【設備検討中の方必見】当社がCNC自動旋盤Cincomを導入した理由。
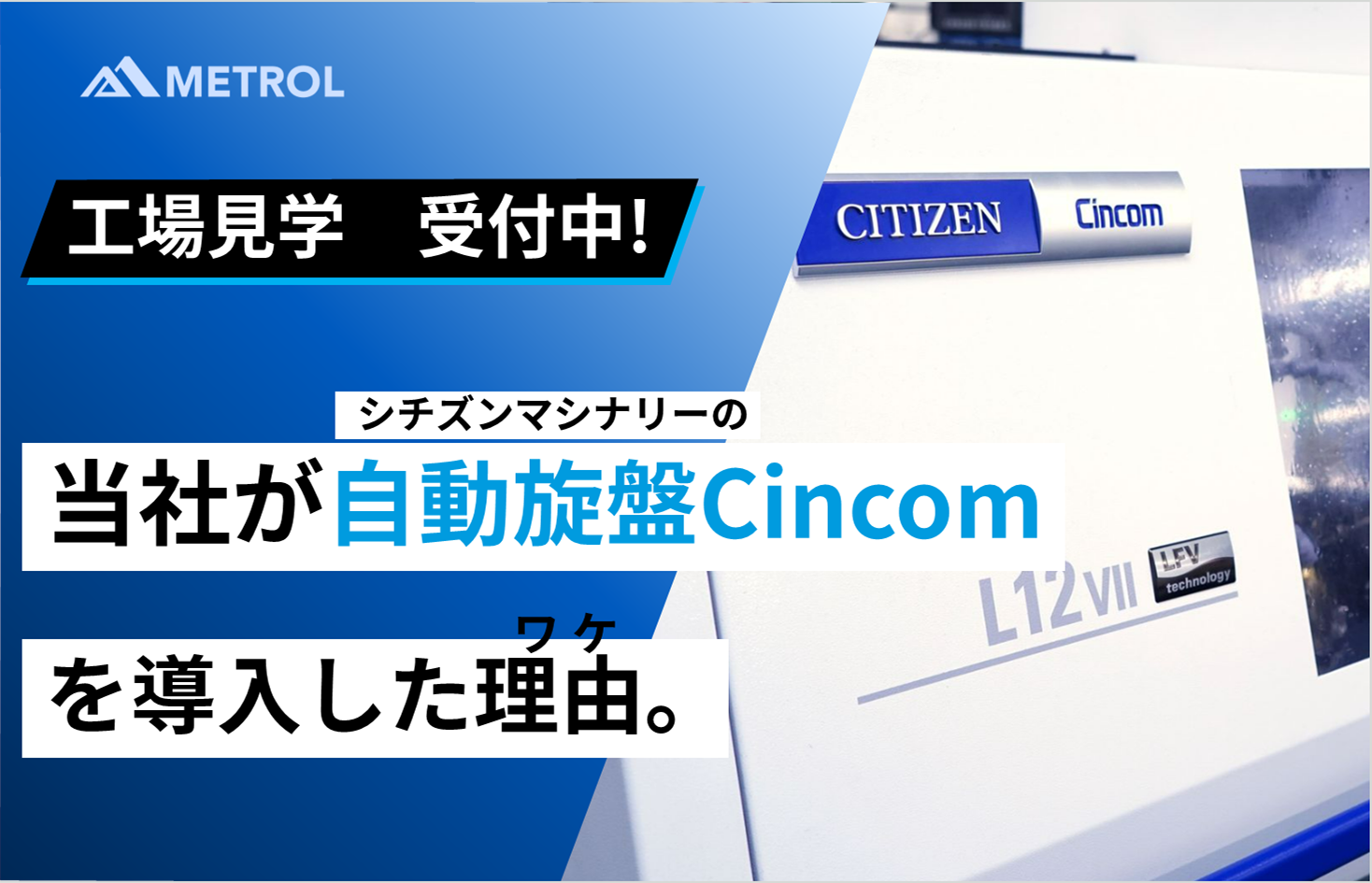
工作機械の導入に携わる、経営者・工場長・エンジニアの皆様、こんにちは。
昨今の人手不足や熟練者の世代交代、採用難が進む中で
・加工部門のNC化を進めたい
・機械トラブルやチョコ停を無くして稼働率を上げたい
・工程集約して、検査などの前後工程を効率化したい
と考えている方は多いのではないでしょうか? 当社もイチメーカーとして日々こうした課題に取り組んでいます。
本記事では、メトロールでも導入をしているシチズンマシナリーのCNC自動旋盤Cincomシリーズについて解説していきます
- CNC自動旋盤を既に使っている方
- これから新たにCNC旋盤の導入を検討している方
に向けて最新の活用方法を解説していきます!
この記事でわかること
- メトロールのCNC自動旋盤の導入背景
- CNC自動旋盤を導入時に欠かせない切粉と不良品対策
