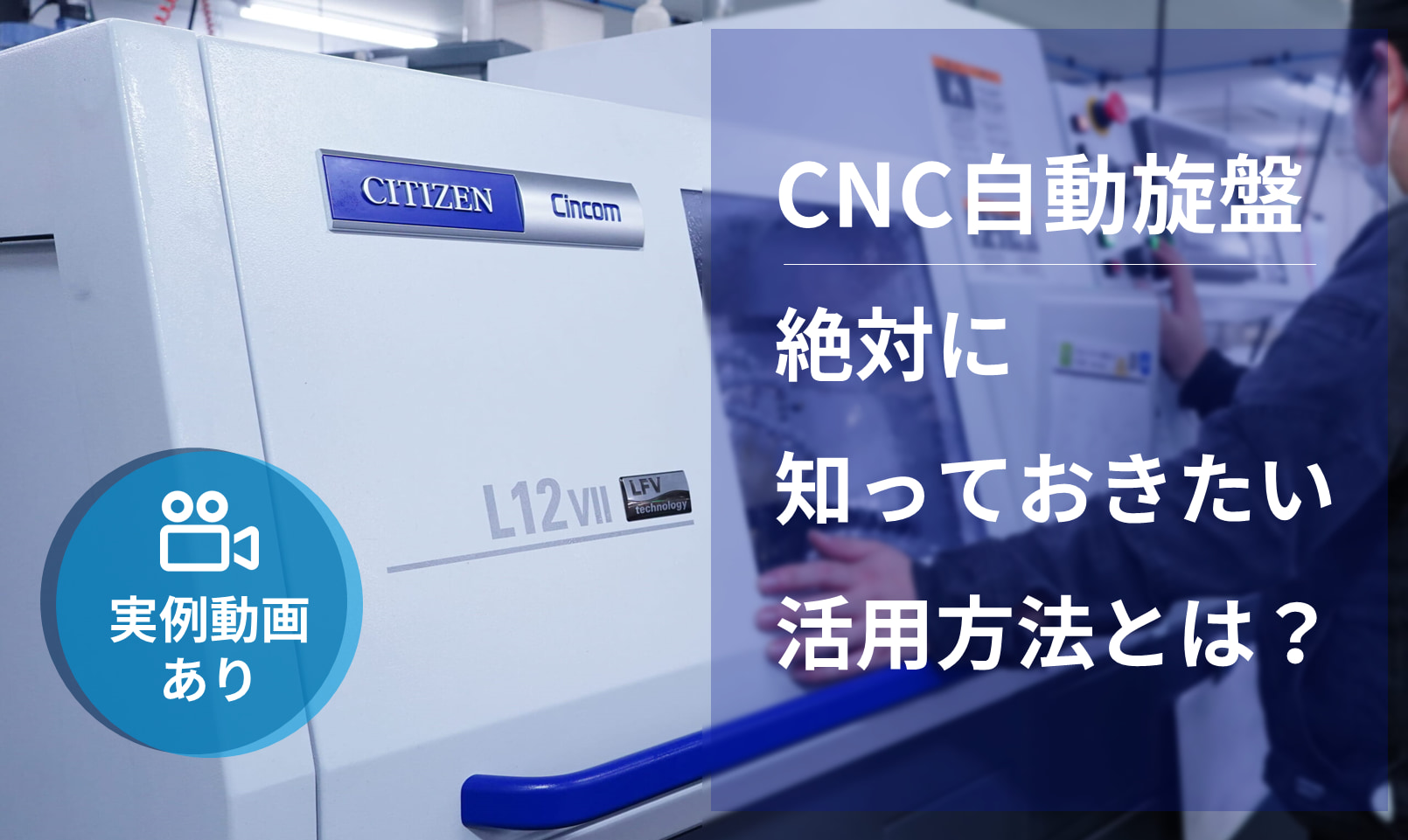
CNC旋盤の導入を検討している方は、以下のような悩みを持つ方も多いのではないでしょうか。
- 「機械を効果的に活用している他社の事例が知りたい」
- 「大量に作ったワークの全数検査で苦労している…」
- 「人件費の高騰で、加工・検査の工数を少しでも減らしたい…」
本記事では、 「CNC自動旋盤」の導入効果を最大化するために、効果的に運用する方法を解説します。
メトロールでもCNC自動旋盤は多数使用しており、その活用事例も一緒に伝えします。
CNC自動旋盤をすでにお持ちの方、これから導入される方はぜひ参考にしてください。
■本記事のポイント
・メトロールのCNC自動旋盤の導入事例がわかる
・CNC自動旋盤で行う機内計測のメリットがわかる
・自動旋盤での連続した加工不良を防ぐ方法がわかる
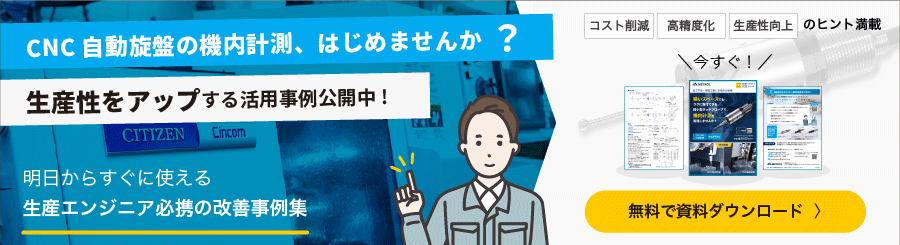
目次
メトロールがCNC自動旋盤Cincomを導入した経緯
メトロールは合計7台のCNC自動旋盤(シチズンマシナリー社のCNC自動旋盤Cincom L12、L20)を保有する装置ユーザーです。
NC機の導入目的は自社製品のパーツの内製化でした。
導入前は、外注・社内の汎用機で内製の2択でしたが、以下の理由から内製化に踏み切りました。
- 外注だとリードタイムが長く、ちょっとした仕様変更に対応できない。
- 品質管理がむずかしい
- 汎用機では数が作れない
- 社内にCNC加工に関するノウハウが蓄積されない
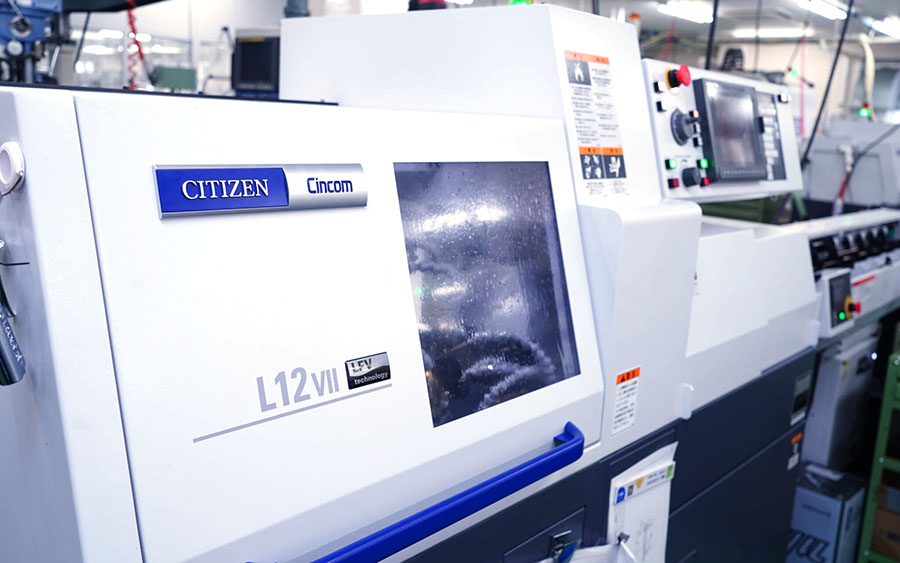
CNC自動旋盤でシチズンのCincomを選定した理由
数ある自動旋盤メーカーでも、シチズンマシナリー社のCincomシリーズを選定した理由は
- すでにCincomユーザであった協力会社から、トラブル時のサービスが速いと口コミがあった
- 初心者でも段替えやプログラムが扱いやすく、「少人数・多台掛け持ちスタイル」のメトロールでは使いやすいと判断
- CincomにはLFV(振動切削)機能がついており、切粉トラブルを回避しやすい
複数メーカーの装置を保有すると、その分オペレーションも増えてしまいます。
メトロールでは標準モデルで、同メーカーで装置を揃える方針で、シチズンマシナリー社のCincomを選定しました。
CNC自動旋盤を導入前に知っておくべき2つの課題
量産・自動運転が得意な自動旋盤では2つの課題と向き合わなければなりません。
それぞれ解説していきます。
課題1.自動運転で不良品を大量に作り続けてしまう
CNC自動旋盤では、一度不良が出始めてから良品に戻る可能性は低いため、不良がでたら可能な限り早く機械をストップし再発防止策を施すことが重要です。
例えば、1000個の部品を連続加工するとき、500個目から加工不良が出始めたとします。
すると、残りの500個は最悪の場合、全て加工不良となり材料費と加工時間がムダとなります。
「いつ(何個目から)加工不良が起きたか」が分からなければ、1000個全数の良否チェック工数も上乗せされます。
なぜ自動旋盤で加工不良が起きるのか?
