タッチプローブ(機内計測)のコストパフォーマンスを徹底解説
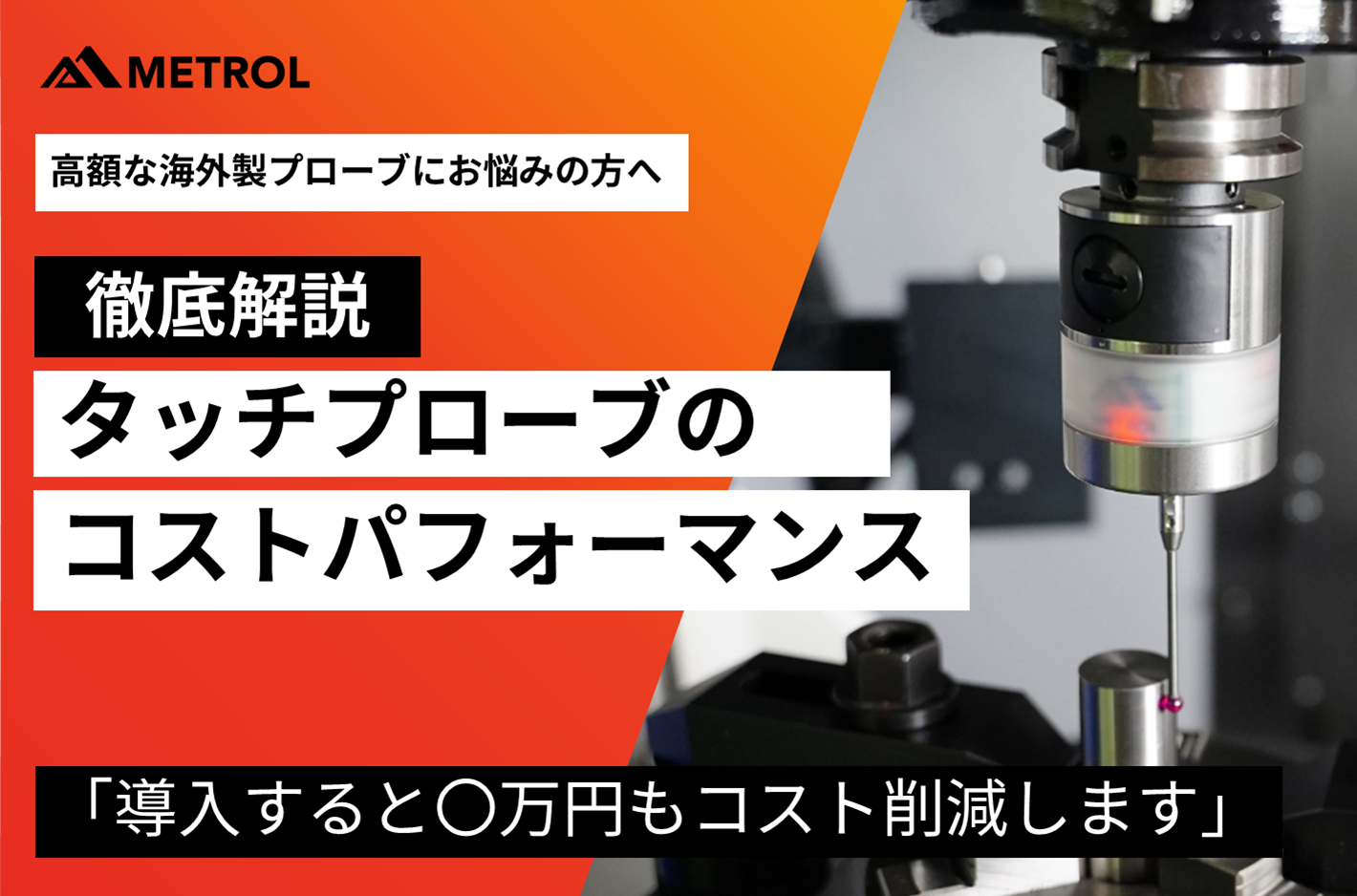
目次
結局、タッチプローブの導入コストは元が取れるのか?
近年、金属加工現場では、品質要求の高まりや人手不足、熟練者の引退により負担が増しています。
そこで、作業者の負荷を減らすためにタッチプローブを使った「機内計測」の重要性が増しています。
一方でタッチプローブは高価な海外製が主流のためコスト面でお悩みを持ちの方も多いのではないでしょうか?
工作機械ユーザの悩み
CNC工作機械のユーザにはタッチプローブをまだ使っていない方、すでに使っている方の2タイプに分かれますがそれぞれ
・高価なタッチプローブの費用対効果がよくわからない。
・すでにタッチプローブを使っているが、交換などランニングコストの負担が大きい
といった課題に悩む方も多いのではないでしょうか?
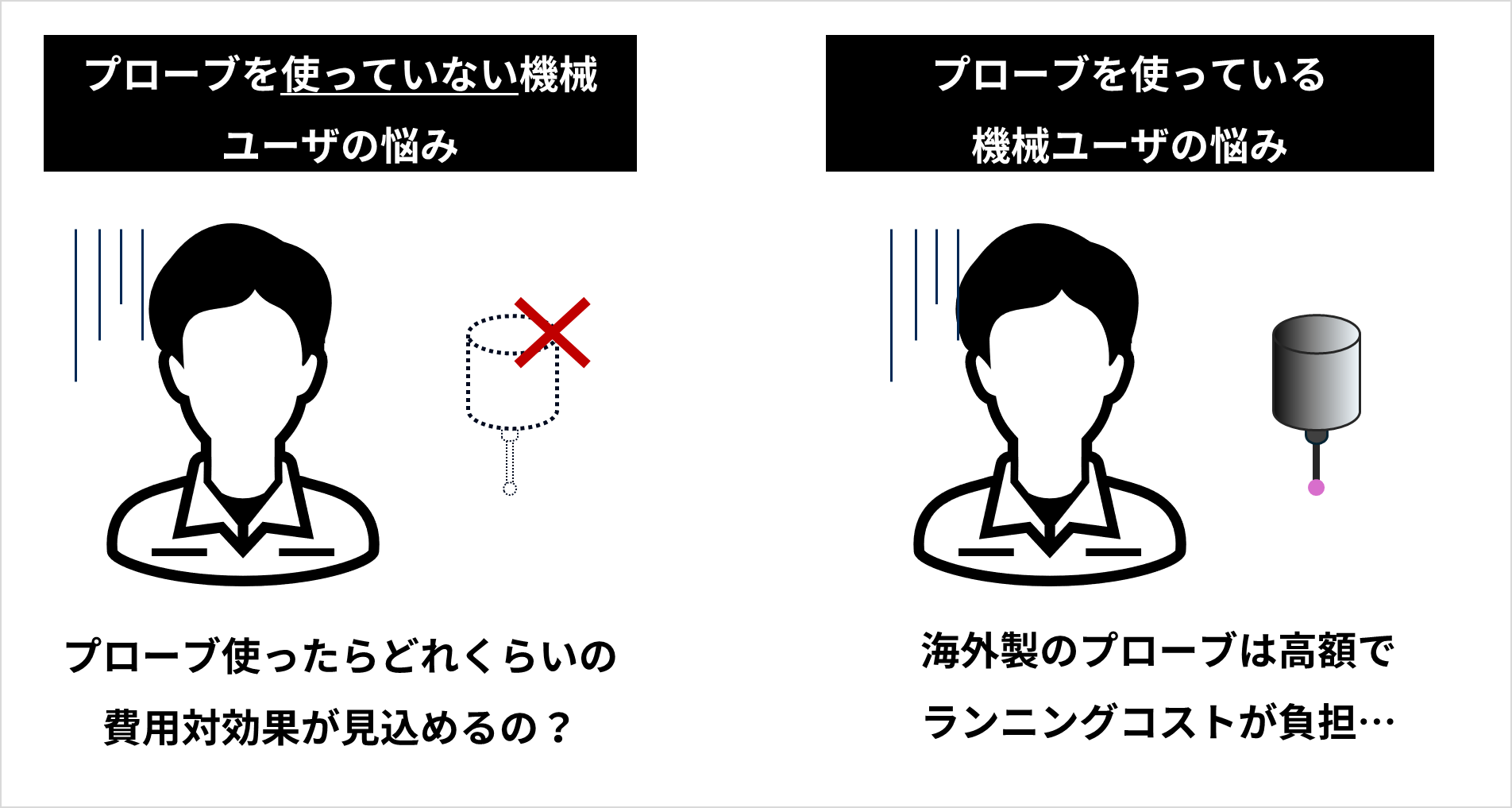
【結論】タッチプローブの費用対効果は5か月あれば回収可能。
本記事でお伝えする2つのコストメリット
・タッチプローブ導入によるコストメリット
・海外製から低コストな国産タッチプローブに置き換えで得られるコストメリット
結論、タッチプローブを1台導入することで工作機械1台あたり
・段取り作業の約80%以上削減
・段取り工程だけで、年間約125万円のコストダウン
・メトロールのタッチプローブを使うことで約260万円のコストダウン
を得られる試算結果があり、高い即効性とコスト削減効果を発揮します。
本記事では、この試算結果の背景は詳しく解説していきます。
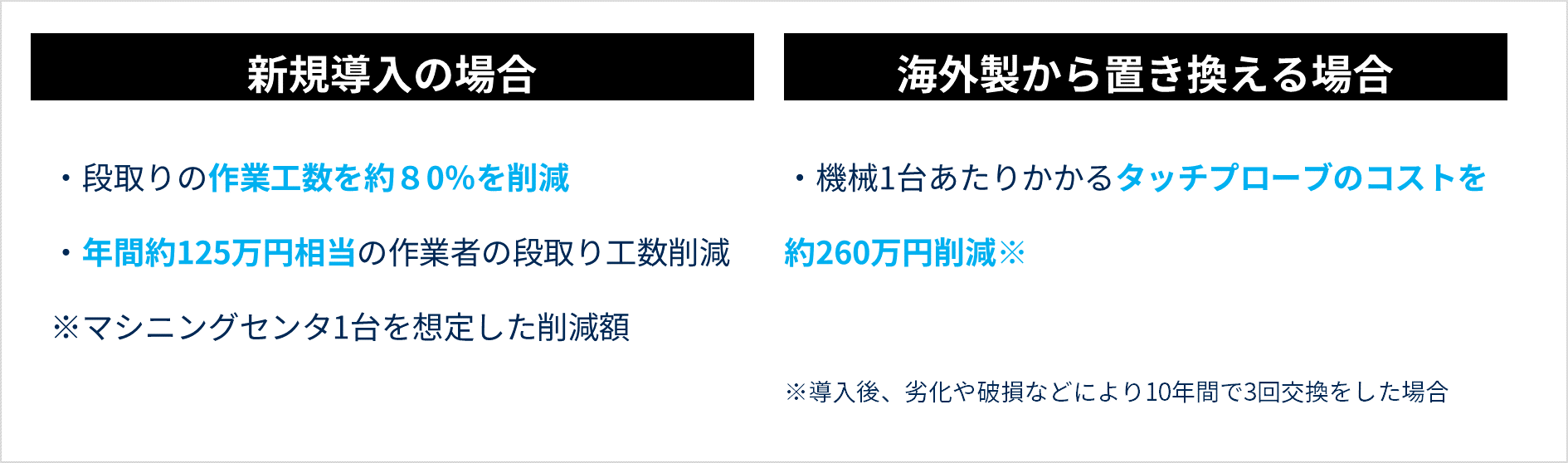
【前提】そもそも、なぜタッチプローブが必要なのか?