- 生産性を上げるCNC自動旋盤Cincomの独自オプションとメリット
- メトロールの工場見学のご案内
目次
【Cincom導入前】メトロールのNC化の経緯とは?
メトロールでは、4年前までは工場の9割以上が汎用機械でした。
そんな状況からNC化へ大きく舵を切り、新規のNC工作機械(マシニングセンタ、CNC自動旋盤、NC平面研削盤)を毎年導入し、現在ではNC機が汎用機の台数を上回っています。
当社がNC化へ大きく舵を切った背景には
- 自社でQCDをコントロールしたい
- 中~大量生産体制をつくりたい
- 将来に向けた人手不足対策とNCオペレーターの育成
- 若手社員のモチベ―ションアップ(汎用機だけのキャリア形成が困難)
が目的としてあります。同様の目的でNC化に注力している会社も多いのではないでしょうか。
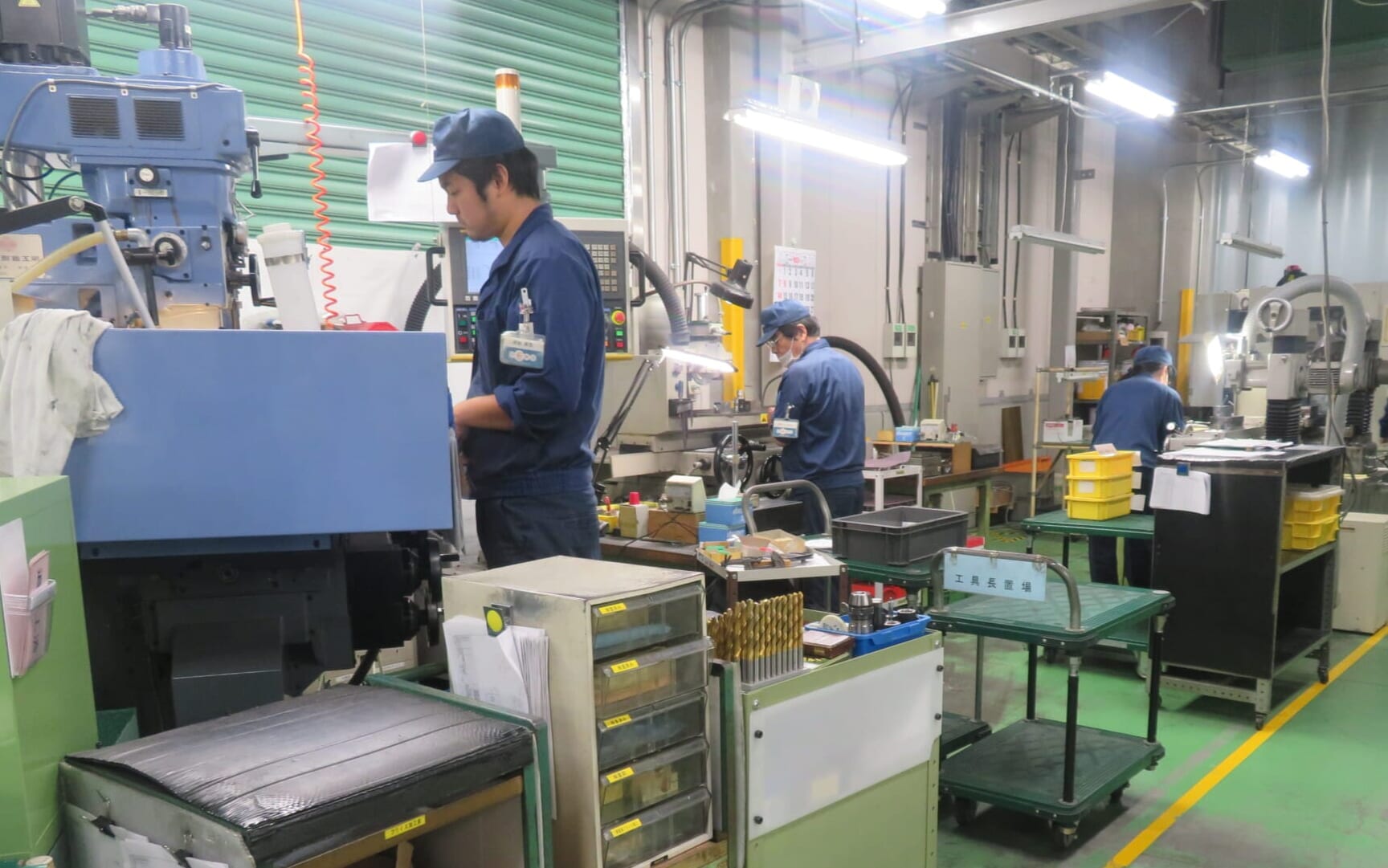
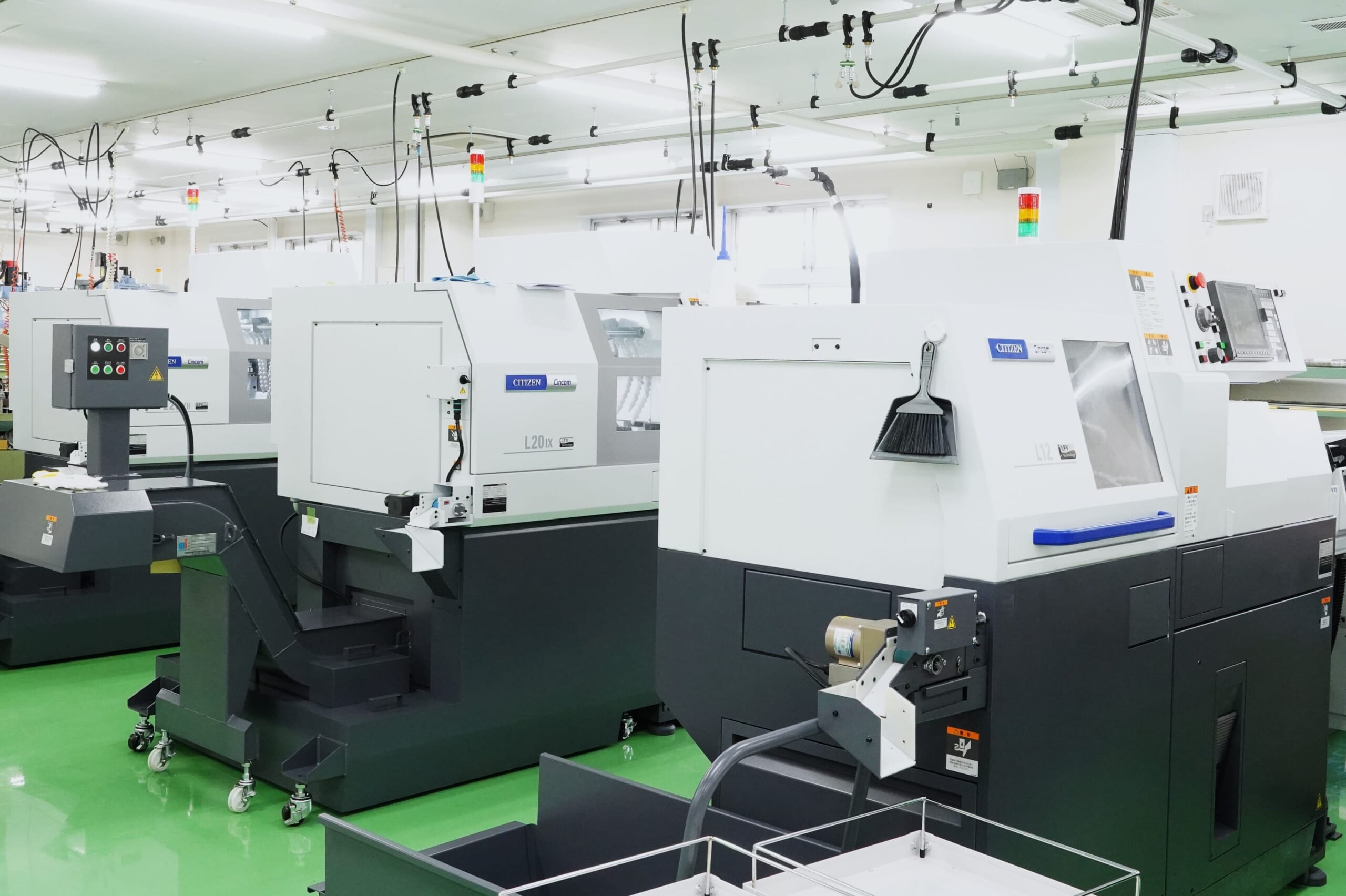
【Cincom導入準備】 NC化はいつ始めるべきか?
