タッチプローブによる研削盤の「機上測定」とは?
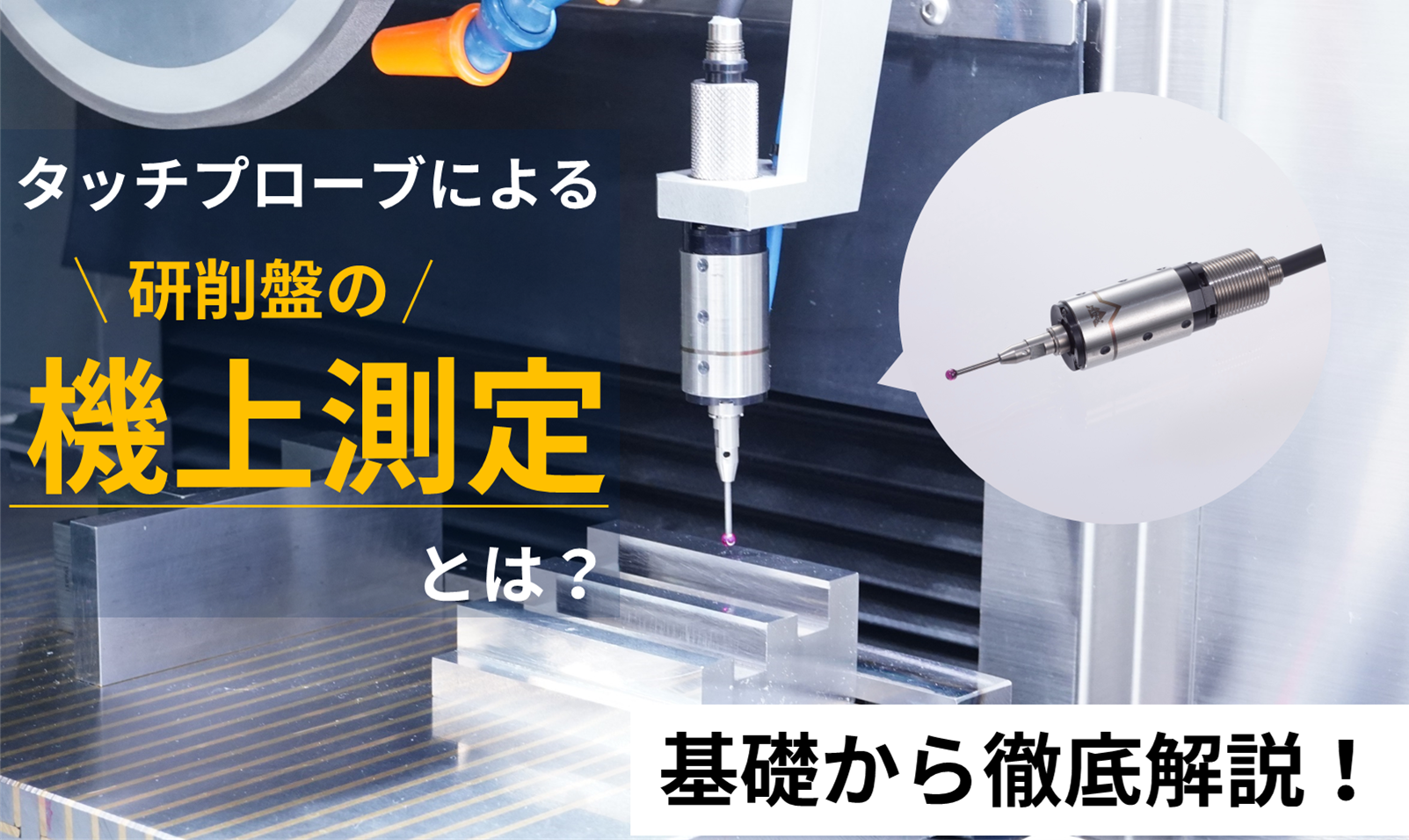
ワークの仕上げ加工の品質を握る「CNC平面研削盤」。
研削加工はシビアな精度が求められる一方で、以下のようなことを感じてはいませんか?
- 「三次元測定機など測定のための段取り作業や移動に時間がかかる…」
- 「測定のやり方が人によってばらつく…」
- 「測定後の手戻りと追加工をやめたい…」
本記事では、これらの課題をクリアする「機上測定」をテーマに解説していきます。
研削加工を含む製造プロセスを改善したいと考えている方は必見の内容です。
本記事の内容をまとめると
- 加工の段取り、寸法測定をラクにする方法が分かる
- 研削盤における「機上測定」が大幅な工数削減に繋がる仕組みが詳しくわかる
- 職人技になっている作業を標準化する方法が分かる
- CNC平面研削盤で機上測定を導入する方法が分かる
目次
機上測定とは?機外測定との違い
「機上測定のメリットがイマイチわからない」、という方は多いのではないでしょうか?
簡単におさらいをしてみましょう。
機上測定
機上測定とは、「工作機械の上で加工物(ワーク)を測定すること」を意味します。
本記事で指す機械は研削盤を指しますが、他にもマシニングセンタやCNC旋盤など様々な工作機械で行われます。