金属加工は「正確にモノを削り、寸法を保証してお客様に納品する」性質の仕事ですから、常に「基準通りのモノが正確につくれているのか?」の確認作業とそのための準備が必要となり、その工程で多大な人手とコストがかかっていることは加工従事者の方であれば、うなずけるのではないでしょうか?
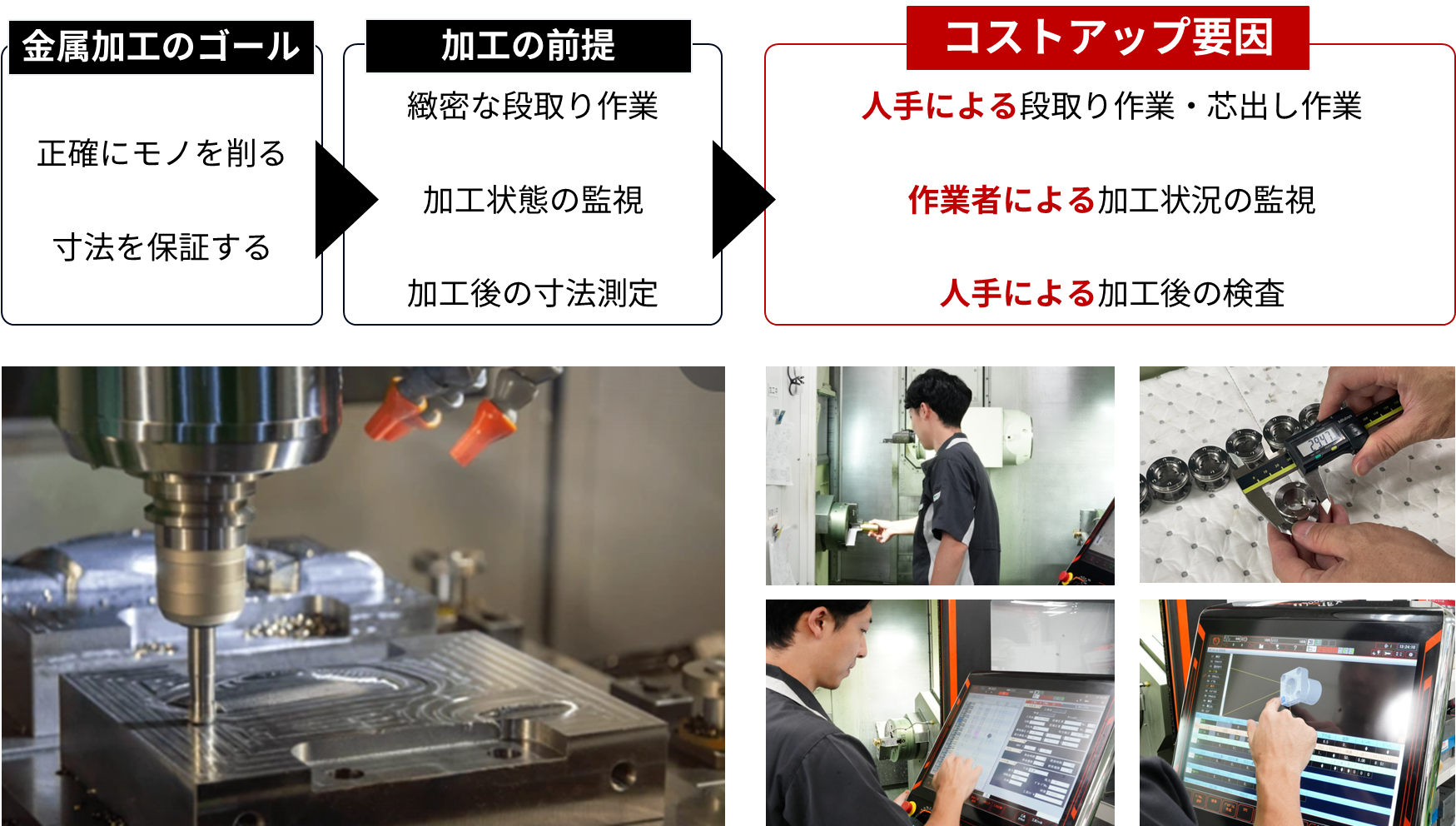
タッチプローブは人手を減らすために開発されたセンサ
タッチプローブはこうした確認作業にかかるコストを削減するために開発されたセンサです。
つまり「どれだけ確認作業のコストを減らすことができたか」でタッチプローブの費用対効果が決まります。
タッチプローブ導入によるコストメリットを試算してみた
タッチプローブは「いつ」お金を生むのか?
タッチプローブが活躍する場面は大きく以下の3つに分けられます。
- 段取り作業(寸法出し・試し削り)
- 量産加工
- 加工後の検査(部品の良否判定)
次に、3つのプロセスでどんな工程改善を生み出しているのかそれぞれ解説していきます。
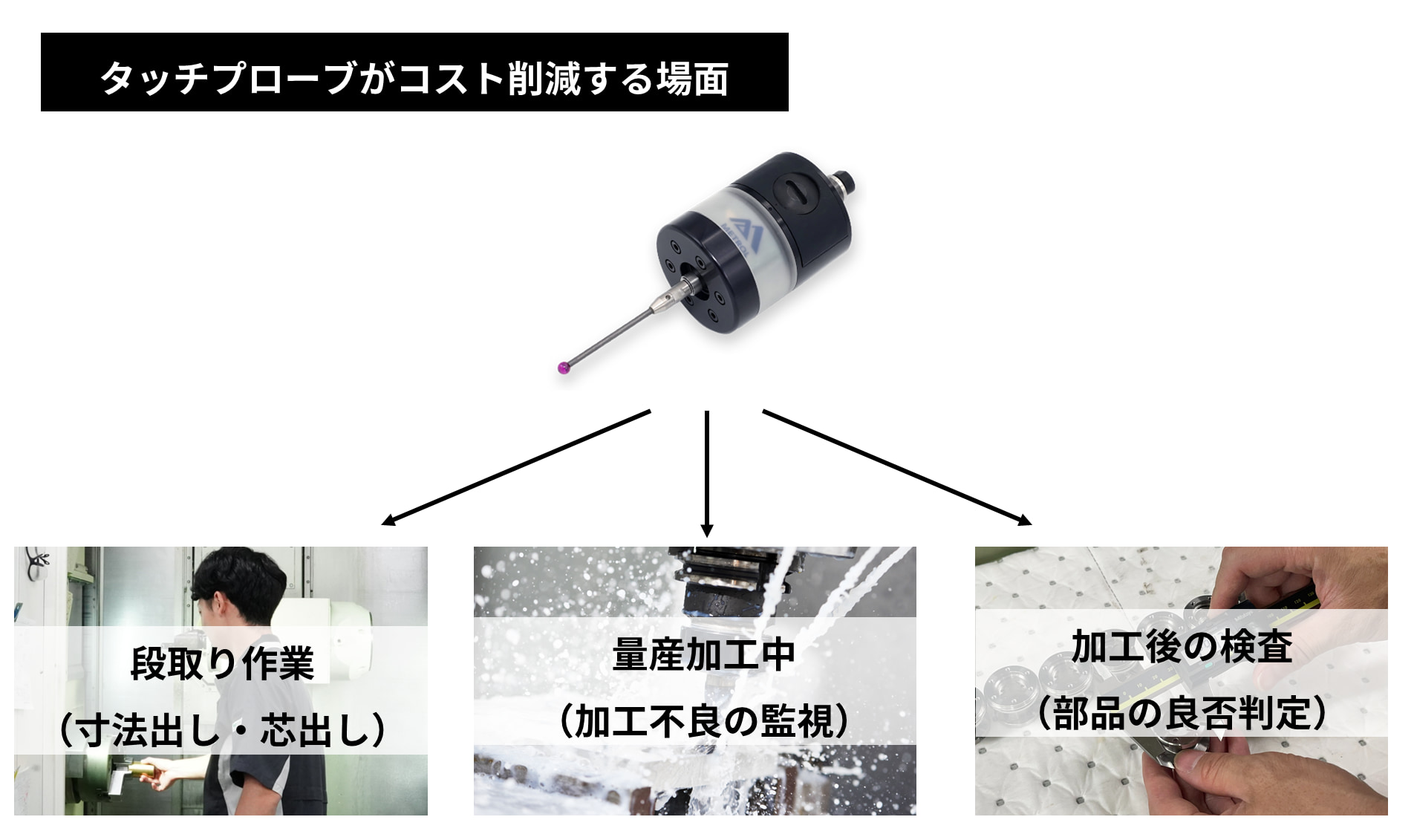
プローブを使えば「段取り作業」だけで〇〇万円工数削減できる。
段取り作業に要する時間は状況によって1~2時間、半日以上かかるケースも珍しくありません。
仮に2時間と想定した場合、タッチプローブ導入で、段取り時間を最大で工数80%以上カット、125万円/年のコスト削減可能な試算結果があります。(※125万円の試算結果は後述)
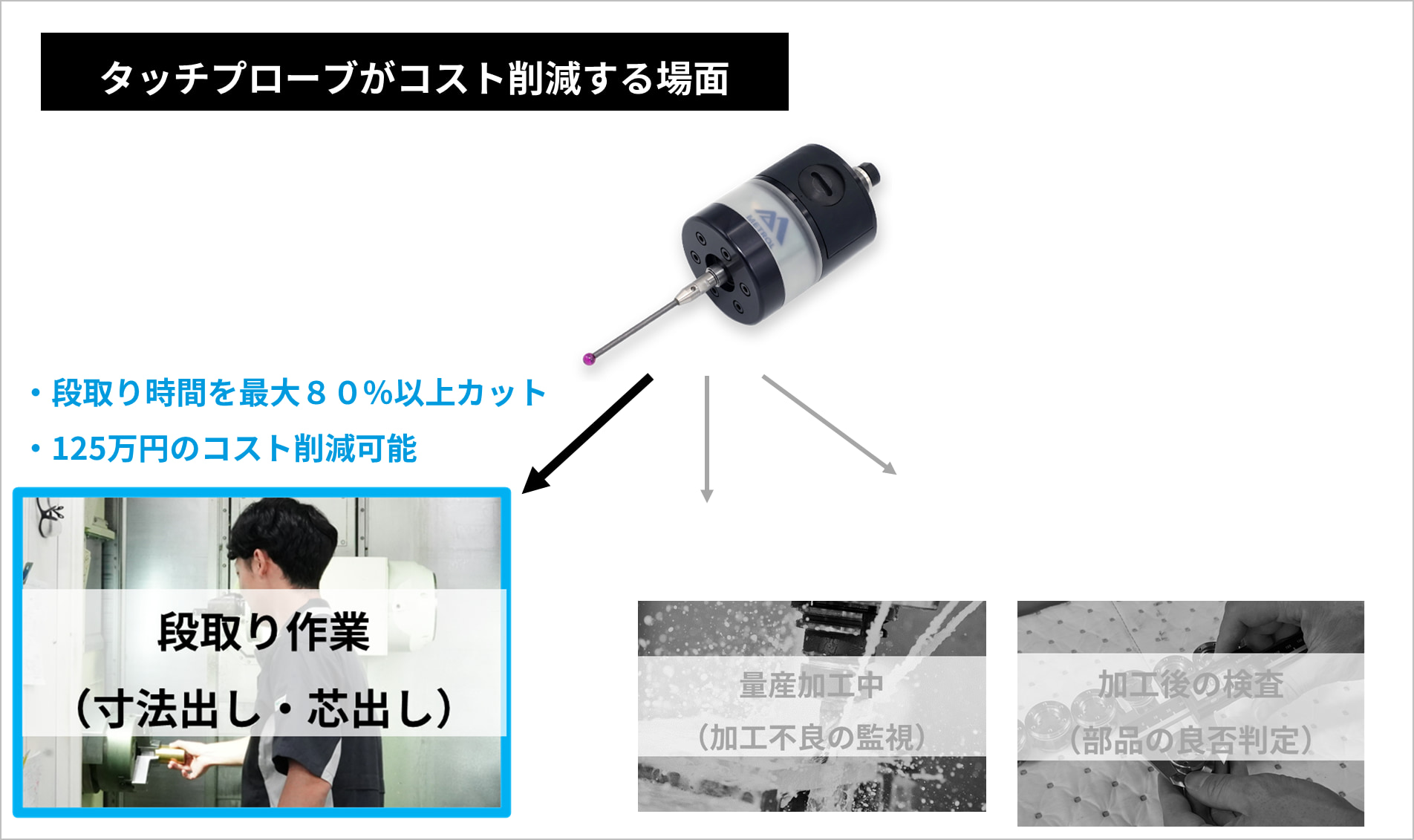
時間を奪う「手作業工程」
段取り作業のゴールは、量産加工を始める前に加工精度が出せているのか、の確認です。