加工不良の原因として以下の3つが一般的です。
- ツールのチッピングによる加工不良
- 熱変位による寸法不良
- 切粉のまきつきや噛みこみによる加工不良
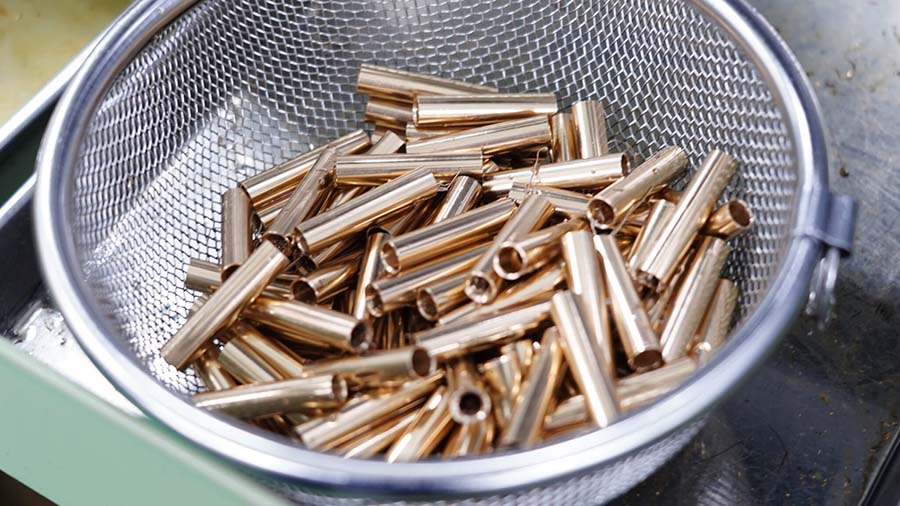
課題2.加工後のワーク検査工数と信頼性
当然ですが、たくさん作れば作った分だけ検査工数が増えます。
さらに測定器具を使って手作業で全数検査をする場合、以下のような課題があります。
- 検査員によって検査のやり方や力加減が微妙に違う
- 集中力の限界でヒューマンエラーが起きる
- 検査員の採用・育成コストがかかる
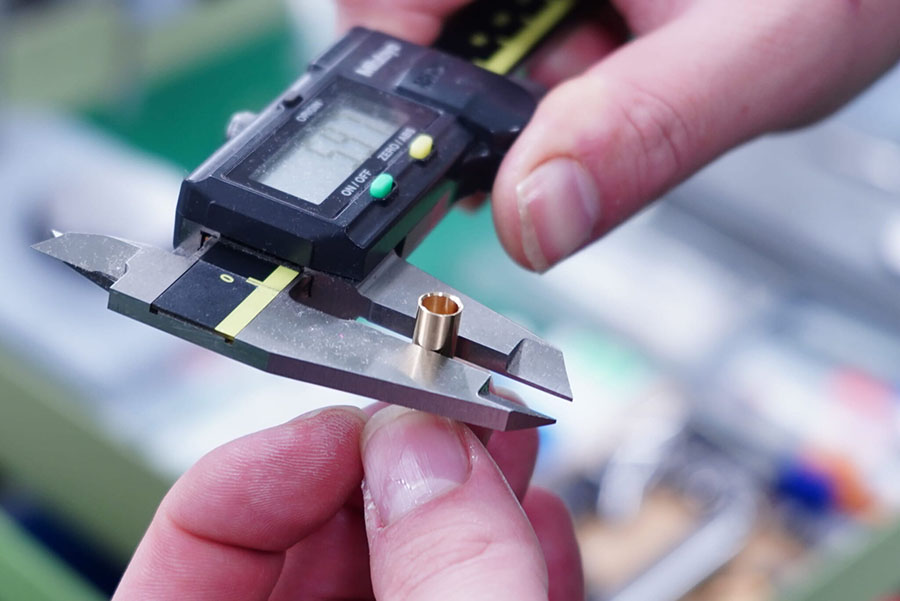
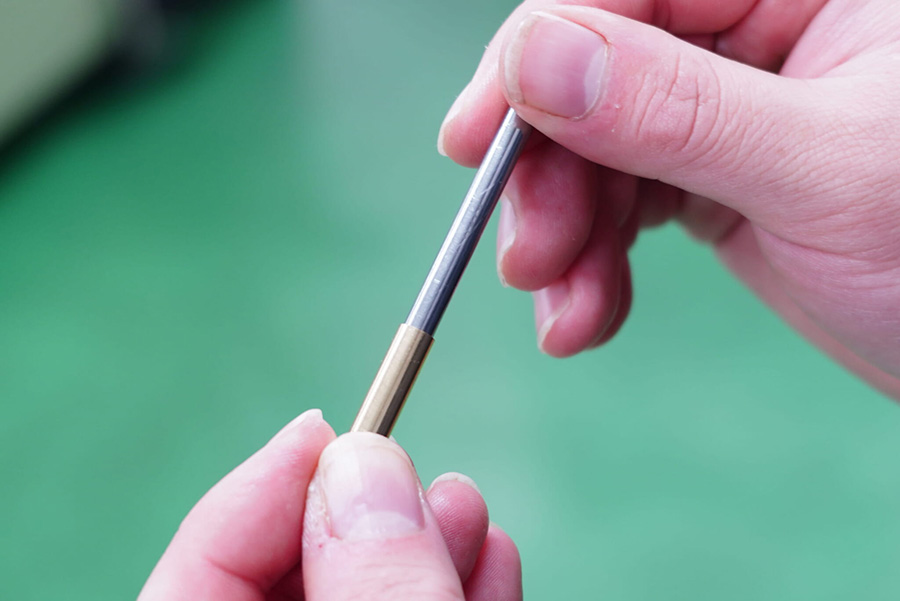
まとめ:CNC自動旋盤導入時の課題
CNC自動旋盤導入時の課題をまとめると、
- 不良品を大量に作り続けてしまう
- 加工不良の早期改善が難しくなる
- 不良品がでなくても作った分だけ検査工数がかかる
- (不良がでた時)何個目から不良が発生したのかがわからない
などが挙げられます。
検査ルールは会社によって異なるため、人手や予算に余裕があれば人海戦術で「全数検査」も良いかもしれません。
いずれにしても効率的で、不良を見落とさない検査の仕組みが重要です。
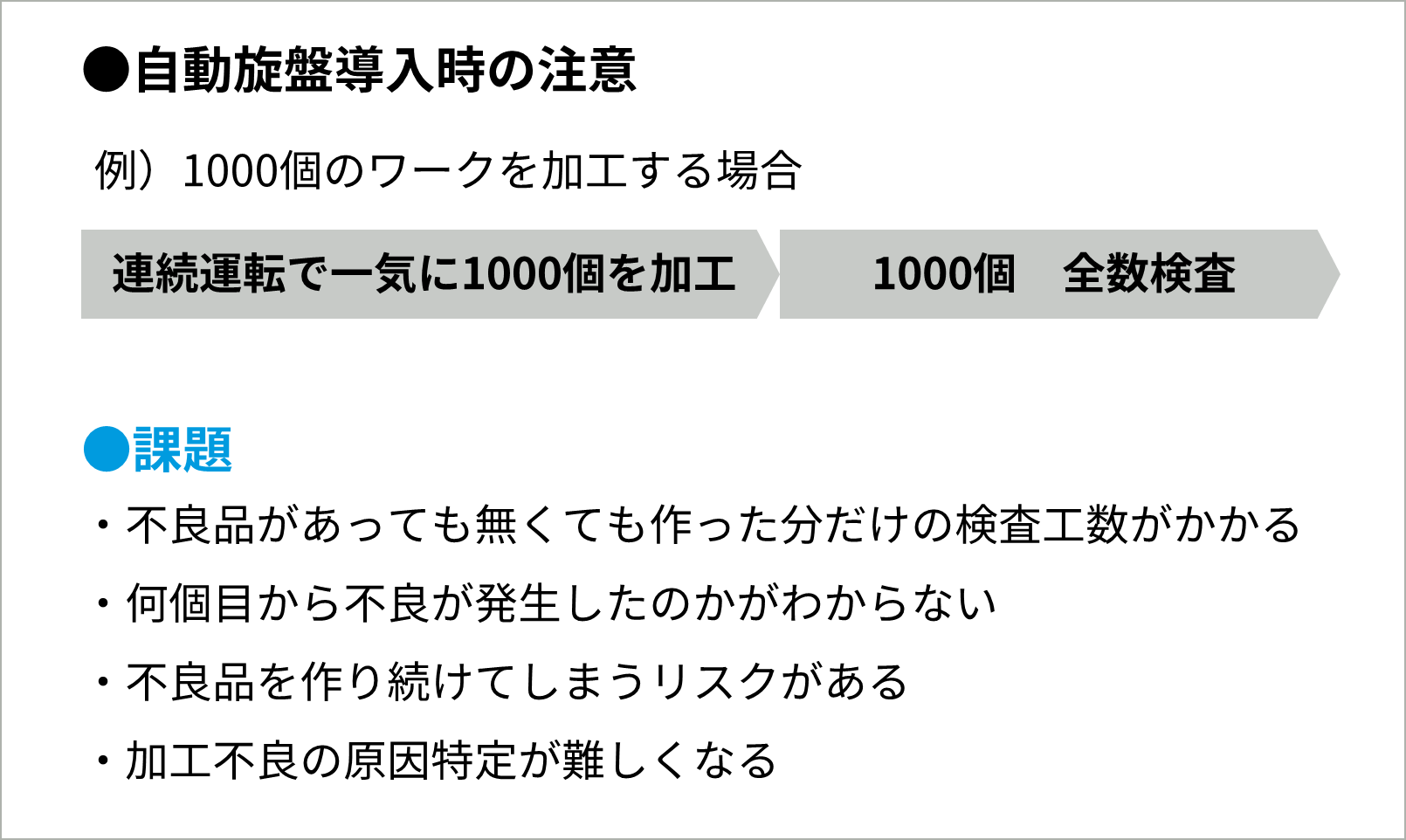
CNC自動旋盤を効率よく活用する運用とは?