一方で、NC化への体制移行はNC工作機械は購入すれば完了、というわけにはいきません。
メトロールでも、NC化へ急速に移行する中で、以下のような課題に現在も取り組み続けています。
- NC機の運用体制の標準化・効率化
- 不良削減、段取りの効率化、内製化
- NC機オペレーター採用
- NCオペレーターの育成体制の構築(勉強会、研修体制)
もちろん、メトロールでも汎用機からNC機への移行期に、は現場の抵抗感がはじめはありました。
しかし課題を先送りにせず、いち早くNC化を現場に定着させることで従業員の成長や体制作りに繋がっています。
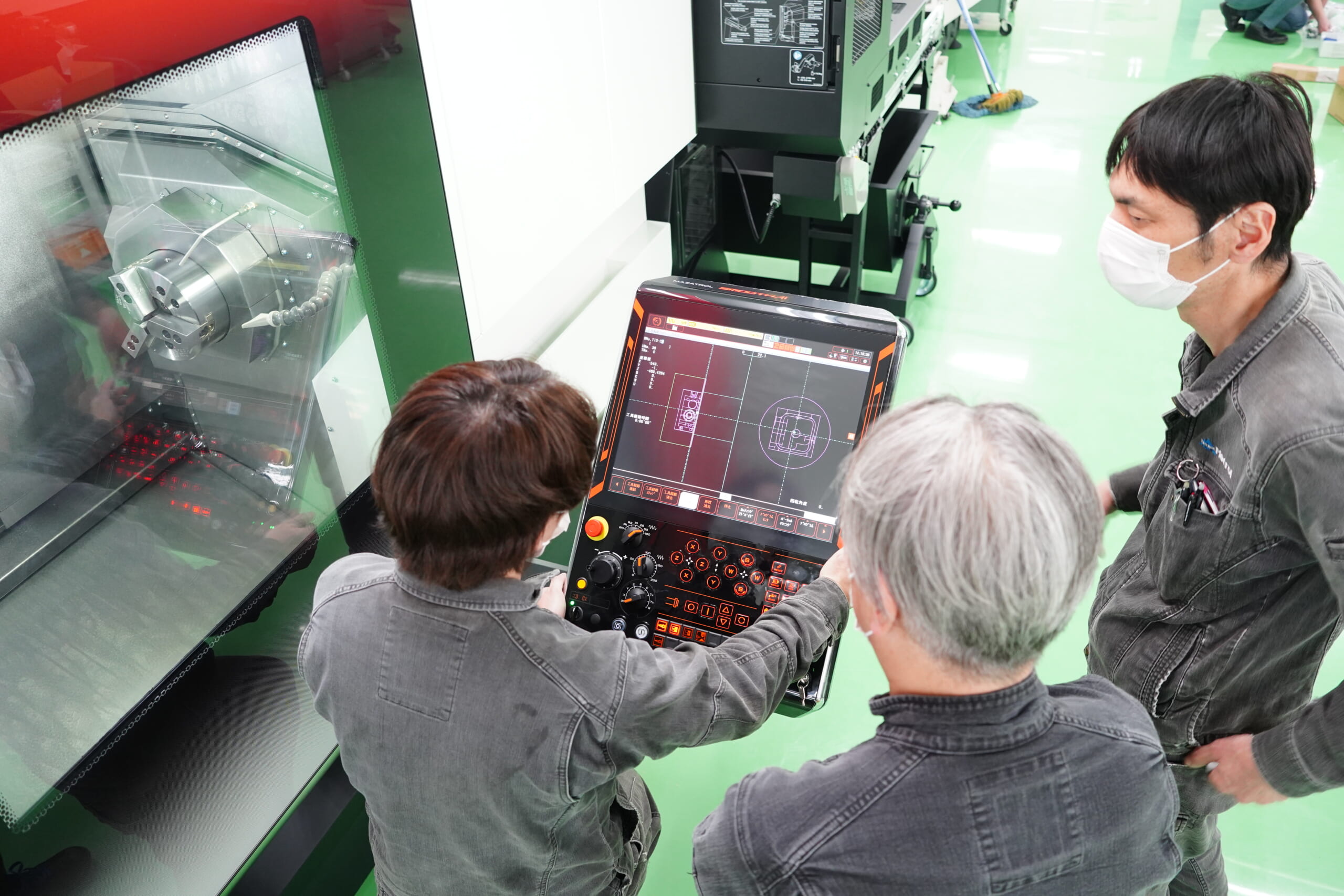
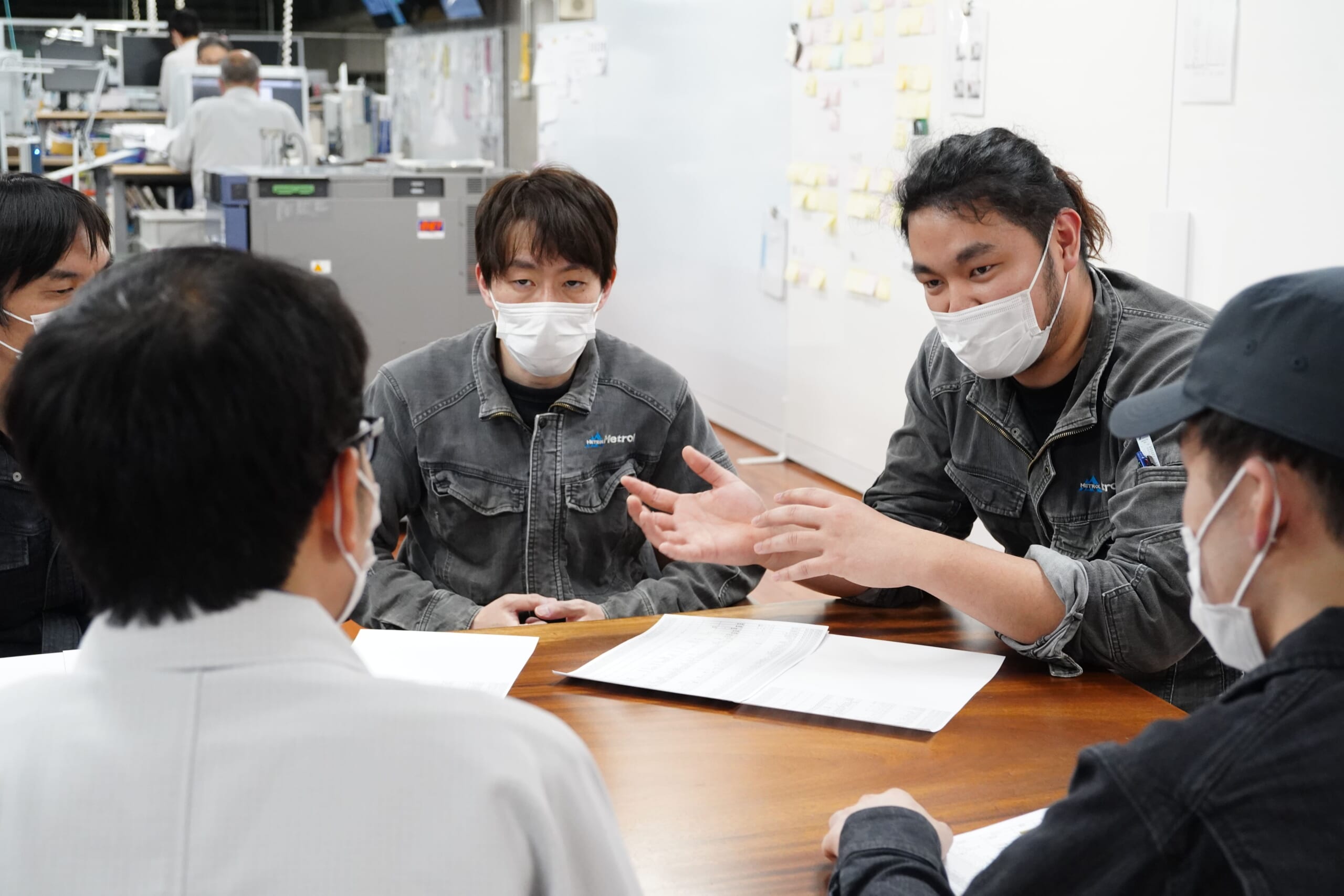
ここからは、なぜメトロールがCNC自動旋盤Cincomシリーズを導入したのかを解説していきます。
・CNC自動旋盤Cincom(シンコム)シリーズとは?