「寸法出し・試し削り」の段階で、正確な加工ができなければ量産加工で不良が大量発生するため作業者は慎重に行います。段取り作業では削っては寸法を確認し、寸法が出なければ調整・追加工、を手作業で繰り返し行うため時間がかかります。
例えば、次のような段取り作業を考えてみましょう。
タッチプローブを使わない場合、以下の作業を全て「人手」で行います。(下記表の赤塗工程)
- 適切な測定器を探す手間
- 寸法計測・確認作業
- 補正値の入力作業
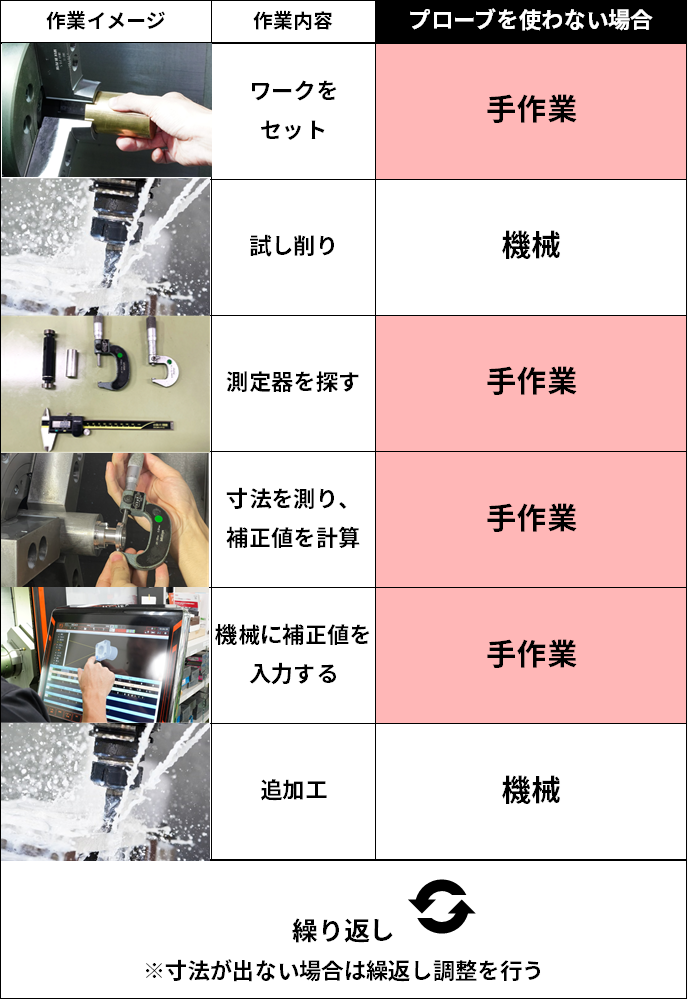
【段取り作業編】 タッチプローブを使うメリット
タッチプローブを使うことで、初回のワークセット以外の工程は「削減・自動化」が可能になります。(下記図の青塗の工程)
- 適切な測定器を探す手間→削減
- 寸法計測・確認作業→タッチプローブにより自動化
- 補正値の入力作業→自動的にフィードバック
のように、タッチプローブを使うことで作業者が機械に張り付いていなくとも段取り作業を完了させることができます。
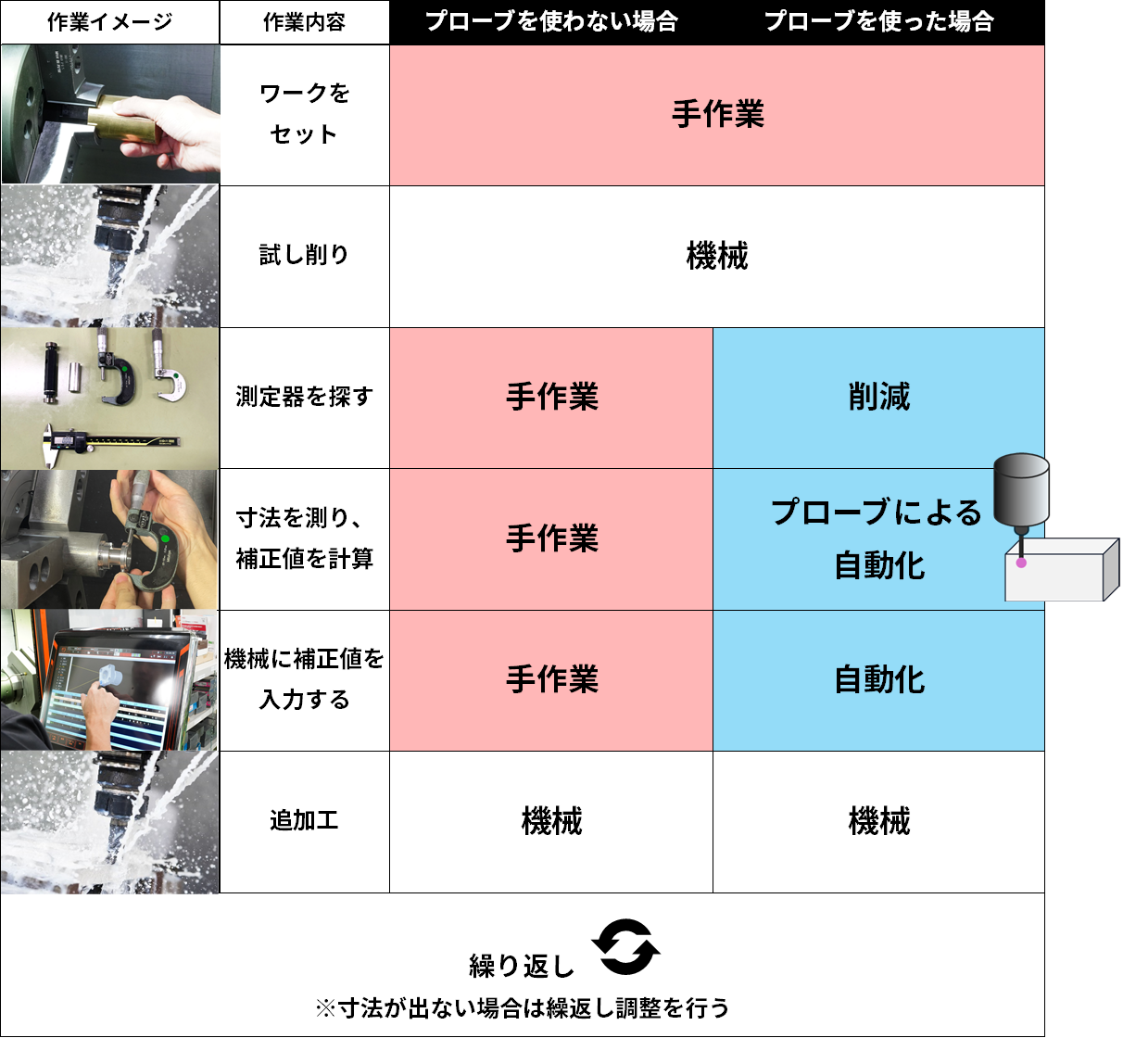
自動化されるだけでなく、機内計測によりワークの取り出しや着脱がゼロになり、作業の時間短縮にもつながります。
結果として
- 数時間かかっていた段取り作業が数分で完了する。
- 作業者の機械立ち合い不要で段取り作業が完了。
タッチプローブの投資回収期間は?【結論:約5か月】
結論からお伝えすると、導入前では機械1台当たり年間150万円かかる段取りコストを約25万円に削減可能です。
つまり125万円のコスト削減を創出します。