結論、メトロールでは「機内計測」を行うことで、この2つの課題をクリアしました。
方法としては、以下の4ステップを行います。
- 一定数を加工したら、タッチプローブでクランプ中のワーク寸法(内径・外径)のチェックを行う。
- 万が一、公差を外れる不良品をプローブが検出した場合、アラームで機械をストップする
- 原因調査・復旧作業を行い加工を再開する
- 再発防止策を検討する
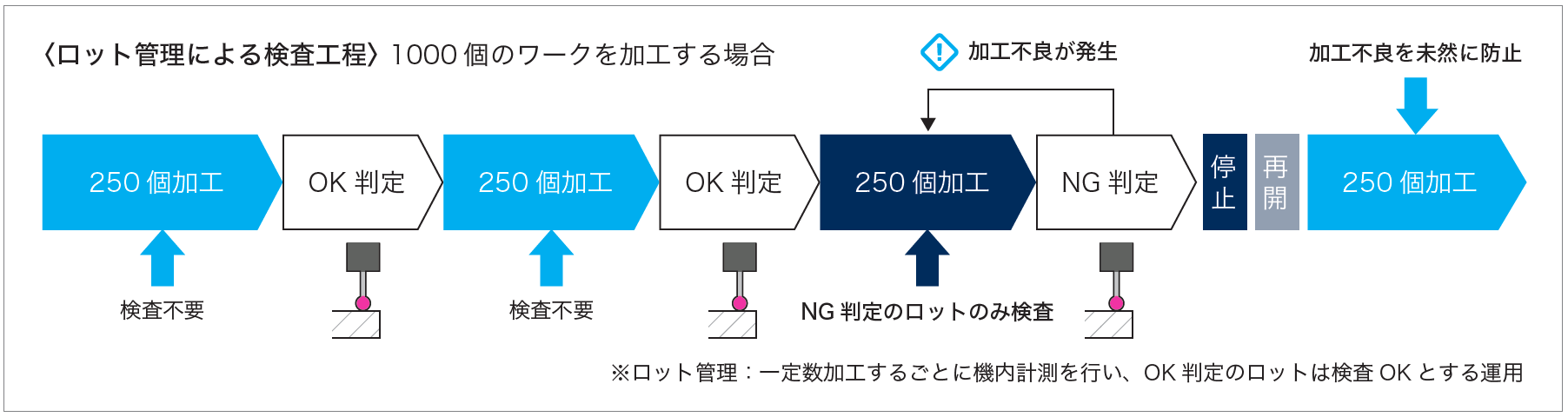
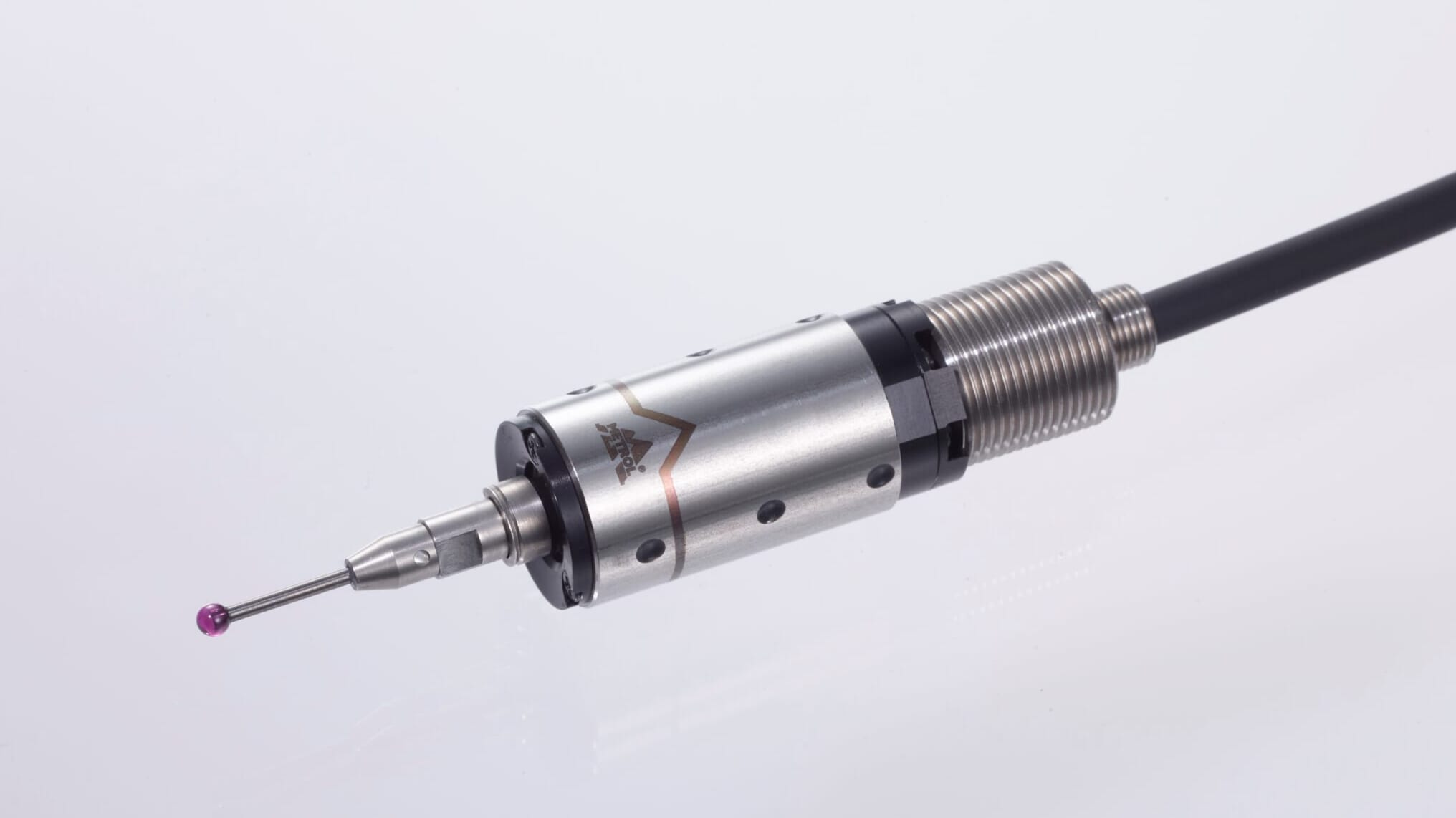
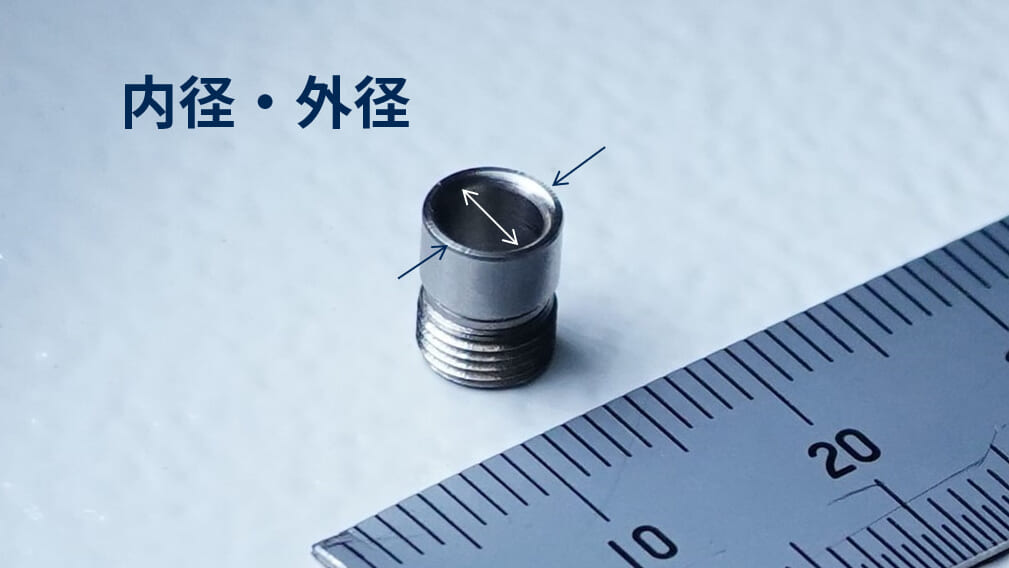
次にこの「機内計測」の運用とメリットを解説します。
誤解されやすい「機内計測」の本当の目的は?
機内計測とは?