Cincom(シンコム)はバー材の連続加工を得意とするシチズンマシナリー株式会社のベストセラーCNC自動旋盤シリーズです。代表的なCincom L20シリーズは、累計販売台数が1万8000台を超えるベストセラー機となっています。
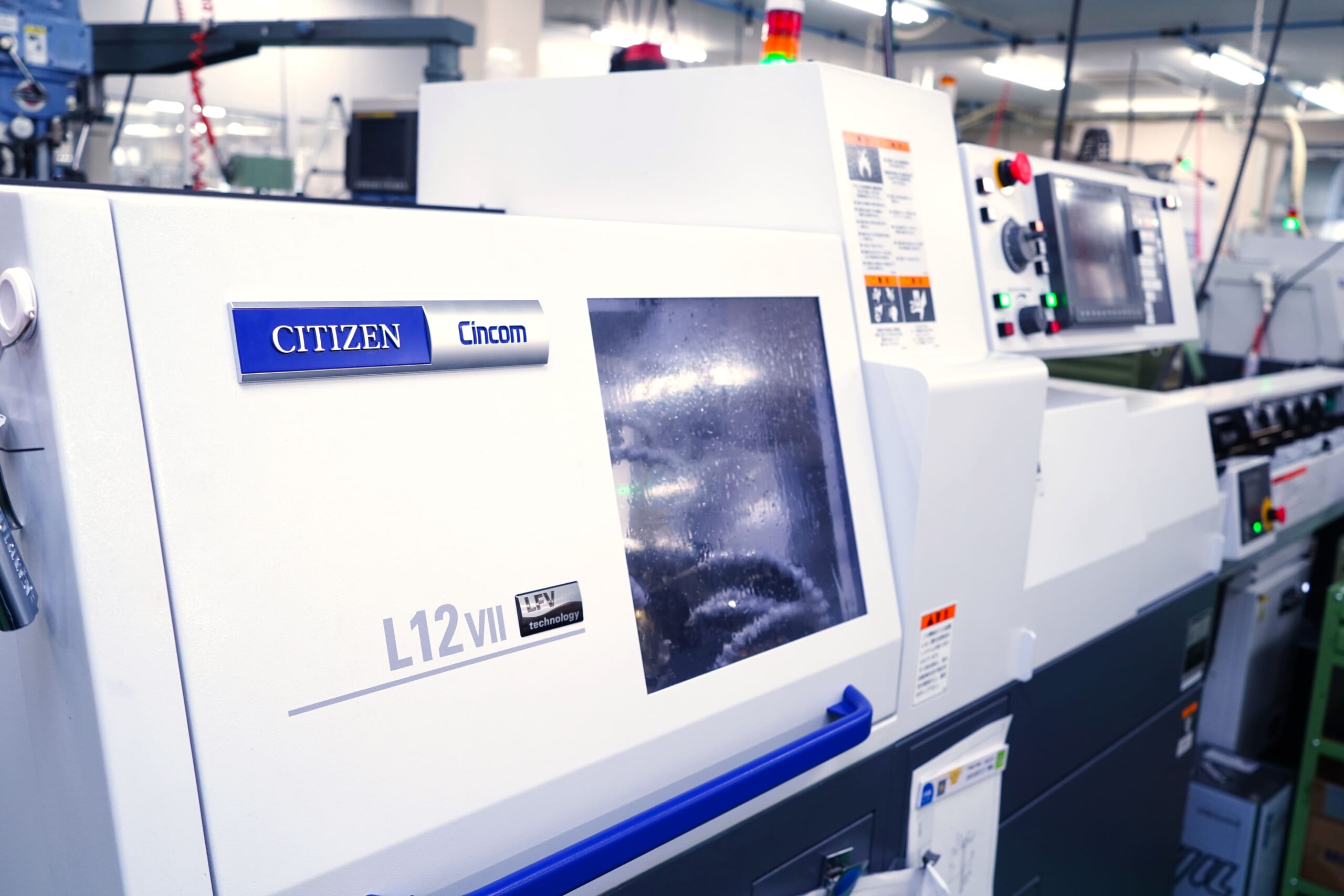
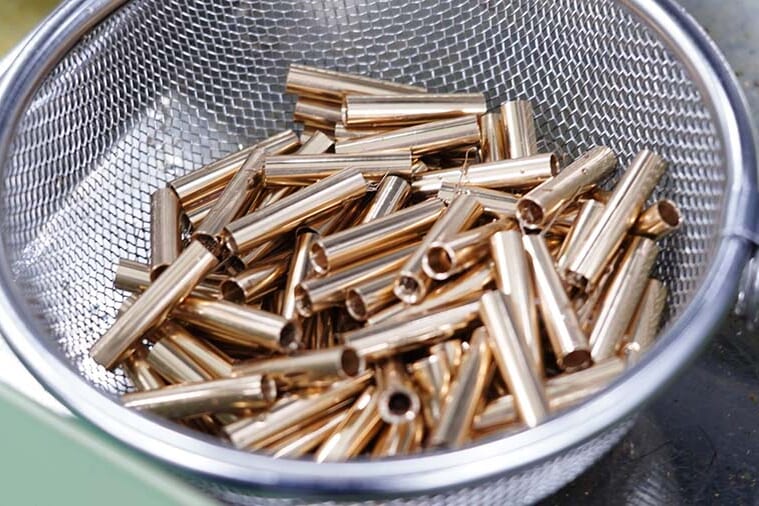
【基礎編】自動旋盤Cincomシリーズの選び方
Cincomに限らず、NC旋盤を選定する際に重要なポイントを簡単におさらいしておきましょう。
加工したいワークを想定して、旋盤の仕様を決めていくことが重要です。
① 材料のサイズ(最大径)と振り
取り付け可能なワークの最大径を確認しましょう。Cincomシリーズでは、Φ1、Φ4、Φ12~Φ32のモデルが揃っています。
② 刃物台の種類
刃物台には「くし刃型」と「タレット型」の2種類があります。
- くし刃型: 刃物交換が迅速で加工能率が高いです。
- タレット型: ツールの旋回に時間がかかりますが、複雑な形状の加工が可能です。
Cincomシリーズには、くし刃型と複合型(くし刃+タレット)のモデルがあります。
③ 軸数(主軸)
軸数は加工するワークの複雑さに応じて選びます。図面をメーカーに見せて相談すると良いでしょう。
④ 主軸台タイプ(固定形、移動形)
主軸台は「移動形」と「固定形」の2種類に分かれますが、Cincomシリーズは主に「移動形(ガイドブッシュ)」です。
- 移動形(ガイドブッシュ): 主軸が移動し、材料を出し入れしながら加工します。
- メリット: バー材から大量生産が可能。
- デメリット: 主軸とガイドブッシュ間に残材が発生します。
- 固定形(ガイドブッシュレス): 材料を固定して加工します。
- メリット: 残材が少なく、材料費の削減が可能。
- デメリット: 細長いワークの加工には不向きです。
以上のように、旋盤を選定する際の仕様やオプションは数多くありますが、方針をまとめておくと機械選定でのミスを防ぐことができるでしょう。
知っておきたい、自動旋盤Cincom導入前の留意事項
Cincomのような自動旋盤では、加工精度やスピードだけでなく、以下の3つの課題は事前に対策を考えておく必要があります。
- 課題1:切粉対策
- 課題2:無人、量産加工での不良品リスク