メトロールのタッチプローブの導入コストが仮に50万円とした場合、初期投資は次のように回収できます。
投資回収期間:約50万円 ÷ 約125万円/年 ≈ 約5か月
よって、5か月で投資回収ができる試算となります。
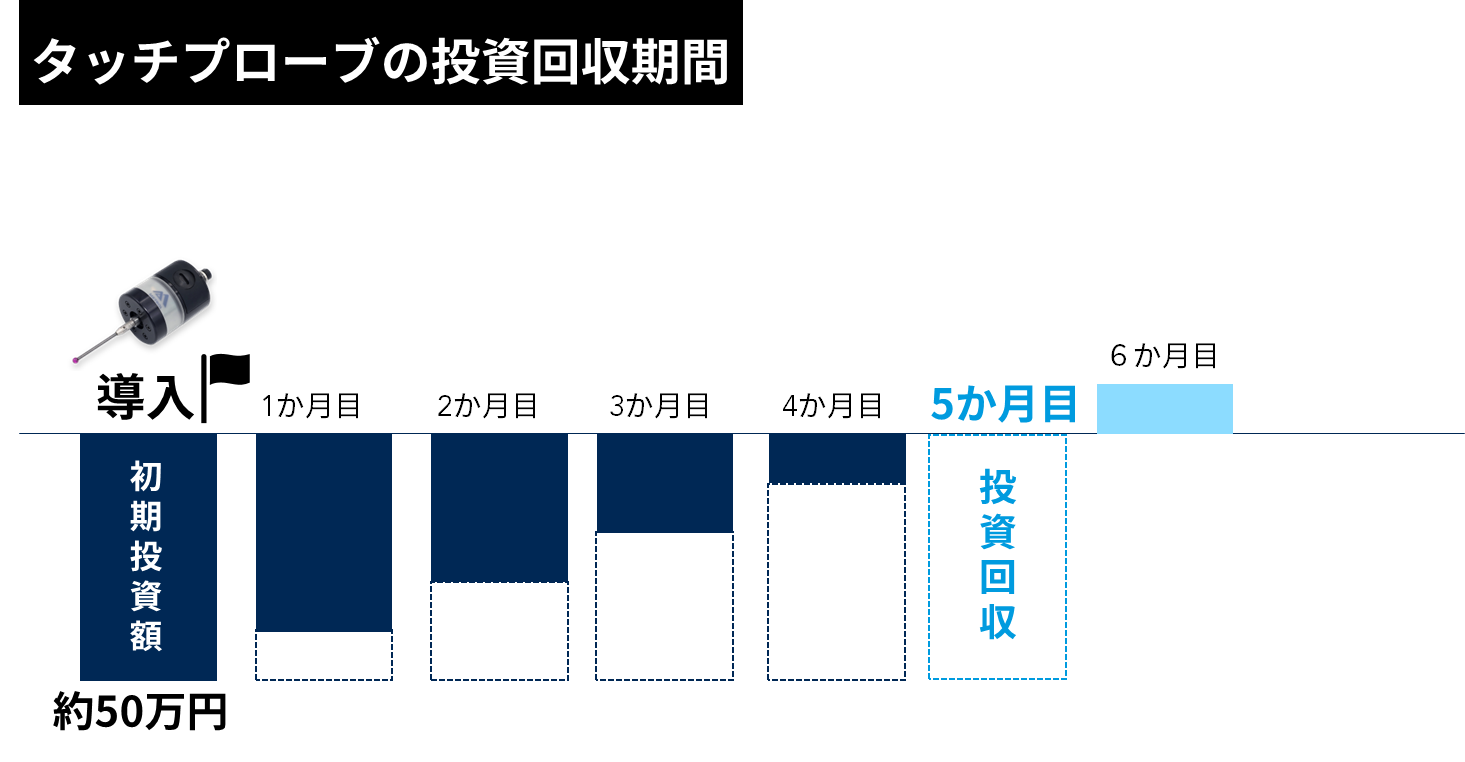
【導入前】コストのシミュレーション
段取りコスト150万円/年の内訳は以下の前提条件で計算されます。
- 段取り時間:2時間
- 作業者の時給:3,000円
- 1日の稼働時間:8時間
- 年間稼働日数:250日
段取り作業のコスト計算: 1回の段取り作業にかかるコスト=2時間 × 3,000円 = 6,000円
仮に、1日に1回の段取り作業が必要だとすると、1日の段取りコストは6,000円/日。
これを年間で計算すると以下のように試算されます。
年間の段取りコスト=6,000円 × 250日 = 150万円/年
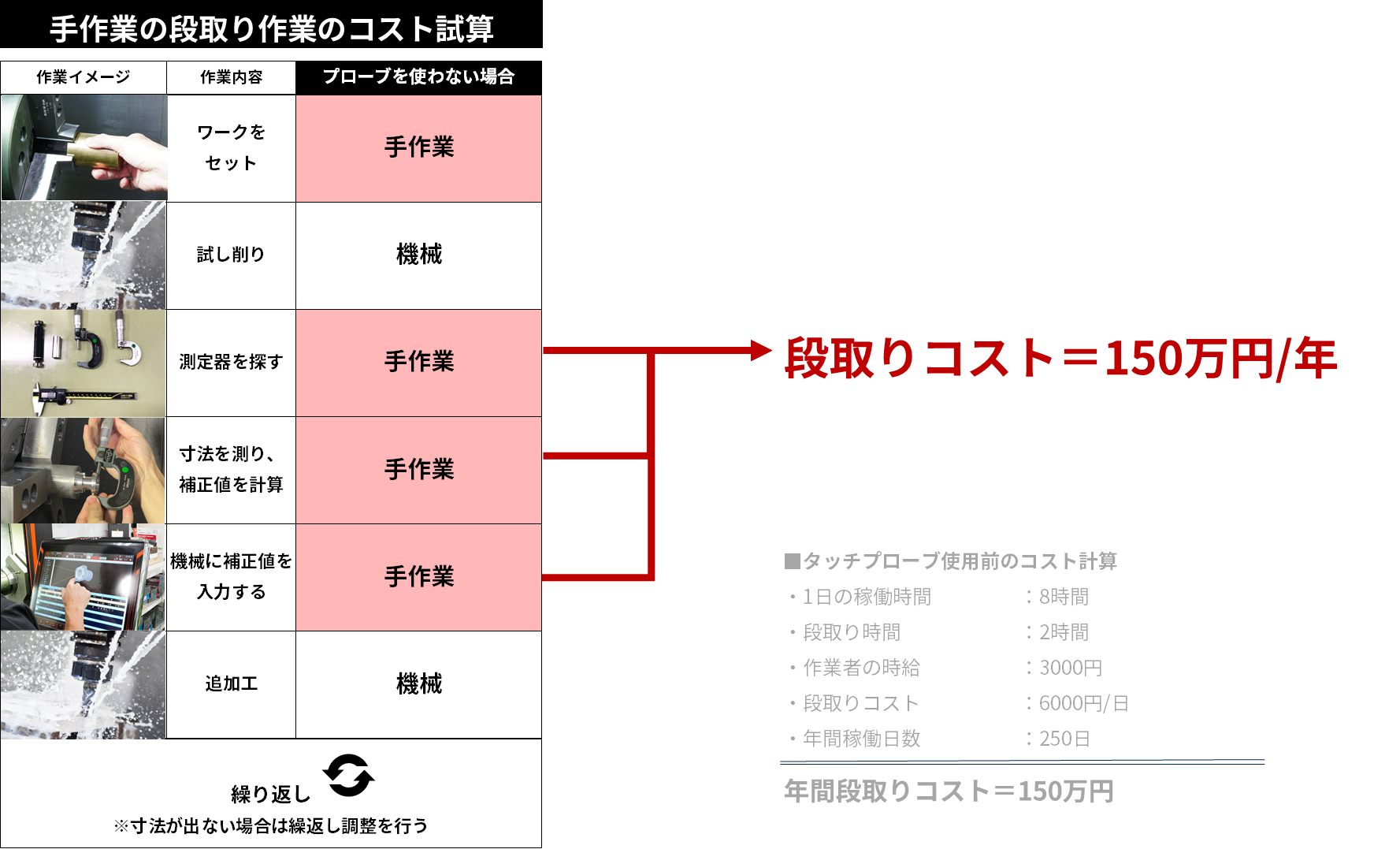
【導入後】コストのシミュレーション
タッチプローブ導入後の 段取りコスト 125万削減の試算を以下の条件で行います。
タッチプローブ導入後の段取り時間が2時間から20分(0.333時間)に短縮されると仮定します。
- 段取り時間:0.333時間
- 作業者の時給:3,000円
先ほどと同じ条件で計算を行うと
1回の段取り作業にかかるコスト=0.333時間 × 3,000円 = 999円
年間の段取りコスト=999円 × 250日 = 249,750円(≒約25万円)
つまり年間のコスト削減効果は、150万円 − 25万円 =125万円となります。
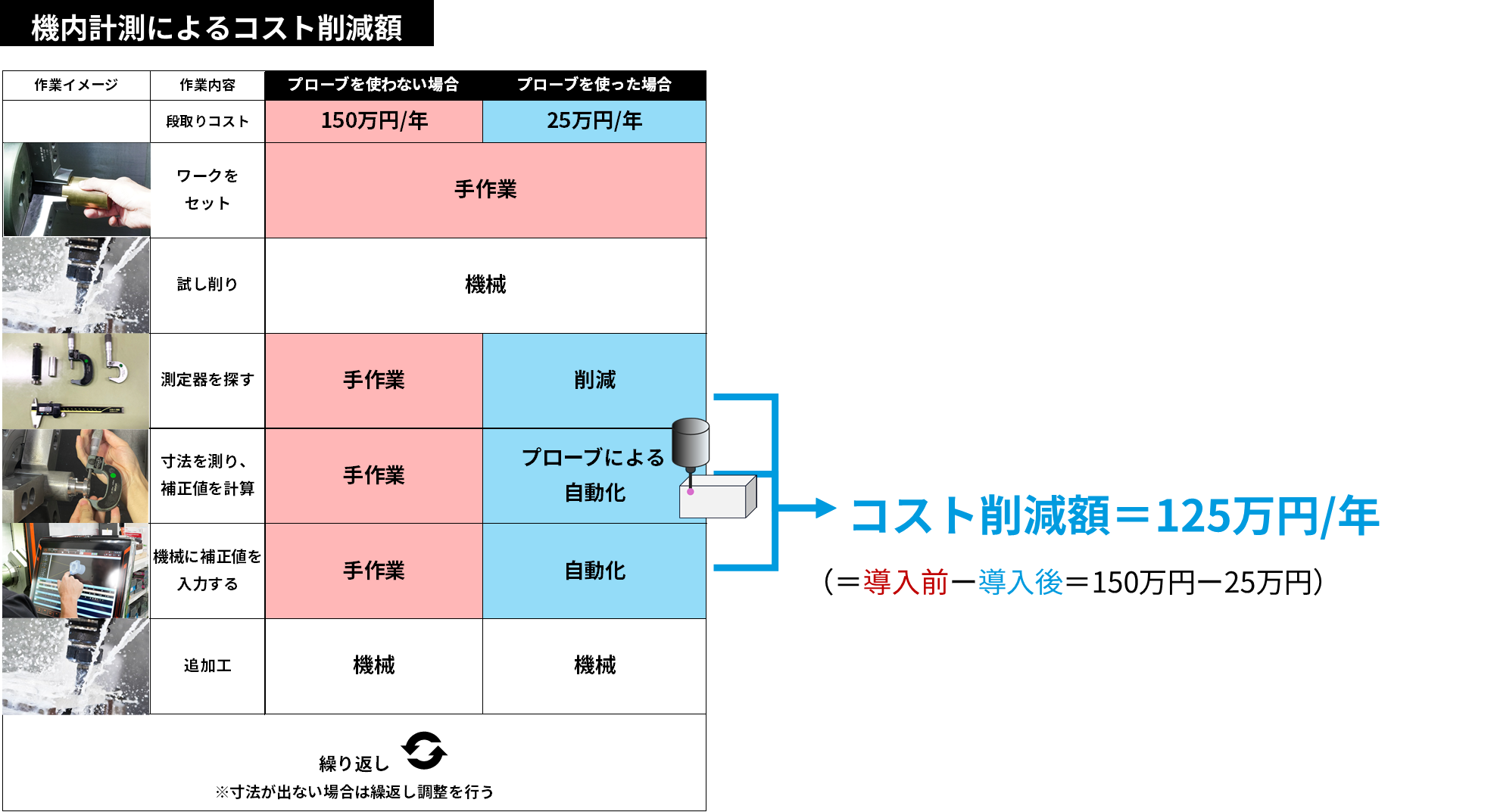