機内計測とは、「工作機械の中で加工物(ワーク)を計測すること」を意味します。
主に加工サイクル中に、タッチプローブなどのセンサを使って計測するプロセスを設けて行います。
反対に、機械からワークを取り外して測定器をつかう方法を「機外計測」と呼びます。
機内計測の大前提と目的
「機内計測」で強調しておきたい前提は、必ずしも機内で全数検査を行う必要はない、という点です。
機内で全数検査を行ってしまうと、測定時間が大幅に増えサイクルタイムに影響してしまいます。
かといって稼働率を最優先するあまり、何時間も不良品を作っていては元も子もありません。
あくまで機内計測の目的は下記の3つ。
- 連続運転で大量に加工不良品を作り出す前に、機械を止めるなどの処置を施すこと
- 加工不良の原因をいち早く察知し、再発防止の改善を行うこと
- 不良発見時の検査数を少しでも減らすこと
そのために、適切な頻度で機内計測を行うことを推奨しています。
とくに自動旋盤を24時間稼働させるような無人運転ラインでは効果を発揮します。
事例で見る、CNC自動旋盤での「機内計測」のメリット
シミュレーション
例えば、1000個のワーク加工サイクルで、250個に1回タッチプローブによるワークの計測を行うとします。
この場合、機内計測を行う回数は1000個÷250個=4回です。
機内計測で不良品を検出した場合は、加工を継続しないようにアラームで機械をストップします。
(下記イラスト工程⑥参照)
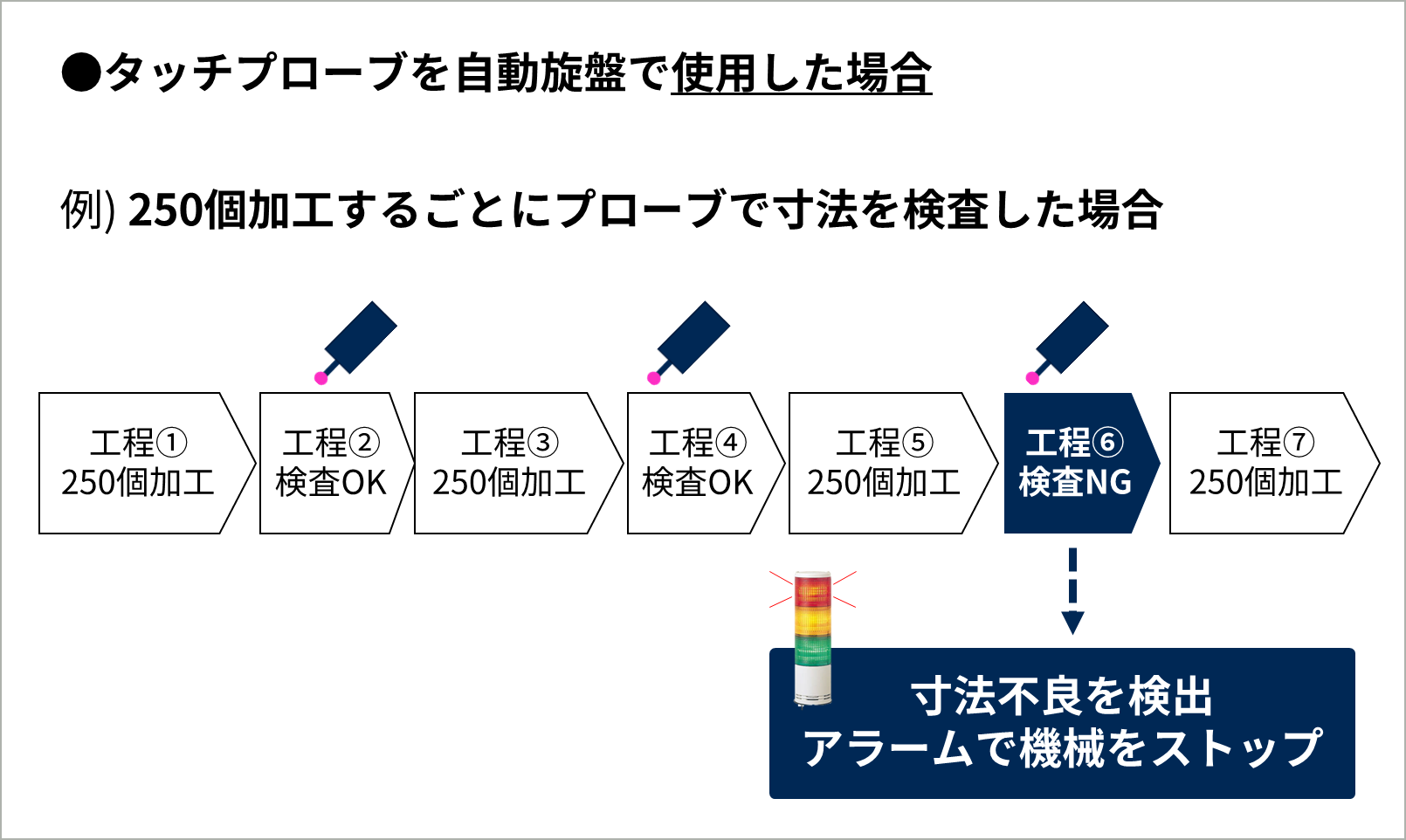