測定機器は主に「タッチプローブ」という接触式のセンサを使います。センサがワークに触れたときの機械の位置情報からワーク寸法の測定を行う方法です。(参照:画像1)
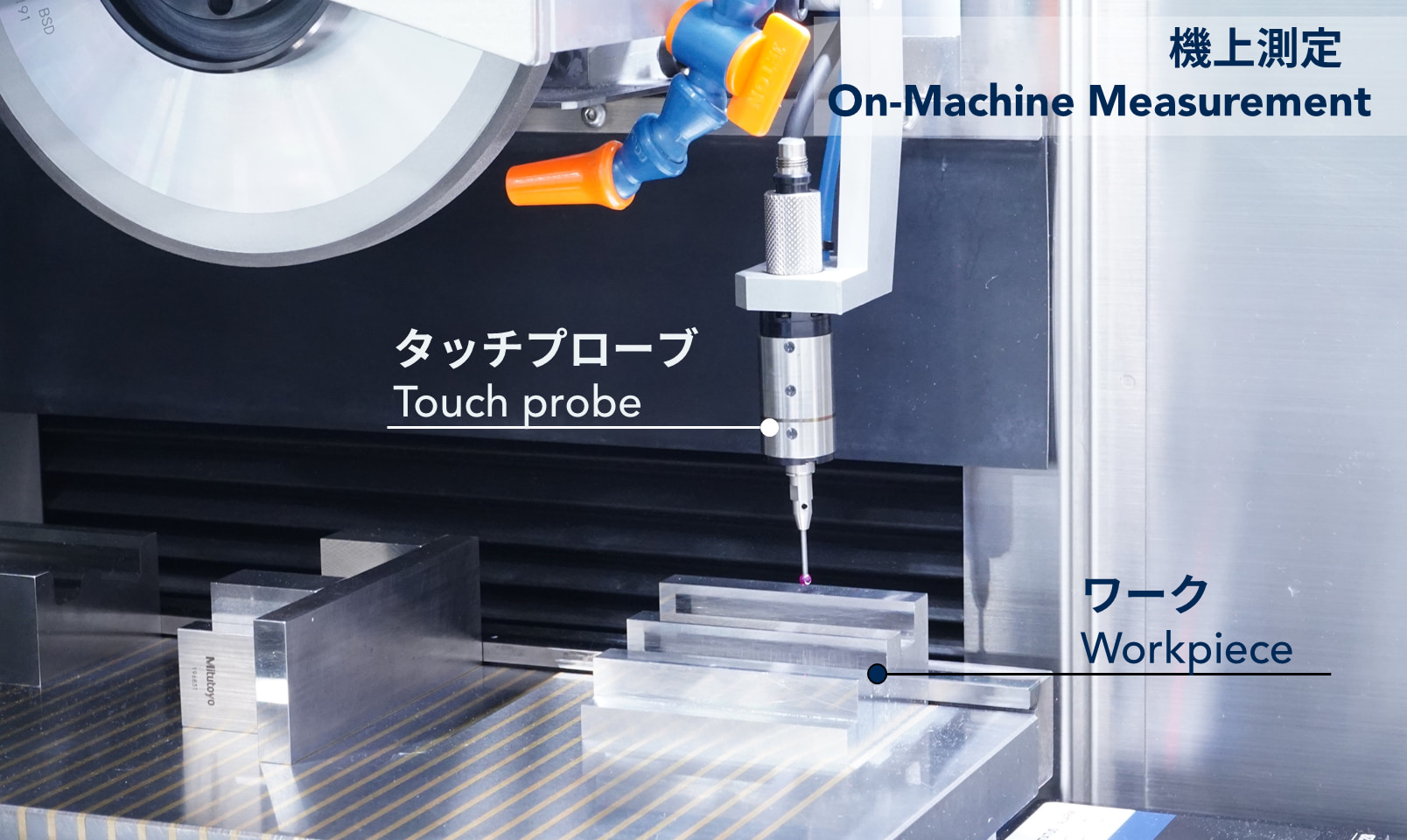
機上測定の目的
機上測定を行う目的は大きく以下の2つです。
- 加工前のワークの原点出し
- 加工物の寸法計測
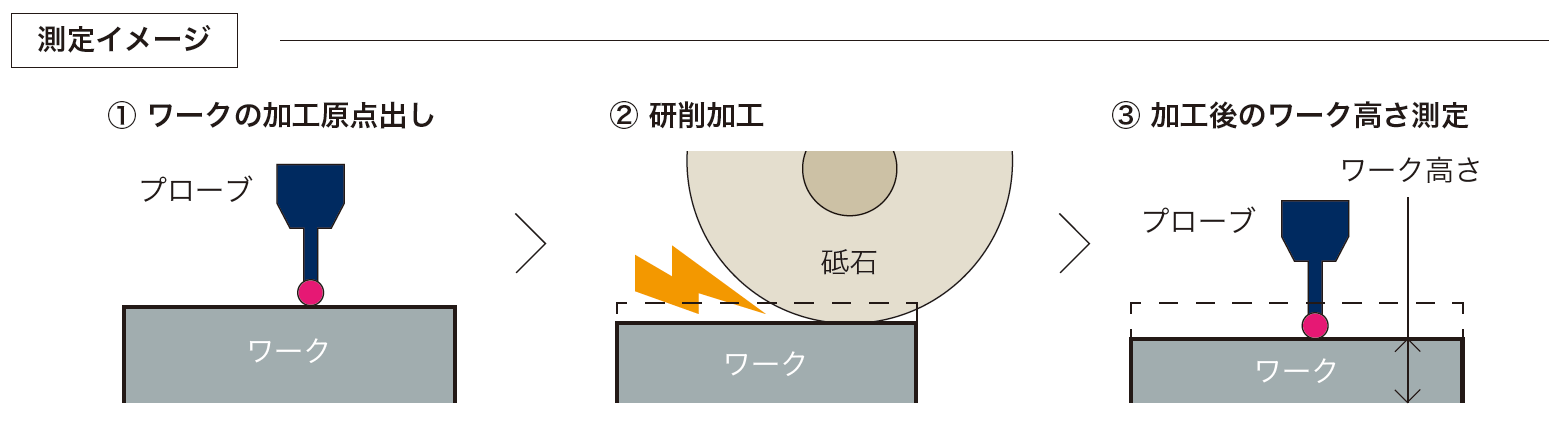
機外測定
機外測定は「機械の外で加工物(ワーク)の測定を行うこと」です。
加工したワークを工作機械から取り外してから、
- 三次元測定機
- シリンダーゲージ
- ピンゲージ
- ノギス
などの測定器で行う測定方法です。要求精度によりますが、厳密な測定ほど温度管理された測定室で行われること一般的です。測定で公差が未達だった場合は、工作機械にワークを戻し追加工を行うこともあります。
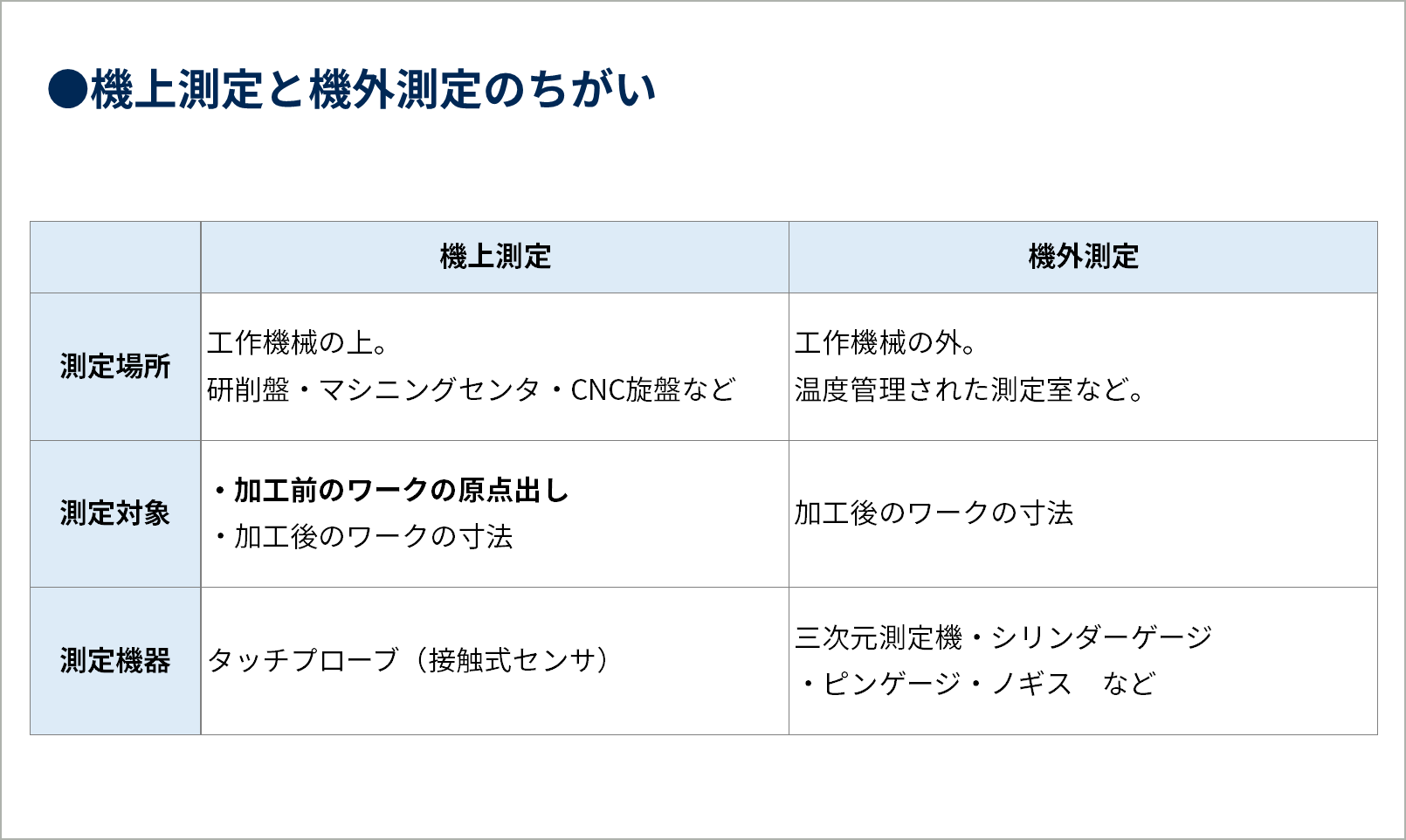
機上測定…の前に、研削加工サイクルのおさらい
一般的な研削加工のサイクル
機上測定と機外測定どちらを採用するかで加工サイクルの工数は大きく変わります。
前提となるCNC平面研削盤の「研削加工のサイクルステップ1~6」について簡単におさらいをします。
