【導入事例】生産性が4倍以上に!CNC平面研削盤の機上計測の活用法とは?
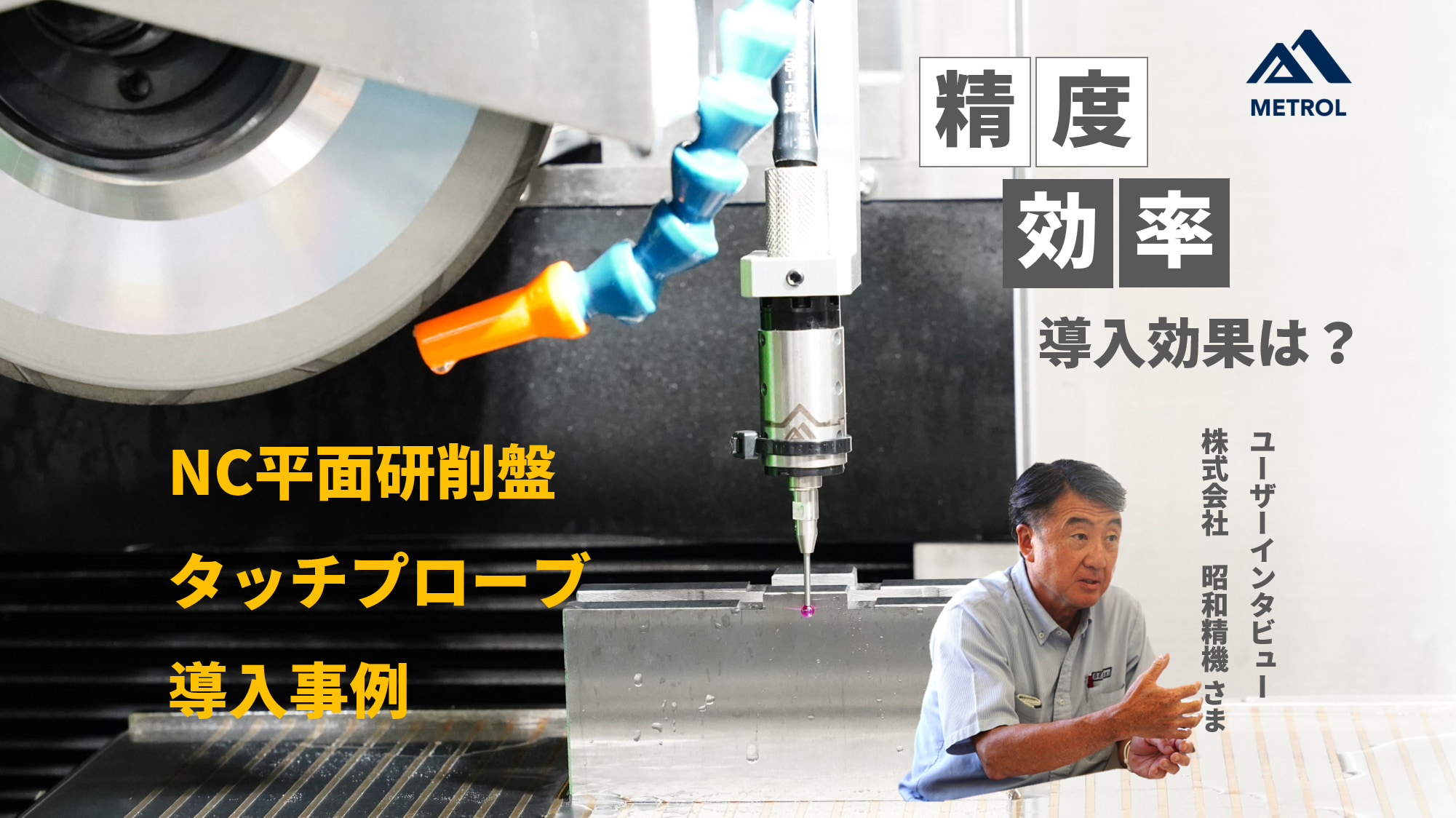
研削・研磨加工に従事されている皆様、以下のようなお悩みはありませんか?
- 「精度が安定せず、やり直し品が多数出てしまう・・・」
- 「加工に人手と時間がかかりすぎて、生産性が上がらない・・・」
- 「若手への技術継承がうまくいかず、ベテランの負担ばかり増してしまう・・・」
本記事では、タッチプローブを搭載したNC平面研削盤を導入したことで 上記のような課題をまるっと解決し、生産効率を大幅に改善されたユーザー様の事例をご紹介します。
センサーを導入した経緯や、実際の効果などについて、率直なご意見をお伺いしました。
キーワードは、
『研削・研磨加工の完全自動化』
『ワークの機上計測』
ぜひ、ご一読ください!
目次
ユーザー様ご紹介
取材にご協力いただいたのは、千葉県松戸市の 株式会社 昭和精機 様。
昭和精機様は、主に工作機械向けの金属部品の研削および研磨工程を幅広く手がけています。
特に厳密な精度が求められる「検査機器部品」の受注も多く、その“技術力の高さ”はお取引先から厚い信頼を寄せられています。
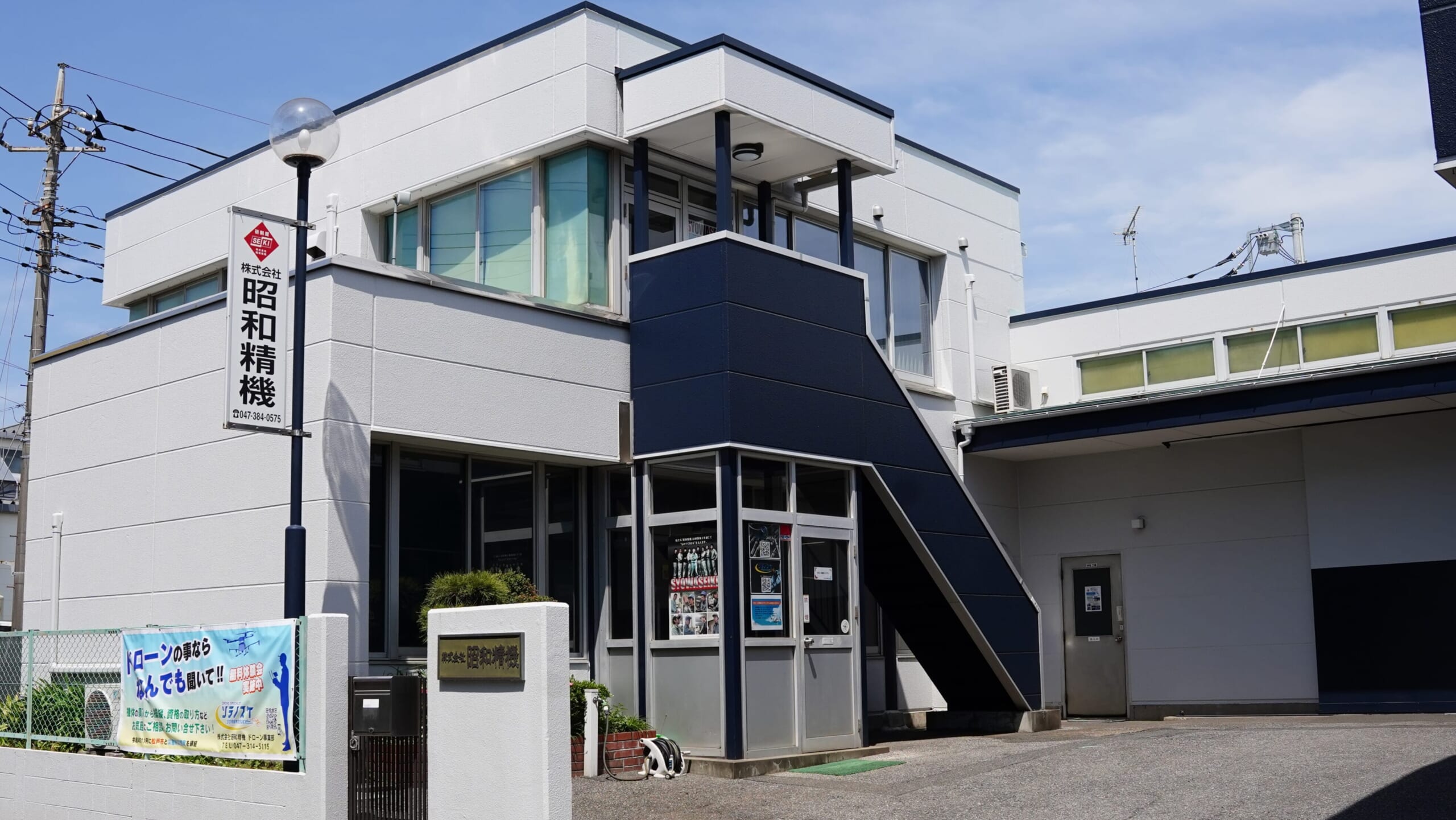
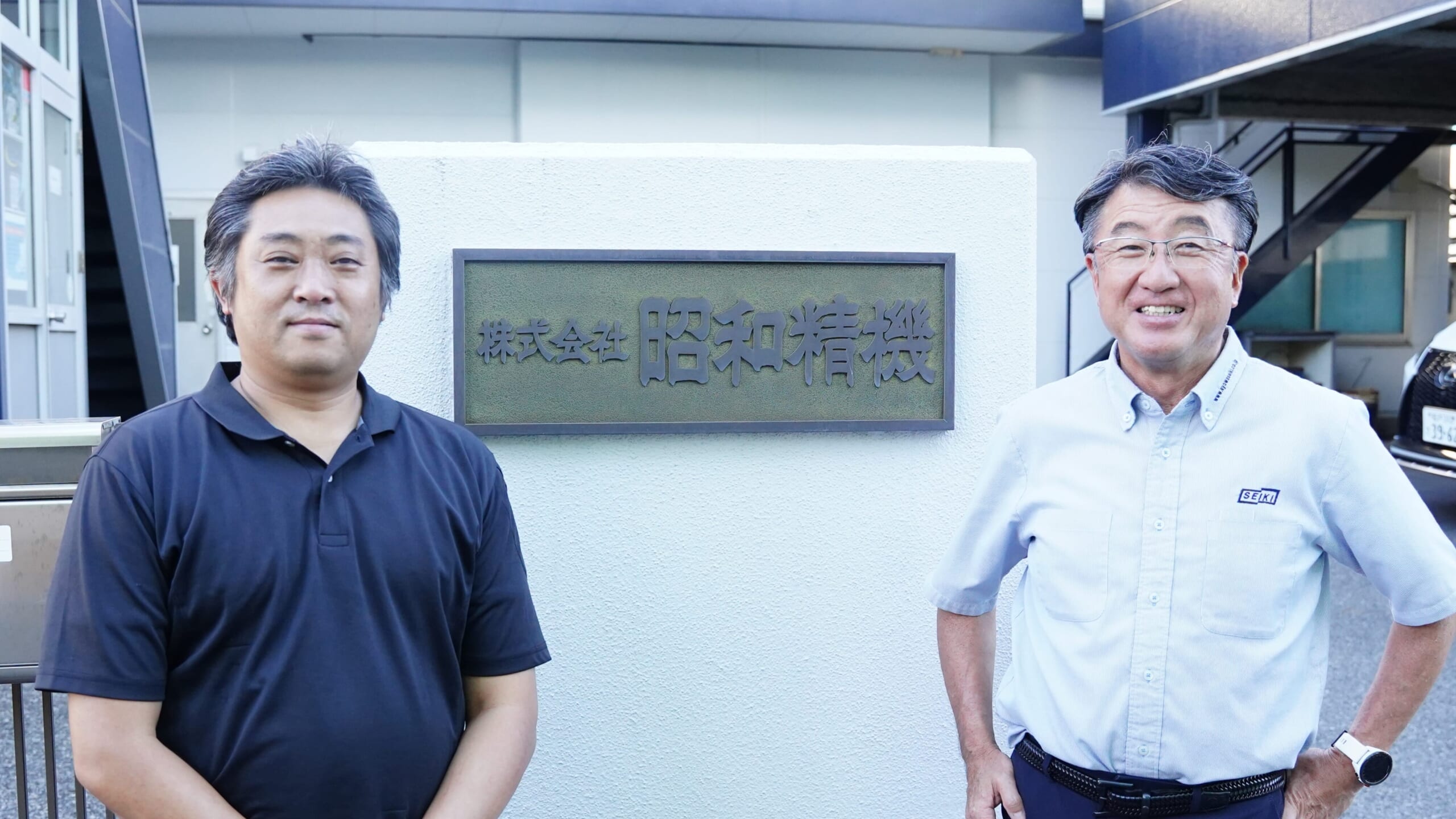