イラストの工程⑥で機械を止め、即座に加工不良の原因を特定し、設備の保全・再発防止策を施します。
これにより工程⑦で発生していたはずの加工不良による損失(材料+加工時間)を防ぐことができます。
機内計測のメリット1:加工不良の防止
不良を発見した段階で機械を止めることで以下3つののメリットがあります。
- (工程①③の)良品ロット500個は検査不要、工程⑤ロット250個のみ検査でOK
- 機械を止めたことで未然に加工不良250個(工程⑦)を防げた
- 加工不良の再発防止策をすぐに立てられる
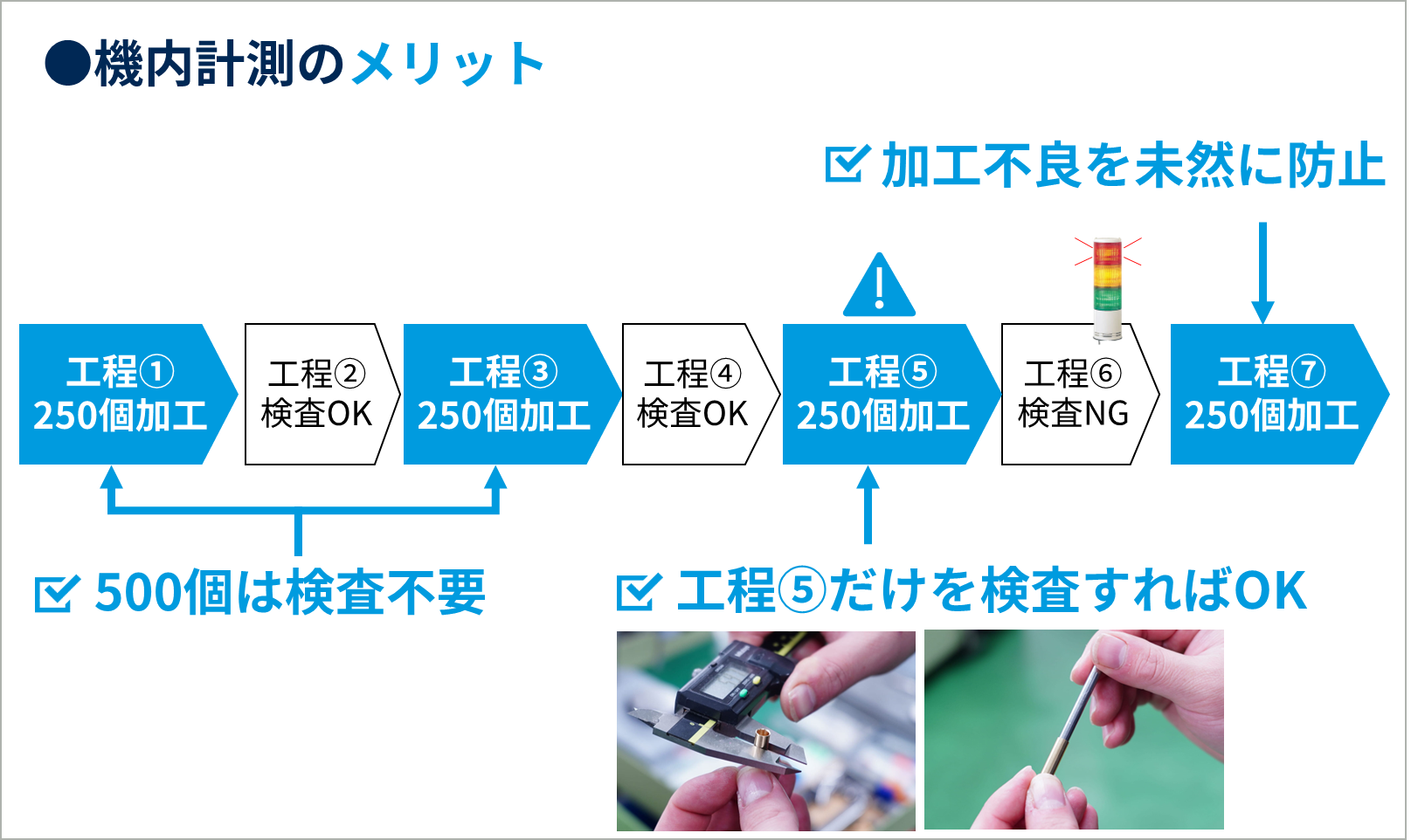
つまり、たった4回の機内計測で、以下の3つのロスを未然に防止できます。
- (工程①③⑦の)750個分の検査工数をカット
- (工程⑦の)250個分の材料費
- (工程⑦の)250個分の加工時間
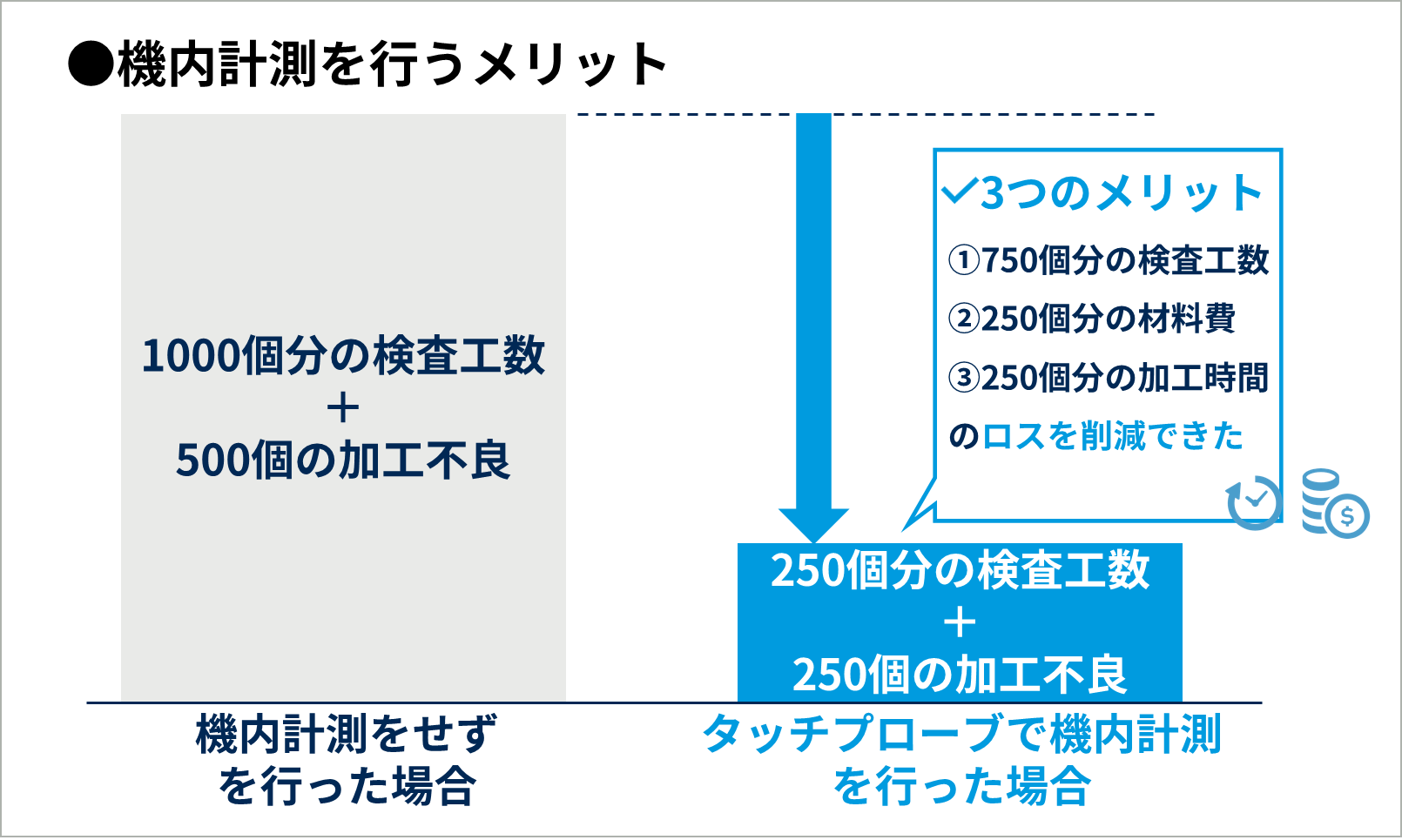
機内計測のメリット2:移動と段取り工数の削減
機内計測はワークの測定に伴う、3つのムダ削減にもつながります。
従来は、
- (段取)設備・測定器にワークを(再)設置する
- (段取)設備・測定器からワークを取り外す
- (移動)ワークを運ぶ
が発生していました。
機内計測により、こうした段取り時間・移動時間を解消できます。(下記イラスト)
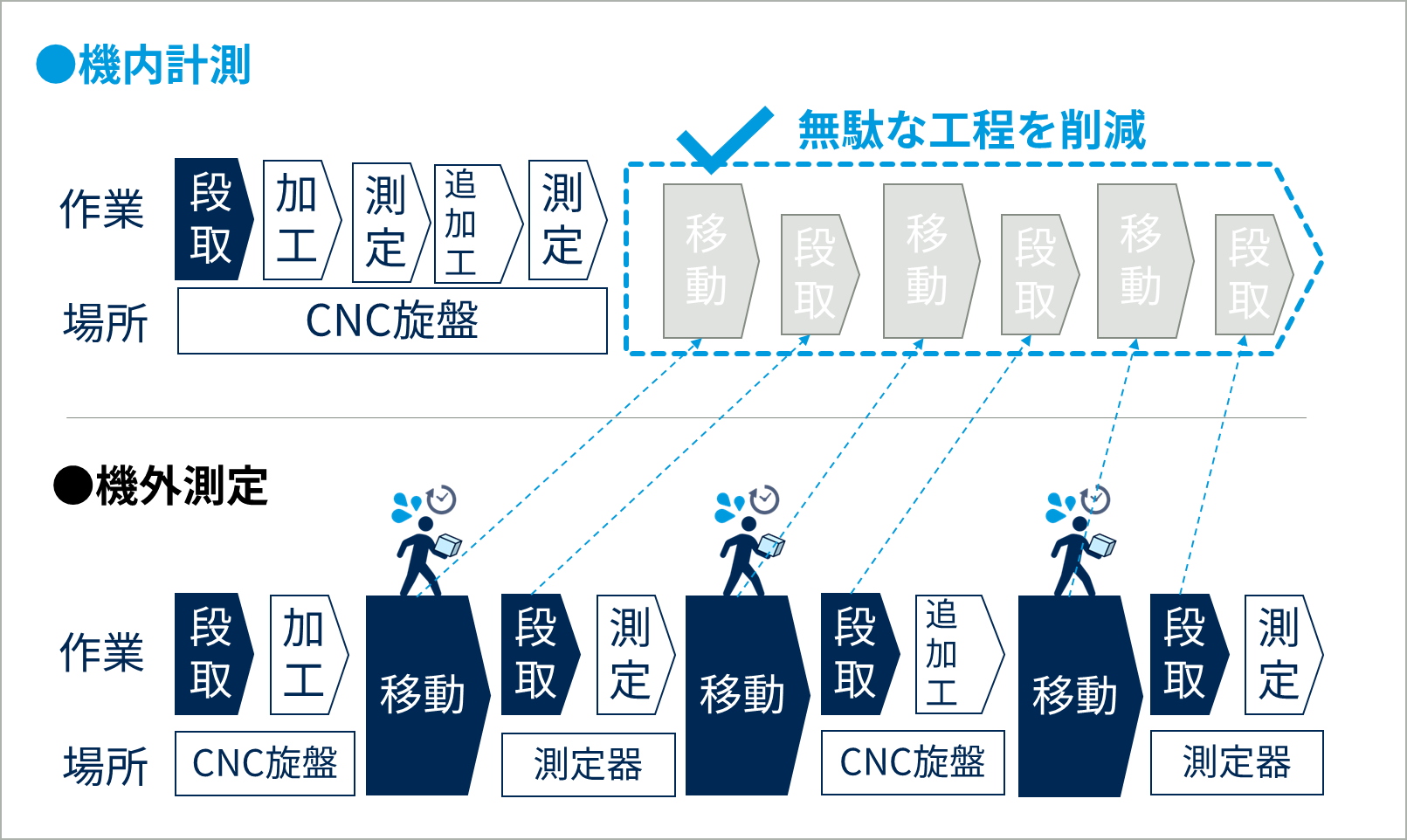
CNC自動旋盤で使えるタッチプローブとは?
メリットが多いCNC旋盤での「機内計測」ですが、馴染みがない方も多いのではないでしょうか?