- 課題3:作業の属人化(職人化)
課題1:切粉対策
旋盤加工では、伸びた切粉が刃物に巻き付くことで加工不良やチョコ停の原因となり、多くの旋盤ユーザを悩ませています。そのため切粉対策は必須です。
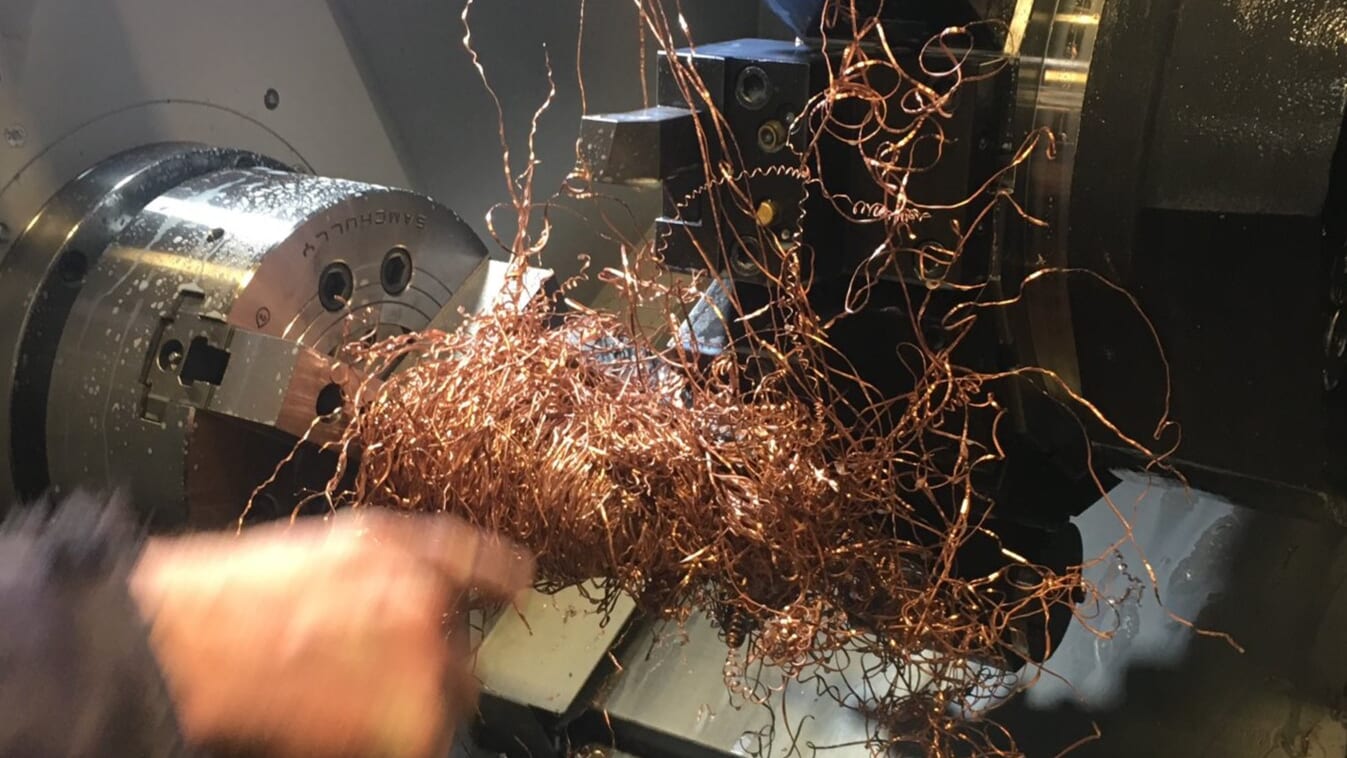
課題2:無人・量産加工での不良品リスク
量産加工では次のような課題とリスクがあります。
- 加工不良が一度発生すると不良品を継続して生産し続けてしまうリスク
- 万が一不良が出た際に全数を対象に行う良品判別、検査の工数が大きい
《例:1000個のワークを加工する場合》
途中の600個目のワークから加工不良が出始めたとすると、高確率で残りの400個は加工不良となります。(下図)
この場合、現場では何個目から不良が出始めたのかが分からないので、1000個分チェックし良品判別する手間がかかります。

課題3:作業の属人化(職人化)
自動旋盤は生産性が高い一方で、以下のような課題があります。
- 生産数が一気に増えるため、検査作業の負担が大幅に増える
- ノギスやマイクロメータなどの手動計測は、人によって測定結果がばらつくリスク
- NC加工の運用が熟練者の経験やカンに頼っていて、若手に引継ぎができない
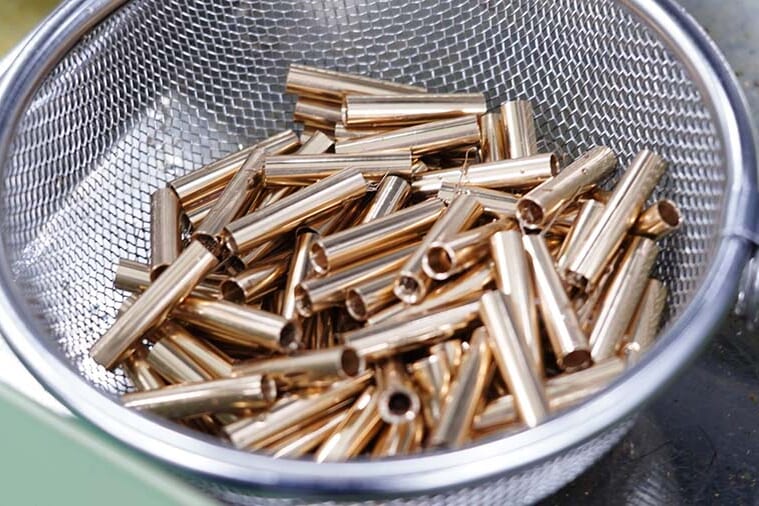
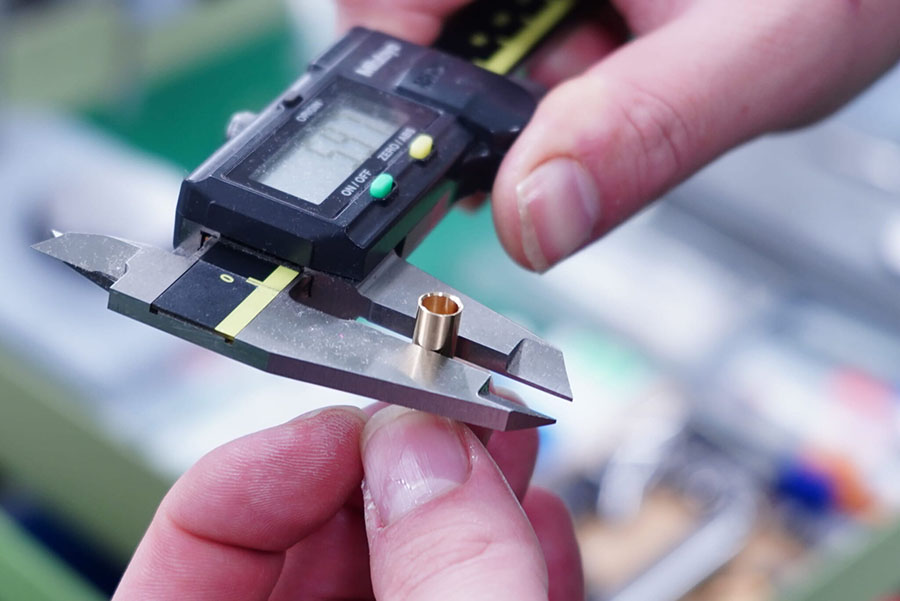
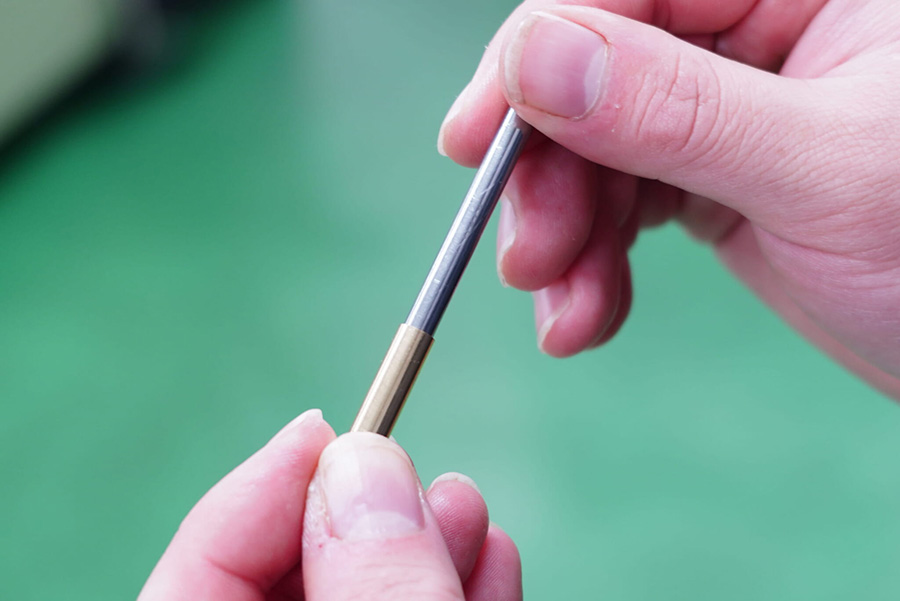
以上3つの課題は、旋盤ユーザ共通の悩みとも言えます。
自動旋盤Cincomを選んだ3つ理由。
先述した3つの課題を回避するためのCincom独自の機能が2つあり、以下が当社がCincomを選定した理由になります。
- LFV(低周波振動切削)
- 機内計測システム
- サポート体制の充実
選定理由1:自動旋盤CincomのLFV(低周波振動切削)
CincomのLFVは伸びたワークの切りくずを振動で細かく分断し、切粉トラブル(チョコ停など)を回避します。
日本、欧州、アジアなど海外含めるとすでに4500台以上、導入されている、旋盤加工には欠かせないスタンダード機能となっています。
メリットとして
- 切りくずによる不良発生や刃具破損が減り、加工コストが抑えられる
- 切りくず除去のためのチョコ停を低減し、無人での量産がしやすくなる