- ステップ1:「砥石の当て込み作業」による加工開始点の確認
- ステップ2:被削材 (ワーク)の加工開始点の確認(厚み測定)
- ステップ3:加工サイクル
- ステップ4:ワークの厚み測定
- ステップ5:(厚みが未達の場合)追加工
- ステップ6:加工後の測定
上記6ステップで研削加工を行います。(本記事ではツルーイングやドレスは省略)
この「ステップ4:ワークの厚み測定」と「ステップ6:加工後のワーク測定」を
- 機外測定で行った場合
- 機上測定で行った場合
でこの全プロセスの工数が大きく変わります。
次に、①と②それぞれの測定方法で実施したとき工数をシミュレーションして、比較検証を解説していきます。
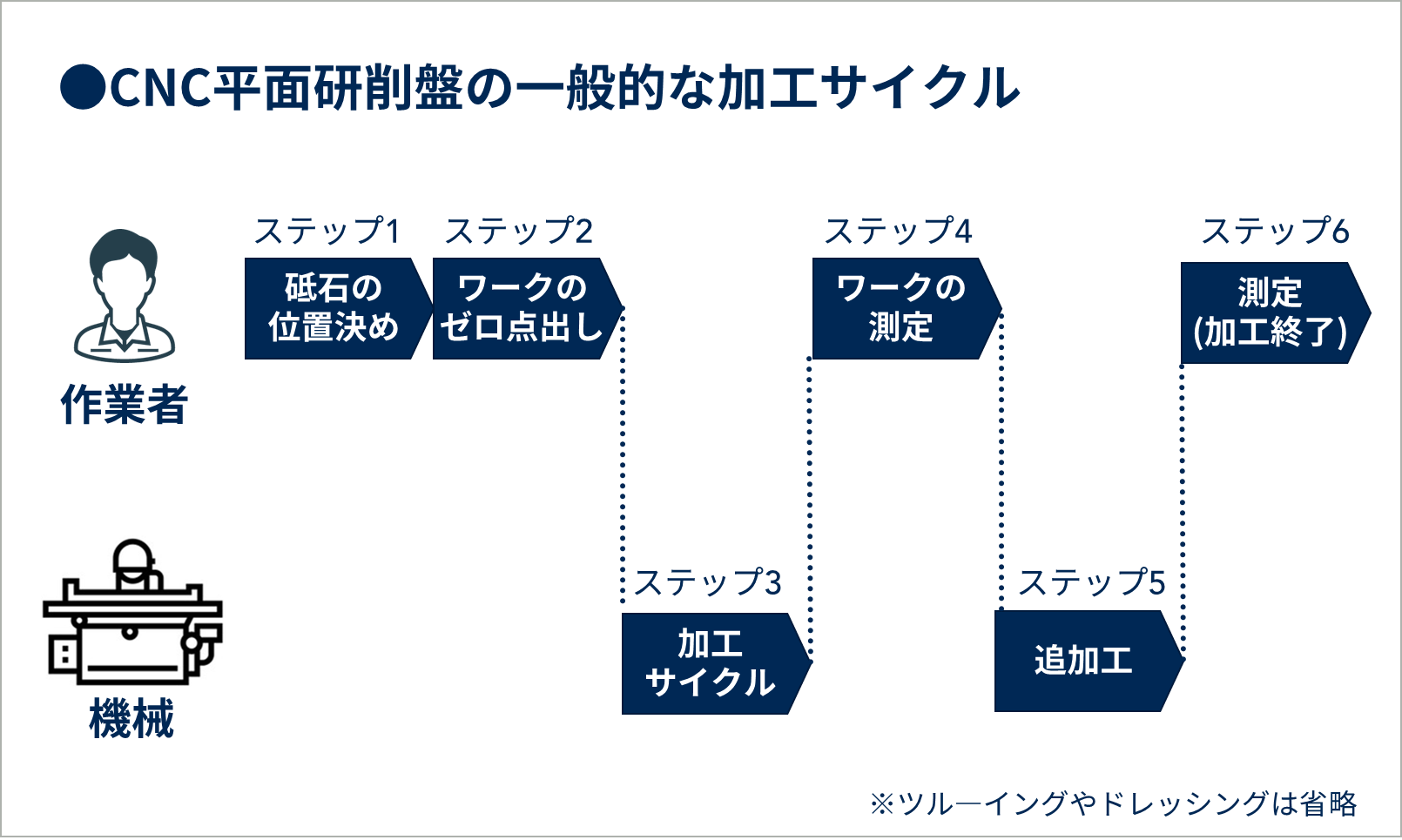
「機外測定」の隠れたデメリットとは?
通常、加工後にワークを測定し許容公差から外れてしまうと、加工工程にワークを戻し基準を満たすよう追加工を行います。
機外測定では、このプロセスの中に以下のような削減すべき「ムダな工程※2」があります。
- ワークの取り外し作業
- 人の移動
- ワークの再度セッティングの段取り作業
- 測定結果(公差外れ)による出戻り
- 測定待ちワークの滞留
これらは、出荷までのリードタイム長期化やコストアップに繋がる工数として現場の課題となっています。
※2:ムダな工程…とは?