研削・研磨加工とは?
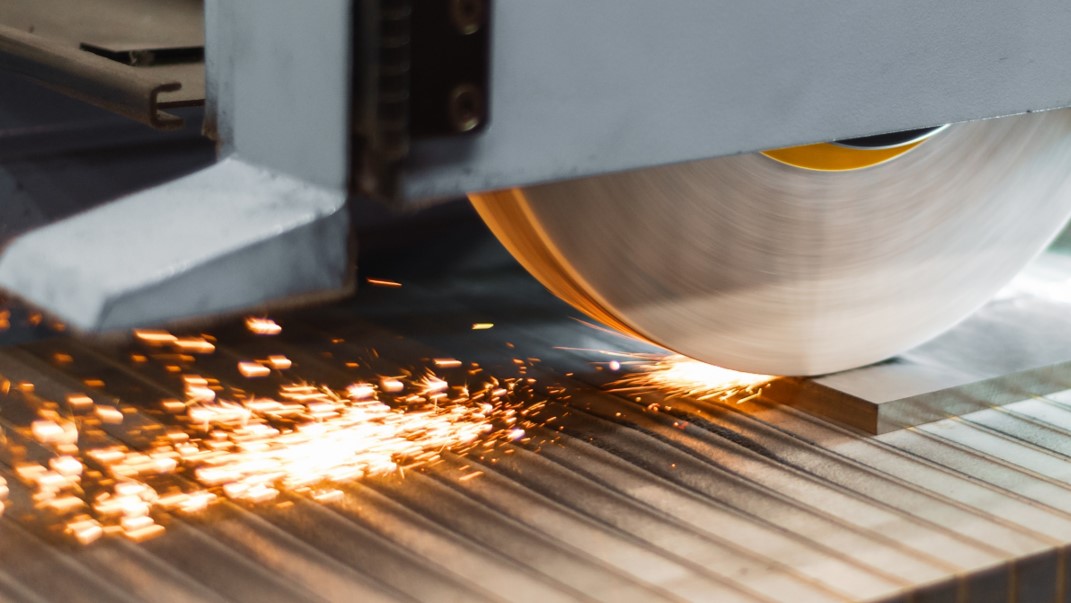
「研削」は加工の最終工程であり、出来栄えが品質に直結するため数ミクロンレベルの厳しい精度が求められます。
ロボットの摺動面や、自動車・航空機産業などで使われる精密部品などを製作する上でも重要な加工です。
研削工程=熟練者頼りの精密加工
研削工程では、砥石とワークの接触時に発生する
・火花
・音
・匂い
・研削油の流れる泡の膨らみ方 など
数値では測れない“人の感覚”に依存する部分が多く、長年の経験に裏打ちされた高い技術力が必要となります。
技術の習得が特に難しい分野だと言われています。
【取材メモ】 昭和精機の従業員は平均年齢27歳と若手が多い。 創業(1975)当時から会社を支える70代〜80代の熟練加工者が週2回ほど出社し、若手に研削研磨技術の伝承を積極的にすすめている。
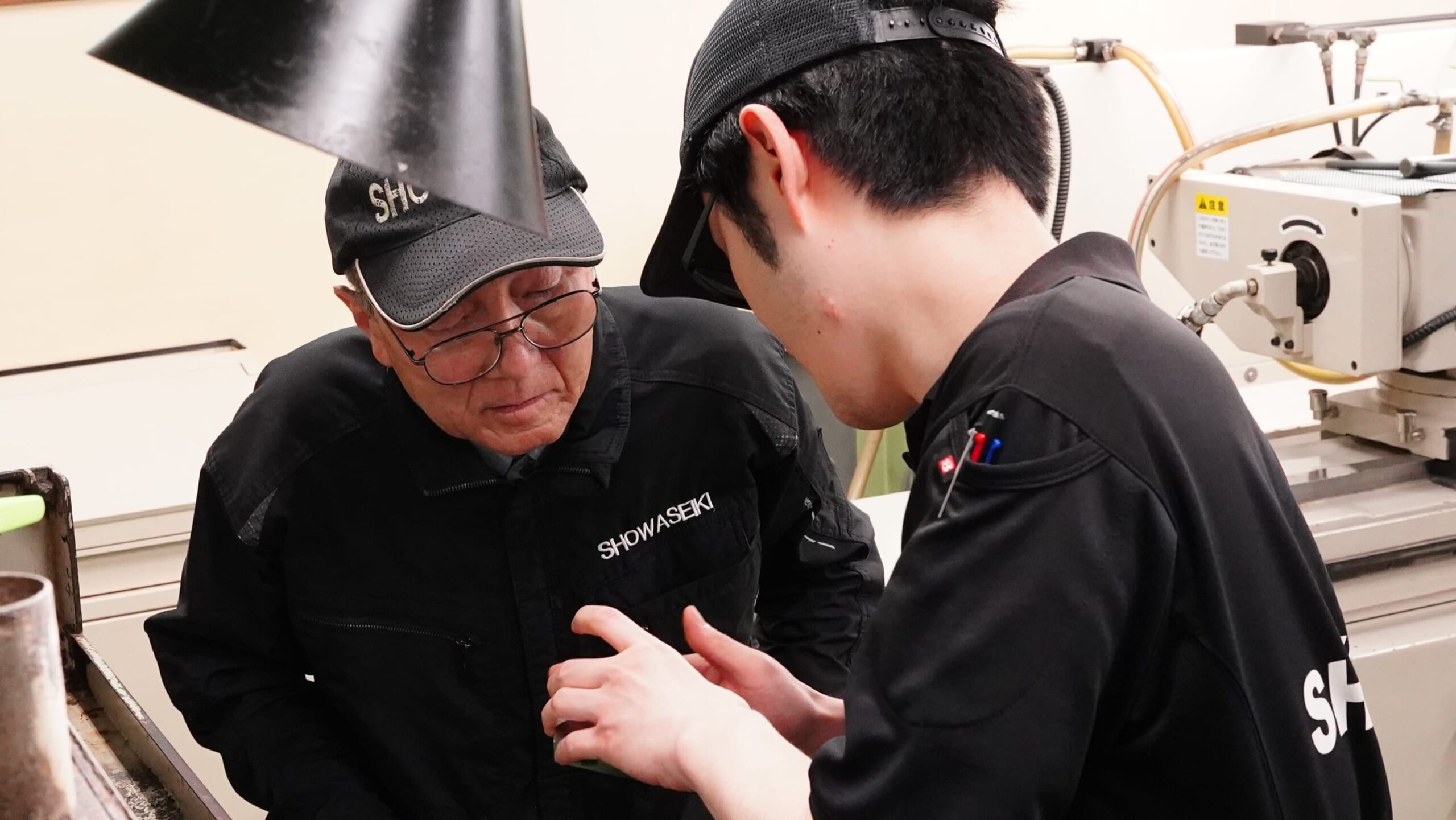
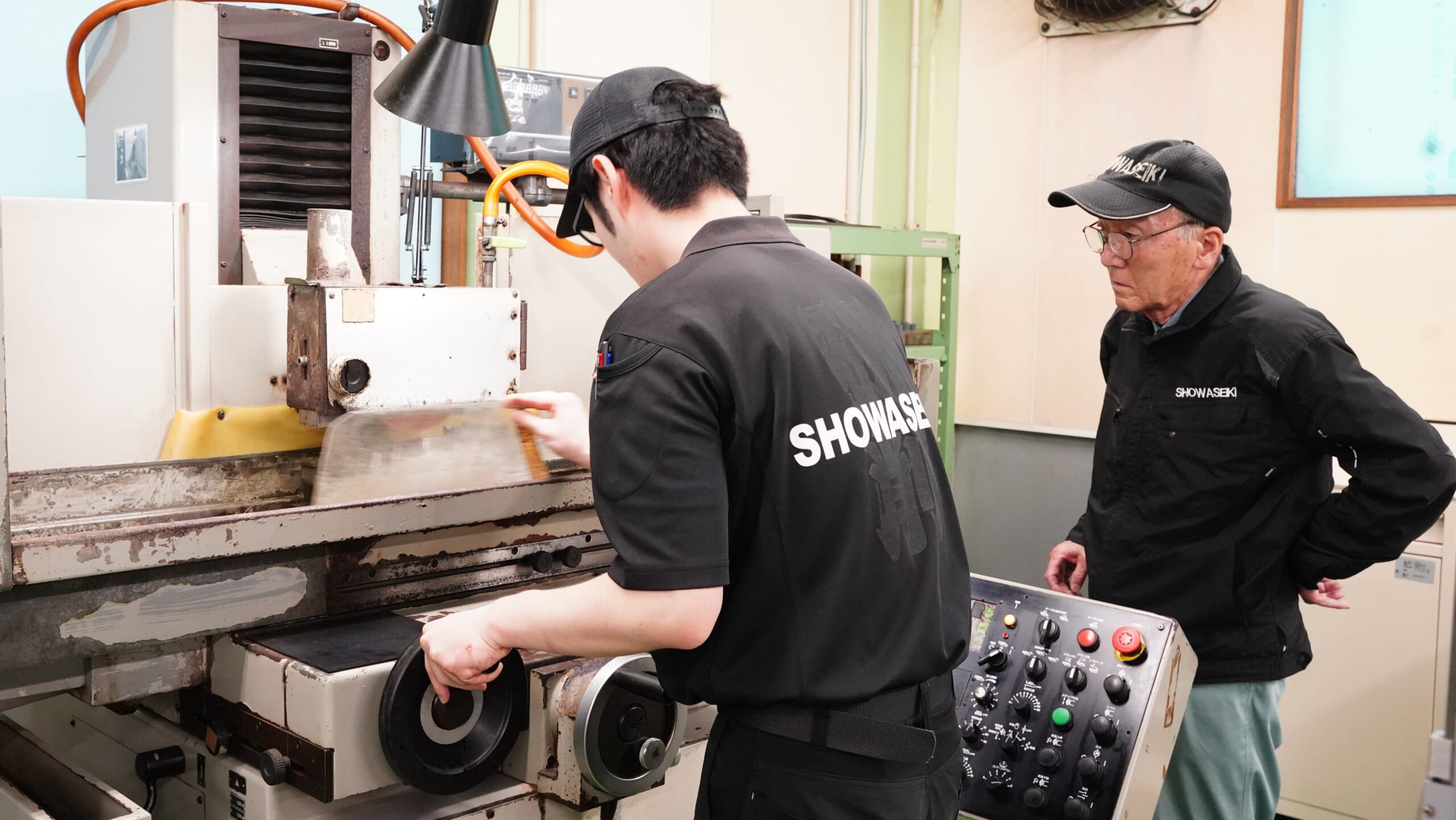
昭和精機様の課題:「生産効率」と「精度」の両立
品質を落とさず、作業時間を短縮したい
研削の精度は、
①加工者の技量
②気温
などの「環境」に左右されやすく、資金力や人材に限りがある中小企業が安定的な品物を提供し続けるのは簡単ではありません。