【工場管理者 必読】プローブの見えにくいコストメリット4選
1.全数検査にかかる負荷を軽減できる
タッチプローブを使わない場合、
- 全数検査のコストが大きい
- 検査員によって検査方法がバラつく
といった課題が挙げられます。
機内計測を導入し「そもそも良品しか作らない」加工条件を整えることは、後工程の検査コスト軽減に大きく寄与します。
検査工程は無くせない場合でも
- 全数検査から抜き取り検査へ切り替え
- ロット管理で、良品ロットと不良品ロットを分ける
だけでも心理的負担を軽減し検査コストは大幅に削減できる可能性があります。
また人による検査方法のバラつきはプローブを使うことで、標準化し管理しやすくなります。
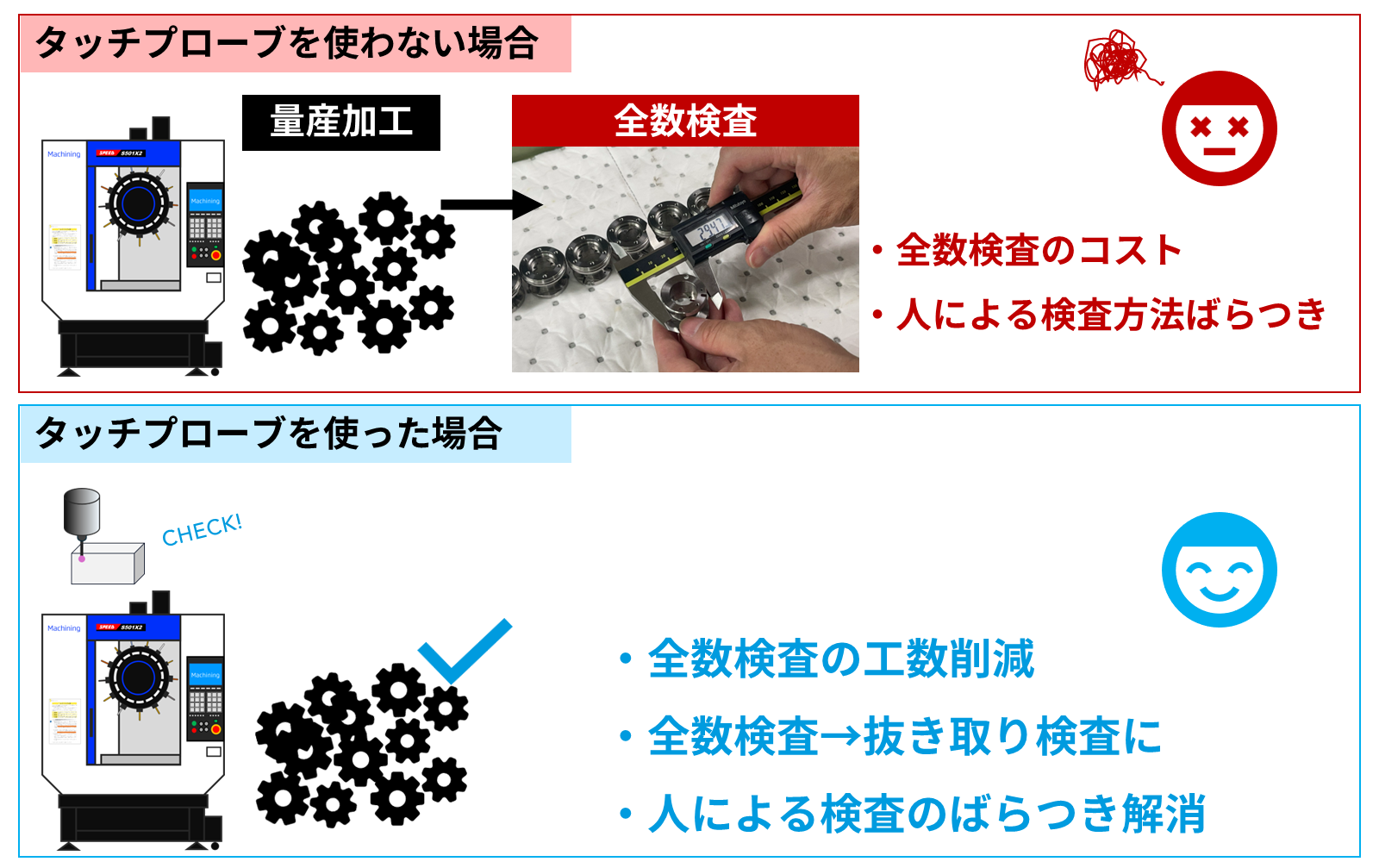
2.多能工化しやすくなる
手作業工程が多い場合、作業者が機械に張り付いて作業を行わなければなりません。
タッチプローブで作業者の手空き時間を作ることができれば、作業者1名に対して多台持ち・多能工化の実施が可能になり人件費のアップを防ぐことが可能です。
3.人の負担軽減・働き方改善
多台持ちが主流となってきている中で、手作業による業務負荷は集中力の低下は業務効率を悪化させ、判断ミスや慢性的な残業過多など悪習慣に繋がるリスクがあります。
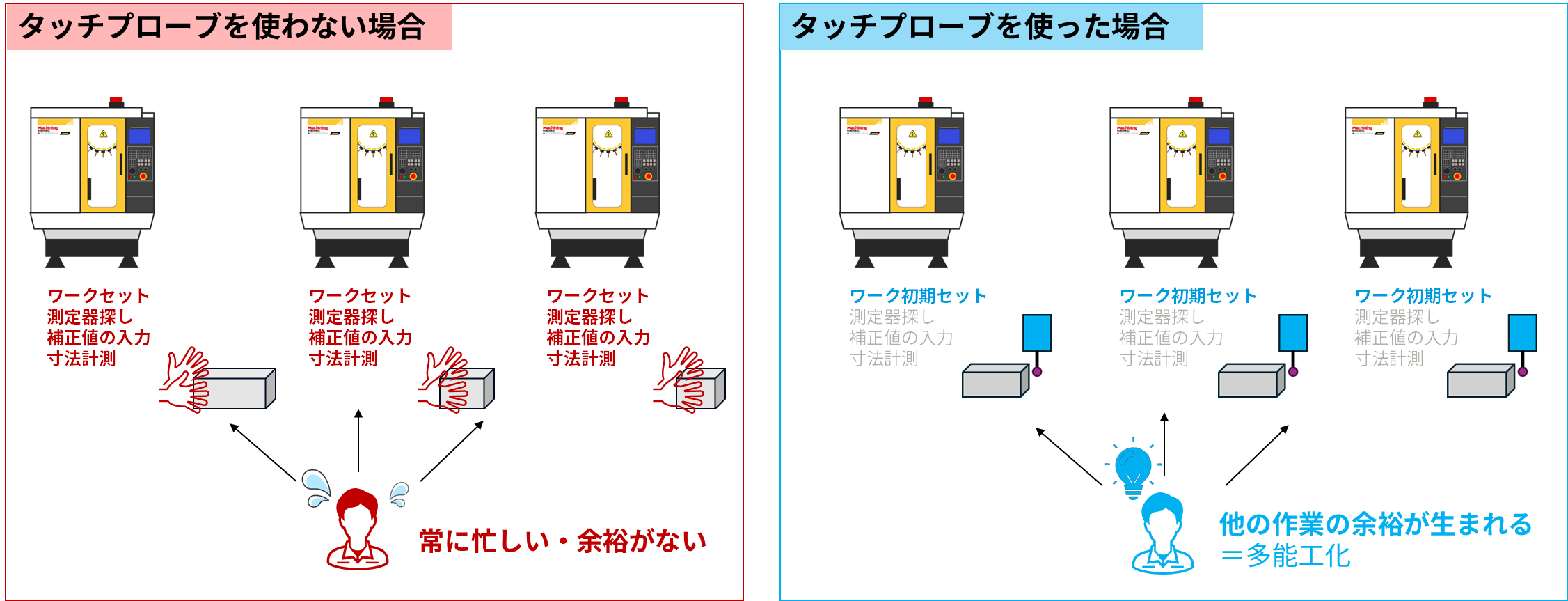
とくに製造業は若手人材の人口減少が顕著です。(グラフ1参照)
グラフから、国内における製造業の若手人材は減り続けています。
自動化を推進して、より働きやすく技能を磨ける環境づくりは若手人材の獲得・育成においても重要なテーマと言えます。