背景に以下の理由が挙げられます。
- 計測時間でタクトタイムが伸びる
- プローブサイズが大きく、主軸やツールホルダーに干渉するため搭載したくない
- センサ本体に切粉がからまり破損するリスクがある
- 機内計測で精度がでるか心配
こうしたデメリットの相談を受け、メトロールでは本体径φ17.8mmの「超小型のタッチプローブK3Sシリーズ」を開発。
従来よりも本体径が圧倒的に細い、デメリットを解消するプローブを設計しました。
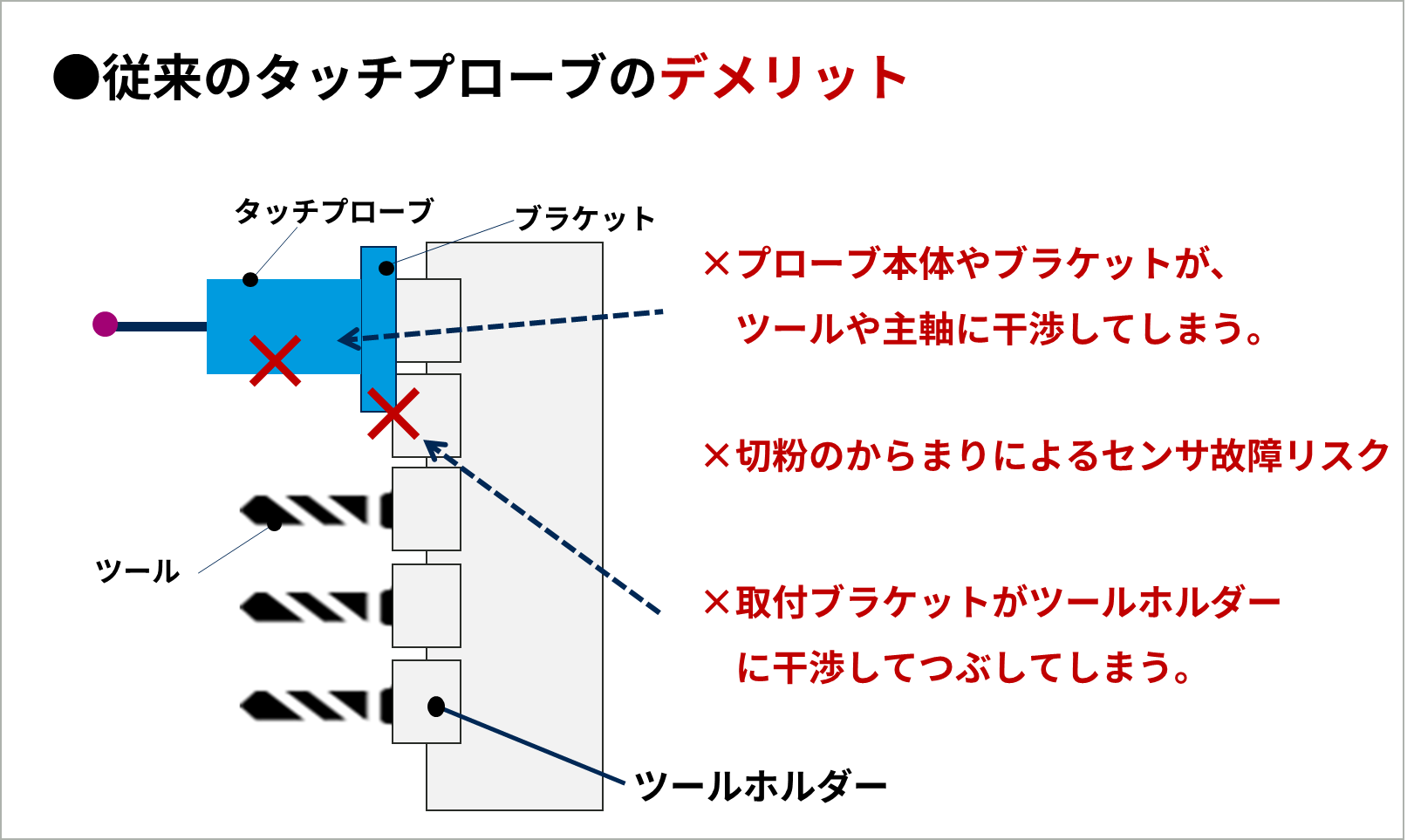
従来のデメリットに対して、K3Sシリーズは以下のメリットがあります。(イラスト参照)
- 本体部がホルダーにすっぽり収まるので主軸やワークに干渉せずツールホルダーもつぶさない
- 切粉による故障リスクが低く、保守パーツのコストを抑えられる
- センサ繰返し精度1μm、加工サイクルの中で測定を行うので高精度な測定が可能。
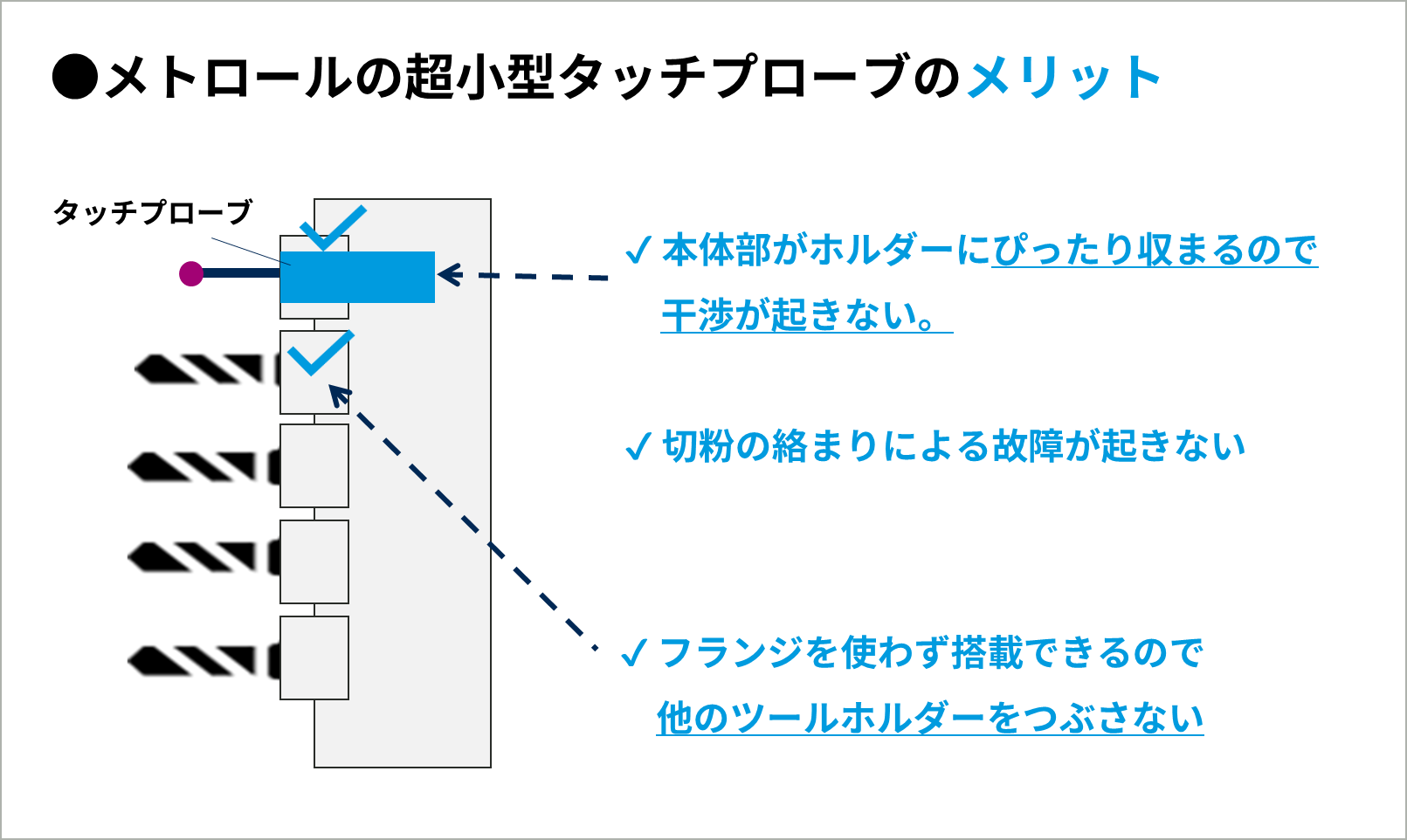
↑のイメージの現物写真が↓になります。
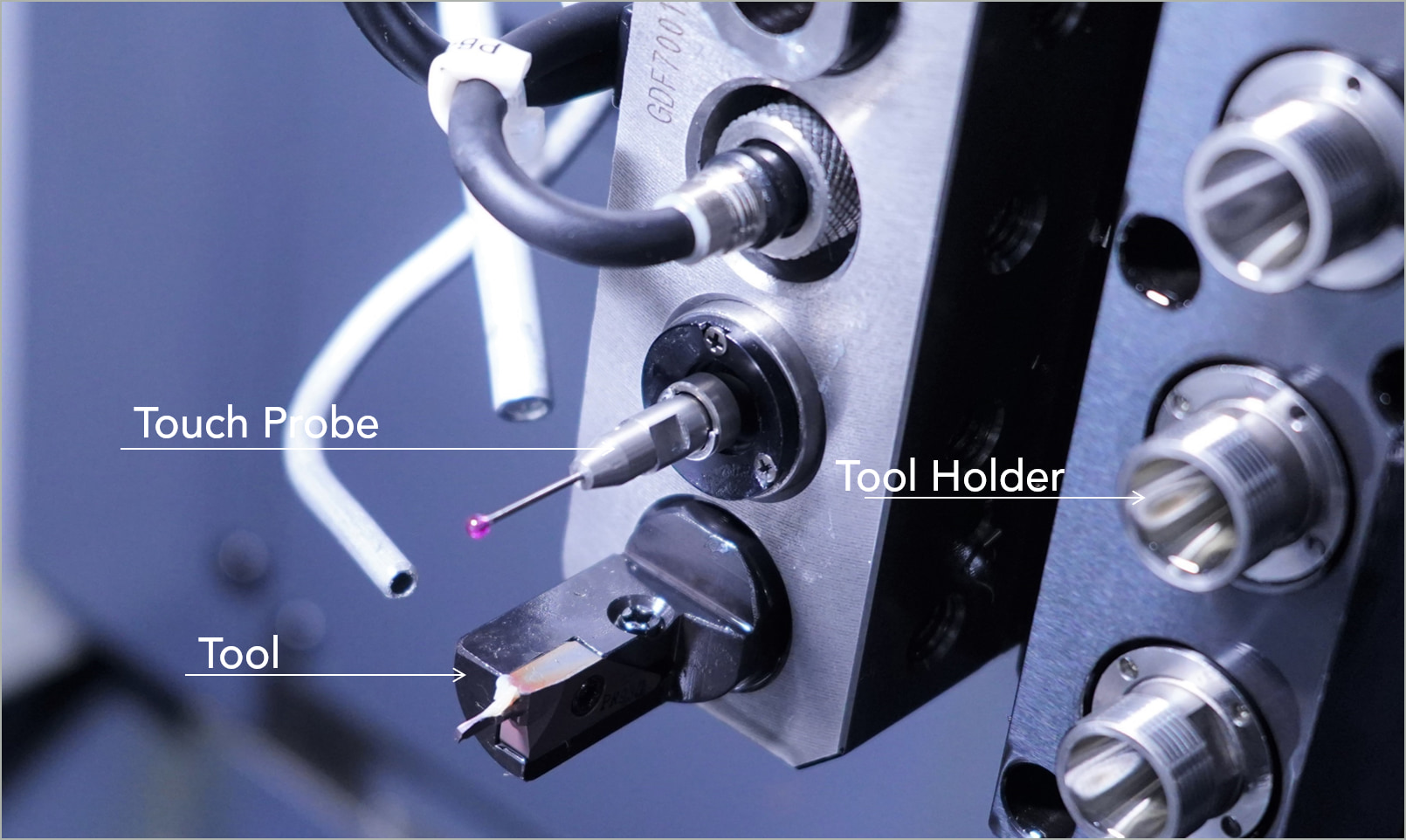
従来のタッチプローブとメトロールのタッチプローブの取付を比較イメージがこちらです。
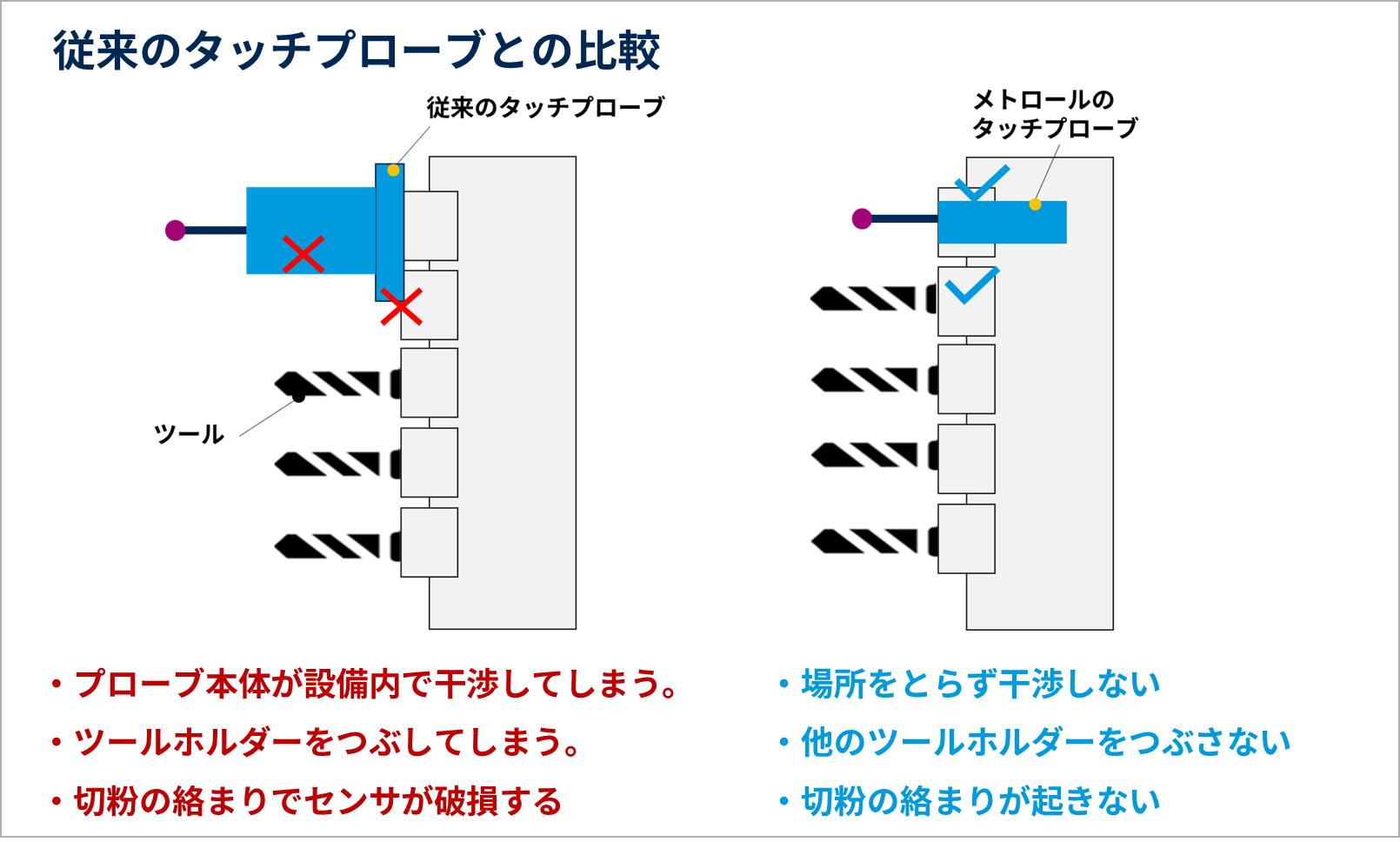
「計測よりもタクトタイムを優先したい」の落とし穴とは?
繰返しですが、必ずしも機内計測で全数検査の必要はなく、計測頻度によってタクトタイムの課題は解消可能です。
それでも機内計測で「タクトタイム」を懸念をする声もあります。
とにかく加工(タクトタイム)を優先し、不良品をあとで選別・追加工し良品に直すといった運用です。
この場合
- 不良品をにかかった加工時間・材料費
- 不良品の選別作業
- 不良要因の改善スピード
などが見落とされがちです。
機内計測の導入コストよりも、こうしたコストが大きければ、機内計測で得られるメリットは大きいでしょう。