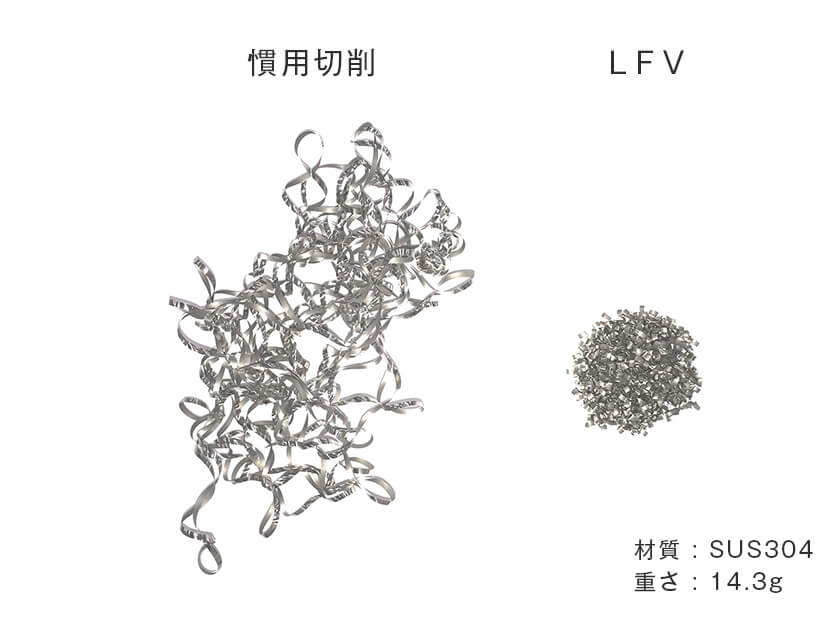
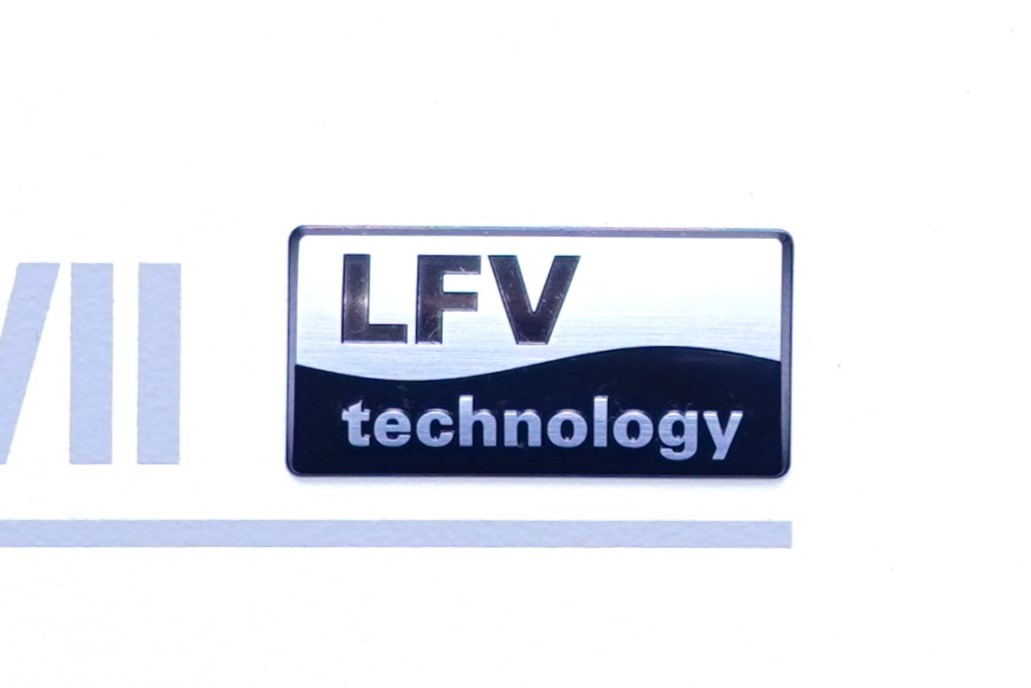
メトロールのLFV活用事例
メトロールでも樹脂やアルミ加工で、ツールに樹脂が巻き付いてワークに刃物が入らない、といったトラブルに悩まされていましたが、LFVでこうしたトラブルを回避しています。
Cincom以外のCNC旋盤では、長い切粉が発生するような場合は、加工プログラム内で切粉を分断するように切削条件を変えて対策するなど手間がかかります。
選定理由 2:自動旋盤Cincom独自の「機内計測システム」
Cincomには、タッチプローブを使ったワークを機内計測する新機能が搭載されています。
これにより、加工後に機内で寸法を確認することが可能です。
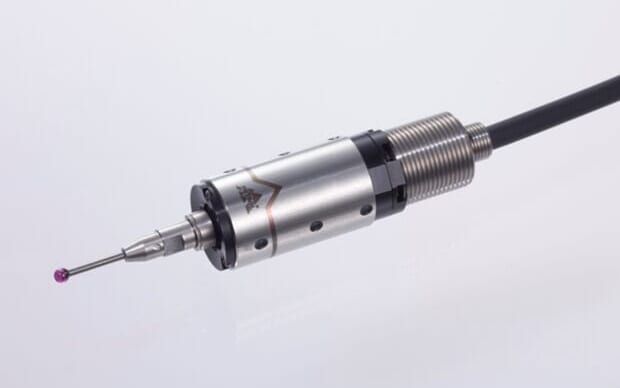
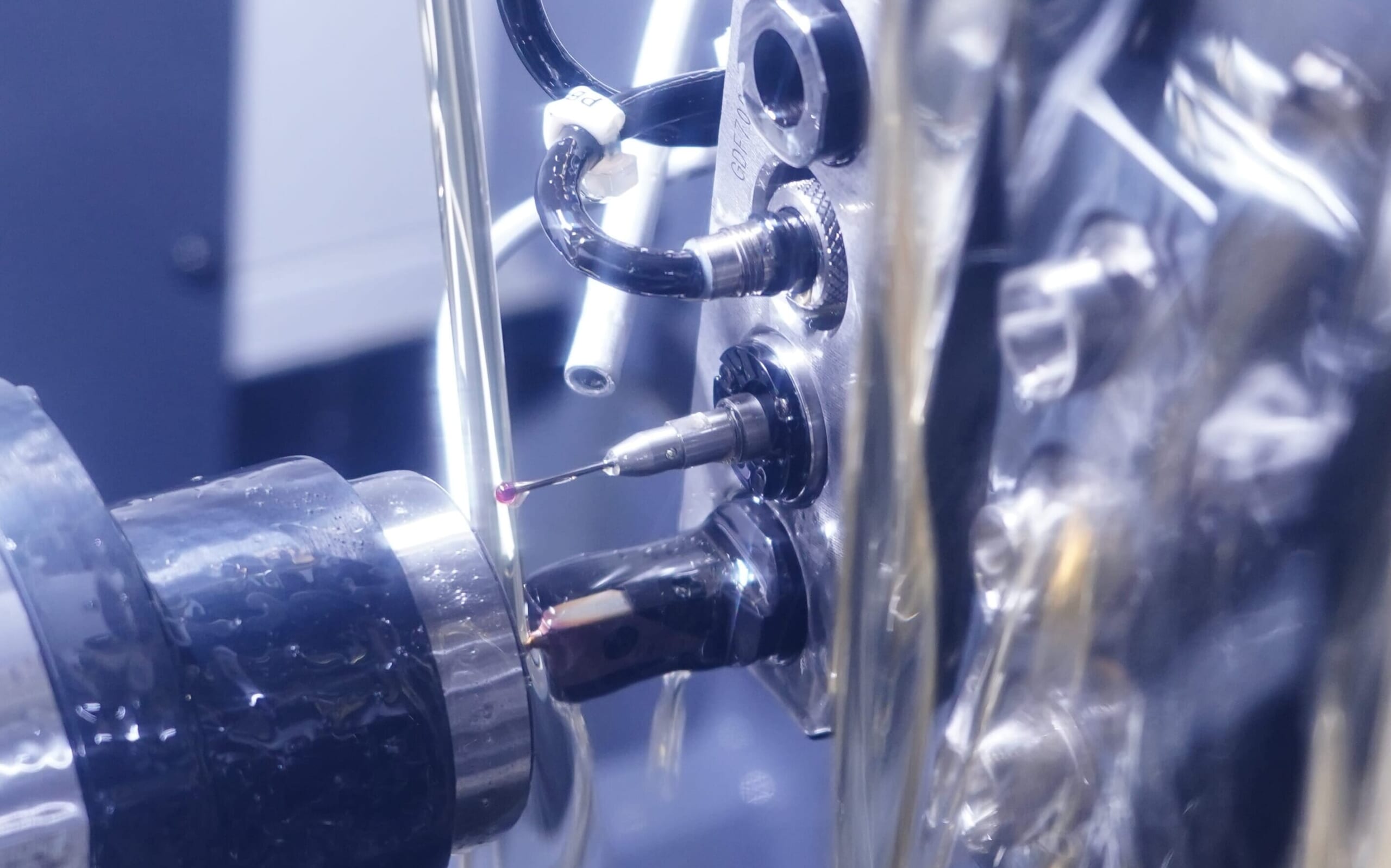
Cincom機内計測システムのメリット
大きなメリットとして以下の2点が挙げられます。
- 簡単操作:設定用の「専用画面※」が用意されており、値を入力するだけで機内計測のGコードを簡単に出力できます。
- データ蓄積と見える化: 計測データを蓄積し、結果をグラフで表示することができます。
※専用画面はCincomの機種によります。最新情報はメーカー様にお問い合わせください。
Cincomでの実際の機内計測の運用例
- 計測頻度の設定:例えば、100個加工したら1回計測するなどの設定が可能です。
- 判定時の動作:OK判定時は運転継続、NG判定時は機械を停止するなど、効率と不良回避のバランス調整が簡単に設定できます。
これにより、初心者でも簡単に使いこなせ、生産効率の向上と不良品の削減が期待できます。
選定理由 3:サポート体制の充実
金属加工に事故やトラブルは常につきものです。
不具合時のサポートスピードが速いという点も選定理由の1つとして挙げられます。
Cincomの「機内計測システム」導入メリットを解説
2つめの 選定理由 である「機内計測」のメリットについて詳しく解説します。
メリットは大きく3つあります。
- メリット①:人手による全数検査の削減
- メリット②:ロット管理によるコスト削減