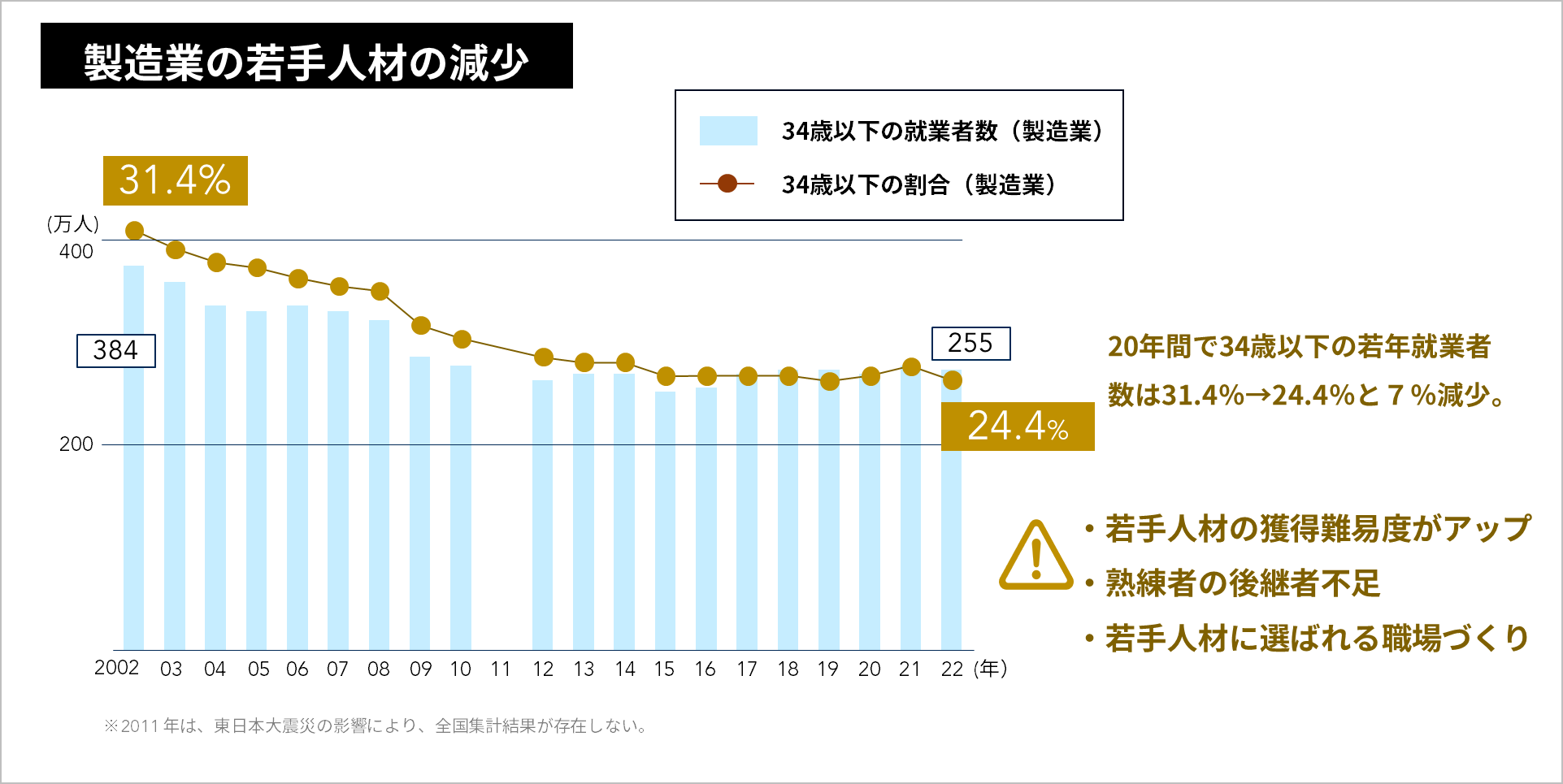
4.加工不良の監視・無人加工の実現
夜間の時間帯も機械を無人で稼働させたい場合、加工中の熱変異や刃具折損などを検出できなければ加工不良や事故の原因となります。
タッチプローブを使うことで無人加工中の寸法の異常値などを検出し、不良を作り続けてしまうリスクを回避でき、担当者も安心して無人加工を実施することができます。
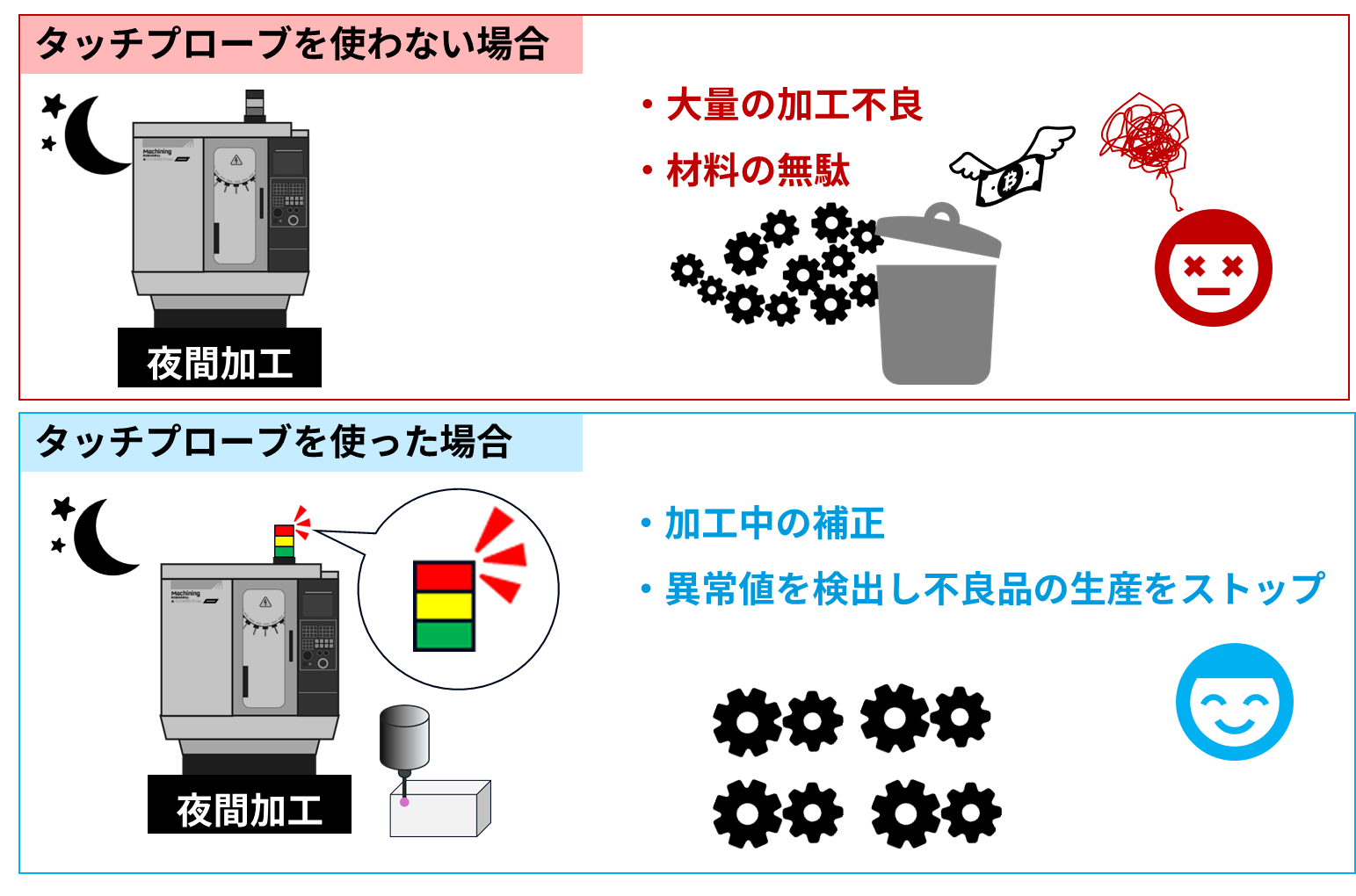
メトロールのタッチプローブRC-K3Xを選ぶ理由
ここからは、メトロールのタッチプローブRC-K3Xシリーズの導入メリットを解説していきます。
見えてますか?タッチプローブ2つのコスト
メトロールのタッチプローブは徹底した国内生産・内製化により海外製と比べ、約70%以上のコスト削減を実現します。
前提として、タッチプローブの運用には2つのコストを考えておく必要があります。
- 導入時の初期費用
- 導入後のランニングコスト
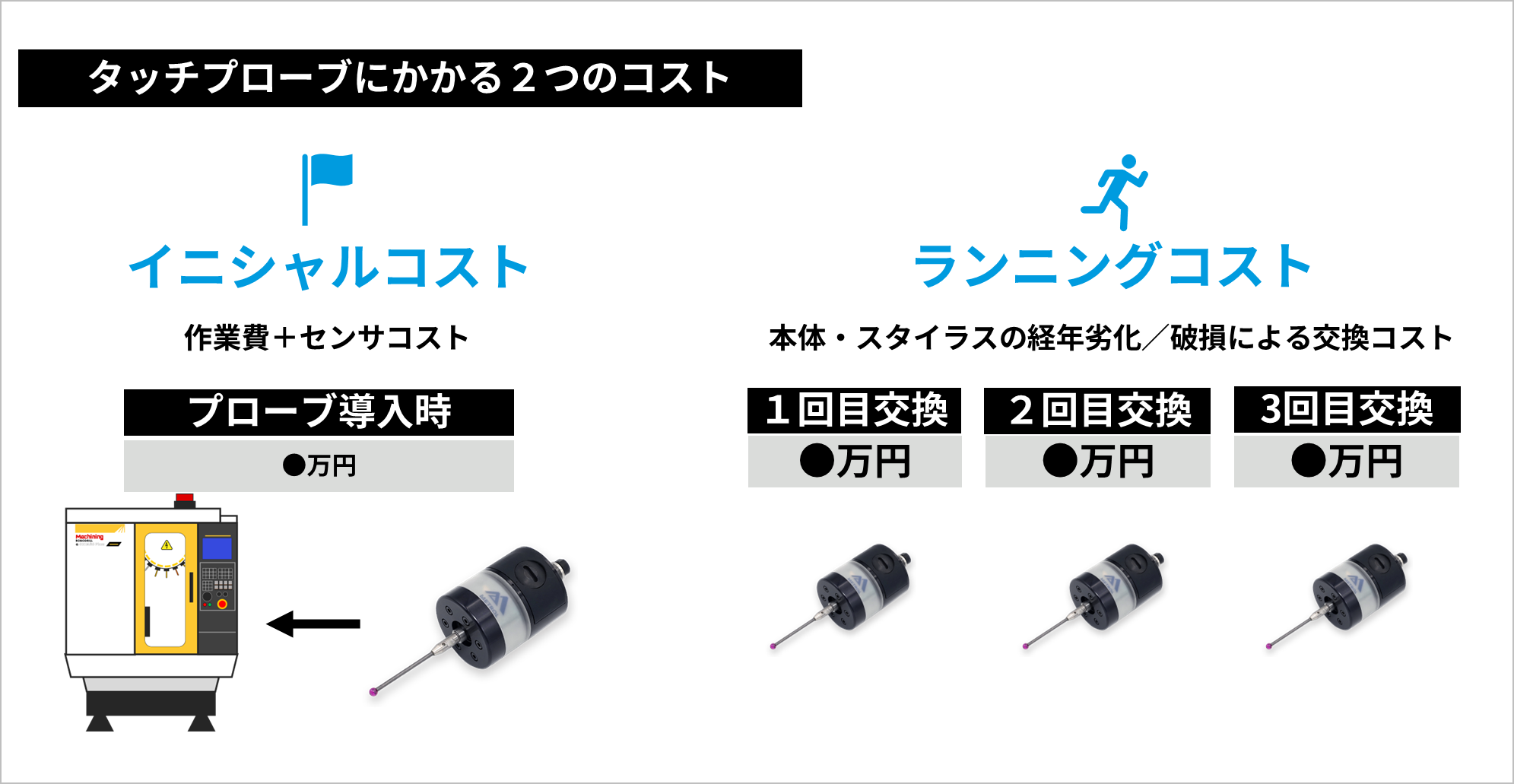
導入にかかる初期費用
海外製のタッチプローブ初期導入費用の相場は、おおよそ100万~150万円前後といわれています。(※当社調べ)
一方でメトロールは、SIerと提携することで約60%以下の低価格で導入可能です。
導入方法としては以下の3つがあります。
- 機械を新規購入する際にオプションで搭載する
- 導入後の設備に「後付け」で搭載する
- タッチプローブ単体で購入し自社で取り付ける(最も低コスト)
自社で対応する場合を除き「初期費用+センサ費用」が発生します。