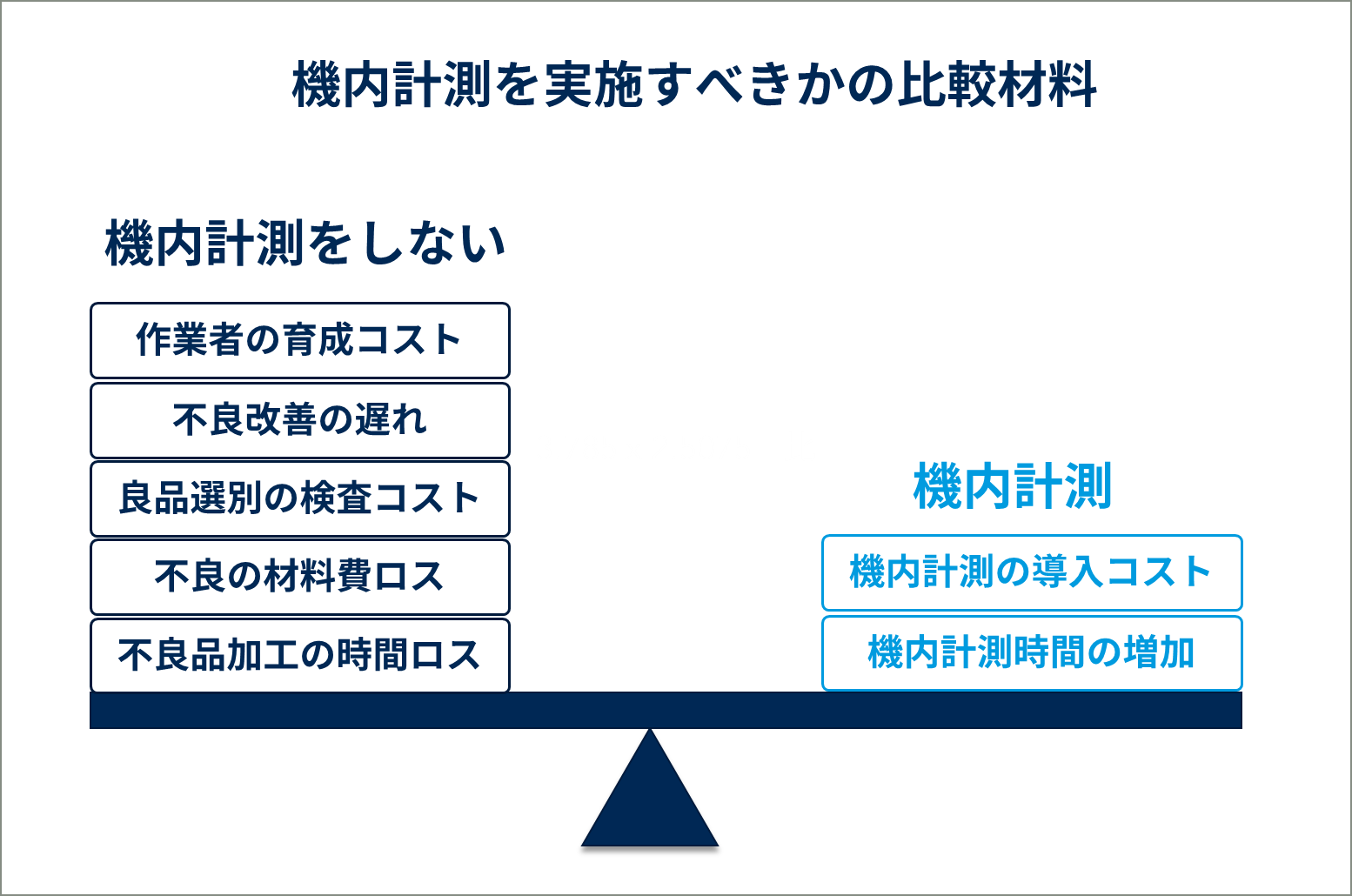
【動画】CNC自動旋盤での機内計測
当社ではタッチプローブを使ってワークの内径と外径を計測しています。
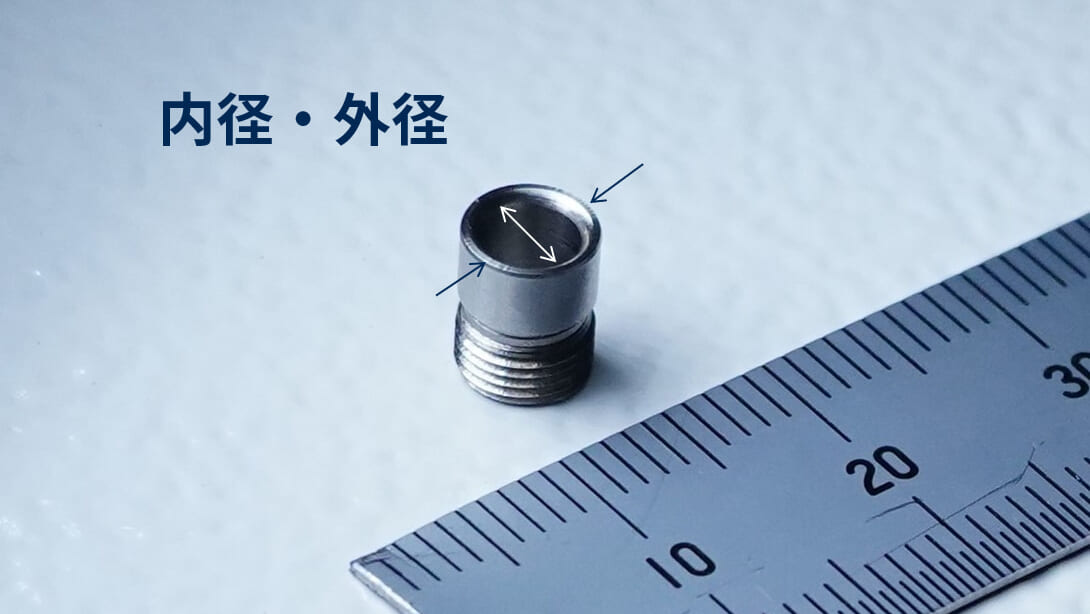
こちらの動画でワークの内径と外径を計測がご覧いただけます。
非常に小さなパーツのため、人手で計測するよりもプローブを使った計測が効率的なのが分かります。
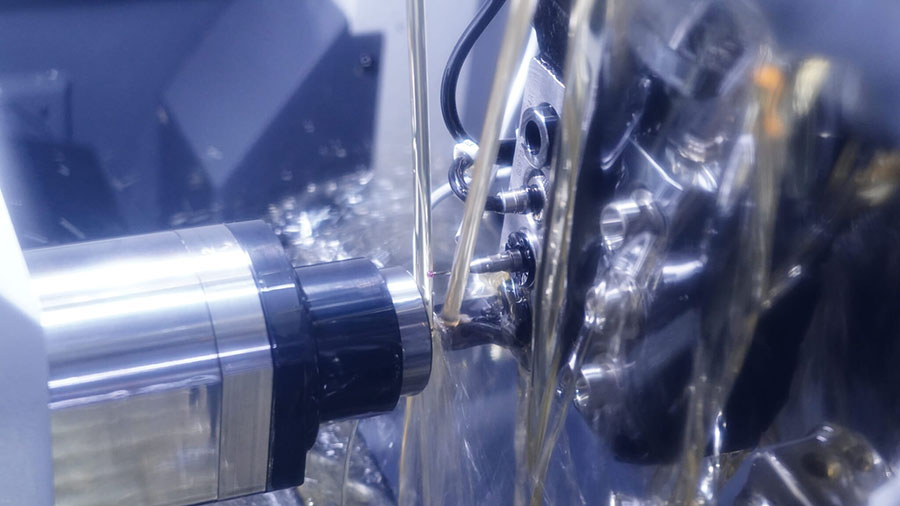
自動旋盤における「機内計測」の考え方、測定精度は?
「機内計測」の精度における最大のメリットは、「ワークが正確に位置決め(チャック)された加工条件下で計測ができる」ことにあります。
逆に、人が機外計測する場合は、以下のリスクがあります。
- 都度ワークを取り外すため、位置決め条件が変わり測定誤差のリスク
- 計測の熟練度が人によって異なり、不良品の見落としリスク
- ノギスなど人の力加減によってワークが歪んでしまう
実際、SNSでも「ノギスの使い方」が人によって認識が異なるケースがあり、話題にも挙がっています。
ノギスの外側測定は、出来るだけ基準端面の近くで測定物を挟んではかる。
— ノギス管理台帳 (@manage_ledger) January 31, 2022
ベテランと思われる人でも先端の方で測る人がたまにいるね。
ノギスの使い方は以外と誰も教えてくれない😵 pic.twitter.com/EPSzM9GYKX
CNC自動旋盤にタッチプローブを搭載するには?
新規設備に搭載する場合
タッチプローブを新規取付するにはプログラムが必要になります。
まずは弊社にお問い合わせ頂くか、メーカー様にお問い合わせください。
シチズンマシナリー社製の場合、CincomシリーズのA20、L20、L12に搭載が可能です。
メトロールではCincom導入時にシチズンマシナリー様にタッチプローブ用のソフトウェアを開発頂いております。
こちらを参考プログラムとしてメトロール工場にてご覧頂くことが可能です。