出典: フリー百科事典『ウィキペディア(Wikipedia)』トヨタ生産方式
トヨタ生産方式では、ムダを「付加価値を高めない各種現象や結果」と定義しており、代表的なものとして以下の7つがある。①作り過ぎのムダ 、②手待ちのムダ、③運搬のムダ、④加工そのもののムダ、⑤在庫のムダ、⑥動作のムダ、⑦不良をつくるムダ
機外測定の工数シミュレーション
例を使って「機外測定」の工数シミュレーションを説明します。
(例):①研削加工 →②測定 → ③追加工→④測定のサイクル
このサイクルでは、
- 人の移動:3回
- 段取作業:3回(=加工段取:1回、測定器へのセッティング:2回)※初回の段取り作業のみ必須
が発生しています。(図1参照)
研削盤と測定器の各装置で、ワークの取付・取り外しや位置決めなどの段取り作業が毎回発生しています。
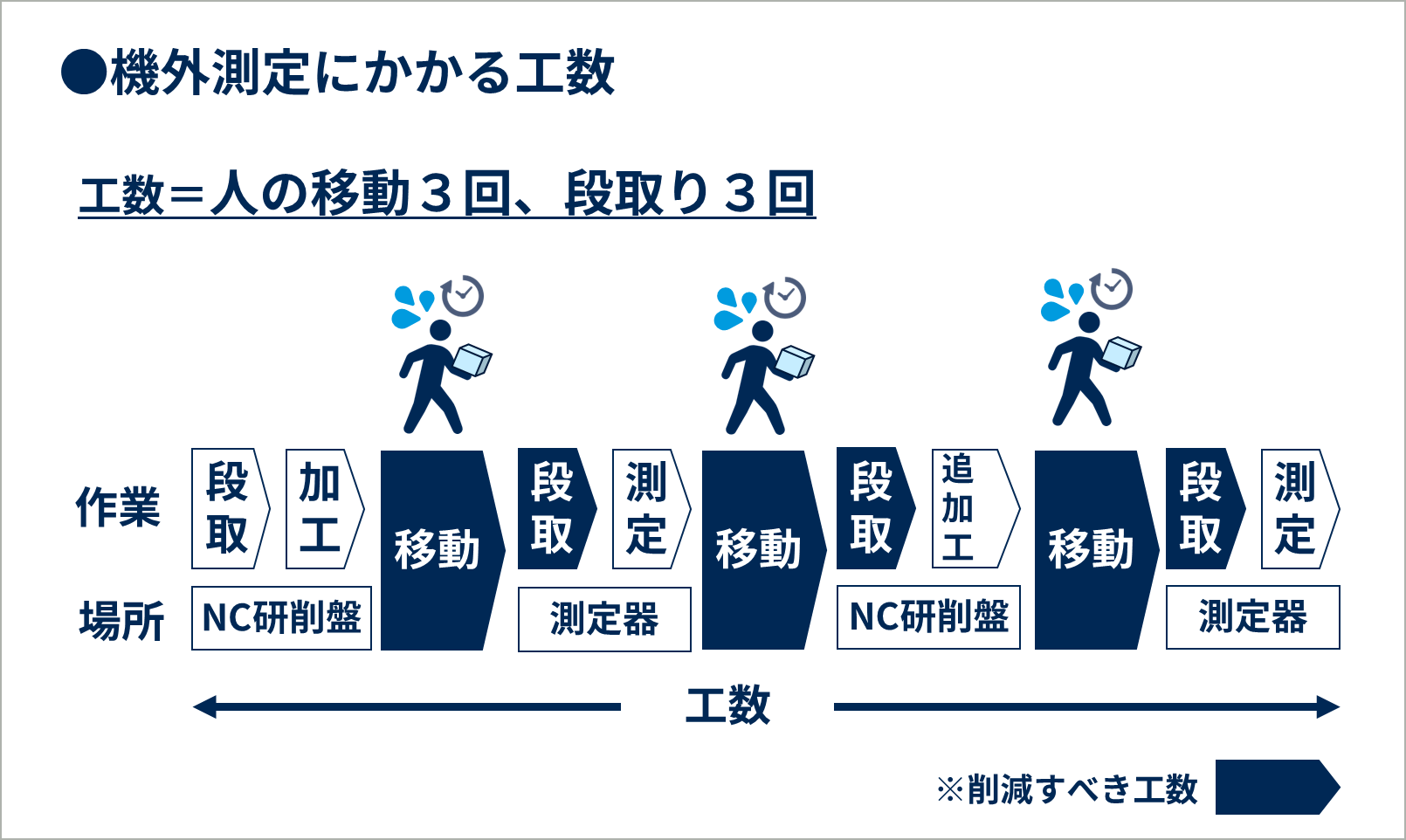
次に、機外計測に対して、機上測定ではどれくらい工数が変わるか解説します。
「機上測定」のメリット
タッチプローブを使った「機上測定」では、①加工~④測定の工程を全て設備上で行うことで、
- ワークの取り外し作業が無くなる
- ワークの再セッティング作業が無くなる