昭和精機様では、完璧な精度を追求するあまり、見積もりの倍以上も作業時間をかけてしまうことがあったといいます。
小林社長:
「普通は、ある程度の±値を決めてその公差範囲内で仕上げていくものですが、弊社の従業員は、“何が何でも誤差ゼロを狙う”というこだわりを皆が持っているんです。」
風間部長:
「『昭和精機の部品がどこよりもいい!』
『ピタっとワーク寸法が合っているから組みつけも早いよ。』
と“図面にのらない精度の高さ”をお客様から褒めてもらうとその時は嬉しいのですが、会社に戻ったら見積以上に作業時間が押していて『早く仕上げなさい!』と急かすことも珍しくありませんでした。」
従来の課題:「段取り作業」と「追加工」の工数
従来、昭和精機様では、以下のプロセスをワーク一面の加工につき4・5回繰り返し行っており品質を追求するための工数に悩まされていました。
・作業者が研削盤からワークを降ろす
・作業者がダイヤルゲージでワークを計測する
・再びワークを研削盤にセッティングする
・追加工する
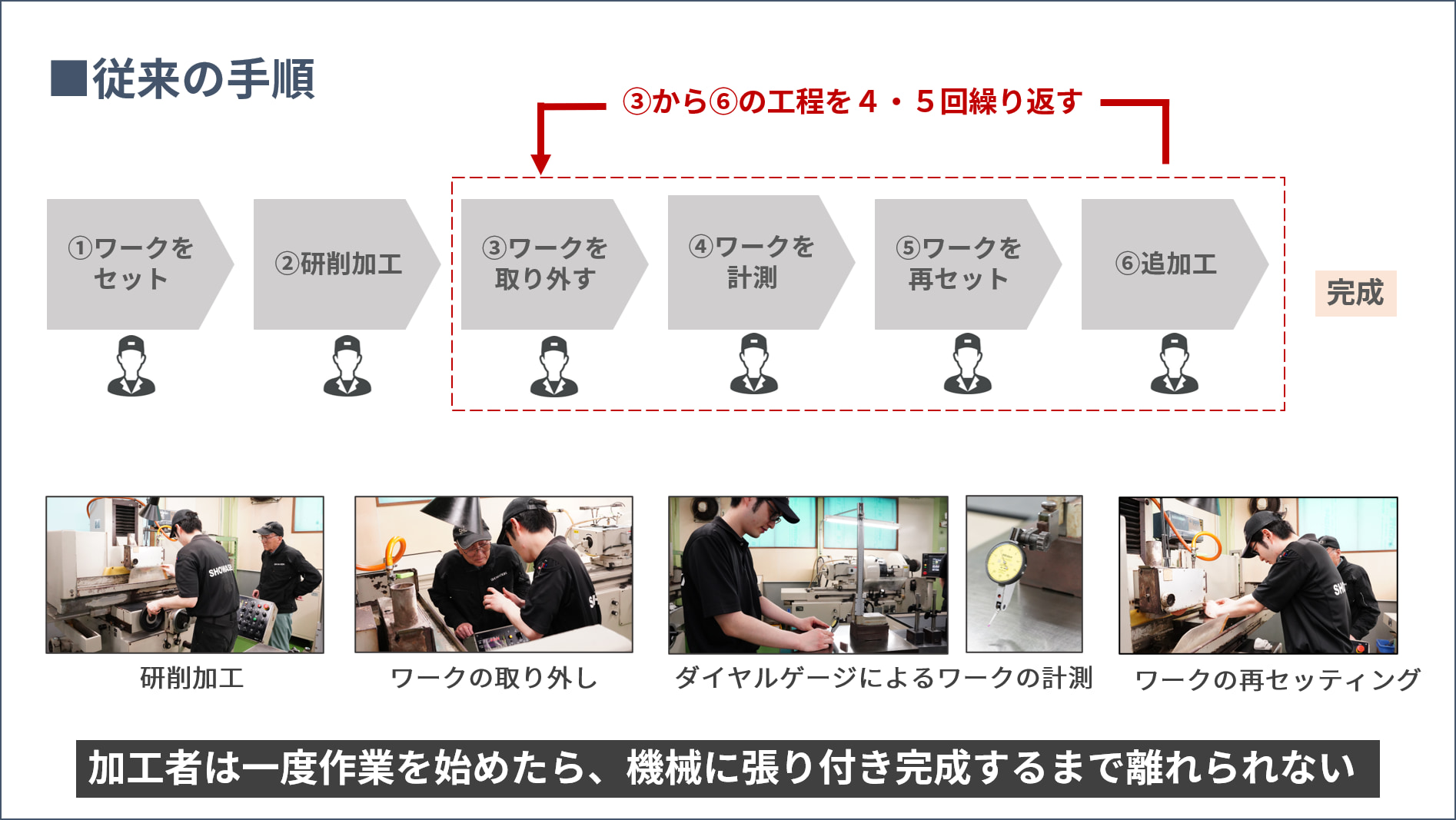
さらに、小林社長は、 ワークを再セッティングするときの「位置決め精度(再現性)」にも問題意識をお持ちでした。
“ワークを着脱する際に生じる加工位置のズレ”です。
計測のために一度ワークを機械からおろしてしまうと、人手で再設置の加工原点を“ゼロ”に戻すのは不可能です。