すでにお持ちの自動旋盤に「後付け」したい場合
メーカー様によっては後付けが可能です。
メトロールで使用しているタッチプローブ用のソフトウェアをメトロール工場にてご覧いただくことが可能です。
ただし、ソフトウェアだけでなく設備のハード面、電気的仕様の条件がそろわないと使用できない可能性があるためメーカー様の確認が必要な場合があります。弊社かメーカー様にお問い合わせください。
■後付け可能な自動旋盤メーカー(弊社調べ)
・シチズンマシナリー様
よくある質問
タッチプローブがワークに衝突しないか?
質問:ツールが破損していると、ワークに加工穴が空いていないケースがある。この状態でタッチプローブが測りに行くとワークに突っ込んで破損しないか?
回答:装置側のスキップ信号を使用すればセンサの衝突を回避することができるでしょう。
タッチプローブのプログラムにもよりますが、スキップ信号を使うことでセンサが信号を出力したタイミングで残りの軸移動を中止することができます。
まとめ
いかがでしたでしょうか?
自動旋盤は高い生産能力がある一方で、大量の加工不良リスクと隣り合わせです。
工作機械は「導入して完了!」ではなく、運用しながら改善していく事もセットで考えていく必要がありますよね。
人材不足の昨今、こうしたセンサーを活用しながら効率的な運用をしてみてはいかがでしょうか?
タッチプローブの評価用サンプルの貸出しなども承っております。
メトロールでも自社の生産にセンサを活用した改善活動を多数実施しています。
いま自動旋盤の導入に悩まれてる方は、ぜひ当社の工場見学にお越しください!
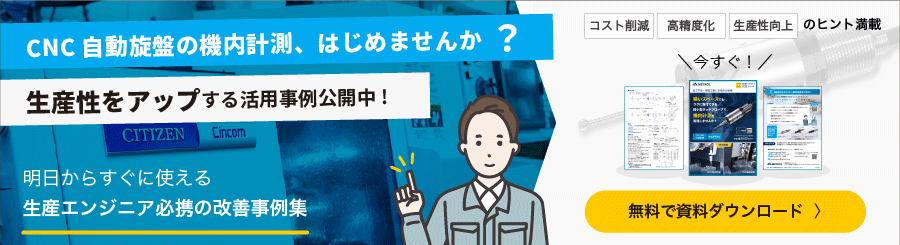
CNC自動旋盤に搭載できる超小型タッチプローブK3S
有線式 小型タッチプローブ[K3Sシリーズ]
超小型で省スペースでのワークの原点出しを自動化
CNC自動旋盤用のセンサに関するお問合せ
自動旋盤用のセンサについてお気軽にお問い合わせください。装置専用設計のご相談も承っております。
経験豊富なエンジニアがご対応致します。