- 人の移動が無くなる
- ワークの多数個取りができるようになる
など、工数削減のメリットがあります。
機外測定と同じ例をつかって、工数がどれだけ削減されるのか比較してみましょう。
機上測定の工数シミュレーション
(例)①加工 ⇒② 測定 ⇒③ 追加工⇒④測定のサイクル
機外測定のシミュレーションと比較すると、
- 人の移動 3回(機外) ⇒ 0回(機内)
- 段取作業 3回(機外) ⇒ 0回(機内)
のように工数改善に繋がることが分かります。(図2参照)
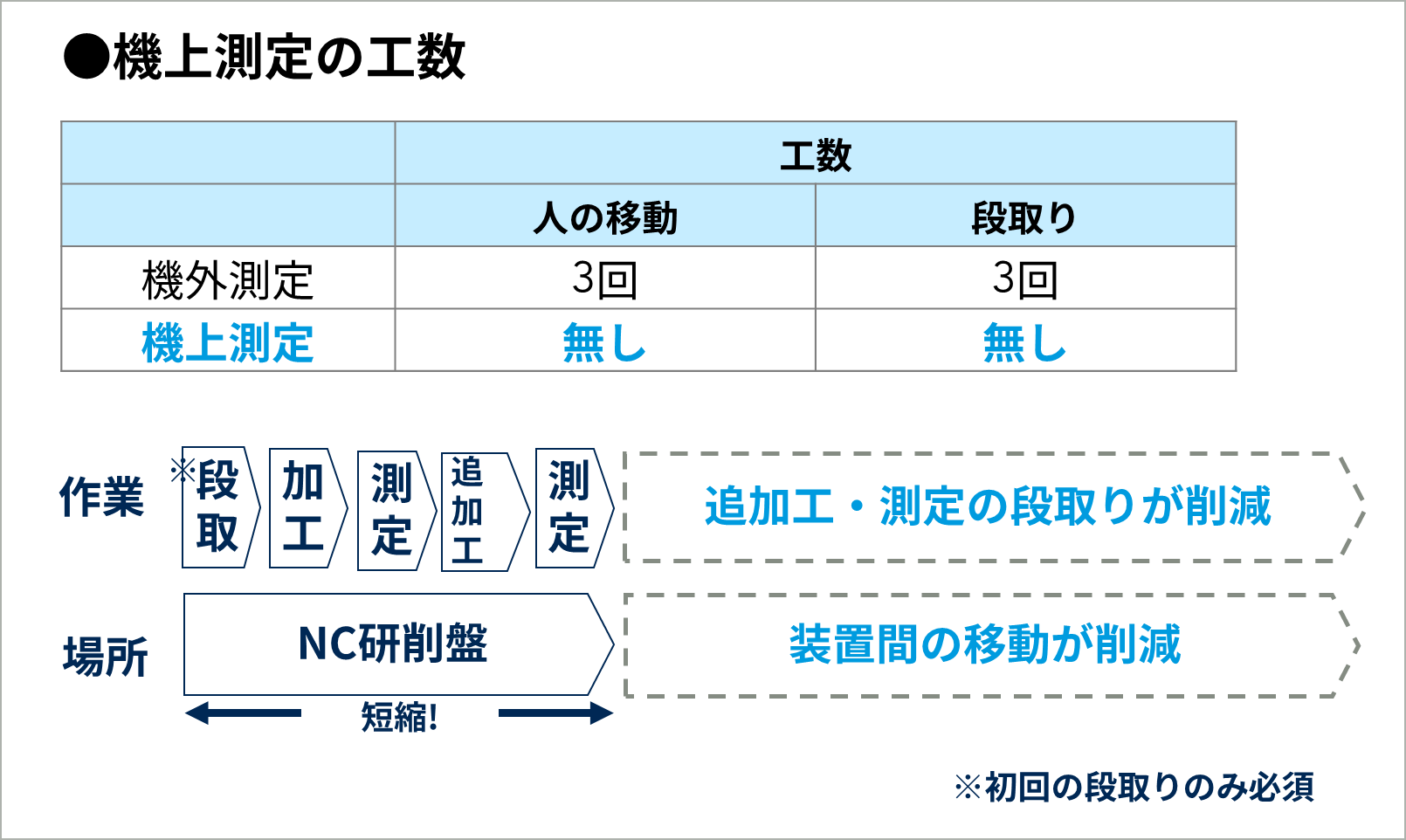
機上測定と機外測定の工数の比較
「機上測定」と「機外測定」を比較すると、削減される工数の差は歴然です。
例えば、(移動+段取り)の1セットで20分かかるとすると、 (移動+段取り)×3セットで、1時間近くの無駄を削減できます。
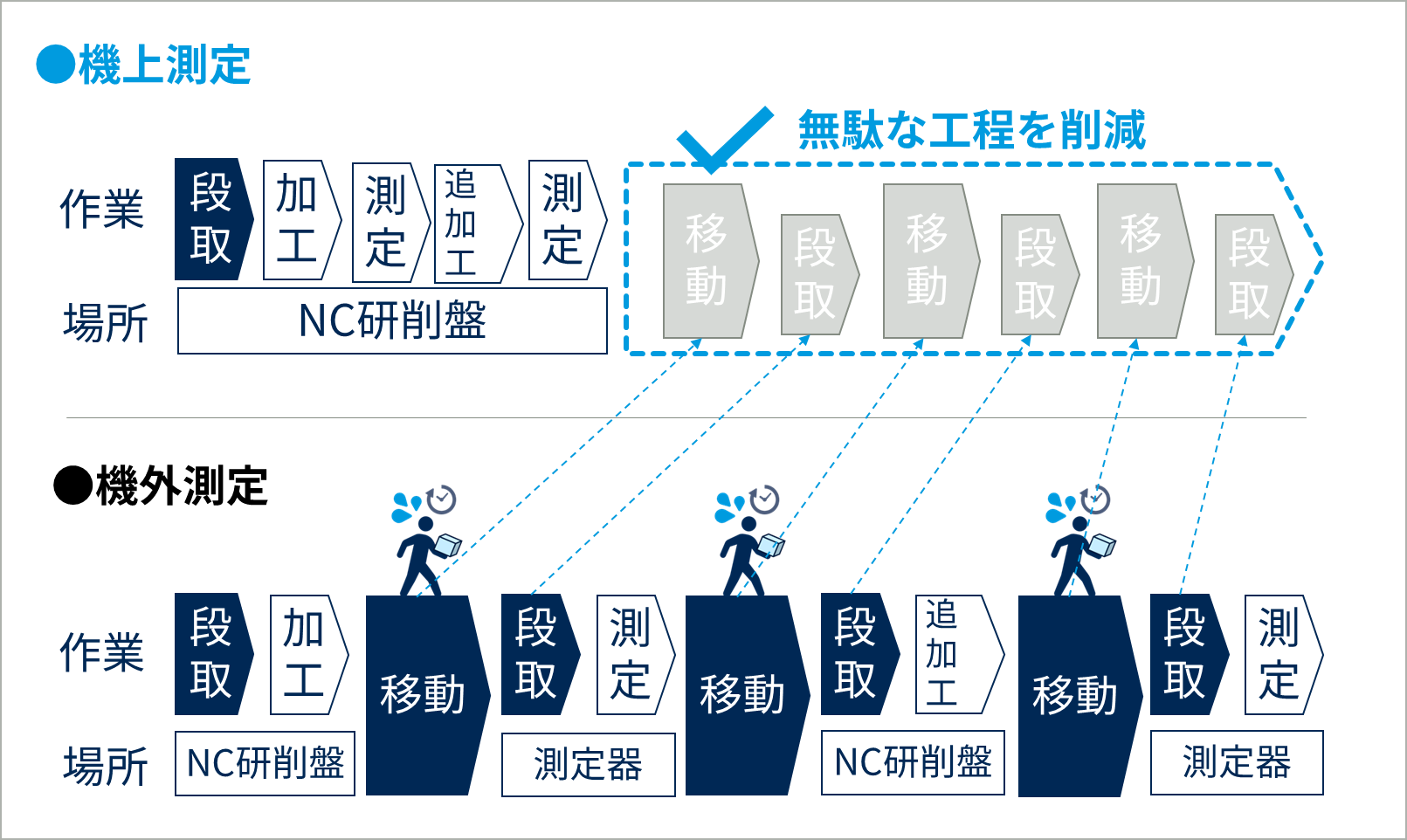
機上測定の測定精度は?研削盤との相性が最適な理由。
たとえ工数がカットできても、精度が低く測定の役割を果たせなければ意味がありません。
機上測定がどれくらいの測定精度で行えるのか?を解説します。
研削盤が機上測定に最適なワケとは?