精度を確保しつつ、作業時間を短縮する方法を長年模索されてきたそうです。
従来のプロセスに起因する課題
・計測するためにワークを機械から着脱する人手と時間的コスト
・ワークの着脱によって生じる加工原点の再現精度
「研削盤の機上計測」導入の決め手
研削と計測を“機上で完結できる”センサーが欲しかった
小林社長は長年、機上計測の用途で様々な研削盤メーカーに問い合わせていましたが、「精度を確保できるセンサーがない」と断り続けられていたそうです。
そんな折、JIMTOF(2022年11月)で【岡本工作機械製作所 研削盤Grind-X】に搭載されたメトロールのタッチプローブを発見。実際にデモ実演をご覧になり、即購入を決断されました。
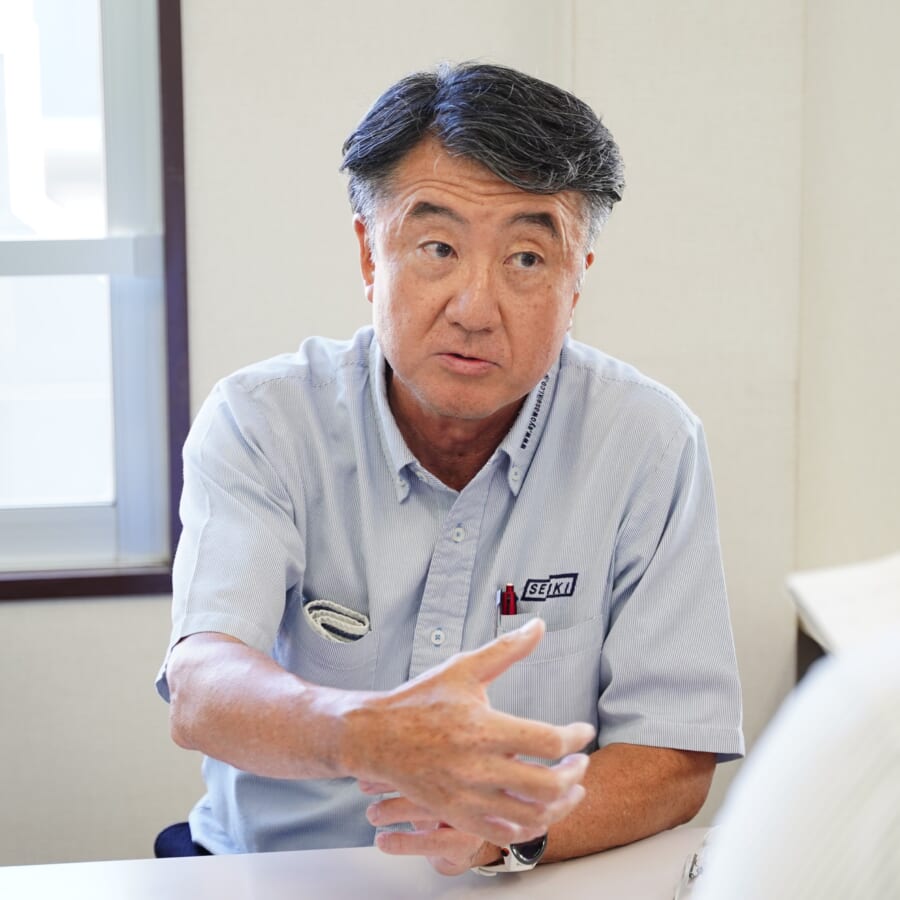
小林社長:
これまでどの研削盤メーカーも唯一出来なかった、平面研削盤における「前後方向の測定」が可能になったのは、画期的でした。
ワンチャックで一度ワークをセットしたら、完成まで全て自動でやってくれます。加工中にワークを一度も動かさないから精度も保証できる。
取引先からの要求精度が高いほど、メトロールのタッチプローブが活きてくると思いました。
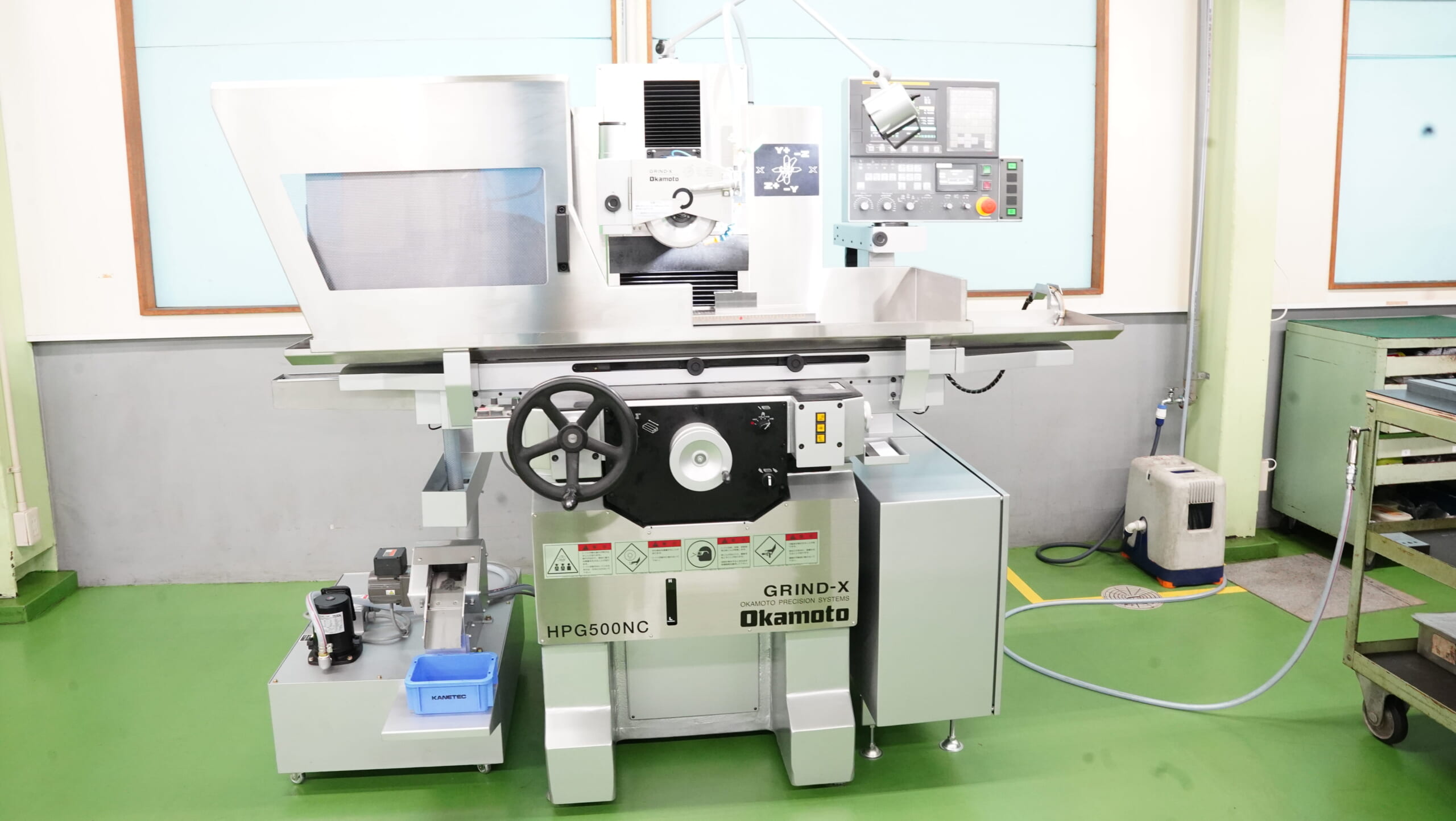
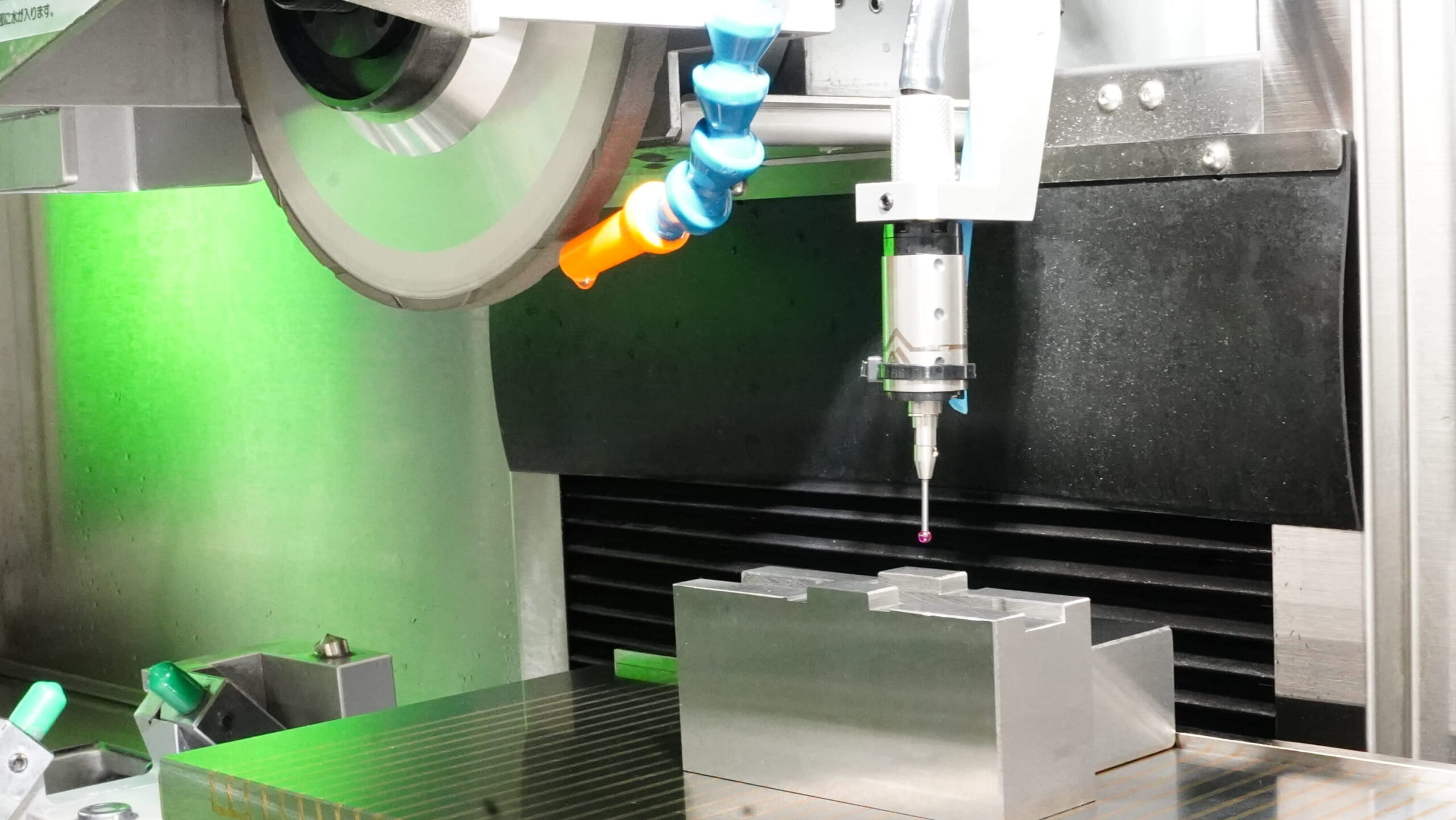
機上計測の4つのメリット