- メリット③:計測データの蓄積と、データを活用した加工運用のDX化
それぞれ解説していきます。
機内計測のメリット1: 人手による全数検査の削減
加工後のワークに対して、全数機内計測をすることで下記のメリットが得られます。
- 人手による検査工程を削減できる
- 加工不良の発生を最速で察知し、コスト(資材、加工時間)を最小限にとどめることができる
- 即座に機械停止を行うことで、スピーディな原因究明と効果的な改善活動につながる
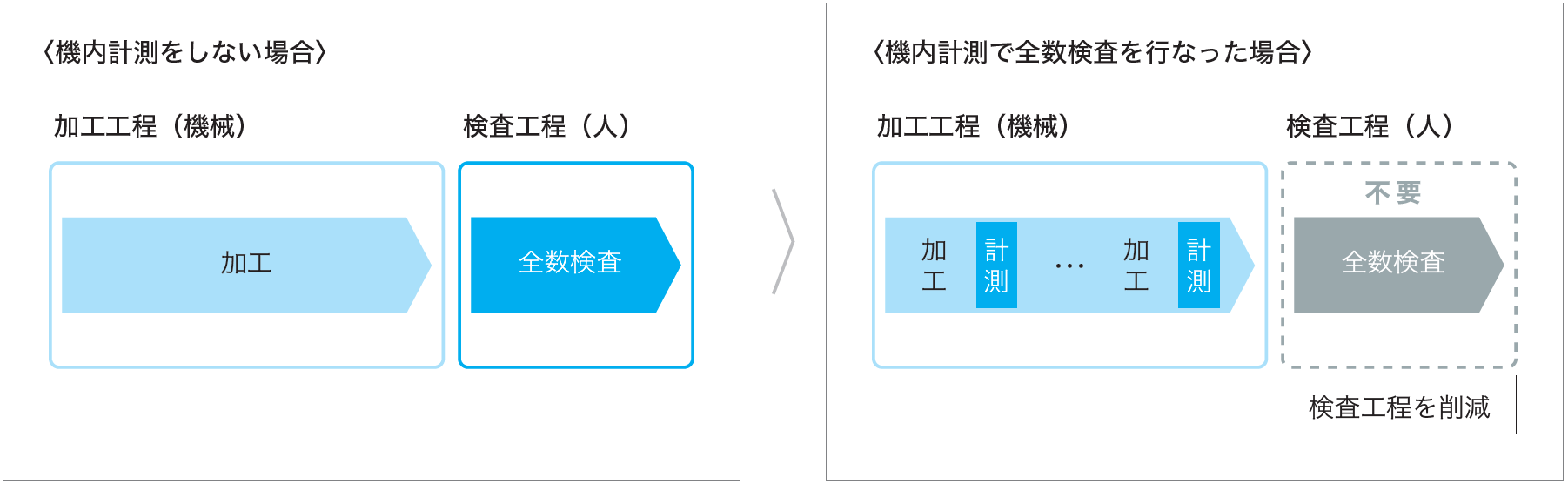
トレードオフとしてタクトタイムに計測時間がプラスされるため、バランスを取りたい場合は次に解説する「ロット管理」がおすすめです。
機内計測のメリット2:「ロット管理」による検査コストを大幅カット
タクトタイム優先で全数検査できない場合は、ロット管理を推奨します。
簡単に言えば「〇個加工したら1回検査する」といったような運用です。
ロット管理のメリットは
- タクトタイムへの影響を抑えつつ、不良品の大量発生を防ぐことができる
- 加工不良が発生した際にNG 判定のロットのみ検査を行うことで、トータルの検査コストを削減できる
- 無人運転では可能な限り早く、加工不良を止めたい
というニーズには最適な運用方法です。
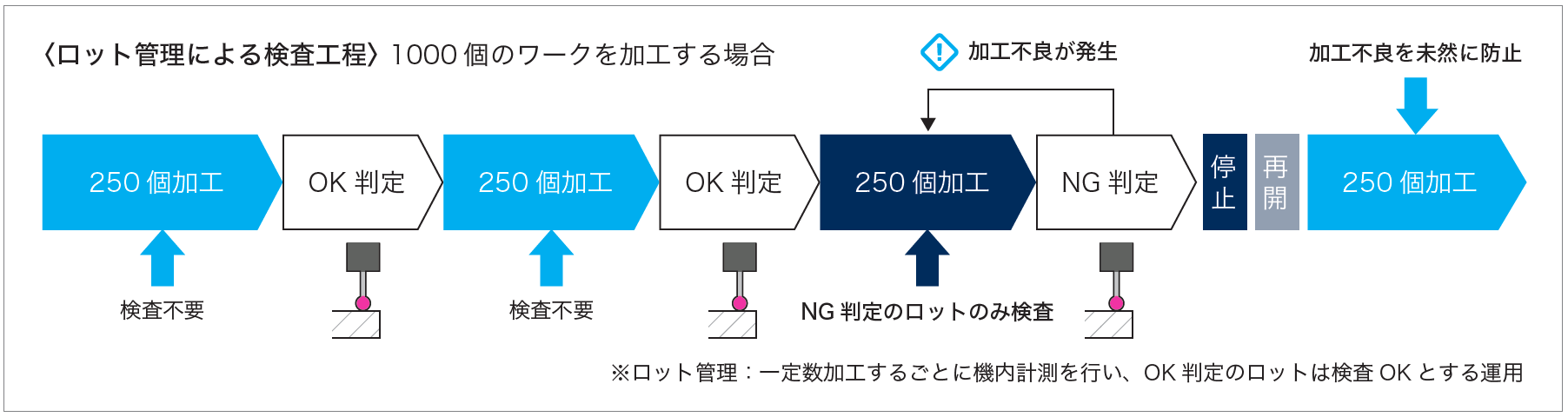
機内計測の導入メリット3:データに基づいた加工運用でDX化へ
加工現場では、多くのデータが見過ごされ、改善のヒントとして活用されません。
むしろそのデータは「熟練者の経験と勘」として誰にも見えない形で蓄積されてしまっています。
機内計測システムを導入することで、「経験と勘」をデータに変換し、客観的なデータに基づくアプローチが可能になります。
特に、以下のような悩みを抱える現場では効果的です。
- 熟練者のノウハウが言語化できず、若手の育成が難しい。
- 何個まで正常に連続加工できるかの判断が熟練者しかできない。
- 機械の熱変位による加工品質の変化が予測できない。
機内計測データの活用メリット
- 標準化: 熟練者頼りの運用から、数値に基づく正確な運用へ移行。
- 品質保証: 計測データの記録により、品質体制への安心感を提供。
- 分析と改善: データの蓄積と分析により、効率的な運用が可能。
データに基づいた運用事例
- 連続加工時間の設定: 例:ワークXの連続加工はN個までに設定。