機上測定の最大のメリットは「ワークを精度よく位置決めした状態」で測定を行える点です。
機外計測の場合、公差がシビアなワークほど、機械・測定器への再セッティングに手間がかかります。
再セッティングの際に、「位置決め条件が変わることで、加工不良や計測誤差が起きる」といったリスクがあります。
その点、ワークを取り外さずにチャックした状態で測定も行えば、手間を削減しながら高精度な測定が可能になります。
また位置決め条件が変わらないので、複数ワークの同時加工(多数個取り)が可能になります。
多数個取りについては以下の記事を参考にご覧ください。
本記事では従来の研削加工の生産性を機上計測によって劇的にアップする理由を詳しく解説します。機上計測によって、加工精度の向上やワークの多数個取りなどが実現されます。
次に、機外測定(シリンダーゲージ)と機上測定の精度の比較を解説します。
機上測定の精度を検証してみた(参考データ)
機上測定と機外測定(シリンダーゲージ)のワークの厚み計測のデータは以下のようになります。
下図のデータから、機上測定でも測定誤差1μm以下での高精度な測定ができていることが分かります。
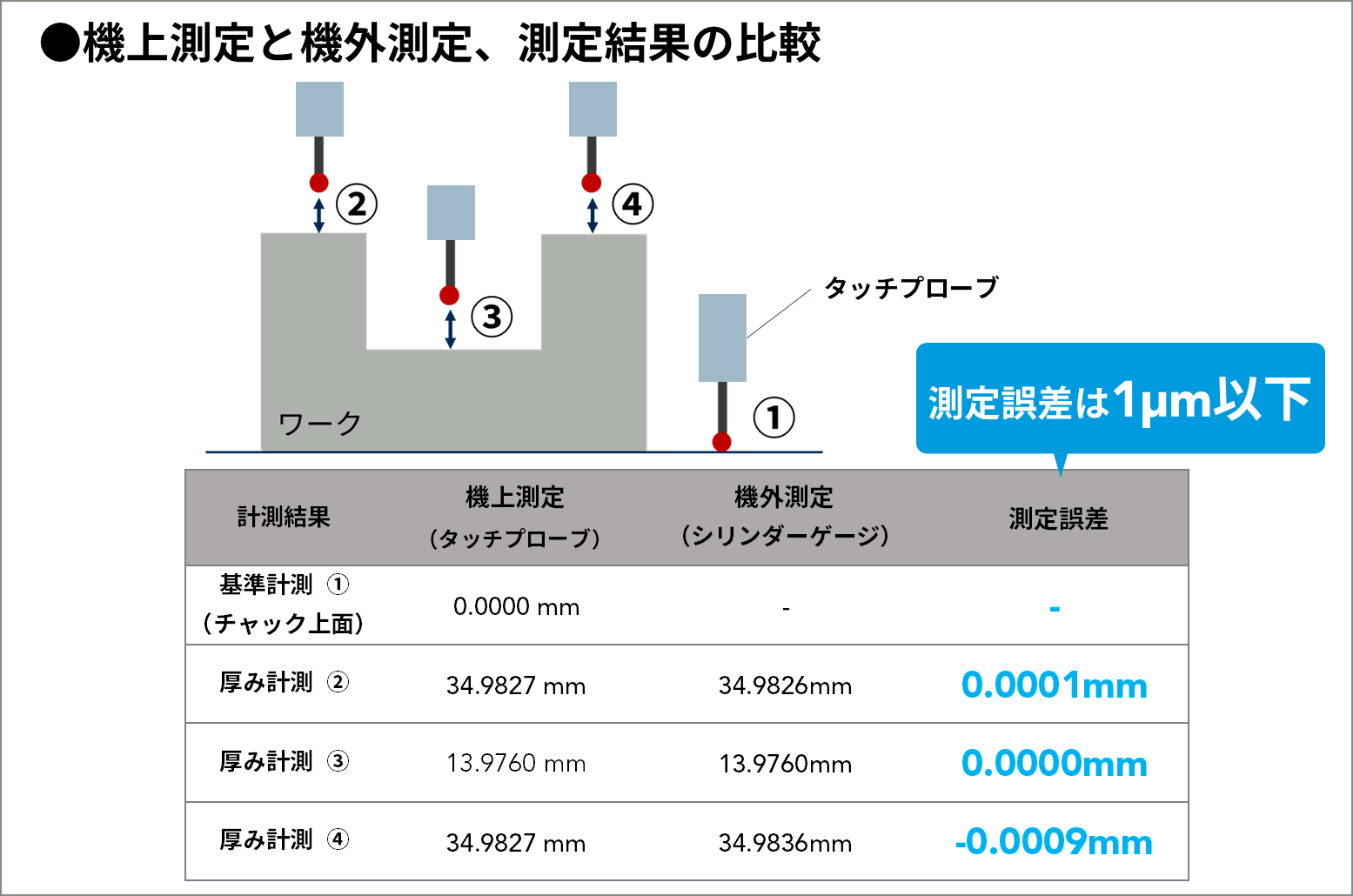
機上測定では加工後のワークを測るため、「熱膨張で数ミクロンワークの寸法が変わってしまう」という懸念の声も一部あります。
重要なのは、「測定結果を工数削減に活用すること」です。
あらかじめ熱膨張係数を考慮し、加工現場での追加工の基準を設けることで測定後の手戻り回数を削減するなど、効果的な測定結果の活用方法が見つかるでしょう。
機上測定が可能なCNC平面研削盤の紹介
現在、岡本工作機械製作所の平面研削盤HPGシリーズで機上計測装置「Quick Touch(クイックタッチ)」では機上測定が可能です。これまで機上測定で考えられていた
- コストが高く導入できない
- プログラミングができないから導入できない
- スタイラス、センサを破損するのが怖い
といった先入観を改善するオプションとして、同社では以下のように提案しており、従来よりも手軽に導入ができるようになりました。
- リーズナブルな導入コスト
- 専用の対話式プログラミング(プログラミングレス)機能でだれでも使用可能
- 繰返し精度1μmの測定精度
【動画】NC研削盤の機上測定デモ
今、機上測定が重要な 2つの理由
理由1:製造現場の測定方法は適切ですか?
メーカーは常に顧客との要求品質とコストのジレンマで悩みが尽きません。
年々、クライアントからの要望もシビアになっています。
- 「検査項目が増えたが価格に乗せられない、無償検査をせざるを得ない…」
- 「(測定機が)高価だから、使わないともったいない…」
- 「検査人員の確保が難しくなってきている」
とお金を生まない検査工程が増え、人手(コスト)に悩む現場の方が増えています。
負担の大きい検査体制は、見落としや不正発生を生み出すリスクがあります。
まず測定ルールを改善するには、
・今の測定品質をもっと低コストで実現できないか?
・コストが見合っているか?