機上計測を導入しワークを機械から一度もおろすことなく、計測から追加工まで「研削加工の完全自動化」が実現したことで、昭和精機様では以下の4つのメリットがありました。
【タッチプローブによる機上計測のメリット】
1. 計測にかかる工数が4分の1以下に削減
2.ワークの着脱がなくなり、複数ワークを同時加工する「多数個取り」が実現
3.装置に張り付いていた作業者が解放され、別作業が可能に
4.ベテラン技術継承の負担を軽減
それぞれのメリットを解説していきます。
機上計測メリット1:ワーク計測の工数が4分の1以下に
加工中にワークを計測するために機械から着脱し、再セッティングする段取りが機上計測では一切不要になりました。
手作業では4,5回は追加工を繰り返していたので、工数は単純に計算しても4分の1に削減しています。
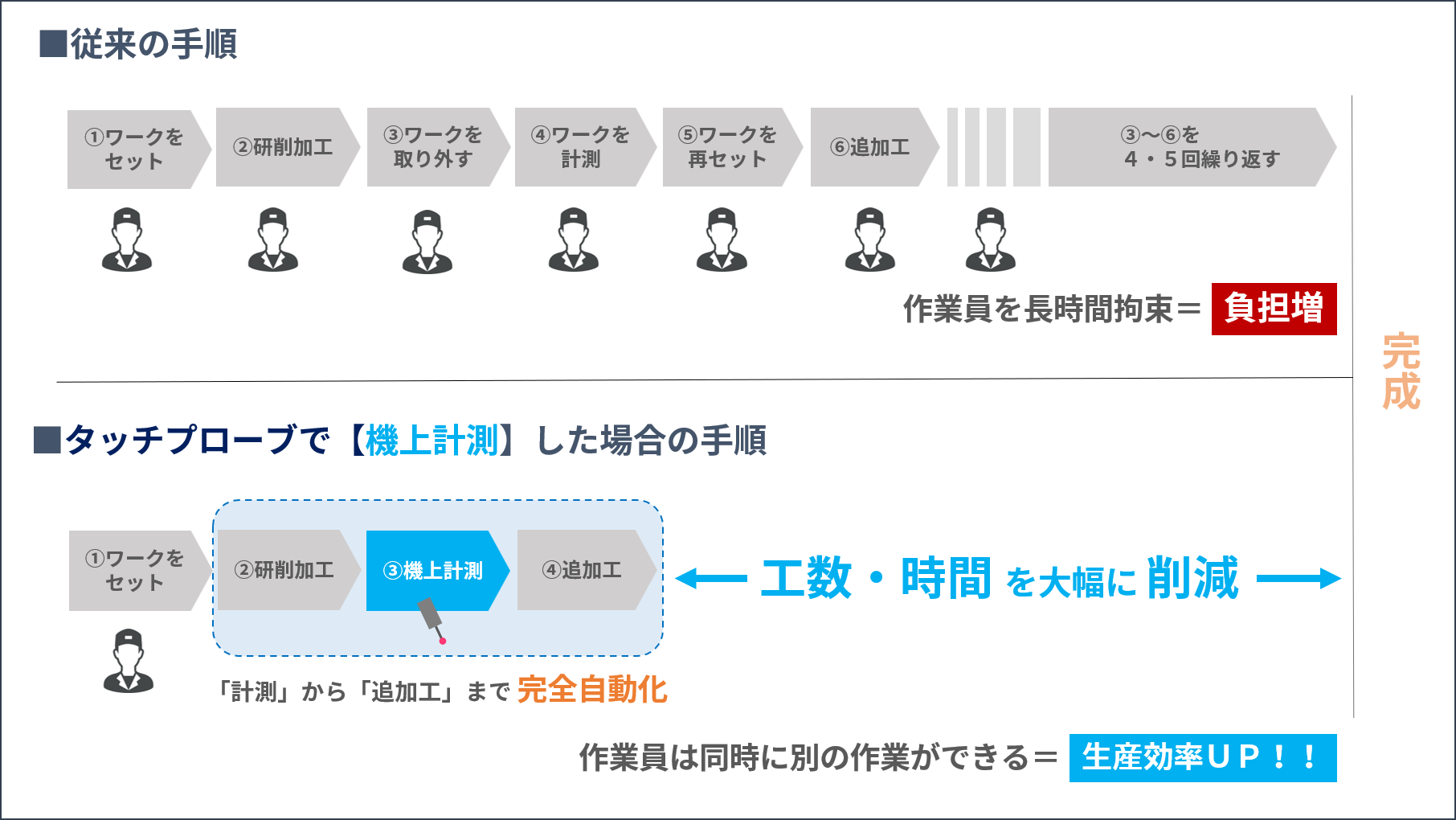
機上計測メリット2:ワーク「多数個取り」で生産性が4倍に。
機上計測はワークの着脱が不要なため、従来は設置位置のズレを考慮して1個ずつしかできなかった加工を、複数個並べて同時に加工する「多数個取り」が可能になりました。
昭和精機様の場合は、ワーク4個をまとめて加工されていて、作業効率がさらに上がっています。
(※【機上計測で生産性が大幅にアップする理由】については、こちらでも詳しく解説しています。)