初期費用には取付のための工事費、操作指導、計測プログラム作成などのコストが含まれます。
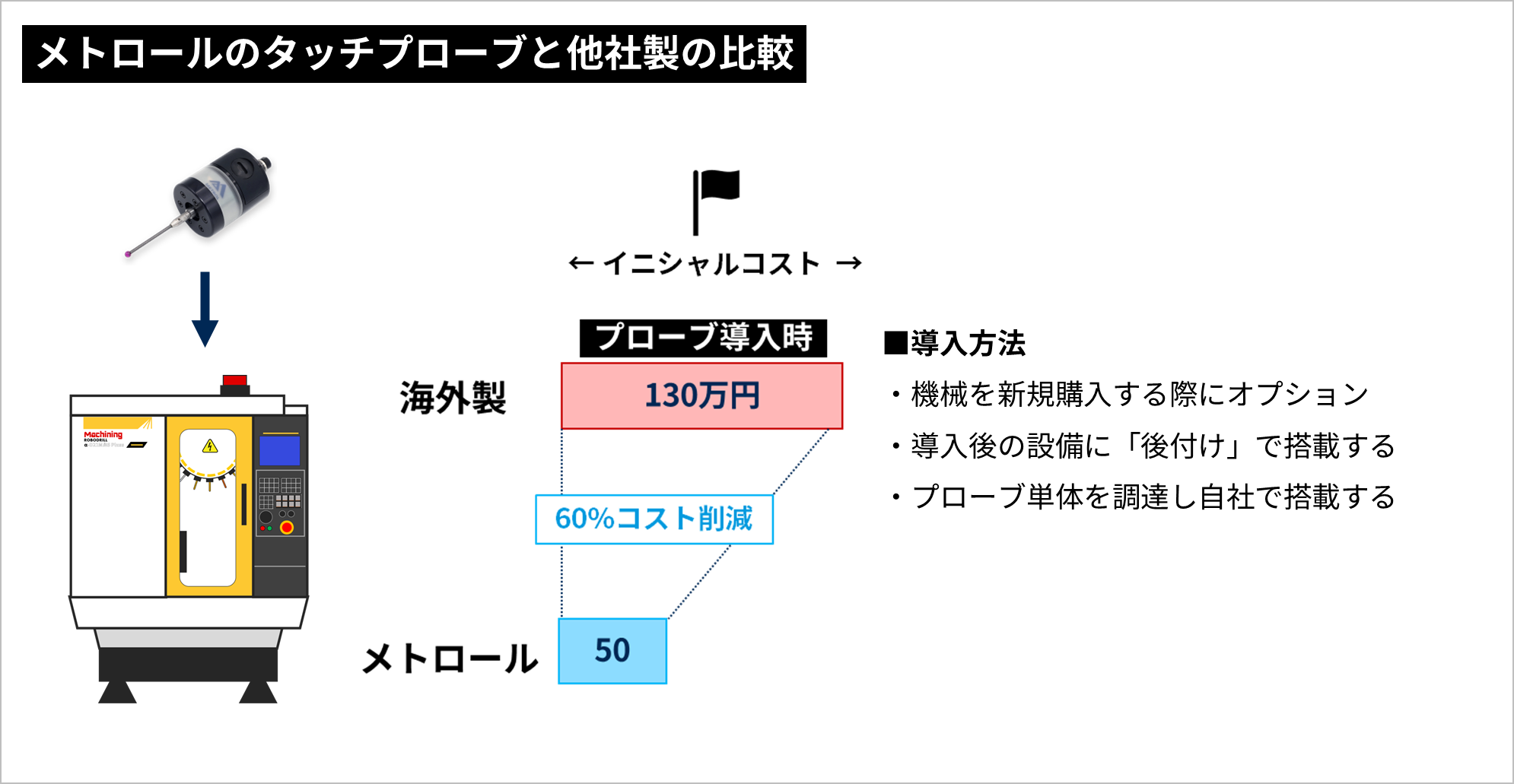
ファナック、ブラザーのマシニングセンタをご利用のお客様に向けて、メトロールでは安価にタッチプローブを後付けするサービスを行っております。
【重要】導入後のランニングコスト
タッチプローブのコストは導入して終わりではありません。
海外製プローブの本体交換コストは数年に一度、80万~100万円程度かかることが一般的です。
一方メトロールのタッチプローブは国産でコア部品の内製化により海外製と同等スペックで約60%以下の価格を実現しました。
交換の場合は初期費用はなくセンサ本体コストのみが発生しますが、センサ交換の主な理由は、
- 経年劣化による精度不良・不具合
- 使用中の誤操作によるセンサの破損
が発生するためです。プローブに付属する測定子(スタイラス)も先端球が劣化し、交換が必要になります。
交換頻度は、誤操作による破損など半年~1年で交換が必要になるケースもあります。
高額なプローブを使っているとこうしたランニングコストに悩むユーザも少なくありません。
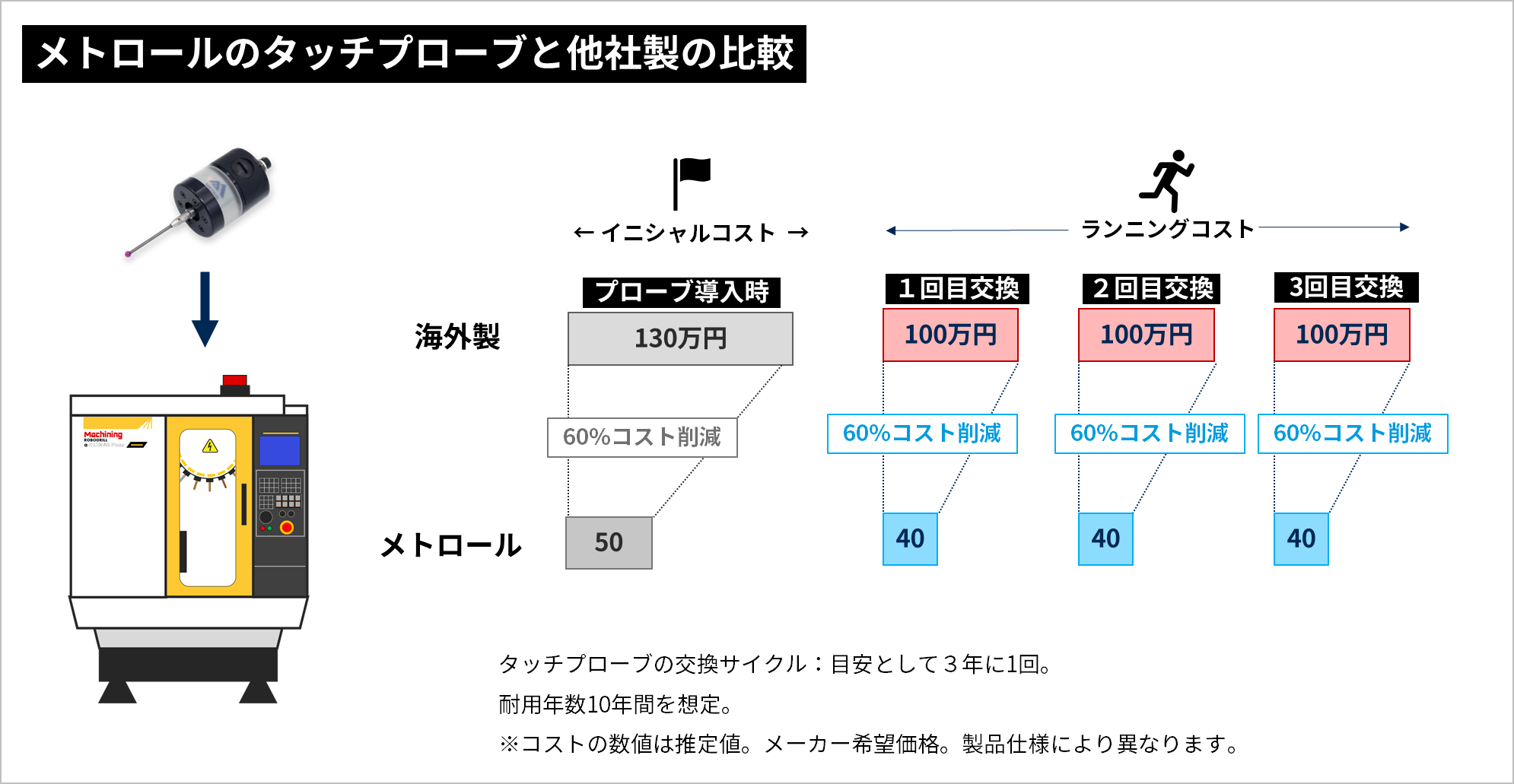
【シミュレーション】トータルのランニングコストを比較
・海外製タッチプローブ
・メトロールのタッチプローブ
を採用した場合ののトータルコストを以下の前提条件で比較してみましょう。
- 工作機械1台
- 3年に1回交換
- 期間:10年(機械の耐用年数)
- センサのコスト:海外製100万(初期:130万)、国産メトロール製40万(初期:50万)とした場合※
※数値は概算値になります。