をまず見直す必要があります。
納入先が求めている品質を「機上測定」でも判定可能かどうか?を検証し適切に判断する必要があるでしょう。
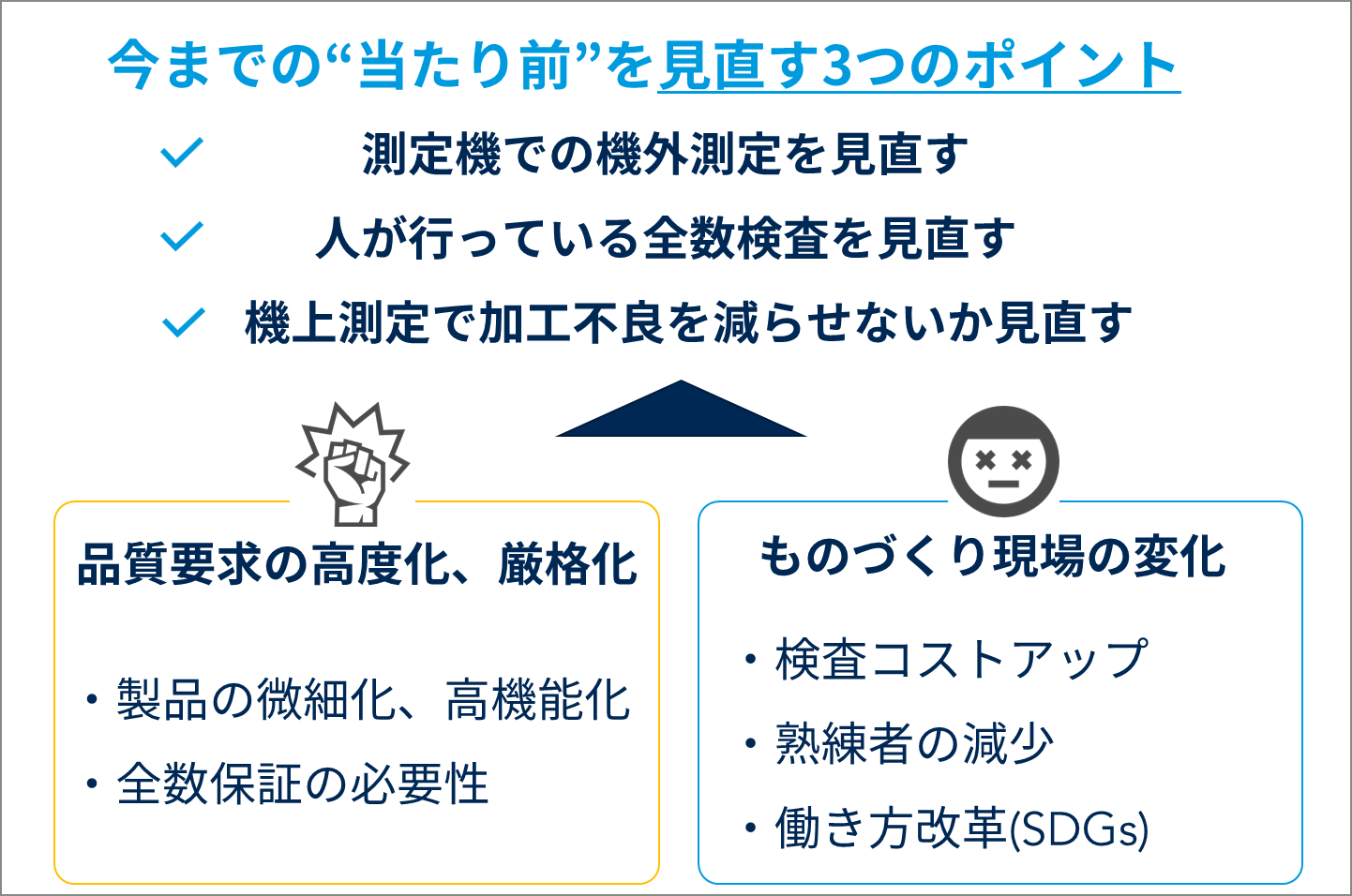
理由2:「稼働率が落ちるから機上測定したくない!」はもう古い?
「自部門だけの部分的な改善」ではなく、「部門を横断した製造工程の全体最適化=工程集約」が求められています。
これまで
- 加工部門は「機械の稼働率」を上げる改善
- 検査部門は人海戦術や専用の検査ラインで不良を見逃さない改善
という部門別の最適化が優先されていました。
しかし、これからは1つの部門どちらにとってもメリットのある改善が重要です。
今は問題なくても5年後、10年後に、今の組織体制や仕組みを維持できるか?を考えなければいけません。
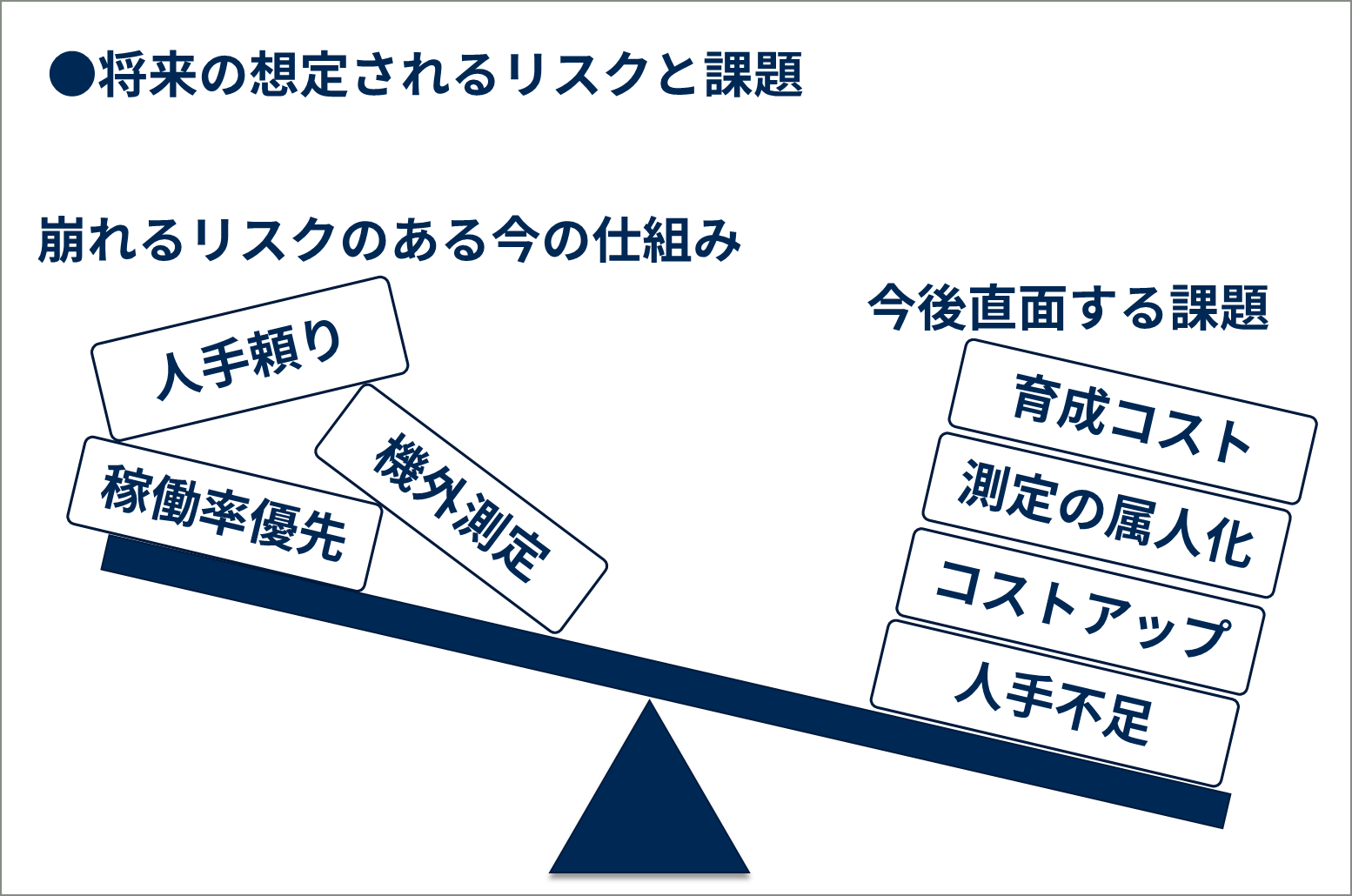
機上測定と三次元測定機の使い分けは?