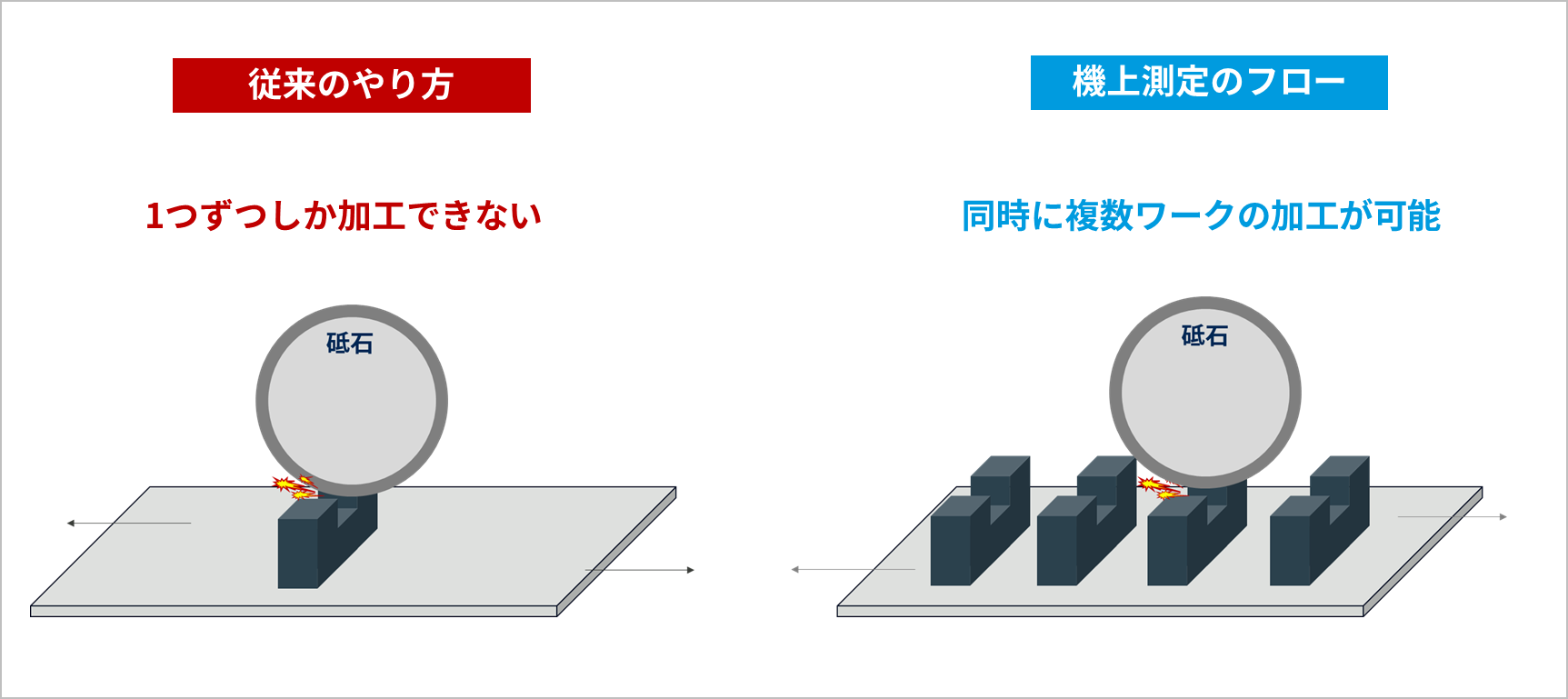
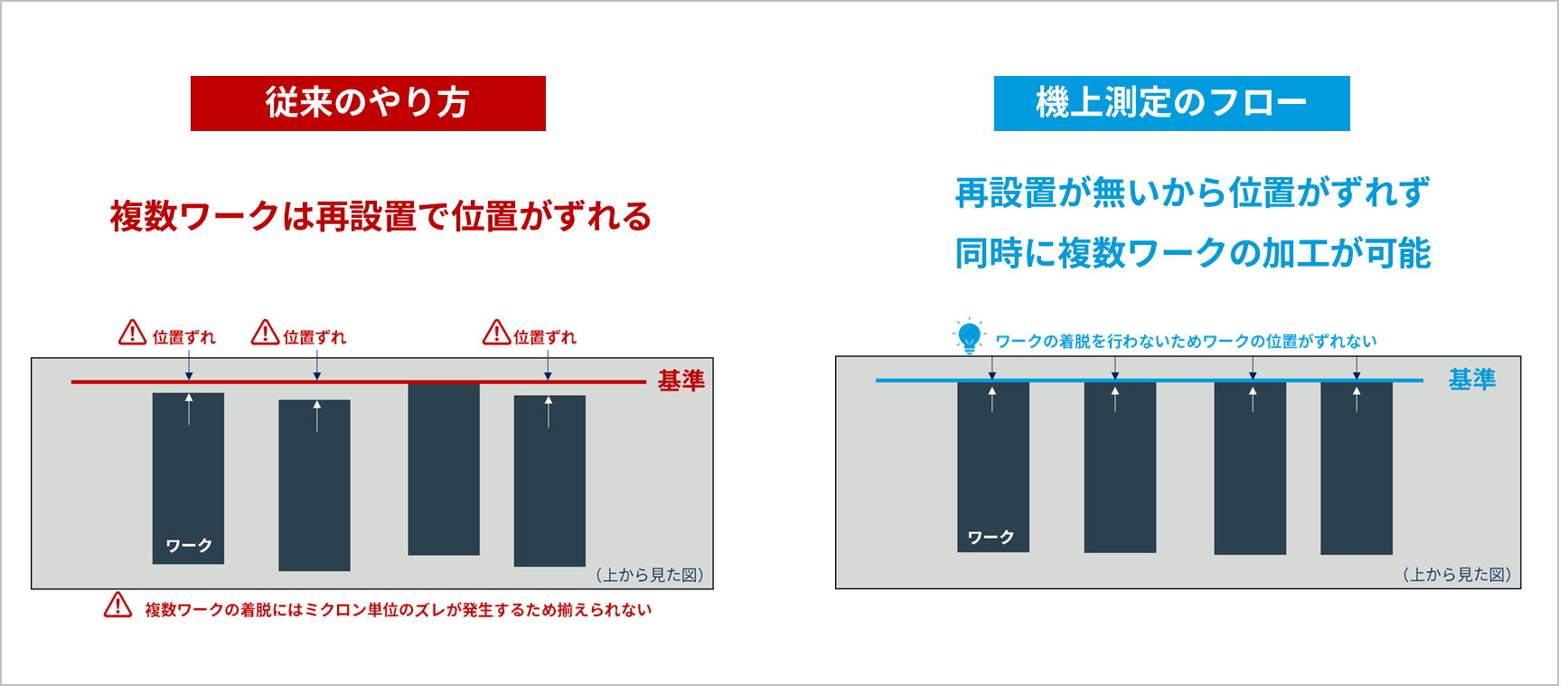
機上計測メリット3:装置に張り付いていた作業者が解放され、別作業が可能に
機上計測のプロセスでは、はじめにワークをセッティングすれば、あとはボタン一つで計測・追加工まで自動で完了します。
従来は、 作業員が終始機械に張りついて監視していなければいけなかったのが、機上計測の導入後は、同時に別の作業に当たることも可能になり、作業効率が飛躍的に上がりました。
「加工が始まったらトイレにも行けなかった(若手社員)」
そうですが、職場にゆとりが生まれたそうで、余裕の無さから生じるヒューマンエラーの削減も期待できるのではないでしょうか。
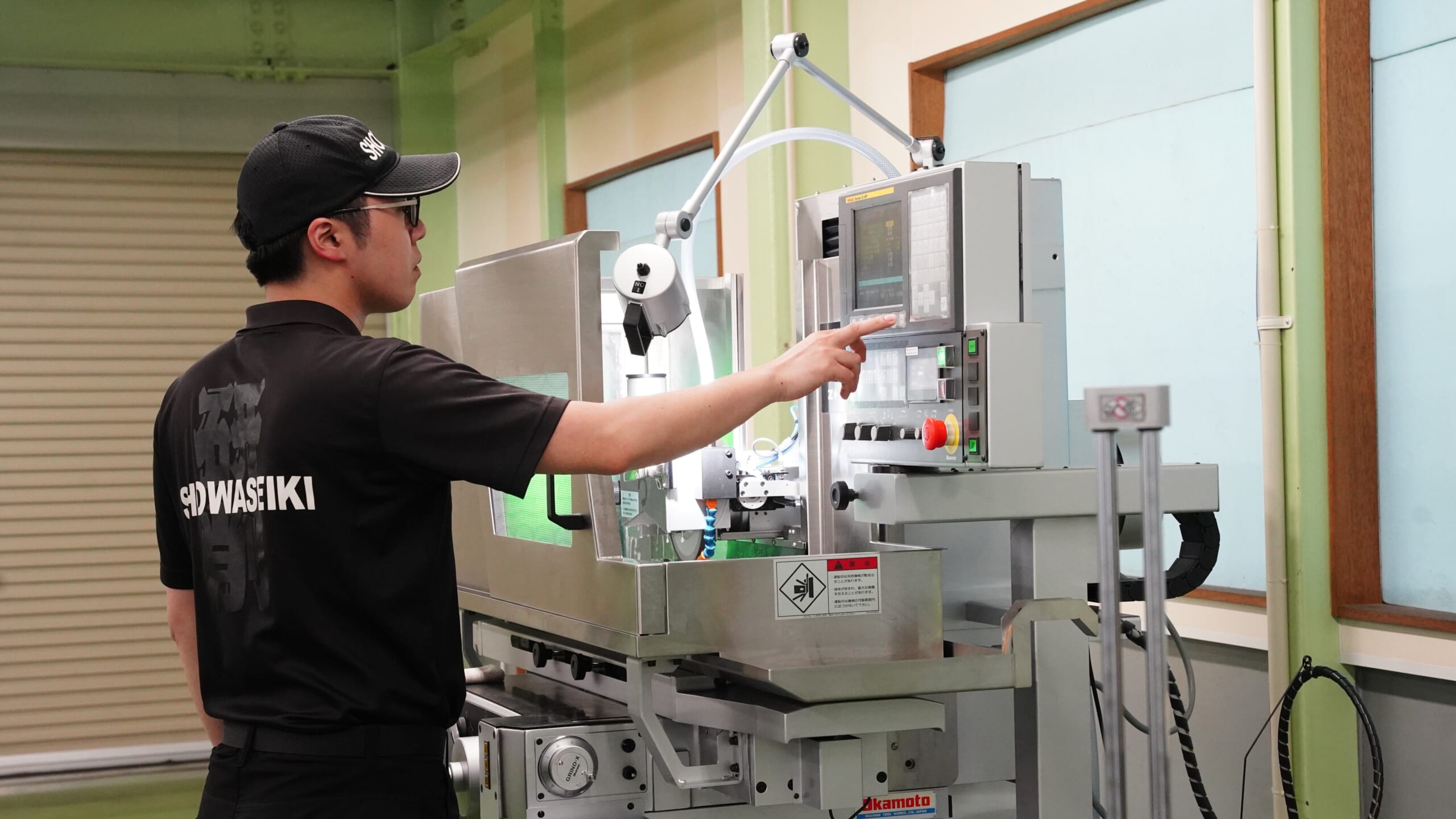
機上計測メリット4:ベテラン技術継承の負担を軽減
昭和精機様では、ベテラン加工者のサポート体制もあって、若手への加工技術の継承を積極的に進めています。それでも、難易度の高い加工は熟練者に頼らざるを得ない場面も多いといいます。
機上計測の導入で、 経験の浅い加工者でも操作が可能に。若手に活躍できる場を提供し、限られたベテランに偏る負担を軽減しています。
小林社長:
例えば、仕上げの2ミクロンを調整する加工は、ベテランの限られた熟練者にしかできない作業です。