- 最適な計測・補正頻度: 例:N個までは加工精度が維持されるため、Y個目から計測頻度を増加。
- メンテナンス時期の決定: 例:ワークXをN個加工したらツールを交換。

これらのデータに基づく運用方法により、生産効率の向上と品質管理が容易になります。
機内計測システム対応のCincomシリーズの紹介
①LFV ②機内計測システムをオプションとして選択可能なCincomシリーズをご紹介します。
Cincomシリーズは、全て名前にL12、L20、M32など数字がついています。これらの数字はバー材の最大加工径を示しているので覚えておきましょう。
LFV | 機内計測 | 最大加工径(mm) | 最大加工長(mm) | 刃物台 | ||
Cincom L12 | 着脱式ガイドブッシュを標準装備した高速主軸搭載マシン | 〇 | 〇 | φ12 | 135 | くし刃 |
Cincom L20 | LFV技術が正面・背面加工ともに使用可能になり、ダウンタイム軽減に貢献 | 〇 | 〇 | φ20 | 200 | くし刃 |
Cincom A20 | 機能性とコストをさらに追究した進化する5軸加工機 | 〇 | 〇 | φ20 | 165 | くし刃 |
Cincom M32 | くし刃 + タレットで複雑加工を実現するCincomのフラッグシップモデル | 〇 | 〇 | φ32 | 320 | くし刃 +タレット |
Cincomの機内計測を搭載するには?
メーカー様へお問い合わせ頂くことで搭載が可能です。
後付けに関しては機種の年式や仕様のヒアリングが必須となりますのでメーカー様にお問い合わせください。
【工場見学のお申込フォーム】実際にCincomを使った運用を見学したい方向け
東京都立川市にあるメトロールの工場で実際に運用を見てみたい方はコチラのフォームよりお問い合わせください。
自動旋盤以外にもマシニングなど様々な機械をご覧いただけます。
《メトロール工場見学会 概要》
対象:新規で工作機械の導入を検討中、もしくは改造を検討中のお客様
場所:メトロール本社工場(東京都立川市)
所要時間:1時間~1時間半
※繁忙期、目的によってお受けできないケースもございますのでご了承くださいませ。
※当社ではL20、L12を使用しております。M32の機内計測専用画面は未導入になりますのでご了承ください。