測定は品質を守る、いわば関所です。
特に金型や航空部品など精密加工部品において三次元測定機は高い信頼性を発揮する測定器でしょう。
納入先からの指定など制約があるユーザも多く今後も必要になるシーンは多くあります。
一方で、専門性の高い測定器には以下のような維持・管理コストが伴うことを知っておかなければなりません。
- 温度管理
- 加工部門と測定部門との連携
- 測定機器の操作方法の習得
- 測定器自体はおカネを生まない
最終仕上げレベルの精度が要求されるCNC平面研削であれば、加工だけでなく高精度な測定が可能です。
測定を研削盤に集約できれば、検査作業者の育成コスト削減や人による測定のバラつきの改善も期待できます。
バランスよく組み合わせて活用してみてはいかがでしょうか。
まとめ:機上測定のメリットとデメリット
ここまでの機上測定と機外測定の主なメリットデメリットを整理すると、
●メリット
- 機上測定:人の移動に関わる段取りや工数が削減される。
- 機外測定:高精度な測定が可能。
●デメリット
- 機上測定:三次元測定機などと比べると測定精度は外乱を受けやすい。
- 機外測定:測定に伴う工数が大きく、維持費(人・機器・運用)が高い。
その他メリットデメリットをまとめると以下のようになります。
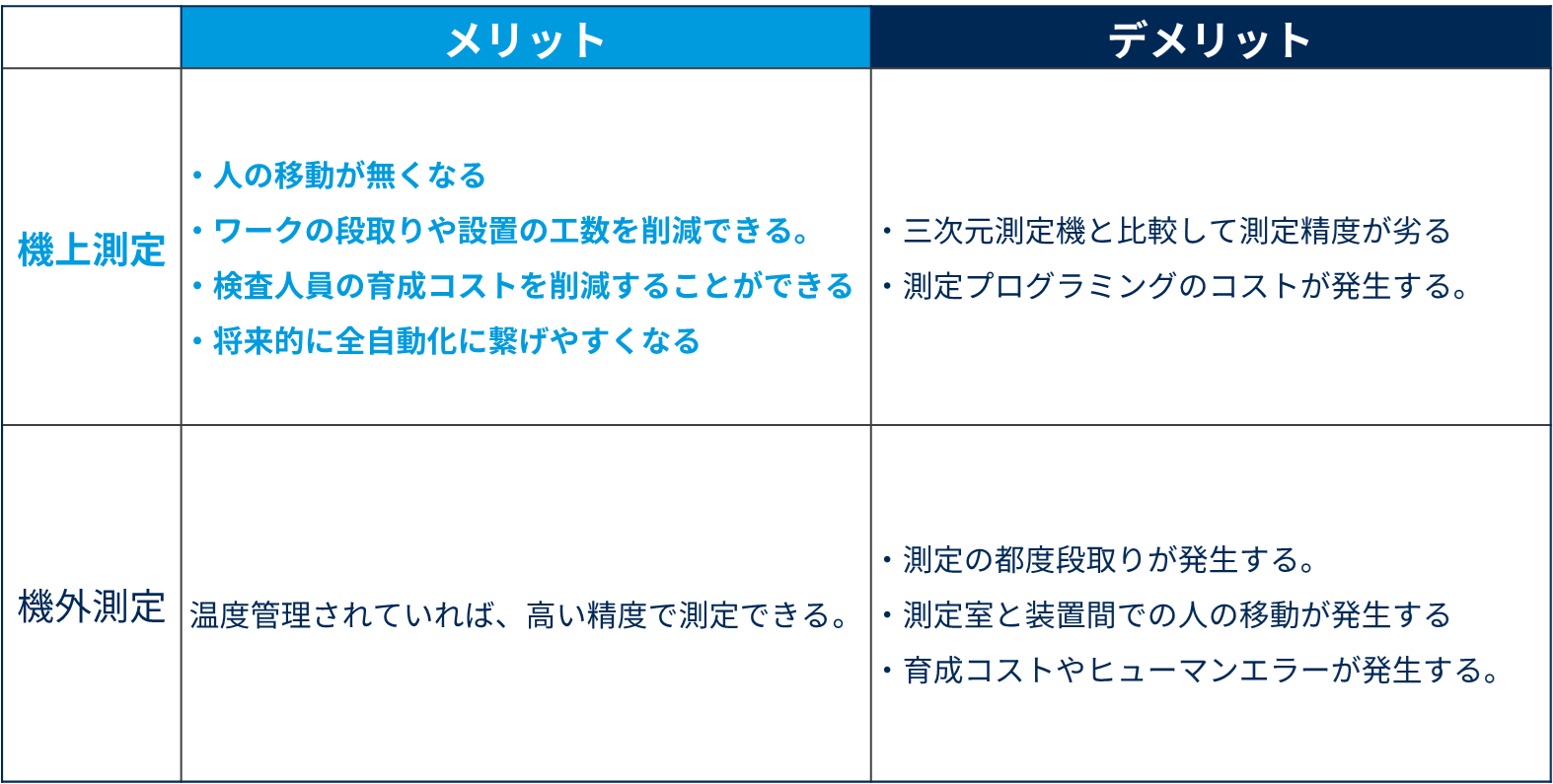
繰返しになりますが、測定は加工品質を見極める重要な工程です。
一方で、測定にかかる工数の付加価値は、理解されにくい領域でもあります。
製造部門と品質管理部門のニーズに折り合いをつけながら製造現場全体の最適化を行う方法としての「機上測定」について、一度考えてみてはいかがでしょうか?
研削盤で使える機上測定用タッチプローブ
超小型で省スペースでのワークの原点出しを自動化
砥石がワークに当たったときの火花、音で確認している、「砥石の当て込み作業」の自動化を徹底解説します。
機上測定との組み合わせで、NC平面研削盤の段取りから加工までが全自動化する業界初の技術です。
モノタロウ・ミスミですぐに購入に可能!
タッチプローブK3Sシリーズの一部ラインナップはモノタロウ・ミスミから即購入できます。
・モノタロウ
・ミスミ
その他オプション、カスタマイズのご要望は お気軽にお問い合わせください。