でも、機上計測を導入したことで、プログラムを覚えれば、若手からベテランまで全員が作業できるようになりました。
うちは若い世代が多いですが、手作業で感覚を頼りにやるより、プログラミングや機械の操作を覚えるのが本当に早いですね。
『人手不足』『後継者不足』はモノづくり業界全般の課題となっていますが、ここでは『作業の標準化』にセンサーが一役買っています。
機上計測の精度は?「人手による検査と同等以上」
昭和精機様は納品の「全数検査」を実施されています。
もともと高かった歩留まり率ですが、機上計測の導入でさらに向上し、手直し品がなくなりました。
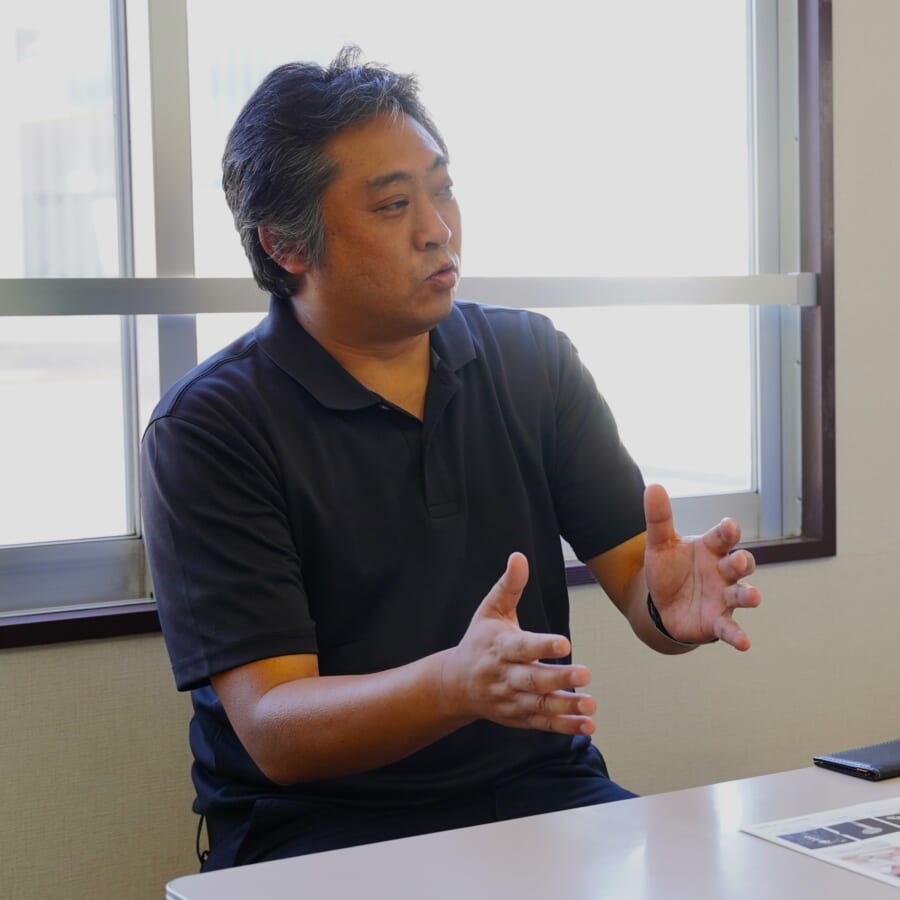
昭和精機 風間部長:
「手作業の時には全数検査をするとどうしても数個はやり直しが発生していましたが、タッチプローブで機上計測して加工したものの中には不良品が全くありません。
正直、機械が入った時は本当に精度が出るのか、人がやった方が正確なんじゃないか、と半分疑っていた部分もありましたが、こんなに繰返し精度がでるのかと驚いています。 」
「精度の追求」と「生産性向上」への挑戦は続く
今回採用頂いた「タッチプローブ」は、主に使用する若手従業員のみならず、ベテランの方々にも精度の高さでお墨付きを頂いたということで、段階的にタッチプローブ付きの研削盤を増設していきたいとお話しくださいました。