以上の条件で試算すると、工作機械1台の耐用年数の中で約430万円のコストがかかります。
一方、メトロールのRC-K3Xシリーズを使用することでこのコストを60%削減し、260万円のコストダウンが実現されます。
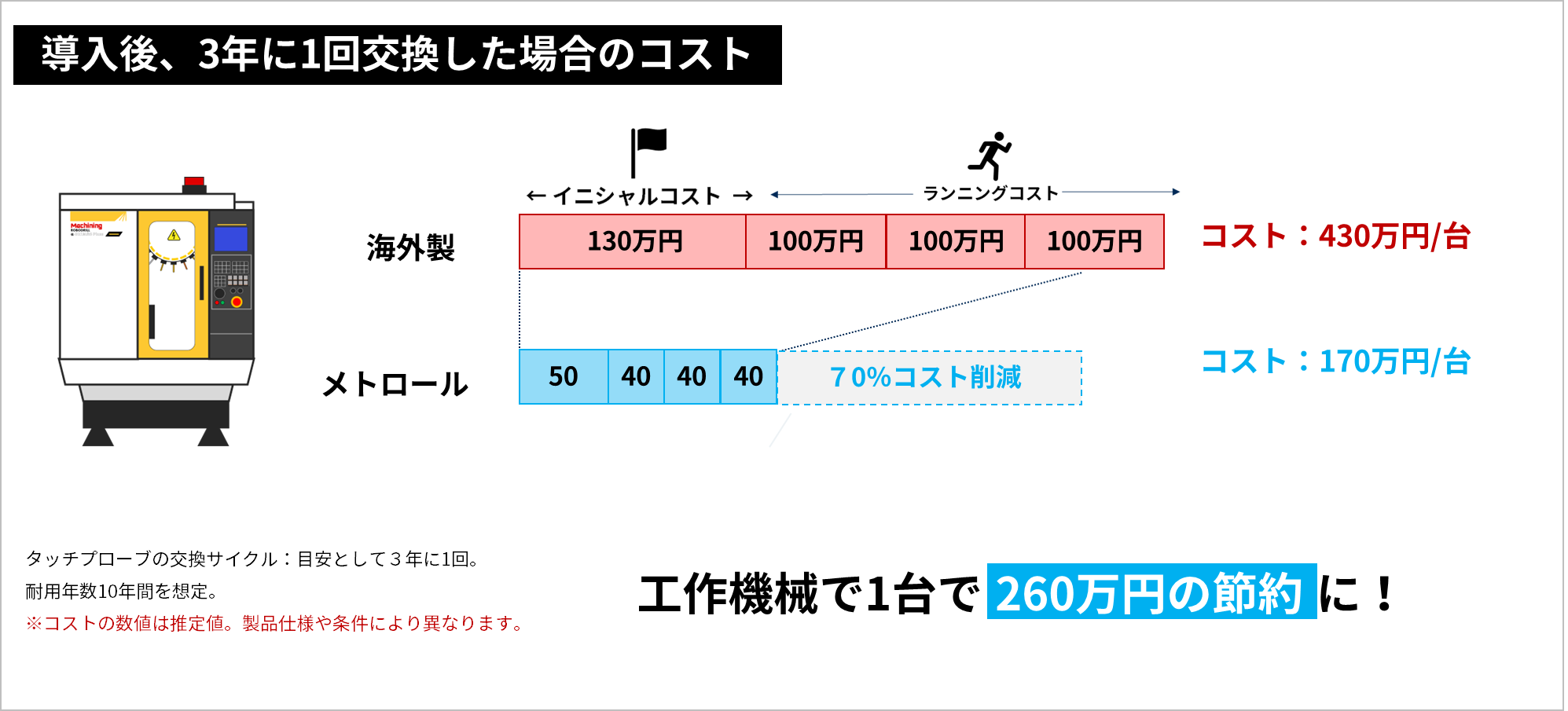
仮に5台のマシニングセンタを使用していたとすると、1300万円のコスト削減につながります。
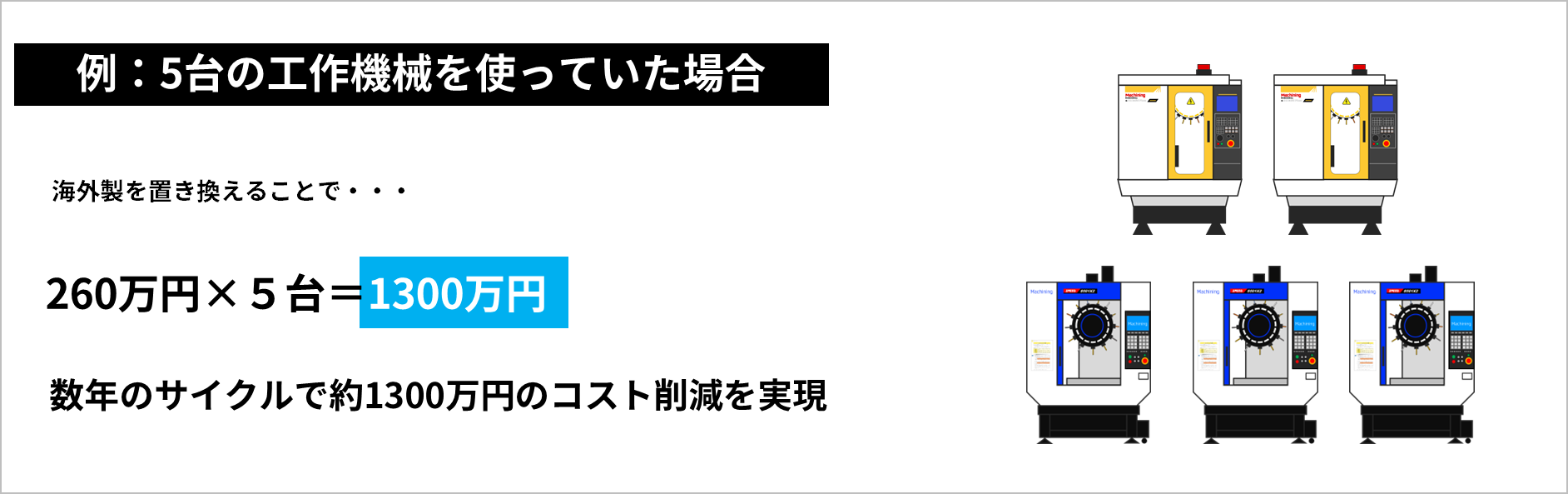
工作機械にかかるコストは、タッチプローブだけでなく工具や機械の保守メンテなど多岐にわたるため、タッチプローブにかかる費用は可能な限り抑えることは重要ではないでしょうか。
まとめ
これまで解説したタッチプローブのコストメリットを以下にまとめます。
タッチプローブを導入するメリット
- 段取り作業にかかるコストを約80%以上削減可能
- 量産加工や検査工程にかかるコストも大幅に削減できる。
- 作業者の負荷を軽減し、働きやすい環境を実現
メトロールのタッチプローブを使用するメリット
- 海外製と比べ初期費用+ランニングコストを大幅に抑えることができる
- 機械の台数が多いほどコスト削減の効果が大きい
おわりに
いかがでしたでしょうか?
本記事では、タッチプローブの導入メリットを「コスト」という切り口で、限定的な前提条件ではありますが費用対効果を試算しました。
もちろん、考慮すべき条件が変わると現場によって試算結果は異なります。
工場管理者の皆様も自社の状況を振り返って一度試算してみてはいかがでしょうか。
ファナック、ブラザーのマシニングセンタをご利用のお客様に向けて、メトロールでは安価にタッチプローブを後付けするサービスを行っております。