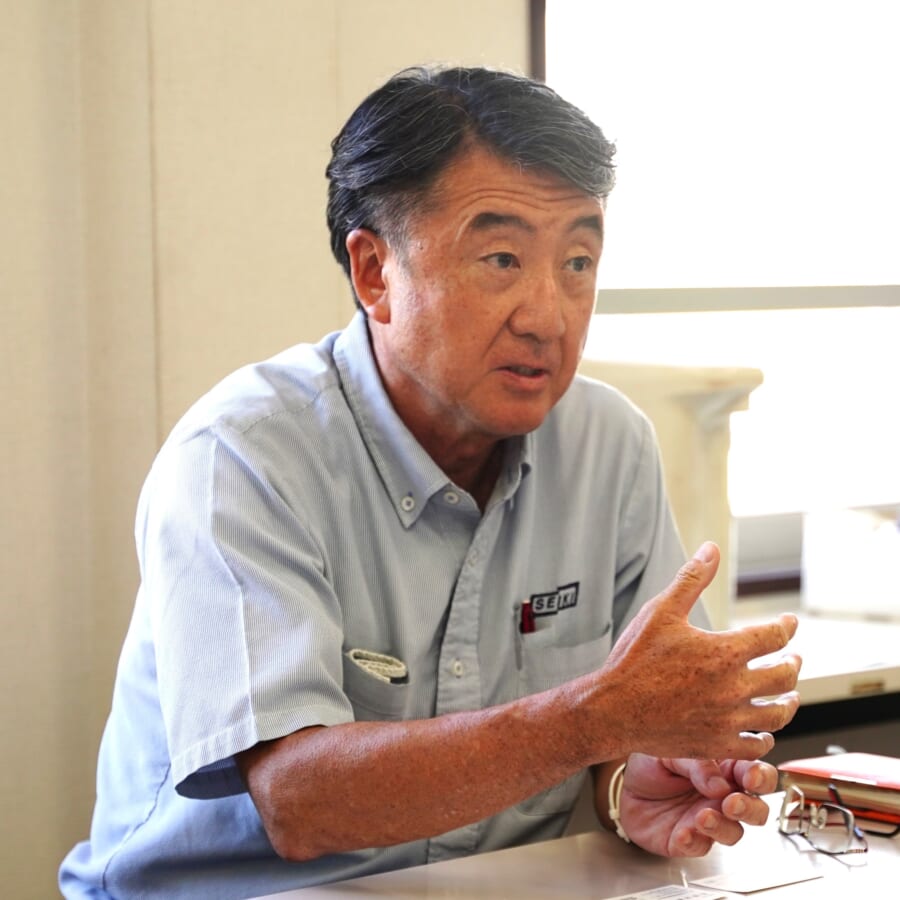
昭和精機 小林社長 :
「ベテランの技術が不要になった、ということではありません。今後、ベテランがどんどん減っていく中、ベテラン技術を若手と機械の進歩でどうカバーしていくか、が重要です。人を育てる事とは別のアプローチで、精度や価格に転化できる“見えないお金”をセンサーが生み出してくれている。それが一番大きいですね。
今回、機上計測の導入で従来からさらに1μという要求に応えられる様になり、それがお客様の安心・信頼に繋がれば嬉しいですね。精度の高さをこれまで以上に弊社の強みにしていきたい。 」
昭和精機様のさらなるご活躍に、メトロールのセンサーで陰ながらお力添えできれば幸いです。
ありがとうございました。
取材協力:株式会社昭和精機
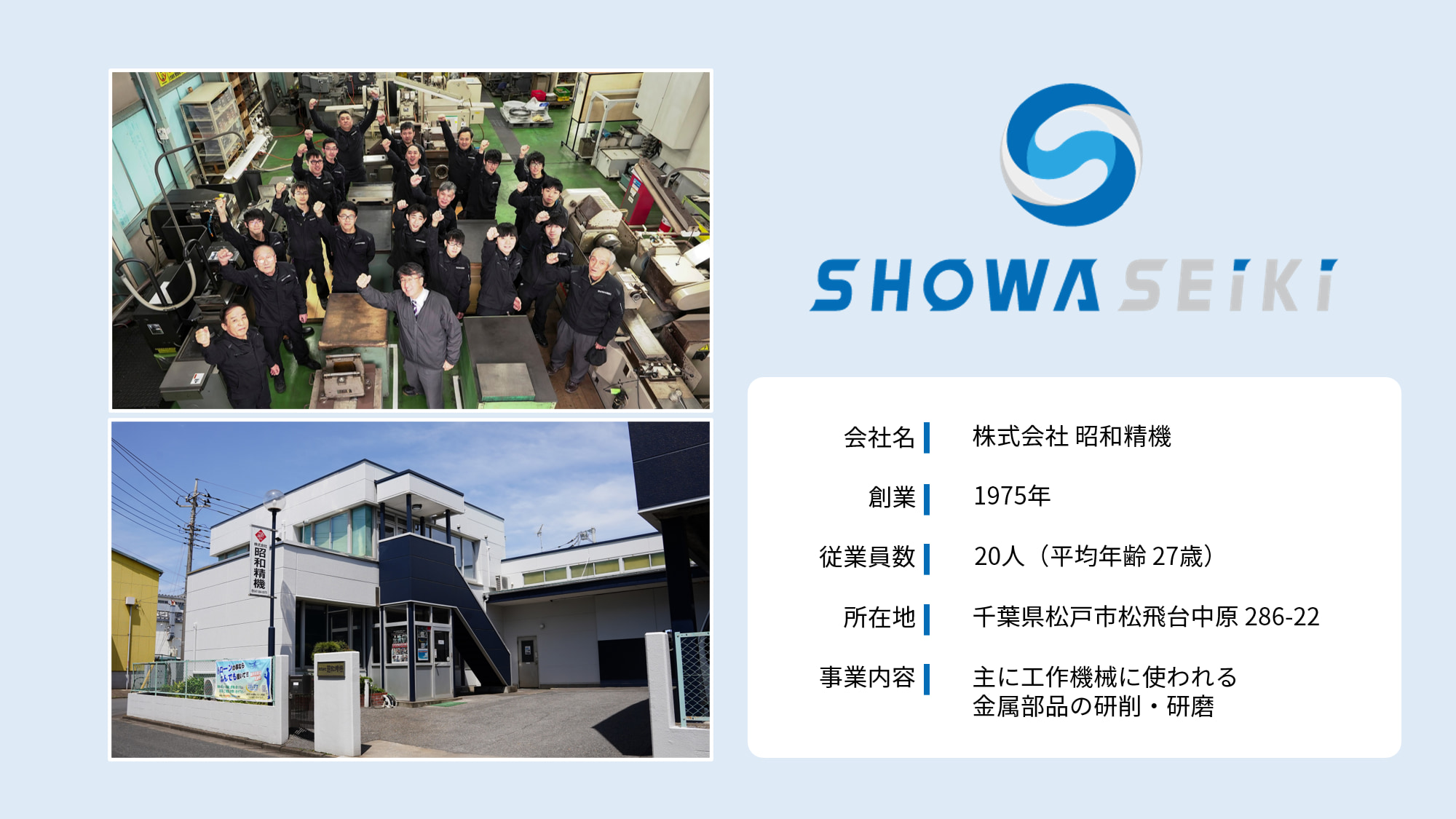
本事例でご紹介した製品はコチラ
機上計測用 小型タッチプローブ K3Sシリーズ
小型タッチプローブ K3Sシリーズ
業界最小径φ17.8mm~で設計され、スペースを取らずセンサが他工具に干渉しません。 特にCNC自動旋盤・小型複合加工機において、は加工ワークの端面を計測し、加工原点や外径・内径を測ります。 円筒研削盤においては砥石の摩耗検出や、NC平面研削盤のワーク高さ計測にも使われます。 検査工程の負担を減らし、生産性向上に貢献します。